ERP知识点汇总
更新时间:2023-10-22 10:10:01 阅读量: 综合文库 文档下载
毛需求量 GR:是在任意给定的计划周期内,项目的总需求量。预测时区:= 预测量 计划时区:毛需求= Max(预测量,订单量)
净需求量=本时段毛需求量+安全库存量-(前一时段末的可用库存量+本时段计划接收量)>0 计划产出量=N×批量≥净需求>(N-1)×批量 PORC(t)=NR(t)+GR(t+1)+GR(t+2)+…+GR(t+n-1)固周 预计可用库存量=(前一时段末的可用库存量+本时段计划接收量+本时段计划产出量)-本时段毛需求量 可用承诺量=某期间的计划产出量(包括计划接收量)-该期间的订单总和。 时段1的ATP=当前库存量 + MPS在时段1的计划接收量 - 时段1的订单量以及在下一个计划产出量出现之前的实际需求量 其它时段的ATP = 计划接收量 - 本时段发生的订单量和随后几个时段的订单量进行合计,直到出现新的计划接收量的时段为止。如果计算出的ATP值为负时(时段1除外),把扣前面最近期的ATP(即将该时段的ATP值减去本期的负值的绝对值,同时把本期的ATP置为0)。如果不够,继续向前扣。
粗能力需求计划 RCCP的编制
粗能力计划的计划对象只是针对设置为“关键工作中心”的工作中心能力
单件总时间 = 0.09+0.0200 = 0.1100= 单件加工时间+单件准备时间
单件准备时间= 0.40÷20 = 0.0200在此例中,将生产准备时间作为变动的提前期(困为和生产批量有关)
图3工艺路线及工时定额信息表
将生产单件产品A对所有工作中心的需求分别计算
出来便得到如下表所示的产品A的能力清单。(+合计)
产品A的粗能力需求计划(+总工时)
已知产品A的MPS数据见表1。产品结构如图1,相应BOM见表2。其中,H、I、G、D是外购件,不在能力计算范围内(若某外购件因受市场供应能力或供应商生产能力限制而成为关键资源时需在RCCP中考虑)。产品A相关工艺路线资料见表3。
分时间周期的能力清单法
E(50,WC1)E(60,WC2)上述能力清单法的主要缺陷是没有很好地反映制造提前期,不能
表6 产品A在偏置期坐标轴上的横道图 体现能力需求的时间属性,对于制造提前期比较长的物料不能适B(20,WC4)期,可以绘制偏置期时间轴上的工序横道图
用。此处假设A、B、F的LT值为1期,C和E的LT值为2
F(70,WC1)A(10,WC5)C(30,WC2)C(40,WC3)偏置期OT3期2期1期0期对WC1,占用时间分别是提前3期的E的头道工序50和提前2期的F的工序70,所以,对WC1的单位负荷TP的计算需区分对应不同的偏执期,即
TP(A-WC1,OT=3)=QPAB*QPBE*TE-WC1=1*1*0.11=0.11, TP(A-WC1,OT=2)=QPAB*QPBF*TF-WC1=1*2*0.11=0.22 但对WC2,E的后道工序60和C的头道工序30占用时间
都
是
偏
执
期
为
2
期
,
所
以
TP(A-WC2,OT=2)=QPAB*QPBE*TE-WC2+ QPAC*TC-WC2 =0.63
逾期0第1期20第2期20第3期30第4期30第5期40A的MPSTP(A-WC1,OT=3)20*0.11+20*0.11+30*0.1140*0.1130*0.11TP(A-WC1,OT=2)20*0.22+30*0.2230*0.2240*0.2220*0.22总 计16.59.911.08.8
相关需求件的毛需求GR(下)=POR(上)×BOM中上下层的
单位用量关系(OP)。
例5-3 存在低层码(单一产品中)的MRP计算 物料在产品结构中处于多个层次时,对物料需求的计算需要考虑低层码。 0层 X 1层 B(1) C D(2) 2层 B(3) F
例5-4 存在低层码(多个产品)的MRP运算
当物料被多个最终产品使用时: 如果层次码<低层码:
各种最终产品对物料的毛需求汇总并保存; 如果层次码=低层码:
毛需求汇总,然后求净需求,并求计划产出量
2
紧迫系数法(SCR)CR 优先级=(交货日期-系统当前时间)/剩余的计划提前期
FCFS先到先服务 加工顺序 SOT最短作业时间 加工时间 Ddate最早交货期最先加工 LCFS后到先服务
随机 (总完成时间、平均完成时间、平均延期)
STR剩余松弛时间最短
1. 五层计划体系:这五层计划体系是经营规划,销售与运作规划,主生产计划,物料需求计划,车间作业及采购计划。在五个层次中,经营规划和销售与运作规划带有宏观规划的性质。主生产计划是宏观向微观过渡的层次。物料需求计划是微观计划的开始,是具体的详细计划,而车间作业控制或生产作业控制是进入执行或控制计划的阶段。经营规划要确定企业的经营目标和策略,为企业长远发展做出规划,下层计划人员只有反馈信息的义务,没有变动规划的权限,只能由高层领导决策。销售与运作规划是为了体现企业经营规划而制定的产品系列生产大纲,主要是人工方式进行决策并录入数据,主要用处是把经营规划中用货币表达的目标转换为用产品系列的产量来表达;制定一个均衡的月产率,以便均衡的利用资源,保持稳定生产,控制拖欠量或库存量,作为编制主生产计划的依据。销售规划不一定和生产规划完全一致。主生产计划以销售与运作规划中的运作规划为依据,将销售与运作规划中的按照金额计量的产品系统计划,进一步细化为按照数量计量的具体型号和类型的产品计划,并根据生产需求,对涉及的关键资源进行能力和负荷的平衡工作。物料需求计划对最终产品的需求数量和交货期,推导出构成产品零部件和材料的需求计划,再导出自制零件的制造订单的下达日期和采购件的采购订单发放日期,并进行需求资源和可用能力之间的进一步平衡。车间作业计划及采购计划处
是由美国著名的计算机技术咨询和评估集团Garter Group Inc.提出的一整套企业管理系统体系标准,其实质是在MRP II(Manufacturing Resources Planning,“制造资源计划”) 基础上进一步发展而成的面向供应链(Supply Chain)的管理思想;是综合应用了客户机/服务器体系、关系数据库结构、面向对象技术、图形用户界面、第四代语言(4GL)、网络通讯等信息产业成果,以ERP管理思想为灵魂的软件产品;是整合了企业管理理念、业务流程、基础数据、人力物力、计算机硬件和软件于一体的企业资源管理系统。ERP定义:ERP是指建立在IT基础上,通过标准化的数据和优化的业务操作流程,建立一个涵盖企业的内部资源和相关外部资源的共享集成信息平台,实现将企业的人、财、物、产、供、销及相应的物流、信息流、资金流进行业务集成、资源优化配臵和流程优化的目的,并为企业各级管理人员提供一个有效、科学的决策管理平台。ERP 是一种借助信息技术用以规范、集成、控制、优化、企业内外 业务流程 的 解决方案:先进的管理思想,集成的信息系统。
13. 企业信息化是指利用电子信息技术,实现企业经营、生产、管理和产品开发的自动化、集成化、智能化,让自动化的工具不仅代替人的体力劳动,而且还代替或者部分代替人的脑力劳动。ERP系统是企业信息化的核心部分。
14. ERP在国内的发展及应用:启蒙期(洋为中用,引进
MRPII),导入期(引入ERP的概念),发展期,普及期。ERP的目标:(1)规范的数据,优化的业务流程(2)集成的企业信息平台(3)资源的优化配臵。ERP管理思想:事先计划与事中控制的思想,企业供应链管理的思想,信息集成的思想。“一个计划”是ERP的原则。
15. 。独立需求:某项物料的需求量不依赖于企业内其他物料的需求量而独立存在。相关需求:某项物料的需求量可由企业内其他物料的需求量来确定。
16. MRP系统的目标是:围绕所要生产的产品,应当在正确的时间、正确的地点、按照规定的数量得到真正需要的物料;通过按照各种物料真正需要的时间来确定订货与生产日期,以避免造成库存积压. 主生产计划(根据客户订单结合市场预测制定出来的各产品的排产计划)
17. MRPII是一个围绕企业的基本经营目标,以生产计划为主线,对企业制造的各种资源进行统一的计划和控制,使企业的物流、信息流、资金流流动畅通的动态反馈系统。MRP II系统实现了物流、信息流与资金流在企业管理方面的集成,并能够有效地对企业各种有限制造资源进行周密计划,合理利用,提高企业的竞争力。
18. ERP 的核心思想:两个集成— 内部集成:产品研发、核心业务、数据采集集成— 外部集成:企业与供需链上所有合作伙伴的集成..内外集成基础上实现:— 设计、管理、监控、优
化整个供需链 — 合作竞争、协同商务
19. 提前期是指某一工作的时间周期,即从工作开始到工作结束所需的时间长度。固定提前期是不论批量大小,都以一定时间为提前期,它适合于用作采购零部件和原材料的提前期。 变动提前期是提前时间的长短随着每批加工量大小而变动的,它适合于用作自制件的提前期。生产准备提前期,是从生产计划开始到生产准备完成(可以投入生产)所需的时间。采购提前期,是采购订单下达到物料完工入库的全部时间。生产加工提前期是生产加工投入开始(生产准备完成)至生产完工入库的全部时间(排队时间,准备时间,加工时间,等待时间,传送时间)装配提前期是装配投入开始至装配完工的全部时间。累计提前期是采购、加工、装配提前期的总和。总提前期是指产品的整个生产周期,包括产品设计提前期、采购提前期以及加工、装配、试车、检测、发运等提前期的总和。 20. 四种典型的生产类型:订单设计(ETO特点:按用户需求设计并制造产品变异性大、标准化程度差、批量小甚至单件在生产过程中,每一项工作都要特殊处理管理难度大)订单生产(MTO)订单组装(ATO按用户需求进行装配最终产品变异性大、依据客户需求而定 产品由标准零部件构成、零部件的生产可以按批量进行)现货生产(MTS按库存组织生产产品标准化程度高、都由标准的零部件构成、可以按批量进行)
确定MPS物料:在不同的生产方式下,MPS物料可以是最终销售的产成品,也可能是组件或模块化的物料,甚至可以是产品结构中最低层次上的某些零件和原材料。MTS环境下,指产品,备品备件等独立需求项目MTO环境下,若交货期比产品生产提前期长,则MPS就是这些最终产品;否则就需预测产品的需求,则产品的零部件或一些重要原材料就成为MPS物料 。ATO的环境下,若产品是一个系列,结构基本相同,都是由若干组件和一些通用件组成,每项基本组件又可有多种可选件,从而可形成一系列多种规格的变型产品,在这种情况下,MPS物料指基本组件和通用件。
21. 毛需求量 GR:是在任意给定的计划周期内,项目的总需求量。计划接收量 SR:指正在执行的订单量。净需求 NR:指任意给定的计划周期内,某项目实际需求数量。计划投入量, POR:是系统根据计划产出量、规定的提前期和成品率计算得出的计划投入数量。预计可用库存量, PAB:是从现有库存中,扣除了预留给其他用途的已分配量,可以用于下一时段净需求计算的那部分库存。可用承诺量(ATP):可用承诺量是指在某一期间内,产品的产出数量可能会大于订单数量的差值。
22. 偏臵天数:0层的独立需求型物料,它的工艺路线中可能并不含有关键工作中心,对这个产品来讲,关键工作中心往往是由它下属低层某个零部件决定的,这个零部件使用关
键工作中心的日期同最终成品完工日期之间的时间,称为偏臵天数或提前期偏臵
23. 0层的独立需求型物料,它的工艺路线中可能并不含有关键工作中心,对这个产品来讲,关键工作中心往往是由它下属低层某个零部件决定的,这个零部件使用关键工作中心的日期同最终成品完工日期之间的时间,称为偏臵天数或提前期偏臵
24. 能力清单则描述了生产该产品所需的关键工作中心及其单位能力需求。能力清单法的流程:编制能力清单,寻找超负荷时段,平衡负荷与能力。
25. 物料需求计划:是对MPS需求按照产品结构进一步展开,把主生产计划排产的产品最终分解成各自制零部件的生产计划和采购件的采购计划。
26. MRP编码原则:以简短的文字、符号或数字、号码来代表物料、品名、规格或类别 ,以便于计算机系统对物料进行识别和处理。物料编码是物料的唯一识别代码,物料编码的基本原则:完整性原则,唯一性原则,简洁性原则,避免有意义,分类的原则,尽量避免英文字母和特殊符号。 27. 物料清单:物料清单是一个用来定义、记录与储存最终产品组成项目、成分、数量及结构的清单,它表明了产品->部件->组件->零件->原材料之间的结构关系。物料清单中定义最终产品与其组成结构的从属关系,最终产品可能是成品
或者是半成品,而组成结构指的是半成品或零件。 28. 计划BOM是主要用于预测由不同的产品特征件组合而成的产品系列。对一种产品系列的销售预测,在计划BOM中,可以分解为每种产品各自总量 的百分比,然后再确定产品的搭配 ,作为主生产计划参照的依据。
29. MRP的工作方法 :1. 全重排法,用于需求计划更新频率有限的情况下,在使用全重排法方法时,主生产计划中所列的每一个独立需求件的需求都要加以分解,每一个 BOM 文件都要被访问到,每一个库存状态记录都要经过重新处理,系统输出大量的报告。MRP 生成后会对库存信息重新计算,同时覆盖原来计算的 MRP 数据,生成的是全新的 MRP。此类MRP的生成一般是周期进行的。2.净改变法:适用于环境变化较大、需求计划更新频率较大的企业。该方法的缺点是信息处理效率较低,计算复杂,生成的时间较长。全重排法是时间触发的,周期性的,而净改变法是变动触发的、连续性的。全重排法中所有的MPS项目都被展开,每个生效的物料都被利用,每个物料的库存和订单状态都被重新计算,而净改变法只有变动的MPS项目被展开,只有部分BOM被利用到,仅重算与库存改变有关的产品项目。全重排法执行频率低、每周批次执行,系统自动清除信息错误,产生大量输出报表。而净改变法执行频率高、每日批次或随时执行,可能存在错误,MPS修订后,更改计划的工作量较少。
30. 能力需求计划是帮助企业在分析物料需求计划后产生出一个切实可行的能力执行计划的功能模块。
31. 工艺路线主要说明物料实际加工和装配的工序顺序、每道工序使用的工作中心,各项时间定额(如:准备时间、加工时间和传送时间,传送时间包括排队时间与等待时间),及外协工序的时间和费用。作用:(1)用于能力需求计划的分析计算、平衡各个工作中心的能力。(2)用于计算BOM的有关物料的提前期。(3)用于下达车间作用计划。(4)用于加工成本的计算。
32. 任务单数据:任务单是下达生产制造指令的有关单据。内容是针对经MRP运算后,或虽未经MRP运算但需要由企业自行制造的物料而下达的加工任务书。
33. 车间作业计划是在MRP所产生的加工制造定单(即自制零部件生产计划)的基础上,按照交货期的前后和生产优先级选择原则以及车间的生产资源情况(如设备、人员、物料的可用性及加工能力的大小等),将零部件的生产计划以订单的形式下达给适当的车间。
企业内部生产管理困境:决策信息实时性、准确性差? 生产上所需要的原材料不能准时供应或供应不足 ? 零部件生产不配套、积压严重 ? 产品生产周期过长,劳动生产率下降 ? 库存资金积压严重,周转期长 ? 市场和客户的需求多变、快速,使企业的经营和计划系统难以应付
制造企业管理中常见的问题:产供销严重脱节,财务与业务脱节,需求供应难沟通
企业内部生产管理问题总结:生产计划的合理性,成本的有效控制,设备的充分利用,作业的均衡安排,库存的合理管理,财务状况的及时分析技术创新,科技改造传统产业,向管理要效益。信息化则是保障先进管理落地的有效途径。 企业信息化是指利用电子信息技术,实现企业经营、生产、管理和产品开发的自动化、集成化、智能化,让自动化的工具不仅代替人的体力劳动,而且还代替或者部分代替人的脑力劳动。
ERP的侧重点也从最早的侧重于库存(物料管理)、到侧重于物流(原料、产品),再扩展到物流与资金流、信息流相结合,一直到最后的整个供应链的“三流合一”。
对于某种物料或产品,由于生产或销售而逐渐减少,当库存量降低到某预先设定的点时,即发出订货单(采购单或加工单),直至库存量降低到安全库存时,发出的订单所定购的物料(产品)刚好到达仓库,补充订购提前期内的物料消耗。发出订货的预先设臵的数值点,即为订货点。订货点数量=平均消耗速率×订货提前期 + 安全库存量。订货点的不足:订货点法本质上是按过去的经验(历史记录)预测未来某物料的需求,并相应进行提前订货以避免缺货现象发生而提出的一种方法。 适用于需求或消耗量比较稳定的物料。适用订
货点法的物料需满足以下条件:1、物料的消耗相对稳定;2、物料的供应比较稳定;3、物料的需求是独立的;4、物料的价格不是太高。所以得出订货点法的假设:(1) 各种物料需求相对独立(1.订货点法不考虑物料之间的关系,每项物料的订货点分别独立地加以确定。2. 但是,制造业物料需求的一个特点就是物料的数量必须是配套的,以便能装配成产品3. 结果是,单项物料的供货率虽然提高了,但是总的供货率却降低了。)(2)物料需求的连续性(1.根据订货点法的假定,其认为需求相对均匀,库存消耗率稳定。而实际生产过程中,零件的需求恰恰是不均匀的,不稳定的。库存消耗是间断的,这往往是由于下道工序的批量要求引起的。2. 订货点法根据平均消耗速率来间接地指出需要时间。3. 结果是,对于很多不连续的非独立需求物料来说,采用订货点法管理时,系统下达订货的时间或者偏早(造成库存积压),或者偏晚(造成库存短缺)。(3)库存消耗后应被立即重新填满(1. 按照这种假定,当物料库存量低于订货点时,就必须发出订货,以重新填满库存。2. 但如果需求是间断的,那么这样做不但没有必要,而且也不合理。因为很可能因此而造成库存积压。(4)提前期已知且固定(1.订货点法一个重要假设,但在现实中,很多的物料的现实情况并非如此。) 时段式MRP与订货点法的区别: (1)通过产品结构表(BOM)将所有物料的需求联系起来;(订货点法是孤立地推测每项物料的需求量,从而造
成库存积压和物料短缺同时出现的不良局面。MRP通过产品结构把所有物料的需求联系起来,考虑不同物料的需求之间的相互匹配关系,从而使各种物料的库存在数量和时间上趋于合理。)(2)将物料需求区分为独立需求和相关需求并分别加以处理;(订货点法不考虑物料项目之间的关系,认为各种物料的需求是相互独立的. MRP把所有物料按需求性质区分为独立需求项和非独立需求项,并分别加以处理。)(3)对物料的库存状态数据引入了时间分段的概念。
(所谓时间分段,就是给物料的库存状态数据加上时间坐标,按具体的日期或计划时区记录和存储库存状态数据。 MRP基本原理是:在已知主生产计划(根据客户订单结合市场预测制定出来的各产品的排产计划)的条件下,根据产品结构(产品物料清单(BOM))、制造工艺流程、产品交货期以及库存状态等信息由计算机编制出各个时间段各种物料的生产及采购计划。
MRP管理模式为实现准时生产、减少库存的基本方法是:将企业产品中的各种物料分为独立物料和相关物料,并按时间段确定不同时期的物料需求;基于产品结构的物料需求组织生产,根据产品完工日期和产品结构制定生产计划,从而解决库存物料订货与组织生产问题。MRP系统的目标是:围绕所要生产的产品,应当在正确的时间、正确的地点、按照规定的数量得到真正需要的物料;通过按照各种物料真正需
要的时间来确定订货与生产日期,以避免造成库存积压。生产加工提前期是生产加工投入开始(生产准备完成)至生产完工入库的全部时间。
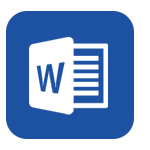





正在阅读:
ERP知识点汇总10-22
诗歌朗诵12-06
伊金霍洛旗第四中学简介12-09
郑州绿博园的现状、存在问题及解决对策06-19
2022考研英语大纲词汇排查文档(一)04-24
乡镇行政执法自查工作总结大全08-23
2 齿轮的设计及校核01-18
400字大学生自我鉴定范文07-25
电极电势-习题01-17
- 高一物理牛顿运动定律全套学习学案
- 水处理一级反渗透加还原剂亚硫酸氢钠后为什么ORP会升高
- 毕业设计(论文)-正文董家口 - 图文
- 荣盛酒店经营管理公司录用通知及入职承诺书II
- 第二讲 大学英语四级快速阅读技巧
- 质量管理体系文件(2015年委托第三方医药物流配送企业专用版本)
- 214071收款办法
- 苏轼对《文选》选文的评价
- 《诊断学基础B》1-8作业
- 广东省东莞市高一数学下学期期末教学质量检查试题
- 海南电网公司VIS推广应用管理办法
- 红星照耀中国习题
- 苏教版小学语文六年级上册期末复习资料之生字词整理
- 局域网组建与应用—王向东
- 税务稽查内部管理文书样式
- 环保社会实践调查表
- 九年级思品第一单元复习
- 2016年全国注册咨询工程师继续教育公路路线设计规范试卷
- 毕业设计-青岛港董家口港区防波堤设计
- 撞背锻炼方法与益处
- 知识点
- 汇总
- ERP
- 新视野大学英语第三版读写教程第三册课文翻译
- 高等数学轻松解决高考压轴题,助现处于120左右却始终无法突破140这个大瓶颈的资优生一举突破140瓶颈!!!
- 新课改下的数学教学反思
- 关注水资源,保护母亲河 - 图文
- 天花开裂原因
- 无刷直流电机控制系统的设计 - 图文
- 白腐真菌
- 浅谈设计美学
- 新视野大学英语第二版读写教程(第四册)Unit 1~Unit 10 答案
- 陆修静在庐山
- 土建专业岗位人员基础知识
- 机修工安全生产目标责任书
- 官员雷人语录
- 现代大学英语精读3 - unit - 6课后答案
- 实验室人数统计课程设计 甄苗军
- 规范11-常用电路
- 临电临水设计参考手册 第二版 - 图文
- 状态空间描述的概念
- 化学镍金(ENIG)常见问题讨论
- 全国职业资格证书种类汇总