化工专业实验教材
更新时间:2024-04-26 00:01:01 阅读量: 综合文库 文档下载
- 化工专业实验教学大纲推荐度:
- 相关推荐
化工专业实验教材
实验一 双驱动搅拌器测定气液传质系数
A 实验目的
气液传质系数是设计计算吸收塔的重要数据。工业上应用气液传质设备的场合非常多,而且处理物系又各不相同,加上传质系数很难完全用理论方法计算得到,因此最可靠的方法就是借用实验手段得到。测定气液传质系数的实验设备多种多样,而且都具有各自的优缺点。本实验所采用的双驱动搅拌吸收器不但可以测定传质系数,而且可以研究气液传质机理。本实验的目的是通过了解双驱动搅拌吸收器的特点,明暸该设备的使用场合以及测定气液传质系数的方法,进而对气液传质过程有进一步的了解。
B 实验原理
气液传质过程中由于物系不同,其传质机理可能也不相同,被吸收组分从气相传递到液相的整个过程决定于发生在气液界面两侧的扩散过程以及在液相中的化学反应过程,化学反应又影响组分在液相中的传递。化学反应的条件、结果各不相同,影响组分在液相中传递的程度也不同,通常化学反应是促进了被吸收组分在液相中的传递。或者将这个过程的传质阻力分成气膜阻力与液膜阻力,就需要了解整个传质过程中哪一个是传质的主要阻力,进而采取一定的措施,或者提高某一相的运动速度,或者采用更有效的吸收剂,从而提高传质的速率。
气膜阻力为主的系统、液膜阻力为主的系统或者气膜阻力与液膜阻力相近的系统在实际操作中都会存在,在开发吸收过程中要了解某系统的吸收传质机理必须在实验设备上进行研究。双驱动搅拌吸收器的主要特点是气相与液相搅拌是分别控制的,搅拌速度可以分别调节,所以适应面较宽。可以分别改变气、液相转速测定吸收速率来判断其传质机理,也可以通过改变液相或气相的浓度来测定气膜一侧的传质速率或液膜一侧的传质速率。
测定某条件下的气液传质系数必需采取切实可行的方法测出单位时间单位面积的传质量,并通过操作条件及气液平衡关系求出传质推动力,由此来求得气液传质系数。传质量的计算可以通过测定被吸收组分进搅拌吸收器的量与出吸收器的量之差求得,或是通过测定搅拌吸收器里的吸收液中被吸收组分的起始浓度与最终浓度之差值来确定。
本实验以热碳酸钾吸收二氧化碳作为系统,该系统是一个伴有化学反应的吸收过程: K2CO3?CO2?H2O
2KHCO3
(1)
1
CO2从气相主体扩散到气液界面,在液相界面与K2CO3进行化学反应并扩散到液相主体中去,由于CO2在K2CO3的溶液中的反应为快速反应,使原来液膜控制的过程有所改善。若气膜阻力可以忽略时,吸收速率的公式可写成:
*NCO2??KLCA?CAL (2)
? 或 NCO2??KGHCO2??P?P??K?P?P? (3) (4)
A*ALA*AL式中 NCO2- 单位时间单位面积传递的CO2量;? - 增大因子;KL - 液相传质系数;
* - 气相中C02分压的平衡浓度;CAL- 液相中的C02浓度; KG- 气相传质系数; CAC02的溶解度系数; PA - C02分压,为总压与吸收液面上饱和水蒸气压之差; HCO2 -
* - 吸收液上C02的平衡分压; K - K2CO3吸收C02的气液传质系数。 PAL实验中以钢瓶装C02作气源,经过稳压,控制气体流量、增湿后进入双驱动搅拌吸收器,气体为连续流动,吸收液固定在吸收器内,操作一定的时间后取得各项数据,可计算出K值,此为一个平均值。
C02在整个吸收过程的传质量可用K2CO3中的KHCO3增加量来确定,即可用酸解法来得到,从每毫升吸收液在吸收前后所持有C02量的差可以确定C02总吸收量(操作方法见实验步骤中的分析方法)。
吸收在60℃下操作,使用1.2M的K2CO3吸收液,它的平衡分压可用下式计算:
P*CO2?1.98?10?C*80.4?f2??1?f????8160??exp?? ?T???(5)
式中 PCO2 - CO2平衡分压 [MPa];C - K2CO3的浓度 [mol/L];T - 吸收温度 [K];
f - 转化度 [无因次 f?CHCO?32CCO??CHCO?33];
60℃时热钾碱上水蒸汽分压较大,应从总压中扣除水蒸汽分压后才是界面上CO2的分压。60℃碱液上水蒸汽分压可按下式计算:
?1?0.3?f? (6) 式中PW - 水蒸汽分压 PW?0.01751[MPa]
吸收液的起始转化度和终了转化度均可用酸解法求取(见分析方法)。
2
为了考察其他物系不同操作条件对吸收速率的影响,可以分别改变气相的搅拌速度与液相的搅拌速度,测得传质系数后进行综合比较,确定系统的传质的情况。
C 预习与思考
*(1) 本实验需要记录哪些数据?如何求取NCO2、PA、PAL 。
(2) 本实验测定过程中的误差来源是什么? (3) 本实验用纯CO2有什么目的?
(4) 实验前为何要用CO2排代实验装置中的空气? (5) 气体进入吸收器前为何要用水饱和器? (6) 气体稳压管的作用是什么? (7) 实验时测定大气压有何用处? (8) 酸解出的CO2为何要同时测定温度?
D 实验装置与流程
进水图1 双驱动搅拌器实验流程示意图 1–气体稳压管;2、12–气体温度计;3、14–皂膜流量计;4–气体调节阀;5、15–压差计; 6–气体增湿器;7–双驱动搅拌吸收器;8–吸收液取样阀;9、10–直流电机;11–弹簧夹;13–吸收剂瓶
气体从钢瓶经减压阀送出,经稳压管稳压后由气体调节阀4调节适当流量,用皂膜流量计计量后进入水饱和器6,饱和器放置在超级恒温槽内,双驱动搅拌吸收器7的吸收温度也由恒温槽控制,增湿的气体从吸收器中部进入,与吸收液接触后从上部出口引出,出口气体经另一皂膜流量计后放空。
双驱动搅拌吸收器是一个气液接触界面已知的设备,气相搅拌轴与液相搅拌轴都与各
3
自的磁钢相连接,搅拌浆的转速分别通过可控硅直流调速器调节。吸收器中液面的位置应控制在液相搅拌浆上浆的下缘1mm左右,以保证浆叶转动时正好刮在液面上,以达到更新表面的目的。吸收液从吸收剂瓶一次准确加入。
E 实验步骤及方法 (1) 实验操作步骤:
1. 细检查实验设备的状况,排掉管路内的积水,关闭放空阀。 2. 吸收剂瓶内放入约350ml, 浓度为1.2 mol/L的前,溶液中CO2的初始含量(
K2CO3吸收液,并取样分析吸收
C0f)。
3. 关闭气体调节阀,开启总电源,打开CO2钢瓶总阀,然后,缓慢开启钢瓶减压阀,观察稳定管内的鼓泡情况。鼓泡稳定后,再开启气体调节阀并通过皂膜流量计调节适当的气体流量,向吸收器内连续通入CO2,以置换器内的空气。
4. 开启恒温槽,设定吸收温度为60℃,并开启恒温槽循环水将吸收器升温至指定温度,用CO2排代约30min,方可进行实验;
5. 开启双驱动的搅拌器的上下搅拌,操作屏仪表显示,如气体进出口温度,调节上搅拌的转速在300prm 左右,下搅拌的转速在150prm 左右;
6. 开吸收剂瓶下的弹簧夹,向搅拌吸收器内加入吸收液,待吸收液的液面升至与液相搅拌桨的上叶片的下缘相切时停止加料,关闭加料管。同时按下秒表,开始计时。
7. 每隔一定时间,利用秒表和进、出口的皂膜流量计,同时测定进出、口气体的流量(ml/s),记录时间和测得的进出、口气体的流量(ml/s)。两个流量的差值,即为该瞬间的吸收速率。
8. 常操作1至1.5小时后,准确记下吸收操作的总时间(tmin),停止上、下搅拌,立即打开吸收器的液相取样阀,将吸收液收集在250 ml量筒中,测取并记录液体总体积(V)。然后,取样分析吸收,测定溶液中CO2的含量(温度,对CO2体积校正。
9. 关闭CO2减压阀及CO2钢瓶出口阀,将搅拌器转速调到“0”,关闭超级恒温槽电源,关闭设备电源,打开放空管路。
(2) 酸解法分析吸收液中CO2含量。
1) 原理:热钾碱与H2SO4的反应放出CO2,用量气管测量CO2体积,即可求出溶液的转
4
Cf)。分析时,记录量气管上端的
化度。反应式为: K2CO3?H2SO4?K2SO4?CO2??H2O
2KHCO3?H2SO4?K2SO4?CO2??2H2O 2) 仪器与试剂:
A.仪器装置,参考实验“热钾碱溶液吸收CO2的吸收速率系数的测定”。 B.1ml移液管1支,5ml移液管1支。 C.3mol/l浓度的H2SO4。 3) 分析操作及计量:
(7) (8)
准确吸取吸收液1ml置于反应瓶的内瓶中,用5ml移液管移5ml 3mol H2SO4置于反应瓶的外瓶内,提高水准瓶,使液面升至量气管的上刻度处,塞紧瓶塞,使其不漏气后,调整水准瓶的高度,使水准瓶的液面与量气管内液面相平,记下量气管的读数V1。摇动反应瓶使H2SO4与碱液充分混合,反应完全(无气泡发生),再记下量气管的读数V2。可计算出吸收液中CO2含量。
溶液中:VCO2ml/ml碱液??V2?V1???
式中:VCO2- 每ml吸收液含CO2的ml量?ml/ml?;? - 校正系数,
??(9)
273.2(P?PH2O)? ??; T101.3(10)
式中P-大气压,(KPa);T -酸解时器内CO2温度,(K);PH2O- t℃时的饱和水蒸气压,(KPa);
PH2O=0.1333exp?18.3036?3816.44?T?46.13??,(KPa); 溶液转化度可按下式计算: f?(11) (12)
CfC0f?1
f- 吸收液的转化度。可用来计算吸收液上CO2的平衡分压与水的饱和蒸汽压。
。 Cf、C0f - 吸收后和吸收前1ml吸收液酸解后放出的CO2校正后体积数(ml)F 实验数据处理
从记录的实验原始数据中逐项计算出单位时间单位面积的CO2传递量,换算成摩尔数,以及从初始及终了吸收液的转化度算出吸收的推动力,求取平均推动力来计算气液传质系数,单位为molS?M?MPa。
5
?2?
对在不同的液相转速下取得的K值进行综合比较,并得出结论。
6
实验二 连续流动反应器中的返混测定
A 实验目的
本实验通过单釜与三釜反应器中停留时间分布的测定,将数据计算结果用多釜串联模型来定量返混程度,从而认识限制返混的措施。本实验目的为
(1) 掌握停留时间分布的测定方法。
(2) 了解停留时间分布与多釜串联模型的关系。 (3) 了解模型参数n的物理意义及计算方法。 B 实验原理
在连续流动的反应器内,不同停留时间的物料之间的混和称为返混。返混程度的大小,一般很难直接测定,通常是利用物料停留时间分布的测定来研究。然而测定不同状态的反应器内停留时间分布时,我们可以发现,相同的停留时间分布可以有不同的返混情况,即返混与停留时间分布不存在一 一对应的关系,因此不能用停留时间分布的实验测定数据直接表示返混程度,而要借助于反应器数学模型来间接表达。
物料在反应器内的停留时间完全是一个随机过程,须用概率分布方法来定量描述。所用的概率分布函数为停留时间分布密度函数f?t?和停留时间分布函数F?t?。停留时间分布密度函数f?t?的物理意义是:同时进入的N个流体粒子中,停留时间介于t到t+dt间的流体粒子所占的分率dNN为f?t?dt。停留时间分布函数F?t?的物理意义是:流过系统的物料中停留时间小于t的物料的分率。
停留时间分布的测定方法有脉冲法,阶跃法等,常用的是脉冲法。当系统达到稳定后,在系统的入口处瞬间注入一定量Q的示踪物料,同时开始在出口流体中检测示踪物料的浓度变化。
由停留时间分布密度函数的物理含义,可知
f?t?dt?V?C?t?dtQ (1)
所以
f?t??Q??VC?t?dt (2)
0?VC?t??0?VC?t?dt?C?t?dt0?C?t?? (3)
由此可见f?t?与示踪剂浓度C?t?成正比。因此,本实验中用水作为连续流动的物料,
7
以饱和KCl作示踪剂,在反应器出口处检测溶液电导值。在一定范围内,KCl浓度与电导值成正比,则可用电导值来表达物料的停留时间变化关系,即f?t??L?t?,这里
L?t??Lt?L?,Lt为t时刻的电导值,L∞为无示踪剂时电导值。
停留时间分布密度函数f?t?在概率论中有二个特征值,平均停留时间(数学期望)t和方差?t2。
tC?t?dt?t的表达式为: t??tf?t?dt? (4)
?C?t?dt????00?0采用离散形式表达,并取相同时间间隔?t,则: t???tC?t??t?t?L?t?? ?C?t??t?L?t???00 (5)
2?t2的表达式为: ?t2???t?t?f?t?dt??t2f?t?dt?t2 (6)
也用离散形式表达,并取相同?t,则:
?t2C?t??t2L?t?22 ????t???t (7)
?C?t??L?t?2t若用无因次对比时间?来表示,即?=t2无因次方差??=?t2t,
t2 。
在测定了一个系统的停留时间分布后,如何来评介其返混程度,则需要用反应器模型来描述,这里我们采用的是多釜串联模型。
所谓多釜串联模型是将一个实际反应器中的返混情况作为与若干个全混釜串联时的返混程度等效。这里的若干个全混釜个数n是虚拟值,并不代表反应器个数,n称为模型参数。多釜串联模型假定每个反应器为全混釜,反应器之间无返混,每个全混釜体积相同,
2则可以推导得到多釜串联反应器的停留时间分布函数关系,并得到无因次方差??与模型参
数n存在关系为 n?当 n?1,
1??2 (8)
??2?1 ,为全混釜特征;
当n??,
??2?0, 为平推流特征;
8
这里n是模型参数,是个虚拟釜数,并不限于整数。 C 预习与思考
(1)为什么说返混与停留时间分布不是一一对应的?为什么我们又可以通过测定停留时间分布来研究返混呢?
(2)测定停留时间分布的方法有哪些?本实验采用哪种方法? (3)何谓返混?返混的起因是什么?限制返混的措施有哪些? (4) 何谓示踪剂?有何要求?本实验用什么作示踪剂? (5)模型参数与实验中反应釜的个数有何不同?为什么? D 实验装置与流程
实验装置如图2所示,由单釜与三釜串联二个系统组成。三釜串联反应器中每个釜的体积为1L,单釜反应器体积为3L,用可控硅直流调速装置调速。实验时,水分别从二个转子流量计流入二个系统,稳定后在二个系统的入口处分别快速注入示踪剂,由每个反应釜出口处电导电极检测示踪剂浓度变化,并由记录仪自动录下来。
E 实验步骤及方法
(1) 通水,开启水开关,让水注满反应釜,调节进水流量为20Lh,保持流量稳定。
(2) 通电,开启电源开关。 图2 连续流动反应器返混实验装置图
1–全混釜(3L);2、3、4–全混釜(1L); 5–转子流量计;6–电机;
7–电导率仪;8–电导电极;9–记录仪;10–四笔记录仪或微机
① 开记录仪,记下走纸速度; ② 开电导仪并调整好,以备测量;
③ 开动搅拌装置,转速应大
于300rmin。
(3)待系统稳定后,用注射器迅速注入示踪剂,在记录纸上作起始标记。 (4)当记录仪上显示的浓度在2min内觉察不到变化时,即认为终点己到。 (5)关闭仪器,电源,水源,排清釜中料液,实验结束。 F 实验数据处理
根据实验结果,我们可以得到单釜与三釜的停留时间分布曲线,这里的物理量 - 电导值L对应了示踪剂浓度的变化;走纸的长度方向对应了测定的时间,可以由记录仪走纸速
9
度换算出来。然后用离散化方法,在曲线上相同时间间隔取点,一般可取20个数据点左右,再由公式(5),(7)分别计算出各自的t和?,及无因次方差?????2t22tt。通过多釜串
?2联模型,利用公式(8)求出相应的模型参数n,随后根据n的数值大小,就可确定单釜和三釜系统的两种返混程度大小。
若采用微机数据采集与分析处理系统,则可直接由电导率仪输出信号至计算机,由计算机负责数据采集与分析,在显示器上画出停留时间分布动态曲线图,并在实验结束后自动计算平均停留时间、方差和模型参数。停留时间分布曲线图与相应数据均可方便地保存或打印输出,减少了手工计算的工作量。
G 结果与讨论
(1)计算出单釜与三釜系统的平均停留时间t,并与理论值比较,分析偏差原因; (2)计算模型参数n,讨论二种系统的返混程度大小; (3)讨论一下如何限制返混或加大返混程度。 H 主要符号说明
?C?t? - t时刻反应器内示踪剂浓度;f?t? - 停留时间分布密度;F?t? - 停留时间分
布函数;Lt,L∞,L(t) - 液体的电导值; n - 模型参数; t - 时间;v - 液体体积流量;
-t - 数学期望,或平均停留时间;?t2,??2 - 方差; ? - 无因次时间。
实验三 催化反应精馏法制甲缩醛
反应精馏法是集反应与分离为一体的一种特殊精馏技术,该技术将反应过程的工艺特点与分离设备的工程特性有机结合在一起,既能利用精馏的分离作用提高反应的平衡转化率,抑制串联副反应的发生,又能利用放热反应的热效应降低精馏的能耗,强化传质。因此,在化工生产中得到越来越广泛的应用。
A 实验目的
(1)了解反应精馏工艺过程的特点,增强工艺与工程相结合的观念。
(2)掌握反应精馏装置的操作控制方法,学会通过观察反应精馏塔内的温度分布,判断浓度的变化趋势,采取正确调控手段。
10
(3)学会用正交设计的方法,设计合理的实验方案,进行工艺条件的优选。 (4)获得反应精馏法制备甲缩醛的最优工艺条件,明确主要影响因素。 B 实验原理
本实验以甲醛与甲醇缩合生产甲缩醛的反应为对象进行反应精馏工艺的研究。合成甲缩醛的反应为: 2CH3OH?CH2O?C3H8O2?H2O (1)
该反应是在酸催化条件下进行的可逆放热反应,受平衡转化率的限制,若采用传统的先反应后分离的方法,即使以高浓度的甲醛水溶液(38—40%)为原料,甲醛的转化率也只能达到60%左右,大量未反应的稀甲醛不仅给后续的分离造成困难,而且稀甲醛浓缩时产生的甲酸对设备的腐蚀严重。而采用反应精馏的方法则可有效地克服平衡转化率这一热力学障碍,因为该反应物系中各组分相对挥发度的大小次序为:?甲缩醛??甲醇??甲醛??水,可见,由于产物甲缩醛具有最大的相对挥发度,利用精馏的作用可将其不断地从系统中分离出去,促使平衡向生成产物的方向移动,大幅度提高甲醛的平衡转化率,若原料配比控制合理,甚至可达到接近平衡转化率。
此外,采用反应精馏技术还具有如下优点:
(1) 在合理的工艺及设备条件下,可从塔顶直接获得合格的甲缩醛产品。 (2) 反应和分离在同一设备中进行,可节省设备费用和操作费用。 (3) 反应热直接用于精馏过程,可降低能耗。
(4) 由于精馏的提浓作用,对原料甲醛的浓度要求降低,浓度为7%—38%的甲醛水溶液均可直接使用。
本实验采用连续操作的反应精馏装置,考察原料甲醛的浓度、甲醛与甲醇的配比、催化剂浓度、回流比等因素对塔顶产物甲缩醛的纯度和生成速率的影响,从中优选出最佳的工艺条件。实验中,各因素水平变化的范围是:甲醛溶液浓度(重量浓度) 12% — 38%,甲醛:甲醇(摩尔比)为1:8—1:2 ,催化剂浓度 1%—3%,回流比 5 — 15。由于实验涉及多因子多水平的优选,故采用正交实验设计的方法组织实验,通过数据处理,方差分析,确定主要因素和优化条件。
C 预习与思考
(1) 采用反应精馏工艺制备甲缩醛,从哪些方面体现了工艺与工程相结合所带来的优势?
(2) 是不是所有的可逆反应都可以采用反应精馏工艺来提高平衡转化率?为什么?
11
(3) 在反应精馏塔中,塔内各段的温度分布主要由哪些因素决定?
(4) 反应精馏塔操作中,甲醛和甲醇加料位置的确定根据什么原则?为什么催化剂硫酸要与甲醛而不是甲醇一同加入?实验中,甲醛原料的进料体积流量如何确定?
(5) 若以产品甲缩醛的收率为实验指标,实验中应采集和测定哪些数据?请设计一张
实验原始数据记录表。
(6) 若不考虑甲醛浓度、原料配比、催化剂浓度、回流比这四个因素间的交互作用,请设计一张三水平的正交实验计划表。
D 实验装置及流程
实验装置如图3所示。反应精馏塔由玻璃制成。塔径为25 mm,塔高约2400 mm,共分为三段,由下至上分别为提馏段、反应段、精馏段,塔内填装弹簧状玻璃丝填料。塔釜为1000ml四口烧瓶,置于1000W电热碗中。塔顶采用电磁摆针式回流比控制装置。在塔釜,塔体和塔顶共设了五个测温点。
原料甲醛与催化剂混合后,经计量泵由反应段的顶部加入,甲醇由反应段底部加入。用气相色谱分析塔顶和塔釜产物的组成。
E 实验步骤 (1) 原料准备:
1) 在甲醛水溶液中加入1%、2%、3%的浓硫酸作为催化剂。
2) CP级或工业甲醇。
(2) 操作准备:检查精馏塔进出料系统各管线 上的阀门开闭状态是否正常。向塔釜加入400ml,
图3 催化精馏实验装置
1–电热碗;2–塔釜;3–温度计;4–进料口;
5–填料;6–温度计;7–时间继电器; 8–电磁铁;9–冷凝器;10–回流摆体; 11–计量杯;12–数滴滴球;13–产品槽; 14–计量泵;15–塔釜出料口;16–釜液贮瓶;
约10%的甲醇水溶液。调节计量泵,分别标定原料甲醛和甲醇的进料流量,甲醇的体积流量控制在4—5 ml/min。
(3) 实验操作:
12
(4) 预先将硫酸催化剂按规定的浓度配入甲醛原料中,调节计量泵,分别标定甲醛和甲醇的进料流量;
(5) 检查精馏塔进出料系统各管线上的阀门开闭状态是否正常(接通进料管线,关闭塔顶、塔釜采出管线上的考克,并关闭回流比分配器开关),向塔釜中加入400ml的10%左右的甲醇水溶液(釜容量的20%左右);
(6) 先开启塔顶冷却水,再开启塔釜加热器,加热量逐步增加,不宜过猛。当塔顶有冷凝液后全回流操作20min;
(7) 开始进料,甲醛由反应段的上端加入,甲醇由反应段的下端加入,同时将回流比控制在预定值。观察并记录塔内各点的温度变化,现场测定塔顶出料速度,调节塔釜加热量,使塔顶出料量达到预定值。待温度稳定后,每隔10min取样分析1次塔顶组成,共取样2—3次,取其平均值作为实验结果;
(8) 按要求改变实验条件,重复步骤4;
(9) 实验完成后,关闭加料釜开关,将回流比调至1:1,继续塔顶采出,直至塔顶温度上升至60℃左右,关闭回流分配器开关。停止加热,先关闭塔釜加热器开关,待塔顶不再有回流液时,关闭冷却水。
注意事项
1.设定时间分配器时,为减小摆针晃动的影响,要求采出时间≥3秒;
2.每次停止加料后应将塔内甲缩醛排尽,以免影响下一次实验,将回流比调为1:1,继续塔顶采出,直至塔顶温度为60℃,关闭回流分配器开关;
3.实验结束后,将蠕动泵管卡松开,卸下胶管,同时将管内原料倒回瓶中,以免胶管变形或破裂,使蠕动泵头腐蚀。
F 实验数据处理
(1) 列出实验原始记录表,计算甲缩醛产品的收率。 甲缩醛收率计算式: ?=(D×xd+W×xw)F×xfM1××100% M0(2) 绘制全塔温度分布图,绘制甲缩醛产品收率和纯度与回流比的关系图。 (3) 以甲缩醛产品的收率为实验指标,列出正交实验结果表,运用方差分析确定最佳工艺条件。
G 实验结果讨论
13
(1) 反应精馏塔内的温度分布有什么特点?随原料甲醛浓度和催化剂浓度的变化,反应段温度如何变化?这个变化说明了什么?
(2) 根据塔顶产品纯度与回流比的关系,塔内温度分布的特点,讨论反应精馏与普通精馏有何异同。
(3) 本实验在制定正交实验计划表时没有考虑各因素间的交互影响,您认为是否合理?若不合理,应该考虑哪些因子间的交互作用?
(4) 要提高甲缩醛产品的收率可采取哪些措施? H 主要符号说明
xd—塔顶馏出液中甲缩醛的质量分率;xw—塔釜出料中甲缩醛的质量分率; xf—进料中甲醛的质量分率,g/min; g/min;W—塔釜出料的质量流率,g/min; M1、M0—甲醛,甲缩醛的分子量;η—甲缩醛的收率。
实验四 乙苯脱氢制苯乙烯
A 实验目的
了解以乙苯为原料,氧化铁系为催化剂,在固定床单管反应器中制备苯乙烯的过程;学会稳定工艺操作条件的方法。
B 实验原理 1.本实验的主副反应 主反应:
-CH2 -CH3-CH=CH2+ H2117.8 KJ/mol 副反应:
-C2H5+ C2H4
105 KJ/mol-C2H5+H2+ C2H6-31.5 KJ/mol-C2H5+H2£?£-£-£--CH3£-£-+ C2H4-54.4 KJ/mol
14
在水蒸汽存在的条件下,还可能发生下列反应:
-C2H5+2H2O£-£-£-- CH-£-3£?+CO2+
3H2
此外还有芳烃脱氢缩合及苯乙烯聚合生成焦油和焦等。这些连串副反应的发生不仅使反应的选择性下降,而且极易使催化剂表面结焦进而活性下降。
(1) 影响本反应的因素 1) 温度的影响
?H0??lnKP??H?0,乙苯脱氢反应为吸热反应,从平衡常数与温度的关系式???2?T??PRT0可知,提高温度可增大平衡常数,从而提高脱氢反应的平衡转化率。但是温度过高副反应增加,使苯乙烯选择性下降, 能耗增大,设备材质要求增加,故应控制适宜的反应温度。本实验的反应温度为:540~600℃。
2) 压力的影响
?P总乙苯脱氢为体积增加的反应,从平衡常数与压力的关系式KP?Kn??n??i??可知,当???????0时,降低总压P总可使Kn增大,从而增加了反应的平衡转化率,故降低压力有利于
平衡向脱氢方向移动。本实验加水蒸汽的目的是降低乙苯的分压,以提高平衡转化率。较适宜的水蒸汽用量为:水:乙苯=1.5:1(体积比)=8:1 (摩尔比)。
3) 空速的影响
乙苯脱氢反应系统中有平衡副反应和连串副反应,随着接触时间的增加,副反应也增加,苯乙烯的选择性可能下降,适宜的空速与催化剂的活性及反应温度有关,本实验乙苯的液空速以0.6h为宜。
(2) 催化剂:本实验采用氧化铁系催化剂其组成为:Fe2O3?CuO?K2O3?CeO2。 C 预习与思考
(1) 乙苯脱氢生成苯乙烯反应是吸热还是放热反应?如何判断?如果是吸热反应,则反应温度为多少?实验室是如何来实现的?工业上又是如何来实现的?
(2) 对本反应而言是体积增大还是减小?加压有利还是减压有利?工业上是如何来实现加减压操作的?本实验采用什么方法?为什么加入水蒸汽可以降低烃分压?
(3) 在本实验中你认为有哪几种液体产物生成?哪几种气体产物生成?如何分析?
15
-1
着FB线而变化,并将与AT线相交于G点。
这时,夹带剂的加入量称作理论恒沸剂用量,它是达到分离目的所需最少的夹带剂用量。如果塔有足够的分离能力, 则间歇精馏时 图5 恒沸精馏原理图
三元恒沸物从塔顶馏出(56℃),釜液组
成就沿着TA线向A点移动。但实际操作时,往往总将夹带剂过量,以保证塔釜脱水完全。这样,当塔顶三元恒沸物T出完以后,是出沸点略高于它的二元恒沸物,最后塔釜得到无水乙醇,这就是间歇操作特有的效果。
倘若将塔顶三元恒沸物(图中T点,56℃)冷凝后分成两相。一相为油相富含正己烷,一相为水相,利用分层器将油相回流,这样正已烷的用量可以低于理论夹带剂的用量。分相回流也是实际生产中普遍采用的方法。它的突出优点是夹带剂用量少,夹带剂提纯的费用低。
(3) 夹带剂的加入方式:夹带剂一般可随原料一起加入精馏塔中,若夹带剂的挥发度比较低,则应在加料板的上部加入,若夹带剂的挥发度比较高, 则应在加料板的下部加入。目的是保证全塔各板上均有足够的夹带剂浓度。
(4) 恒沸精馏操作方式:恒沸精馏既可用于连续操作,又可用于间歇操作。 (5) 夹带剂用量的确定:夹带剂理论用量的计算可利用三角形相图按物料平衡式求解之。若原溶液的组成为F点,加入夹带剂B以后,物系的总组成将沿FB线向着B点方向移动。当物系的总组成移到G点时,恰好能将水以三元恒沸物的形式带出,以单位原料液F为基准,对水作物料衡算,得 DXD水?FXF水 D?FXF水/XD水
夹带剂B的理论用量为 B=D?XDB
21
式中;F---进料量;D一塔顶三元恒沸物量;B――夹带剂理论用量;XFi??i组分的原料组成;XDi一塔顶恒沸物中i组成。
C 预习与思考
1.恒沸精馏适用于什么物系?
2.恒沸精馏对夹带剤的选择有哪些要求? 3.夹带剂的加料方式有哪些?目的是什么? 4.恒沸精馏产物与哪些因素有关?
5.用正己烷作为夹带剂制备无水乙醇,那么在相图上可分成几个区?如何分?本实验拟在 哪个区操作?为什么?
6.如何计算夹带剂的加入量?
7.需要采集哪些数据,才能作全塔的物料衡算? 8.采用分相回流的操作方式,夹带剂用量可否减少? 9.提高乙醇产品的收率,应采取什么措施?
10.实验精馏塔有哪几部分组成?说明动手按装的先后次序,理由是什么? 11.设计原始数据记录表。 D 实验装置与流程
实验所用的精馏柱为内径?20mm的玻璃塔,塔内分别装有不锈钢三角形填料,压延孔环填料, 填料层高1米。塔身采用真空夹套以便保温。塔釜为1000ml的三口烧瓶,其中位于中间的一个口与塔身相连,侧面的一口为测温口,用于测量塔釜液相温度,另一口作为取样口。塔釜配有350w电热碗,加热并控制釜温。经加热沸腾后的蒸汽通过填料层到达塔顶,塔顶采用一特殊的冷凝头,以满足不同操作方式的需要。既可实现连续精馏操作,又可进行间歇精馏操作。塔顶冷凝液流入分相器后,分为两相,上层为油相富含正已烷,下层富含水,油相通过溢流口,用考克控制回流量。实验流程见图6。
E 实验步骤及方法
(1) 称取100克95%(wt)乙醇(以色谱分析数据为准),按夹带剂的理论用量算出正己烷的加入量。
(2) 将配制好的原料加入塔釜中,开启塔釜加热电源及塔顶冷却水。 (3) 当塔顶有冷凝液时,便要注意调节回流考克,实验过程采用油相回流。 (4) 每隔10分钟记录一次塔顶塔釜温度,每隔20分钟,取塔釜液相样品分析,当塔
22
釜温度升到80℃时,若釜液纯度达99.5%以上即可停止实验。
(5) 取出分相器中的富水层,称重并进行分析,然后再取富含正己烷的油相分析其组成。(称出塔釜产品的质量)。
(6) 切断电源,关闭冷却水,结束实验。(实验中各点的组成均采用气相色谱分析法分析。)
F 实验数据处理
(1) 作间歇操作的全塔物料衡算,推算出塔顶三元恒沸物的组成;
(2) 根据下表的数据,画出25℃下,乙醇–水–正己烷三元系溶解度曲线,标明恒沸物组成点,画出加料线。
(3)计算本实验过程的收率。 注:图6中:1–加热锅;2–进料口;
图6 恒温精馏装置图
3–填料;4–保温管;5–温度计; 6–冷凝器;7–油水分离器;8–温度计
表3. 水–乙醇-正己烷25℃液–液平衡数据 水 相 %(mol) 水 69.423 40.227 26.643 19.803 13.284 12.879 11.732 11.271
乙醇 30.111 56.157 64.612 65.678 61.759 58.444 56.258 55.091 正己烷 0.466 3.616 8.745 14.517 22.957 28.676 32.010 33.639 水 0.474 0.921 1.336 2.539 3.959 4.940 5.908 6.529 油 相 % (mol) 乙醇 1.297 6.482 12.540 20.515 30.339 35.808 38.983 40.849 正己烷 98.230 92.597 86.124 76.946 65.702 59.253 55.109 52.622 23
G 结果与讨论
(1) 将算出的三元恒沸物组成与文献值比较,求出其相对误差,并分析实验过程产生误差的原因。
(2) 根据绘制相图,对精馏过程作间要说明; (3) 讨论本实验过程对乙醇收率的影响。
实验六 液膜分离法脱除废水中的污染物
A 实验目的
掌握液膜分离技术的操作过程;了解两种不同的液膜传质机理;用液膜分离技术脱除 废水中的污染物。 B 实验原理
液膜分离技术是近三十年来开发的技术,集萃取与反萃取于一个过程中,可以分离浓度比较低的液相体系。此技术已在湿法冶金提取稀土金属、石油化工、生物制品,三废处理等领域得到应用。
液膜分离是将第三种液体展成膜状以分隔另外两相液体,由于液膜的选择性透过,故第一种液体(料液)中的某些成分透过液膜进入第二种液体(接受相),然后将三相各自分开,实现料液中组分的分离。
所谓液膜,即是分隔两液相的第三种液体,它与其余被分隔的两种液体必须完全不互溶或溶解度很小。因此,根据被处理料液为水溶性或油溶性可分别选择油或水溶液作为液膜。根据液膜的形状,可分为乳状液膜和支撑型液膜,本实验为乳状液膜分离醋酸–水溶液。
由于处理的是醋酸废水溶液体系,所以可选用与之不互溶的油性液膜,并选用NaOH水溶液作为接受相。这样,先将液膜相与接受相(也称内相)在一定条件下乳化,使之成为稳定的油包水(W/O)型乳状液,然后将此乳状液分散于含醋酸的水溶液中(此处称作为外相)。这样,外相中醋酸以一定的方式透过液膜向内相迁移,并与内相NaOH反应生成
NaAc而被保留在内相,然后乳液与外相分离,经过破乳,得到内相中高浓度的NaAc,
而液膜则可以重复使用。
为了制备稳定的乳状液膜,需要在膜中加入乳化剂,乳化剂的选择可以根据亲水亲油
24
平衡值(HLB)来决定,一般对于W/O 型乳状液,选择HLB值为3- 6的乳化剂。有时,为了提高液膜强度,也可在膜相中加入一些膜增强剂(一般粘度较高的液体)。
溶质透过液膜的迁移过程,可以根据膜相中是否加入流动载体而分为促进迁移I型或促进迁移II型传质。
促进迁移I型传质,是利用液膜本身对溶质有一定的溶解度,选择性地传递溶质(见图1)。
促进迁移II型传质,是在液膜中加入一定的流动载体(通常为此溶质的萃取剂),选择性地与溶质在界面处形成络合物,然后此络合物在浓度梯度的作用下向内相扩散,至内相界面处被内相试剂解络(反萃),解离出溶质载体,溶质进入内相而载体则扩散至外相界面处再与溶质络合。这种形式,更大地提高了液膜的选择性及应用范围(见图2)。
料液(外相) 液膜 内相料液(外相) 液膜 内相CHAcHAcHCAcHHAc?NaOH?NaAc?HO2HAc?NaOH?NaAc?HO2
图1. 促进迁移Ⅰ型传质示意图 图2. 促进迁移Ⅱ型传质示意图
综合上述两种传质机理,可以看出,液膜传质过程实际上相当于萃取与反萃取两步过程同时进行:液膜将料液中的溶质萃入膜相,然后扩散至内相界面处,被内相试剂反萃至内相(接受相)。因此,萃取过程中的一些操作条件(如相比等)在此也同样影响液膜传质速率。
C 预习与思考
(1) 液膜分离与液液萃取有什么异同?
(2) 液膜传质机理有哪几种形式?主要区别在何处? (3) 促进迁移Ⅱ型传质较促进迁移Ⅰ型传质有哪些优势? (4) 液膜分离中乳化剂的作用是什么?其选择依据是什么? (5) 液膜分离操作主要有哪几步?各步的作用是什么? (6) 如何提高乳状液膜的稳定性? (7) 如何提高乳状液膜传质的分离效果? D 实验装置与流程
25
实验装置主要包括:可控硅直流调速搅拌器二套;标准搅拌釜两只,小的为制乳时用,大的进行传质实验;砂芯漏斗两只,用于液膜的破乳。
液膜分离的工艺流程如图3所示。
内相NaOH制传乳质乳液液膜相乳液破澄乳清废水排放澄清 NaAc溶液回收膜相重复使用
图3. 乳状液膜分离过程示意图
稀醋酸水溶液E 实验步骤及方法 (1) 实验步骤
本实验为乳状液膜法脱除水溶液中的醋酸,首先需制备液膜。 液膜组成已于实验前配好,分别为以下两种液膜: 1) 液膜1#,组成:煤油95%,乳化剂E644,5%
2) 液膜2#,组成:煤油90%,乳化剂E644,5%,TBP(载体),5%。
内相用2M的NaOH水溶液。采用HAc水溶液作为料液进行传质试验,外相HAc的初始浓度在实验时测定。
具体步骤如下:
① 在制乳搅拌釜中先加入液膜1# 70ml,然后在1600rpm的转速下滴加内相NaOH水溶液70ml(约1分钟加完),在此转速下搅拌15分钟,待成稳定乳状液后停止搅拌,待用。
② 在传质釜中加入待处理的料液450ml,在约400rpm 的搅拌速度下加入上述乳液90ml,进行传质实验,在一定时间下取少量料液进行分析,测定外相HAc浓度随时间的变化(取样时间为2、5、8、12、16、20、25分钟),并作出外相HAc浓度与时间的关系曲线。待外相中所有HAc均进入内相后,停止搅拌。放出釜中液体,洗净待用。
③ 在传质釜中加入450ml料液,在搅拌下(与②同样转速)加入小釜中剩余的 乳状液(应计量),重复步骤2。
④ 比较②,③的实验结果,说明在不同处理比( 料液(V)/ 乳液(V))下传质速率的差别,并分析其原因。
26
⑤ 用液膜2 膜相,重复上述步骤①- ④。注意,两次传质的乳液量应分别与②、③步的用量相同。
⑥ 分析比较不同液膜组成的传质速率,并分析其原因。
⑦ 收集经沉降澄清后的上层乳液,采用砂芯漏斗抽滤破乳,破乳得到的膜相返回至制乳工序,内相NaAc进一步精制回收。
(2) 分析方法:
本实验采用酸碱滴定法测定外相中的HAc浓度,以酚酞作为指示剂显示滴定终点。 F 实验数据处理
(1) 外相中HAc浓度CHAc CHAc?#
CNaOH?VNaOH
VHAc - 标准NaOH溶液滴定ml数;
式中:CNaOH-标准NaOH溶液的浓度(M);VHOaN; VHAc - 外相料液取样量(ml)
(2) 醋酸脱除率 ?=C0?Ct?100% C0式中:C代表外相HAc浓度,下标0,t,分别代表初始及瞬时值。
实验七 二元系统汽液平衡数据的测定
在化学工业中,蒸馏、吸收过程的工艺和设备设计都需要准确的汽液平衡数据,此数据对提供最佳化的操作条件,减少能源消耗和降低成本等,都具有重要的意义。尽管有许多体系的平衡数据可以从资料中找到,但这往往是在特定温度和压力下的数据。随着科学的迅速发展,以及新产品,新工艺的开发,许多物系的平衡数据还未经前人测定过,这都需要通过实验测定以满足工程计算的需要。此外,在溶液理论研究中提出了各种各样描述溶液内部分子间相互作用的模型,准确的平衡数据还是对这些模型的可靠性进行检验的重要依据。
A 实验目的
(1) 了解和掌握用双循环汽液平衡器测定二元汽液平衡数据的方法;
(2) 了解缔合系统汽–液平衡数据的关联方法,从实验测得的T–P–X–Y数据计算
27
各组分的活度系数;(3)学会二元汽液平衡相图的绘制。
蒸馏循环线B 实验原理
b以循环法测定汽液平衡数据的平衡器类型很多,但基本原理一致,如图1所示,当体系达到平衡时,a、b容器中的组成不随时间而变化,这时从a和b两容器中取样分析,可得到一组汽液平衡实验数据。
液体循环线图1 循环法测定汽液平衡 数据的基本原理示意图 C 预习与思考
(1) 为什么即使在常低压下,醋酸蒸汽也不能当作
理想气体看待? (2) 本实验中气液两相达到平衡的判据是什么?
(3) 设计用0.1 N NaOH标准液测定汽液两相组成的分析步骤、并推导平衡组成计算式。 (4) 如何计算醋酸-水二元系的活度系数? (5) 为什么要对平衡温度作压力校正?
(6) 本实验装置如何防止汽液平衡釜闪蒸、精馏现象发生?如何防止暴沸现象发生? D 实验装置
本实验采用改进的Ellis气液两相双循环型蒸馏器,其结构如图2所示。
改进的Ellis蒸馏器测定汽液平衡数据较准确,操作也较简便,但仅适用于液相和气相冷凝液都是均相的系统。温度测量用分度为0.1℃的水银温度计。
在本实验装置的平衡釜加热部分的下方,有一个磁力搅拌器,电加热时用以搅拌液体。在平衡釜蛇管处的外层与汽相温度计插入部分的外层设有上下两部分电热丝保温。另还有一个电子控制装置,用以调节加热电压及上下两组电热丝保温的加热电压。
分析测试汽液相组成时,用化学滴定法。每一实验组配有2个取样瓶,2个1ML的针筒及配套的针头,配有1个碱式滴定管及1架分析天平。实验室中有大气压力测定仪。
E 实验步骤及方法:
(1) 加料:从加料口加入配制好的醋酸–水二元溶液。
(2) 加热:接通加热电源,调节加热电压约在150~200V左右,开启磁力搅拌器,调节合适的搅拌速度。缓慢升温加热至釜液沸腾时,分别接通上、下保温电源,其电压调节在(10~15)V左右。
(3) 温控:溶液沸腾,汽相冷凝液出现,直到冷凝回流。起初,平衡温度计读数不断
28
(4) 变化,调节加热量,使冷凝液控制在每分钟60滴左右。调节上下保温的热量,最终使平衡温度逐趋稳定,汽相温度控制在比平衡温度高(0.5~1)℃左右:保温的目的在于防止气相部分冷凝。平衡的主要标志由平衡温度的稳定加以判断。
图2 改进的Ellis气液两相双循环型蒸馏器
1– 蒸馏釜;2–加热夹套内插电热丝;3–蛇管;4–液体取样口;5–进料口;
6–测定平衡温度的温度计;7–测定气相温度的温度计;8–蒸气导管;9、10–冷凝器;
11–气体冷凝液回路;12–凝液贮器;13–气相凝液取样口;14–放料口
(5) 取样:整个实验过程中必须注意蒸馏速度、平衡温度和气相温度的数值,不断加以调整,
经半小时至1小时稳定后,记录平衡温度及气相温度读数。读取大气压力计的大气压力。迅速取约8ml的气相冷凝液及液相于干燥、洁净的取样瓶中。
(6) 分析:用化学分析法分析气、液两相组成,每一组分析两次,分析误差应小于0.5%,得到WHAc汽及WHAc液两液体质量百分组成。
(7) 实验结束后,先把加热及保温电压逐步降低到零,切断电源,待釜内温度降至室温,关冷却水,整理实验仪器及实验台。
F 数据处理 (1) 平衡温度校正
测定实际温度与读数温度的校正:t实际?t观?0?00016nt观?t室
??t观: 温度计指示值;t室: 室温;n: 温度计暴露出部分的读数
29
沸点校正: tP?t实际?0?000125?t?273??760?P?
。 tP: 换算到标准大气压(0.1MPa)下的沸点;P: 实验时大气压力(换算为mmHg)(2) 将tP,WHAc汽,WHAc液输入计算机,计算表中参数。 计算结果列入下表
0 PA0 nB0nA1nA1 nA2 nB ?A ?B (3) 在二元汽液平衡相图中,将本实验附录中给出的醋酸 - 水二元系的汽液平衡数据作成光滑的曲线,并将本次实验的数据标绘在相图上。
G 结果与讨论:
(1) 计算实验数据的误差,分析误差的来源。 (2) 为何液相中HAC的浓度大于气相?
(3) 若改变实验压力,汽液平衡相图将作如何变化,试用简图表明。 (4) 用本实验装置,设计作出本系统汽液平衡相图操作步骤。 H 主要符号说明
? — 气相中组分的真正摩尔分数;下标A1、A2 — 混合平衡气相中单分子和双分
子醋酸;下标A、B 一 分别表示醋酸与水。
附录1 醋酸–水二元系汽液平衡数据的关联
No 1 2 3 4 5 6
t, x1.00 0.95 0.90 0.80 0.70 0.60 yH1.00 0.90 0.812 0.664 0.547 0.452 No 7 8 9 10 11 12 t, x0.50 0.40 0.30 0.20 0.05 0 yH0.356 0.274 0.199 0.316 0.037 0 ℃ 118.1 115.2 113.1 109.7 107.4 105.7 ℃10 4.3 103.2 102.2 101.4 100.3 100.0 附录2 醋酸–水二元系汽液平衡数据的关联
在处理含有醋酸–水的二元汽液平衡问题时,若忽略了汽相缔合计算活度,关联往往失败,此时活度系数接近于1,恰似一个理想的体系,但它却不能满足热力学一致性。如
30
果考虑在醋酸的汽相中有单分子,两分子和三分子的缔合体共存,而液相中仅考虑单分子体的存在,在此基础上用缔合平衡常数对表观蒸汽组成的蒸汽压修正后,计算出液相的活度系数,这样计算的结果就能符合热力学一致性,并且能将实验数据进行关联。
为了便于计算,我们介绍一种简化的计算方法
首先,考虑纯醋酸的汽相缔合。认为醋酸在汽相部分发生二聚而忽略三聚。因此,汽相中实际上是单分子体与二聚体共存,它们之间有一个反应平衡关系,即
2HAc???HAc?2 缔合平衡常数 K2?P2?2 (1) ?P12P?12其中?1、?2为气相醋酸的单分子体和二聚体的真正摩尔分数,由于液相不存在二聚体,所以气体的压力是单体和二聚体的总压,而醋酸的逸度则是指单分子的逸度,汽相中单体的摩尔分数为?1,而醋酸逸度是校正压力,应为 fA?P?1
?1与n1、n2的关系如下: ?1=n1
?n1?n2?现在考虑醋酸–水的二元溶液,不计入H2O与HAc的交叉缔合,则汽相就有三个组成:HAc,(HAc)2,H2O,所以 ?1=n1n1?n2?nH2O
汽相的表观组成和真实组成之间有下列关系:
??yA??n?n1?2n2?n总?2n2?nH2On总1??n1?2n2
n1?2n2?nH2O将n1?n2?nH2O?1 的关系代入上式,得 yA=2?1?2?2 (2)
1??2利用(1)和(2)经整理后得:K2P?1?2?yA???1?yA?0 (3) 用一元二次方程解法求出?1,便可求得?2和?H2O
?2?K2P?12
?H2O?1???1??2? (4) 醋酸的缔合平衡常数与温度T的关系如下:
31
lgK2??10.4205?3166/T (5) 由组分逸度的定义得:
??Py??fAAA?P?1 ???y ?A1A??? ?H2OH2OyH2O (6)
00对于纯醋酸,yA?1,?A ??10;因低压下的水蒸汽可视作理想气体,故?H2O?1,0其中?1可根据纯物质的缔合平衡关系求出:
0K2??2P??10??200 ?1+?2=1
0K2PA??10+?10?1?0 (7)
??
2解一元二次方程可得?10利用汽液平衡时组分在汽液二相的逸度相等的原理,可求出活度系数?i
P?i?Pi0?i0xi?i
00即 ?HAc?P?1PH?Ac1xHAc
0?HO?P?HOPHOxHO
2222式中饱和蒸汽压PHAc,00可由下面二式得 : PH2O0logPHAc?7.1881?0logPH2O1416.7t?211 1636.909?7.9187?t?224.92 32
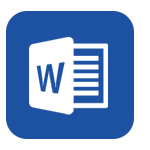





正在阅读:
化工专业实验教材04-26
施工组织设计07-03
2017年高考化学二轮复习精品资料 专题03 氧化还原反应(教学案)03-08
汉语句法分析10-02
英语单词口诀07-03
七年级(下)科学测试题(3)06-27
2015-2016学年度新译林英语五年级第一学期总复习资料07-05
终止派遣合同通知书、协议书07-04
《大学生就业指导》教学大纲05-20
县规范性文件备案制度07-08
- 多层物业服务方案
- (审判实务)习惯法与少数民族地区民间纠纷解决问题(孙 潋)
- 人教版新课标六年级下册语文全册教案
- 词语打卡
- photoshop实习报告
- 钢结构设计原理综合测试2
- 2014年期末练习题
- 高中数学中的逆向思维解题方法探讨
- 名师原创 全国通用2014-2015学年高二寒假作业 政治(一)Word版
- 北航《建筑结构检测鉴定与加固》在线作业三
- XX县卫生监督所工程建设项目可行性研究报告
- 小学四年级观察作文经典评语
- 浅谈110KV变电站电气一次设计-程泉焱(1)
- 安全员考试题库
- 国家电网公司变电运维管理规定(试行)
- 义务教育课程标准稿征求意见提纲
- 教学秘书面试技巧
- 钢结构工程施工组织设计
- 水利工程概论论文
- 09届九年级数学第四次模拟试卷
- 教材
- 实验
- 化工
- 专业
- 美标高压铸钢闸阀-Z61Y美标高压铸钢闸阀 - 图文
- 3%水泥稳定土施工方案
- 教育学基础重点复习题
- PEP Book 7 Unit5 the first period teaching plan
- 沈阳幸福基业房地产开发有限公司居住(英国宫三期)建设项目立项
- 鼎龙逸挥中学校志(修订稿201612) - 图文
- XXXXXXXX楼盘设计任务书(正式版)0318
- 机械原理(第七版) 孙桓主编 第3章
- 《电力系统分析》习题集及答案
- 计算机论文
- 2012年度获四川省建设工程天府杯奖(省优质工程)名单
- 人教版2018-2019学年 六年级数学上册全册单元测试卷
- 第五章 - 贝塞尔函数
- 10kV配电线路检修中危险点的预判及控制措施探讨
- 挑战杯 哲学社科类 全国特等奖作品汇编
- 维修电工技师问答题
- 2011计生调度会李镇长讲话
- 湖南省常德六中高二语文《伶官传序》导学案
- 盾构机笔试题库(最终版-打印) - 图文
- 商业银行流动性风险管理办法(试行含4个附件)