机械工程英语原文+翻译
更新时间:2023-10-11 13:13:01 阅读量: 综合文库 文档下载
Unit 6 Injection Molding
Injection molding (Fig 6.1) is the predominant process for fabrication of thermoplastics into finished forms, and is increasingly being used for thermosetting plastics, fiber-filled composites, and elastomers.
It is the process of choice for tremendous variety of parts ranging in weight from 5g to 85g. It is estimated that 25% of all thermoplastics molded. If newer modification, such as reaction injection molding, and the greatly increased rate of adoption of plastics as substitutes for metals are considered, it is likely that the worldwide industrial importance of injection molding will continue to increase. Currently, probably close to half of all major processing units is injection molding machines. In 1988, a dollar sale of new injection molding machinery in the U.S. was approximately 65% of total major polymer machinery sales volume; this included 4,600 injection molding units. The machines and their products are ubiquitous and are synonymous with plastics for many people.
A reciprocating screw injection molding machine combines the functions of extruder and a compressive molding press. It takes solid granules of thermoplastic resin, melts and pressurizes them in the extruder section, forces the melt at high velocity and pressure through carefully designed flow channels a cooled mold, then ejects the finished part(s), and automatically recycles. This machine is a descendant of the plunger type “stuffing machine” patented by the Hyatt brothers in 1872 to mold celluloid. In 1878, the Hyatts developed the first multicavity mold, but it was not until 1938 that Quillery (France) patented a machine incorporating a screw to plasticize the elastomer being molded. In 1956, Ankerwerk Nuremberg commercialized the modem reciprocating screw injection molding machine for thermoplastics. Today, over 50 machine manufacturers are listed in Modern Plastics Encyclopedia, offering machines to the U.S. market ranging from 2 to 6,000 tons clamping capacity. (A machine with a 10,000-ton capacity has been built to mold 264-gallon HDPE trash containers.) A host of suppliers of auxiliary equipment, molds, instruments, and controls service this major segment of the polymer industry.
Injection molding is particularly worthy of intensive study because it combines many areas of interest extrusion, mold design, rheology, sophisticated hydraulic and electronic controls, robotic accessories, design of complex products, and, of course, the integration of materials science and process engineering. The objectives of injection molding engineers are simple enough: to obtain minimum cycle time with minimum scrap, to attain specified product performance with assurance, to minimize production costs due to downtime or any other reasons, and to steadily increase in expertise and competitiveness. Profit margins for
1
custom injection molders are said to be generally skimpy; an established way to improve profits is to be selected for more demanding, higher margin jobs demand the highest level of efficiency and competence.
This text will concentrate on the reciprocating screw machine thermoplastics, which has largely replaced the older reciprocating plunger types except for very small-capacity machines.
Injection Molding Materials
It is not possible to injection-mold all polymers. Some polymers like PTFE (Poly-tetre-fluoro-ethylene), cannot be made to flow freely enough to make them suitable for injection molding. Other polymers, such as a mixture to resin and glass fiber in woven or mat form, are unsuitable by their physical nature for use in the process. In general, polymers which are capable of being brought to a state of fluidity can be injection-molded.
The vast majority of injection molding is applied to thermoplastic polymers. This class of materials consists of polymers which always remain capable of being softened by heat and of hardening on cooling, even after repeated cycling. This is because the long-chain molecules of the material always remain as separate entities and do not from chemical bonds to one another. An analogy car, be made to a block of ice that can be softened (i.e. turned back to liquid), poured into any shape cavity, and then cooled to become a solid again. This property differentiates thermoplastic materials from thermosetting ones. In the latter type of polymer, chemical bonds are formed between the separate molecule chains during processing. In this case the chemical bonding referred to as cross linking is the hardening mechanism.
In general, most of the thermoplastic materials offer high impact strength, corrosion resistance, and easy processing with good flow characteristics for molding complex designs. Thermoplastic are generally divided into two classes: namely crystalline and amorphous. Crystalline polymers have an ordered molecular arrangement, with a sharp melting point. Due to the ordered arrangement at molecules, the crystalline polymers reflect most incidents light and generally appear opaque. They also undergo a high shrinkage or reduction in volume during solidification. Crystalline polymers usually are more resistant to organic solvents and have good fatigue and wear-resistant properties. Crystalline polymers also generally are denser and have better mechanical properties than amorphous polymers. The main exception to this ruler is polycarbonate, which is the amorphous polymer of choice for high-quality transparent molding, and has excellent mechanical properties.
2
The mechanical properties of thermoplastics, while substantially lower than those of metals, can be enhanced for some applications through the addition of glass fiber reinforcement. This takes the form of short-chopped fibers, a few millimeters in length, which are rsndomly mixed with the thermoplastic resin.
The fibers occupy up to one third of the material volume to considerably improve the material strength and stiffness. The negative effect of this reinforcement is usually a decrease in impact strength and an increase in abrasiveness. The latter also has an effect on processing since the life of the mold cavity reduced from1,000,000 parts for plain resin parts to about 300,000 for glass-filled parts.
Perhaps the main weakness of injection-molded parts is the relatively low service temperatures to which they can be subjected. Thermoplastic components an only rarely be operated continuously above 250℃, with an absolute upper service temperature of about 400℃. The temperature at which a thermoplastic can be operated under load can be defined qualitatively by the heat deflection temperature. This is the temperature at which a simply supported beam specimen of the material, with a centrally applied load, reaches a predefined. The temperature value obviously depends upon the conditions of the test and the allowed deflection and for this reason, the test value are only really useful for comparing different polymers.
Cycle of Operation
The reciprocating screw injection molding machine is considered as consisting of two: a fixed injection side, and a movable clamp side. The injection side-contain the extruder that receives solid resin in pellet or granular form and converts it into a viscous liquid or melt that can be forced through the connecting nozzle, spine, and runners to the gates that lead into the mold cavities. The mold is tightly clamped against injection pressure and is cooled well below the melt temperature of the thermoplastic. When the parts in the cavities have cooled sufficiently the mold halves are opened at the mold parting plane and the parts ejected by a knockout system drop into a receiving bin below. This summarizes the overall cycle, but leaves out much vital detail that is necessary for understanding the process. However, with this introduction, it is possible to understand the advantages and disadvantages of the process.
Effects of Process Variables on Orientation
In injection molding, any variation in processing that keeps the molding resin hot throughout filling allows increased and, therefore, decreased orientation. Some of the steps
3
that can be taken to reduce orientation are as follows.
Faster injection (up to a point): less cooling during filling, hence a thinner initial frozen layer, lower viscosity due to shear thinning; better flow to corners; and less crystallinity all favor lower subsurface orientation. The primary effect is that the gate will freeze more quickly. At that point, orientation stops and relaxation starts.
Higher melt and mold temperature: lower melt viscosity, easier filling, and greater relaxation favor reduced orientation.
Reduced packing time and pressure: overpacking inhibits relaxation processes. Reduce gate size: larger gates take longer to freeze off and permit increased orientation.
Excessively high injection speed can cause high surface orientation and increase susceptibility to stress cracking. For example, molding that are to be electroplated, and will be subject to acid solutions during plating, must be made using very slow injection speeds to minimized surface orientation. On the other hand, the transverse motion component of the melt front in most molding can cause transverse subsurface orientation superimposed on the primary orientation, giving a desirable biaxial orientation effect.
Orientation can be seriously increased by obstruction to flow during filling of the cavity. Flow around an obstruction causes a decrease in melt front speed and leads to high local viscosity and reduced relaxation. This is also likely to occur near the end of the filling phase if gating is inadequate.
The molder must recognize the dangers of excessive fill speed, insufficient injection pressure, excessive melt temperature, and inadequate packing. These dangers are weighed against the opposing effects on orientation discussed above. Thicker parts delay cooling and increase relaxation time and tend to result in lower orientation. Thicker parts also tend to warp less. Therefore, a minimum wall thickness can be established by experience for various shapes, materials, and process combinations. Lower molecular weight broader molecular weigh distribution in thermoplastic favor lower orientation and reduced internal stress in moldings.
The skin thickness ratio is affected by process variables in the same way as one would predict for the orientation; that is, it decrease as the melt for mold temperatures and cavity pressure increases. Thensile strength and stiffness increase as skin thickness ratio increases. Microscopic examination thus provides another way of studying the process efficiently.
Advantages
1. High production rates. For example, a CD disk can be produced with a 10-12s cycle
4
in high melt flow index PC.
2. Relatively low labor content. One operator can frequently take care of two or more machines, particularly if the moldings are unloaded automatically onto conveyors.
3. Parts require little or no finishing. For example, flash can be minimized and molds can be arranged to automatically separate runners and gates from the part itself.
4. Very complex shapes can be formed. Advances in mold tooling are largely responsible.
5. Flexibility of design (finishes, colors, inserts, materials).More than one material can be molded through co-injection. Foam core materials with solid skins are efficiently produced. Thermosetting plastics and fiber-reinforced shapes are injection molded.
6. Minimum scrap loss. Runners, gates, and scrap can usually be reground. Recycled thermoplastics can be injection molded.
7. Close tolerances are obtainable. Modem microprocessor controls, fitted to precision molds, fitted to precision molds, and elaborate hydraulics, facilitate tolerances in the 0.1% range on dimensions and weights (but not without a high level of operational skills in constant attendance).
8. Makes best use of the unique attributes of polymers, such as flow ability, light weight, transparency, and corrosion resistance. This is evident from the number and variety of molded plastic products everyday use.
Disadvantages and Problems
1. High investment in equipment tools requires high production volumes.
2. Lack of expertise and good preventive maintenance can cause high startup and running costs.
3. Quality is sometimes difficult to determine immediately. For example, post-mold warpage may render parts unusable because of dimensional changes that are not completed for weeks or months after molding.
4. Attention is required on many details requiring a wide variety of skills and cross-disciplinary knowledge.
5. Part design sometimes is not well suited to efficient molding.
6. Lead time for mold design, mold manufacture and debugging trials is sometimes very long.
5
第六章 注塑成型
注塑成型主要是将热塑性材料加工成半成品的过程,也越来越多地用于热固性塑料,纤维填充复合材料,弹性体的加工。
它主要加工重量在5g~85g之间形状不规则的产品。据估计大约有25%的热塑性材料成型,如果经过修改,如注射成型,可替代金属的热塑性材料,可能使注塑成型越来越广泛的被应用。现在被广泛采用的是注塑机。在美国,1988年新型注塑机的销售额占注塑机械总额的65%,大约有4600家注塑机生产厂家。机械和注塑产品无处不在,越来越多的人开始离不开注塑产品。
注射机是使塑料塑化和均化,并在很高的压力和较快的速度下,通过螺杆和柱塞的推挤将熔料注射入模具的成型机。它利用热塑性树脂的固体颗粒,挤出机的压力使他们融化,通过精心设计的熔体流道使之进入高流速和高压力的冷却模具内,完成成型过程,回收,然后过程循环。本机是1872年凯悦兄弟的后代塑造赛璐珞发明的一种柱塞式“馅机”机械。1878年,海厄茨开发了第一个多腔模具,但直到1938年Quillery(法国)发明了一种机器装有螺杆塑化成型但是没有弹性体的模具。1956年,Ankerwerk纽伦堡商品化调制解调器用于热塑性塑料螺杆往复式注塑机。今天,超过50家机制造商都列在现代塑料百科全书中,在美国生产的注塑机有2 6000吨锁模能力。 (一个有10,000吨的能力已建机模具264加仑的高密度聚乙烯垃圾容器。)是关于辅助设备,模具,仪器仪表和控制这种聚合物服务行业的主要供应商。
注塑机值得深入研究,因为它结合了挤压工艺,模具设计,流体力学,精密液压和电子控制,机器人配置,复杂产品设计等许多领域,当然,也是材料学科和工艺技术的集成。注塑成型工程师的目标是很简单:在最小废料最小循环时间为前提的条件下,保证达到规定的产品性能,最大限度地减少生产成本,并逐步增加专业知识和竞争力。定制注塑商的利润通常说是少得可怜;必须用一个既定的方式来提高利润,追求更高利润、更大就业需求、更高效率和能力的最高水平。本文将主要介绍往复螺杆机热塑性塑料的注塑成型,它已在很大程度上取代小容量机器的类型,除了比较古老的大型往复柱塞式注塑机。 注塑成型的材料
注塑模具的材料不可能是聚合物,如聚四氟乙烯,由于这些聚合物不能作出足够的自由流动,使他们能够注塑成型。其他聚合物,如以树脂和玻璃纤维编织的混合物,是由于他们的物理性质不适合。所以一般来说,聚合物是没有流动性可以注塑成型状态的能力。
6
绝大多数的注塑材料都是热塑性聚合物。这种聚合物材料类,即使经过多次循环,它们仍有被加热软化和冷却硬化的能力。这是因为材料的长链分子始终作为独立的结构存在,然而化学键却未被破坏。例如,这种聚合物可以变成液体,浇成任何形状的空腔,然后冷却成为固体。这就是属性和热固性热塑性材料不同之处,在后一种类型的聚合物,化学键是在加工过程中形成独立的分子链。在这种情况下,化学键被称为交联,这就是是硬化的机制。
一般来说,大多数的热塑性材料具有高冲击强度,耐腐蚀,以及复杂的设计与良好的可塑性,流动特性强很容易处理。热塑性塑料一般分为两大类:即结晶和无定形。结晶聚合物具有排列的紧密的熔点分子序列。由于分子的有序排列,结晶聚合物的普遍表现为质轻和不透明。他们还出现在凝固过程中体积收缩率增加或减少。结晶聚合物通常更耐有机溶剂,具有良好的抗疲劳和耐磨损性能。结晶聚合物的密度也普遍比无定形聚合物高,有较好的力学性能。主要的例外是聚碳酸酯,它是为高品质透明无定形聚合物成型的主要选择,并具有优良的机械性能。
虽然热塑性塑料的机械性能比金属的低,但可以以采取措施增强玻璃纤维的含量,来强化裁量的机械性能。这是以短纤维的形式展现,长数毫米,这是与热塑性树脂随机混合形式。
该纤维占有体积不大,却能使材料的强度和刚度增强三分之一。这种负面影响通常是冲击强度降低,好处是耐磨性提高。后者对加工过程也有影响,因为模具腔的寿命从典型的普通树脂零件大约1,000,000件减少到玻璃纤维填充树脂零件的约300,000件。
也许,注塑件的主要缺点是工作时能承受的温度相对较低。热塑性塑料部件只有很少部分能连续运行250℃以上, 400℃是绝大部分材料的温度上限。热塑性材料可根据负荷运行温度,将其定义为热变形温度。这是在温度达到了预定义,此种材料组成简支梁的中央载荷达到预定义,比较不同的聚合物后,材料允许挠度的测试的目的是用于说明温度值取决于测试值。 循环操作
往复式螺杆注塑机被认为是由两个部分人能组成:一个是固定的注射,一个是可移动的夹子。在注射侧挤出机接收包含在颗粒或粒状的固体树脂,并将其转换成一种粘性液体,或使其熔化,可通过连接喷嘴,首先进入到高温高压的模具腔内。模具是紧紧闭合目的使注射压力和冷却温度远低于热塑性熔体的温度。当零件在腔内充分冷却时,剖分模在模具分模面处打开,推出系统将零件推出落入下面的接收容器内。这概括了整个循环,这概述了整个循环,但省略了许多对理解此工艺所必需的很重要细节。所以通本章介绍,了解这种工艺的优缺点仍是必要的。
7
加工变量对方向性的影响
在注塑成型时,整个填料过程始终保持成型树脂的高温,任何加工变化都会增加松弛作用而使方向性减少。下面是可以用于减少方向性的若干措施。
较快注塑(到点):在填料过程中冷却较少,因此初始固化层较薄,由于剪应变稀少而粘性较低;能较好地流到角落;结晶度较小;所有这些促成表面下的方向性也较低。主要效果是闸道将较快固化。这样使得方向性停止产生而松弛作用开始增加。
较高的融化和成型温度:融化粘性较低,更容易填充,较大松弛作用促成方向性减少。
减少挤压时间和压力:过度挤压会抑制松弛过程。
减小闸道尺寸:闸道越大则固化时间越长并会使方向性增加。
过高的注塑速度会引起较高的表面方向性及增加应力破裂的敏感性。例如,要电镀的注塑件在电镀时会经受酸溶液,必须采用很低的注塑速度制造以使表面方向性最小化。另一方面,大多数注塑件的融化前部横向运动部分能导致在主要方向性上有层理的表面下横向方向性,产生需要的双轴方向性效应。
在填充模腔时流动受到阻碍会极大地增加方向性。围绕障碍物流动使融化前部的速度下降并产生较高的局部粘性而减少松弛作用。如果闸道不适当,这也很可能发生在接近填充结束阶段。
注塑工必须认识过快填充速度、不足注塑压力、过高融化温度和不充分挤压的危害性。这些危害性要与上述方向性的反向效应相权衡。较厚零件会延迟冷却并且增加松弛时间,趋向于导致较低的方向性。较厚零件也有助于减少翘曲。因此,对各种形状、材料和工艺组合能通过经验来确定最小壁厚。在热塑性塑料中较小的分子量以及较宽泛的分子量分布促成方向性减少同时降低注塑件中的内应力。
外壳厚度比受加工变量影响的方式与方向性预测一样;也就是它能随融化或成型温度及模腔压力的增加而减少。拉伸强度和硬度随外壳厚度比增加而增加。因而显微镜检查提供了有效研究该工艺的另一方法。 优点
1. 高生产率:例如,一张CD盘在高融体流动指数生产控制中只需10~12s一个循环就能生产出来。
2. 相对较少的工作内容:一个操作者经常可以照看两台以上机械,尤其是当成品能自动卸到输送机上时。
3. 零件几乎不需要修整:例如,飞边可以最小化并且模具能被设计成自动将浇道和闸道从零件本身分离。
8
4. 非常复杂的形状也能成型:模具的进步很大程度上是可靠的。
5. 设计的灵活性(光洁度、颜色、插入物、材料):通过复合注塑可以成型多于一种材料。可以高效地生产带有固体外壳的泡沫型芯材料。热硬化性塑料和纤维加强形状都可以注塑成型。
6. 废料损失最小化:浇道、闸道和废料通常可以重新研磨。循环热塑性塑料可以注塑成型。
7. 能得到接近的公差:现代微处理器控制、合适的精密模具和精心制作的液压设备使得尺寸和重量的公差保持在0.1% 的范围内(但不是没有在持续照看时的高水平操作技能)。
8. 充分利用聚合物诸如流动能力、重量轻、透明和耐腐蚀等独特属性:从日常使用成型塑料产品的数量和种类就能明显看到。 缺点和存在的问题
1. 较高的设备和模具投资需要较高生产量才合算。
2. 缺少专门技术和良好的预防性维修会导致较高的启动和运行成本。 3. 质量有时难以马上确定。例如,成型后的翘曲会导致零件不能用,因为在成型后几星期甚至几个月尺寸变化都不能完成。
4. 对许多需要广泛多样性技能和交叉学科知识的细节必须加以注意。 5. 零件设计有时不能很好地适应有效率的成型。
6. 模具设计、模具制造和调试试验这些先导工作有时要花费很长时间。
9
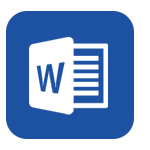





正在阅读:
机械工程英语原文+翻译10-11
IDA简易教程01-25
国内外初中思想品德教材比较分析06-27
二年级1班辅导员工作计划01-16
这件事真有趣作文350字07-12
单亲家庭的学生同伴交往存在的问题及对策07-03
16《黄山奇松》优质课教案06-10
解决WIN7下OrCAD Capture不显示窗口的问题01-05
模8计数器verilog报告11-28
- 高一物理牛顿运动定律全套学习学案
- 水处理一级反渗透加还原剂亚硫酸氢钠后为什么ORP会升高
- 毕业设计(论文)-正文董家口 - 图文
- 荣盛酒店经营管理公司录用通知及入职承诺书II
- 第二讲 大学英语四级快速阅读技巧
- 质量管理体系文件(2015年委托第三方医药物流配送企业专用版本)
- 214071收款办法
- 苏轼对《文选》选文的评价
- 《诊断学基础B》1-8作业
- 广东省东莞市高一数学下学期期末教学质量检查试题
- 海南电网公司VIS推广应用管理办法
- 红星照耀中国习题
- 苏教版小学语文六年级上册期末复习资料之生字词整理
- 局域网组建与应用—王向东
- 税务稽查内部管理文书样式
- 环保社会实践调查表
- 九年级思品第一单元复习
- 2016年全国注册咨询工程师继续教育公路路线设计规范试卷
- 毕业设计-青岛港董家口港区防波堤设计
- 撞背锻炼方法与益处
- 英语
- 机械工程
- 原文
- 翻译
- 浙江高考数学(理科卷)试题真题,历年(07年08年09年10年11年),含答案解析,完美终结版
- (7)TC3运动控制入门指南
- 200t运梁车毕业设计说明书
- 康师傅方便面市场定位分析
- 韩国国家概况
- 第三单元1 站立起来的中国人
- 经济发展应鼓励超前消费
- 公务员考试行测:积累成语 提高逻辑填空正确率
- 天大matlab 大作业 逐步回归分析方法
- 农业经济学课件
- 第8讲 盈亏问题(五年级教师版)
- 医疗机构健康体检申请书
- 雅思培训丨雅思大作文评分标准
- 南京师范大学 - 图文
- 第五章糖 代 谢 2
- 财政预算执行分析的思考及建议
- S7-200PLC编程及应用(廖常初第2版)习题参考答案报告 - 图文
- 游泳健身价值分析
- 两千成语,头尾接龙!
- 新版《建筑设计防火规范》图文解读