精密加工技术的发展现状与趋势
更新时间:2024-03-13 06:43:01 阅读量: 综合文库 文档下载
精密加工技术的发展现状与趋势
回顾过去的20世纪,人类取得的每一项重大科技成果,无不与制造技术,尤其与超精密加工技术密切相关。在某种意义上,超精密加工担负着支持最新科学发现和发明的重要使命 。可以说,没有高水平的超精密加工技术,就不会有真正强大的国防。另外,在航天、航空工业中,人造卫星、航天飞机、民用客机等,在制造中都有大量的精密和超精密加工的需求。当前,微型卫星、微型飞机、超大规模集成电路的发展十分迅猛,涉及微细加工技术、纳米加工技术等,已形成微型机械制造。这些技术都在精密和超精密加工范畴内,与计算机工业、国防工业的发展直接相关。
超精密加工就是在超精密机床设备上,利用零件与刀具之间产生的具有严格约束的相对运动 ,对材料进行微量切削,以获得极高形状精度和表面光洁度的加工过程。 其精度从微米到亚微米,乃至纳米,其应用范围日趋广泛,在高技术领域和军用工业以及民用工业中都有广泛应用,尤其是电气自动化领域,如超大规模集成电路、高密度磁盘、精密雷达、导弹火控系统、精密机床、精密仪器、录像机磁头、复印机磁鼓、煤气灶转阀等都要采用超精密加工技术。它与当代一些主要科学技术的发展有密切的关系,是当代科学发展的一个重要环节;而且,超精密加工技术的发展也促进了机械、液压、电子、半导体、光学、传感器和测量技术以及材料科学的发展。
通常,按加工精度划分,机械加工可分为一般加工、精密加工、超精密加工三个阶段。由于生产技术的不断发展,划分的界限将逐渐向前推移,过去的精密加工对今天来说已是普通加工,因此,其划分的界限是相对的,且在具体数值上至今没有固定。 二、 几种常用的精密加工方法及特点
传统的精密加工方法有布轮抛光、砂带磨削、超精细切削、精细磨削、珩磨、研磨、超精研抛技术、磁粒光整等。
①抛光 是利用机械、化学、电化学的方法对工件表面进行的一种微细加工,主要用来降低工件表面粗糙度,常用的方法有:手工或机械抛光、超声波抛光、化学抛光、电化学抛光及电化学机械复合加工等。
②砂带磨削 是用粘有磨料的混纺布为磨具对工件进行加工,属于涂附磨具磨削加工的范畴,有生产率高、表面质量好、使用范围广等特点。国外在砂带材料及制作工艺上取得了很大的成就,有了适应于不同场合的砂带系列,生产出通用和专用的砂带磨床,而且自动化程度不断提高,但国内砂带品种少,质量也有待提高,对机床还处于改造阶段。
③精密切削 用高精密的机床和单晶金刚石刀具进行切削加工,主要用于铜、铝等不宜磨削加工的软金属的精密加工,还具有较好的光学性质。
④超精密磨削 用精确修整过的砂轮在精密磨床上进行的微量磨削加工,金属的去除量可在亚微米级甚至更小,可以达到很高的尺寸精度、形位精度和很低的表面粗糙度值。尺寸精度0.1~0.3μm,表面粗糙度Ra0.2~0.05μm,效率高。应用范围广泛,从软金属到淬火钢、不锈钢、高速钢等难切削材料,及半导体、玻璃、陶瓷等硬脆非金属材料,几乎所有的材料都可利用磨削进行加工。 但磨削加工后,被加工的表面在磨削力及磨削热的作用下金相组织要发生变化,易产生加工硬化、淬火硬化、热应力层、残余应力层和磨削裂纹等缺陷。
⑤珩磨 用油石砂条组成的珩磨头,在一定压力下沿工件表面往复运动,加工后的表面粗糙度可达Ra0.4~0.1μm,最好可到Ra0.025μm,主要用来 加工铸铁及钢,不宜用来加工硬度小、韧性好的有色金属。
⑥精密研磨与抛光 通过介于工件和工具间的磨料及加工液,工件及研具作相互机械摩擦,使工件达到所要求的尺寸与精度的加工方法。
三、我国精密加工技术的发展现状
我国的超精密加工技术在70年代末期有了长足进步,80年代中期出现了具有世界水平的超精密机床和部件,研制出了多种不同类型的超精密机床、部件和相关的高精度测试仪器等,达到了国内领先、国际先进水平。精密和超精密加工技术的发展,直接影响到一
个国家尖端技术和国防工业的发展,因此世界各国对此都极为重视,投入很大力量进行研究开发,同时实行技术保密,控制关键加工技术及设备出口。随着航空航天、高精密仪器仪表、惯导平台、光学和激光等技术的迅速发展和多领域的广泛应用,对各种高精度复杂零件、光学零件、高精度平面、曲面和复杂形状的加工需求日益迫切。目前国外已开发了多种精密和超精密车削、磨削、抛光等机床设备,发展了新的精密加工和精密测量技术。
我国目前已是一个“制造大国”,制造业规模名列世界第四位,仅次于美国、日本和德国,近年来在精密加工技术和精密机床设备制造方面也取得了不小进展。但我国还不是一个“制造强国”,与发达国外相比仍有较大差距。我国每年虽有大量机电产品出口,但多数是技术含量较低、价格亦较便宜的中低档产品;而从国外进口的则大多是技术含量高、价格昂贵的高档产品。目前我国每年需进口大量国内尚不能生产的精密数控机床设备和仪器由于国外一些重要的高精度机床设备和仪器对我国实行封锁禁运,而这些精密设备仪器正是我国发展国防工业和尖端技术所迫切需要的,因此,为了使我国的国防和科技发展不受制于人,我们必须投入必要的人力物力,自主发展精密和超精密加工技术,争取尽快将我国的精密和超精密加工技术水平提升到世界先进水平。 四、精密加工技术的发展趋势及前景
(1) 高精度、高效率。高精度与高效率是超精密加工永恒的主题。当前超精密加技术虽能获得极高的表面质量和表面完整性,但以牺牲加工效率为保证。探索能兼顾效率与精度的加工方法,成为超精密加工领域研究人员的目标。
(2) 工艺整合化。当今企业间的竞争趋于白热化,高生产效率越来越成为企业赖以生存的条件。在这样的背景下,出现了“以磨代研”甚至“以磨代抛”的呼声。另一方面,使用一台设备完成多种加工的趋势越来越明显。
(3) 大型化、微型化。为加工航空、航天、宇航等领域需要的大型光电子器件,需要建立大型超精密加工设备。为加工微型电子机械、光电信息等领域需要的微型器件,需要微型超精密加工设备。 (4) 在线检测。尽管现在超精密加工方法多种多样,但都尚未发展成熟。主要原因之一是超精密加工检测技术还不完善,特别是在线检测技术。从实际生产角度讲,开发加工精度在线测量技术是保证产品质量和提高生产率的重要手段。
(5) 智能化。超精密加工中的工艺过程控制策略与控制方法也是目前的研究热点之一。以智能化设备降低加工结果对人工经验的依赖性一直是制造领域追求的目标。加工设备的智能化程度直接关系到加工的稳定性与加工效率,这一点在超精密加工中体现更为明显。
精密加工方法在今天显得越来越重要,精密加工技术已成为目前高科技技术领域的基础,提高超精密加工的精度已成为目前迫在眉睫的问题。目前,很多学者正在这方面做着大量的研究和实验,相信不久的将来,超精密加工会取得长足进展。
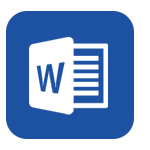





正在阅读:
精密加工技术的发展现状与趋势03-13
苏教版语文三年级上册第二单元试卷06-27
发电厂继电保护试题库02-03
兽用处方药管理制度08-15
随想录(软件调试)06-08
长须鲸的自述作文450字07-07
软件工程课程设计心得总结03-27
最常用的PowerPoint动画效果及设置方法 - 图文02-29
红石公园作文600字06-27
- 高一物理牛顿运动定律全套学习学案
- 水处理一级反渗透加还原剂亚硫酸氢钠后为什么ORP会升高
- 毕业设计(论文)-正文董家口 - 图文
- 荣盛酒店经营管理公司录用通知及入职承诺书II
- 第二讲 大学英语四级快速阅读技巧
- 质量管理体系文件(2015年委托第三方医药物流配送企业专用版本)
- 214071收款办法
- 苏轼对《文选》选文的评价
- 《诊断学基础B》1-8作业
- 广东省东莞市高一数学下学期期末教学质量检查试题
- 海南电网公司VIS推广应用管理办法
- 红星照耀中国习题
- 苏教版小学语文六年级上册期末复习资料之生字词整理
- 局域网组建与应用—王向东
- 税务稽查内部管理文书样式
- 环保社会实践调查表
- 九年级思品第一单元复习
- 2016年全国注册咨询工程师继续教育公路路线设计规范试卷
- 毕业设计-青岛港董家口港区防波堤设计
- 撞背锻炼方法与益处
- 精密
- 发展现状
- 趋势
- 加工
- 技术
- 2011达县教师公招职位表 - 图文
- 采煤安全质量标准化考试试卷
- 广州版本新旧教材的教学话题的对比 - 图文
- 为什么夏天要穿浅色衣服
- 2018-2024年中国作文辅导行业市场发展态势及投资前景可行性报告
- 北语15秋《汉字学》作业4100分答案
- 手机游戏项目可行性研究报告 - 图文
- 高中作文-以成长的轨迹为中考作文600字5篇
- 摄像机的使用方法
- 邓亚萍:有一群乔布斯这样的人,才能成功
- 郑州代理记账公司:两个“营业收入”
- (课标版)2019高中地理第4章地表形态的塑造第2节山地的形成学案
- 中西方文化对商务谈判的影响
- 08. 一次分式型函数学案
- 道路运输应急救援预案 - 图文
- 2015年初级会计实务真题 1
- (苏科版)八年级物理下册《第六章物质的物理属性》复习教案
- 食堂承包合同范本
- 最新精选鲁人版初中政治思品七年级上册第三单元 相逢是首歌第5课
- 乡镇2018年林业上半年工作总结及下半年工作计划