甲醇气化工艺设计
更新时间:2024-03-09 07:37:01 阅读量:1 综合文库 文档下载
甲醇气化工艺设计任务书
专业 化学工程与工艺 班级 化工1 设计人 孟德东 一 设计题目
题目三 年产 120 万吨煤制甲醇气化工艺设计
二 设计条件
1 生产规模
年产 120 万吨甲醇,年开工日为330天,工作小时为24小时。 2原料煤规格
原料煤的元素分析为:C 67.5%;H 4.0% ;O 10.2%;N 0.65% ;S(可燃)1.73%;S(不可燃)0.34%; Cl/(mg/kg)229;F/(mg/kg)104;Na/(mg/kg)2180;K/(mg/kg)292 。
3产品质量标准及粗甲醇组成
本产品(精甲醇)执行国家《GB338—92》标准,具体指标见下表
表1 甲醇《GB338—92》
指标 项 目 优等品 色度(铂—钴),号 ≤ 密度(200C),g/cm3 温度范围(0℃,101325Pa),℃ 沸程(包括64.6±0.10C),℃ ≤ 高锰酸钾试验,min ≥ 水溶性试验 水分含量,% ≤ 酸度(以HCOOH计),% ≤ 或碱度(以NH3计),% ≤ 羰基化合物含量(以CH2O计),% ≤ 蒸发残渣含量,% ≤
0.10 0.0015 0.0002 0.002 0.001 0.8 50 澄清 0.15 0.003 0.0008 0.005 0.003 0.791~0.792 5 0.791~0.793 64.0-65.5 1.0 30 1.5 20 0.005 0.0015 0.01 0.005 一等品 合格品 10
表2 粗甲醇组成
组分 甲醇 二甲醚 高级醇(以异丁醇计) 高级烷烃(以辛烷计) 水 粗甲醇 百分比 93.40% 0.42% 0.26% 0.32% 5.6% 100%
年产83万吨甲醇气化工艺设计
1.总论 1.1 设计概况
1.1.1 产品介绍
煤气化产物的有效组分是CO,H2 和CH4。通过调节其各自比例后广泛地应用于国民经济的不同部门,包括合成气、城市煤气、工业用燃气、联合循环发电用燃气及冶金工业还原气等。如今,国内外正在把煤化学发展成以煤炭气化为基础的碳化学工业,使煤化工由能源型逐渐转向化工型。所以,煤气化制合成气 (主要成分为CO+H2)将成为目前主要发展方向。
合成气又称化工原料气,其除了作为气体燃料使用外,另一个重要用途是作为化工合成原料,已展现出广阔的前景。由于合成气化工和碳化学技术的开发和发展,煤气化制取合成气,进而直接合成各种化工产品的工艺已成为现代煤化工的基础。
当前国内外进行合成研究的重点包含以下三个方面:
(1) 醇类:甲醇、乙醇、低碳混合醇、乙二醇; (2) 烃类:烷烃 (CH4)、烯烃、芳烃 (汽油、柴油); (3) 酸类:醋酸。
近来研究表明,大多数化工原料 (烷烃,烯烃,芳烃等)均可以用合成气直接合成,而其一次产物 (如甲醇)又可进一步合成更多不同产物。
如下图1所示。
F-T油裂解 烃类 烯烃 催化剂 H2O 甲烷 CO+H2 (合成气) 羟基合成 甲醇 H2/CO 乙醇 NH3 含氧化合物 醋酸
图1-各种合成路线
在醇类合成过程中,甲醇占据着重要的地位,它既是重要的化工原料,又是
重要的二次能源。能直接用CO+H2 合成的大部分产物,都可以通过甲醇间接制取,而且间接过程往往在技术上和经济上更简便,综合考虑本装置所生产的合成气将被应用于制取甲醇。
在烃类合成中,甲烷合成作为从合成气中脱出微量CO+CO2的手段已在合成氨等工业中得到广泛应用,现阶段大规模制取高浓度甲烷的工艺已在美国实现工业性生产。我国为了提高城市煤气的热值也正在开发低热值部分甲烷化。
液态烃的合成,即费-托合成工艺以合成气为原料,烃类及其含氧化合物,是煤液化的主要方法之一。它是煤炭间接液化的基础,其制取烯烃的直接液化过程目前还处于试验阶段,并不成熟。
醋酸的合成通常采用CH4和CO的羟基化法,用Rh-I2作催化剂。 在我国,目前合成气用量最大的是化肥工业,尤其是中小合成氨厂几乎均采用水煤气工艺,由煤制合成气作为合成氨原料。
因而,无论从近期或远景来看,煤炭气化制合成气都在我国化工工业发展以及能源安全保障中发挥着不可估量的作用。 1.1.2 简要结论
(1) 产品市场前景良好,符合国家能源发展战略和国家产业政策;工艺技术先进、成熟、可靠,能耗低,安全、卫生、环保等各项措施完善、符合国家标准; (2) 从财务分析看,所得税前内部收益率14.68%,大于行业基准收益率12%; (3) 敏感性分析表明本项目有较好的抗风险能力;
(4) 增加地区和国家税收、扩大就业岗位,拉动社会需求,促进地区社会繁荣,社会效益良好,因此本项目是可行的。
2 . 煤气化工艺
2.1 煤气化的应用及重要性
进入21世纪,为了保护中国经济的可持续发展,实施《京都议定书》减少燃煤对大气的污染,必须大力发展洁净煤技术,煤炭气化是最重要的应用广泛的洁净煤技术,是发展现代煤化工最重要的单元技术,煤炭气化可以生产工业燃料气、民用燃料气、化工合成原料气、合成燃料油原料气、氢燃料电池、煤气联合循环发电、合成天然气和火箭燃料等。
煤气化技术广泛应用于化工、冶金、机械和建材等重要工业部门和城市煤气的生产,目前中国拥有各种类型的煤气炉约有9000台,其中化工行业煤气化炉约有4000台,以固定床气化炉为主。多数中小化肥厂和少数大型化肥厂以煤炭 (焦炭)为原料,通过煤气化生产合成氨和甲醇,年耗原料煤4000多万吨,合成氨产量占全国总产量的60%以上,为中国农业生产提供了充足的化肥。因此,煤气化过去和今后在中国工农业生产和居民生活中,特别是对现代煤化工和洁净煤技术的发展占有十分重要的地位,是实现中国经济可持续发展的主要技术手段之一。
2.2 煤气化技术的现状及发展趋势
目前世界正在应用和开发的煤气化技术有数十种之多,气化炉型也是多种多样,最有发展前途的有10余种,所有煤气化技术都有一个共同的特征,即气化炉内煤炭在高温条件下与气化剂反应,使固体煤炭转化为气体燃料,剩下的含灰
残渣排出炉外。气化剂为水蒸气、纯氧、空气、CO2 和H2 。粗煤气中主要成分有CO、CO2、H2、CH4 、N2、H2O,还有少量硫化物、烃类和其他微量成分。各种煤气的组成和热值取决于煤的种类、气化工艺、气化压力、气化温度和气化剂组成。
2.2.1煤炭气化技术的发展趋势 (1) 气化压力向高压发展
气化压力由常压低压 (﹤1.0 MPa)向高压 (2.0-8.5 MPa)气化发展,从而提高气化效率、硫转化率和气化炉能力,实现气化装置大型化和能量高效利用,降低合成气的压缩能耗或实现等压合成 (如甲醇低压合成)降低生产成本。如Texaco气化压力可达6.5 MPa-8.5 MPa,Shell气化压力为2-4 MPa。 (2) 气化炉能力向大型化发展
Texaco和Shell单台气化炉气化煤量已达2000 t/d以上,prenflo气化炉单台气化煤量已达2600 t/d 。大型化便于实现自动控制和优化操作、降低能耗和操作费用。
(3) 气化温度向高温发展
Texaco气化温度1400-1500 ℃,Shell气化温度高达1400-1700 ℃,流化床气化温度为1000-1200 ℃。气化温度高煤中有机物质分解气化,消除或减少环境污染,对煤种适应性广。
(4) 不断开发新的气化技术和新型气化炉
提高硫转化率和煤气质量,降低建设投资。目前硫转化率高达98%-99%,煤气中含CO+H2 达到80%-90%。
(5) 现代煤气化技术与其他先进技术联合应用
如与燃气轮机发电组合的IGCC发电技术,高压气化 (6.5 MPa)与低压合成甲醇、二甲醚技术联合实现等压合成,省去合成气压缩机,使生产过程简化、总能耗降低。
(6) 煤气化技术与先进脱硫除尘技术相结合,实现环境友好、减少污染。
如在气化炉内加入脱硫剂(石灰石),脱硫效率可达80%-90%。采用高效除尘器使煤气中含尘降到1-2 mg/m3以下。
总之,先进的流化床、气流床煤气化技术目前已成功实现工业化和大型化,并不断改进和完善,应用范围不断扩大,是今后的主要发展方向。而固定床气化技术特别是固定床间歇式气化技术其气化效率低、能耗高、污染大,随着各气化工艺的不断发展将会被淘汰。
2.2.2国内外煤气化技术的现状和发展 1.国内煤气化技术的发展趋势
煤气化技术在中国已有近百年的历史,但仍然较落后和发展缓慢,就总体而
言,中国煤气化以传统技术为主,工艺落后,环保设施不健全,煤炭利用效率低,污染严重。目前在国内较为成熟的仍然只是常压固定床气化技术。它广泛用于冶金、化工、建材、机械等工业行业和民用燃气,以UGI、水煤气两段炉、发生炉两段炉等固定床气化技术为主。常压固定床气化技术的优点是操作简单,投资小;
但技术落后,能力和效率低,污染重,急需技术改造。如不改变现状,将影响经济、能源和环境的协调发展。
近40年来,在国家的支持下,中国在研究与开发、消化引进技术方面进行了大量工作。我国先后从国外引进的煤气化技术多种多样。通过对煤气化引进技术的消化吸收,尤其是通过国家重点科技攻关,对引进装置进行技术改造并使之国产化,使我国煤气化技术的研究开发取得了重要进展。50年代末到70年代进行了仿K-T气化技术研究与开发;70年代中科院山西煤化所开发了灰熔聚流化床煤气化工艺并取得了专利;“九五”期间华东理工大学、兖矿鲁南化肥厂、中国天辰化学工程公司承担了国家重点科技攻关项目“新型(多喷嘴对置)水煤浆气化炉开发”(22吨煤/天装置),中试装置的结果表明:有效气成分约83%,比相同条件下的Texaco生产装置高1.5~2个百分点;碳转化率>98%,比Texaco高2~3个百分点;比煤耗、比氧耗均比Texaco降低7%。 “十五”期间多喷嘴对置式水煤浆气化技术已进入商业示范阶段。“新型水煤浆气化技术”获“十五”国家高技术研究发展计划(863计划)立项,由兖矿集团有限公司、华东理工大学承担,在兖矿鲁南化肥厂建设多喷嘴对置式水煤浆气化炉及配套工程,利用两台日处理1150吨煤多喷嘴对置式水煤浆气化炉(4.0MPa)配套生产24万吨甲醇、联产71.8MW发电,总投资为16亿元。 2国内煤气化技术简介
煤气化是发展新型煤化工的重要单元技术,煤-电-化工联产是发展的重要方
向。研究表明,煤气化技术在单元工艺,中间产物,目标产品等方面有很大的互补性。将不同的工艺进行优化组合实现多联产,并于尾气发电,废渣利用等形成综合联产,达到资源能源综合利用的目的,能有效地减少工程建设投资,降低生产成本,减少污染物或废物排放。
3.国外煤气化技术的现状及发展趋势
间歇固定床气化炉( UGI) 固定床气化 UGI炉:世界上第一台气化炉是德 国于1882年设计的规范为200t/d的 煤气发生炉,1913年在德国 OPPAU建设第一套用炭制半水煤 气的常压固定层造气炉,能力为 300t/d,这种炉与后来演变成UGI 炉。 主要特点:以块状无烟煤或焦炭 为原料,以空气和水蒸气为气化剂, 在常压下生产合成原料气和燃料气。 该技术是20世纪30年代开发成功 的,设备容易制造、操作简单、投 资少。但在日益重视规模化、环境 保护和能源利用率的今天,其设备 能力低、三废量大以及必须使用无 烟块煤等缺点变得日益突出。 Lurgi加压气化炉 Lurgi加压气化炉:该技术是20世纪30年代由联邦德国鲁奇 公司开发,是目前世界上建厂数量最多的煤气化技术,主要用 于生产城市煤气和合成原料气。德国Lurgi加压气化炉压力位 2.5-4.0MPa,气化反应温度800-900 ℃,固态排渣,以小块煤 原料、蒸汽-氧连续送风制取中热值煤气。产品煤气经热回收 和除油,含有约10%~12%的甲烷和不饱和烃,适宜作城市煤气, 粗煤气经烃类分离和蒸汽转化后可作合成气。 主要特点:固态排渣,适宜弱黏结性碎煤(5-50mm);生 产能力大;结构复杂,炉内设有破黏和煤分布器、
炉箅等转动 设备,制造和维修费用大;入炉煤必须为块煤,原料来源受限 制;出炉煤气中含焦油、酚等,污水处理和煤气净化工艺复杂、 流程长、设备多,炉渣含碳5%左右。 鲁奇改进(BGL)气化炉 固定床气化BGL炉:由鲁奇公司和英国煤 气公司联合开发,将固体燃料 全部气化产生燃料气和合成气。 其工作压力为2.5-3.0MPa,气 化温度在1400-1600 ℃,超过 了灰渣流动温度,灰渣呈液态 形式排出。 主要特点:与传统Lurgi炉相比, BGL炉结构简单,取消了转动 炉箅,气化强度高,生产能力 大,水蒸气耗量低,煤气热值 提高,煤种适应性增强,碳转 化率、气化效率和热效率均有 提高,对环境的污染也减少, 在当时受到了更广泛的重视。 流化床气化流化床煤气化又称为 沸腾床气化。其以小颗 粒煤为气化原料。这些 细煤在自下而上的气化 剂作用下,保持着连续 不断和无次序的沸腾和 悬浮状态运动,迅速地 进行着混合和热交换, 其结果导致整个床层温 度组成的均一。 高温温克勒气化炉(HTW)温克勒气化炉是最早工业化的 流化床气化炉, 主要特性:① 单炉生产能力可以达到 47000m3/h,较常压移动床气 化炉要高得多; ② 对原煤要求不需筛分,备煤系 统简单; ③ 操作温度低,无运动部件、操 作维修简单,运转可靠性高; ④气化操作温度低,带出物和灰 渣中含碳量较高,因而碳利用 率不高,至今只有少数炉子在 运行。 U-Gas气化炉 U-Gas气化炉是应用灰团 聚的原理,来进行反应和 排灰的。在这种气化炉内, 允许灰成分中熔点较低的 部分先熔化,黏结其他为 熔化的灰,并形成团聚。 这种工艺的优点是不需要 熔化所有的灰,对灰渣的 流动性要求不高。这种气 化炉的灰渣比纯干式排灰 的灰渣对环境的污染小。 Kellogg-Rust Westinghouse(KRW) 气化炉KRW也是采用灰团聚的流化 床气化炉,其运行状况与UGas系统非常相似。二者主要 的差别在于底部排灰方式不同。 在KRW气化炉中,煤,氧气 (或空气)一起从底部通过一 个喷嘴喷入反应器。煤的裂解 和燃烧发生在底部喷嘴的附近。 产生的热量迅速传到整个床层。主要特点:对原煤的适应性宽 广,碳效率高、环境影响小, 炉内无运转部件,操作简便、 稳定,操作弹性大。 气流床气化气流床气化是一支并流式气化。 气化剂(氧和蒸汽)将煤粉(70% 以上的煤粉通过200目筛)夹带入 气化炉。也可将煤粉制成煤浆,用 泵送入气化炉。在气化炉内,煤炭 细粉粒与气化剂经特殊喷嘴进入反 应室,会在瞬间着火,直接发生火 焰反应,同时处于不充分的氧化条 件下。因此,其热解、燃烧以及吸 热的气化反应,几乎是同时发生的。 顺气流的运动,未反应的气化剂、 热解挥发物及燃烧产物裹挟着煤焦 粒子高速运动,运动过程中进行着 煤焦颗粒的气化反应。这种运动形 态,相当于流化技术领域里对固体 颗粒的“气流输送”,习惯上称为 “气流床气化”。 常压K-T炉常压K-T炉:K-T煤气化工艺是最早工业化的常压气流床煤气化方法,第一 台工业化K-T炉于1949年建在法国。据悉以前在西方以煤为原料生产合成氨, 有90%用K-T炉生产原料气。 优点:煤气中CO和H2产气相当高,达90%,产物中无焦油、酚及烃类,甲烷 含量甚低,生产灵活性大,可在较短时间开炉、停炉或改变生产负荷。 缺点:氧耗高,常压下操作,低活性煤较难达到高转化率,同时也带来许多 经济上和操作上的问题。 4.国外煤气化技术简介
(1)Texaco(德士古)气化炉 : 德士古气化工艺是20世纪80年 代煤气化的最新工艺之一,它是由 美国德士古公司开发的以水煤浆为 原料、液态排渣气流床加压气化技 术。原料煤与水、添加剂、石灰石 等经磨机研磨制成浓度为60%~70% 的水煤浆,由煤浆泵加压后与高压 氧气一起经烧嘴混合后,呈雾状喷
入气化炉燃烧室发生气化反应。通过调节氧和煤浆的比例,使炉内气化温度高于煤灰流动温度(FT)。 GSP气化炉GSP气化法,是下喷式加压气流床液态排 渣气化炉,操作压力2.5-3.0MPa,用粉煤、 氧气鼓风,其结构及工作原理与德士古气 化炉相类似。粉煤的气化在以氧气和蒸汽为气化剂的火焰反应中进行。物料在炉内的平均停留时 间约10s,气化火焰温度约在1800-2200℃。 反应室中有水冷壁,在耐火层表面会结一 层凝固渣层,最后形成流动渣膜,对耐火层起保护作用。特点:产品煤气高氢、高一氧化碳、低甲烷可在多种行业用作燃料气、合成气或 制氢;工艺技术简单,整个气化过程没有冷凝产物;反应速率高,气化装置生产能 力大;烧嘴和水冷壁的使用寿命较长;气化原料适应范围广;能够获得较高气化效 率和碳转化率;气化炉操作弹性大,负荷 调节灵活。
(2) Shell气化 Shell 气化炉为立式圆筒形气化炉,炉膛周 围安装有由沸水冷却管组成的膜式水冷壁,其内 壁衬有耐热涂层,气化时熔融灰渣在水冷壁内壁 涂层上形成液膜,沿壁顺流而下进行分离,采用以渣改渣的防腐办法,基本解决了高温耐火材料 损坏严重和检修频繁的难题。水冷壁与筒体外壳 之间留有环形空间,便于输入集水管和输出集汽 管的布置,便于水冷壁的检查和维修;环形空间 内充满温度为250-300℃的有压合成气。Shell煤气化工艺从示范装置到大型工业化装 置均采用废锅流程。原料煤经破碎、干燥后进入 磨煤机中被磨成粒度90%能通过170目筛孔的煤粉, 用氮气把煤粉从常压煤粉仓送到加压煤粉仓,再以 较高的固气比将煤粉送至气化炉四个喷嘴,煤粉在 喷嘴里与来自空分并预热的氧气(95%纯度)混合后 与蒸汽一起进入气化炉。由对称布置的四个燃烧 器喷入的煤粉、氧气和蒸汽的混合物在炉内迅速 发生气化反应,反应温度在1400℃~1700℃。
2.3 煤气化基本原理
煤气化,从狭义来说,即原料煤在煤气发生炉中,在高温条件下,与气化剂 (空气、氧气、水蒸汽、二氧化碳或是它们的混合物)作用产生煤气的过程。从广义上来说,是煤由固态形式转化为气态产物的过程,也就是从煤转化成煤气的过程。
2.3.1 煤气化的本质
煤气化过程的实现,必须有气化炉,原料和气化剂。气化炉是进行煤炭气化作业的主要设备;气化原料包括各种煤或焦炭;气化剂为氧气或其他含氧物质 (空气、水蒸汽、二氧化碳等)或它们的混合物。其本质如下: 焦炭 氧化 煤质大分子子 活性的不稳定的碳 气化剂 气化剂 气化剂 焦化 煤焦 挥发分 气态物(CO、H2、CH4) 图2:煤气化的本质
2.3.2 煤气化的主要反应 (1) 碳的氧化反应:
C?O2?CO2 ?H??393.8MJ/kmol
(2) 碳的部分氧化反应:
2C?O2?2CO ?H??221.2MJ/kmo l(3) 二氧化碳的还原反应:
C?CO2?2CO ?H??162.4MJ/kmo l(4) 水蒸汽分解反应:
C?H2O(g)?CO?H2 ?H??131.5MJ/kmol C?2H2O(g)?CO2?2H2 ?H??90.0MJ/kmol
(5) 一氧化碳变换反应:
CO?H2O(g)?CO2?H2 ?H??41.0MJ/kmol
(6) 碳的加氢反应:
C?2H2?CH4(7) 甲烷化反应:
?H??74.9MJ/kmol
CO?3H2?CH4?H2O?H??206MJ/kmolCO?3H2?CH4?CO2 ????247MJ/kmol
?H??165.4MJ/kmolCO?3H2?CH4?H2O2.3.3 煤气化影响因素
A 温度
对于化学平衡和化学反应速度来说,温度是一个非常敏感的因素,在气流床气化炉中,提高炉内温度提高,一方面使气化反应的速度常数增大,反应速度加快,有利于碳在瞬间完全氧化;另一方面,温度影响吸热反应平衡,使水蒸汽的分解反应平衡朝着有利于生成一氧化碳和氢气的方向移动,因而在煤气中一氧化碳和氢气的含量增加,意味着合成气质量的提高,所以一般情况下需维持较高的反应温度。但是,炉温的提高也受其它条件的制约。通常在高温状态下进行的反应,必须要考虑到气化炉的耐火材料、液渣能否顺利排放以及高温煤气的废热回收等问题。
通常化工操作中通过改变煤气化和蒸汽煤比来调节气化炉温度。 B 氧煤比
在水煤浆气化中,氧煤比是最重要的反应条件,而氧耗又是重要的经济指标,故氧煤比的调节是控制气化过程的主要手段之一。
从水煤浆气化部分氧化的化学方程可知: CmHn?m/2O2?mCO?n/2H2?热量
氧的理论用量应该与氧原子数与煤中的碳原子数相等。此时,煤浆中的碳通过部分氧化反应完全转化为一氧化碳;但如果氧的用量超过了这个比值,则一部分碳将被完全氧化,生成二氧化碳。因此,按原子数计算,氧与碳之比最高不能超过1。
氧煤比对气化过程同时存在两方面的影响:一方面,氧煤比的增加使燃烧反应放出的热量增加,炉温相对提高,有利于二氧化碳还原反应和水蒸汽分解反应的进行,增加了煤气中的有效成分,提高了碳的转化率;另一方面,氧煤比的增加,燃烧反应所生成的二氧化碳和水蒸汽量也增加,从而增加了煤气中的无用成分。考虑到上述两方面的因素,在它条件一定的情况下,氧煤比存在一个最佳值,此时,可以到最佳的气化结果。
C 蒸汽煤比
在气化剂中加入适量的水蒸汽可增加煤气中氢的含量,降低氧耗,并能控制炉膛的温度。但是,蒸汽煤比也不能过高,因为炉温的降低将不利于气化反应的进行。因此,水蒸汽的加入量与煤浆浓度以及生成气的组成要求有关。
D 反应压力
水煤浆气化炉已是近年来世界各国研究煤气化中普遍使用的方法。在高压下,
(4)煤气输送
可以降低动力消耗,便于远距离输送。
2.4.6各种气化工艺的比较
Texaco水煤浆气化技术、Shell煤气化技术、熔融床气化工艺、鲁奇加压气化炉成分及工艺比较分别见下表:
表1-1 四种煤气工艺水煤气的成分含量
成分 H2 CO CO2 CH4 H2S+COS N2 Ar
德士古 35.1 45.5 17.1 0.1 1.1 0.7 0.6
Shell 26.7 63.3 1.5 0.1 1.7 4.1 1.1
表1-2 四种煤气化工艺比较
项目 灰熔点/oC 德士古 小于1300 Shell 小于1450 水分/% 小于8 小于8(褐煤) 小于2(烟煤) 灰分/% 操作压力/MPa 操作温度/ oC 排灰方式 碳的转化率/% 原料准备 小于13 2.65-6.5 1350-1400 液态 98-99 复杂,费用高 小于13 2.0-4.0 1400-1700 液态 大于98 复杂,费用高 灰分无限制 2.0-3.1 1100-1300 固态 98 简单,费用低 小于40 2.0-3.0 900-1000 固态 88-95 简单,费用低 小于20 小于154 熔融床
34.8 26.0 10.3 5.8 0.5 0.3 0.2
鲁奇加压
38 21.5 28.5 11.2 0.7 9073
熔融床 大于1400 鲁奇加压 1600-1700 煤气水处理 较简单 简单 量大,复杂 量大,复杂 以上比较可以看出,Shell工艺在运行周期、单炉产能、变负荷能力、碳的转化率和有效气(CO+H2)含量等方面优势明显,而且在环保和资源综合利用方面也具有优势,有较好的技术发展前景,但该技术设备投资较大。中国石化集团公司和壳牌公司合作,已投资136亿美元在岳阳洞庭化肥厂建设日耗煤2 000 t的煤气化厂,以煤代油生产合成氨300 kt/a。目前还有多家采用Shell粉煤气化工艺造气用于生产合成氨的装置正在建设中。
鲁奇加压气化工艺在国内合成氨生产中已有多套工业化装置,技术成熟,运行可靠,国产化率高。但Lurgi煤气化工艺明显存在许多缺陷,导致合成工艺流程复杂,废水处理困难,环境污染严重。
Texaco工艺在我国已有近10 年的成功应用经验。水煤浆是一种由水、煤、添加剂混合制备而成的新型煤基流体环保燃料,流动性好、储存稳定、运输方便,既保留了煤的燃烧特性,又具备了类似重油的液态燃烧特点,燃烧效率高,污染物排放低,2 t水煤浆可以替代1 t燃油。[8]相比之下,Texaco工艺具有明显的优势,而且水冷激流程特别适合与合成氨、甲醇生产工艺相匹配。若将我国每年烧掉的30000 kt重油全改为水煤浆,其意义将是深远的。有关资料表明,我国每年的原油产量在1.6亿t左右,2004年中国石油进口达1亿t。因此,Texaco水煤浆气化技术是目前合成氨、甲醇生产厂家的优选工艺,将成为缓解我国石油供需矛盾和减少常规污染的主要途径。
3.工艺流程简述
3.1工艺流程说明
3.1.1 煤浆制备及输送工段
来自原料贮运系统的粒度为10mm以下的碎煤,连续送入煤仓V1101,在煤仓中储存可供4小时的用量。煤仓中的煤经煤称量给料机W1101计量后送入磨煤机M1101。
磨煤机M1101中还加入添加剂,以稳定煤浆,降低煤浆粘度。从界区外运来的添加剂(主要是造纸废液,含木质素磺酸钠)由软管注入到添加剂地下槽V1207,再由添加剂地下槽泵P1202送到添加剂槽V1202中储存,添加剂槽V1202底部设有蒸汽盘管。添加剂槽中的添加剂经添加剂给料泵P1203计量后送入磨煤机M1101。
制浆用水为渣水处理工序的冷凝液和滤液。来自渣水处理工段滤液受槽V1416的滤液经滤液泵P1409由调节阀FV1101进行流量调节后送入磨煤机M1101。气化炉未开车时,磨煤机M1101的工艺水由新鲜水补充。
煤﹑添加剂﹑工艺水按比例在磨煤机M1101中湿磨至所要求的粒度分布﹑浓度约为58~62%(WT)的水煤浆后从磨煤机M1101出口溢出,溢流出的煤浆经滚筒筛S1101滤去3mm以上的大颗粒,煤浆依靠重力自流至磨煤机出料槽V1102,由磨煤机出料槽泵P1101送至煤浆槽V1201储存,再由煤浆给料泵P1201送往气化工序。
为防止煤浆在储存过程中发生沉淀,在磨煤机出料槽V1102、煤浆槽V1201顶部分别安装有搅拌器X1101﹑X1201进行搅拌。
同时,在开﹑停车时为防止煤浆管线堵塞,还设置了冲洗水系统:来自管网的新鲜水送到冲洗水槽V1103后由冲洗水泵P1102分配到磨煤机区域﹑煤浆槽区域﹑气化框架﹑渣水处理等四个区域,冲洗时用软管连接。
磨煤单元的排放﹑冲洗﹑泄漏等废水都汇集到磨煤排放池V1203中,由磨煤排放池泵P1204送到滤液受槽V1416中,以供循环利用。
工艺流程中还考虑了用于降低煤灰熔点的石灰石工艺流程。用以改善熔渣性能的石灰石由槽车运至界区,并用气力输送至石灰储仓V1104,在石灰储仓V1104顶部设有除尘系统以防止粉尘污染,石灰石经石灰称量给料机W1102称量后送至磨煤机M1101。
3.1.2 多喷嘴对置式气化及煤气初步净化工序
由磨煤机出口槽泵来的煤浆送入煤浆槽V1201。煤浆槽有一定的标高,提供煤浆给料泵所需的入口压头。来自煤浆槽的煤浆,由两台煤浆给料泵P1201A、P1201B加压后,分别经煤浆切断阀进入工艺烧嘴X1301。投料前,煤浆经煤浆循环阀循环回煤浆槽V1201。空分装置来的纯氧,分别经氧气流量调节阀、氧气切断阀后,进入工艺烧嘴X1301的中心通道和外通道。根据安全系统要求,投料前用氧气放空方式建立氧气流量。
水煤浆和氧气通过四个对称布置在同一水平面的工艺烧嘴同轴射流进入气化炉内,气化反应的条件为~4.0MPa、~1350℃。生成的粗合成气为H2、CO、CO2及水蒸汽等的混合物。煤中的未转化组分与煤灰形成灰渣。粗合成气与灰渣一起向下,穿过洗涤冷却水分布环,沿洗涤冷却管进入洗涤冷却室的水浴中。大部分的灰渣冷却后,落入洗涤冷却室底部。粗合成气经分布器后由多层横向分隔器破泡洗涤,出洗涤冷却室,去煤气初步净化工序。
洗涤水经黑水过滤器V1309滤去可能堵塞洗涤水分布环的大颗粒,送入位于洗涤冷却管上部的洗涤水分布环。洗涤冷却室底部含渣水中含固量~1%,通过液位调节连续排出洗涤冷却室,送入含渣水处理工序。
在气化炉烘炉期间,洗涤冷却室底部水经过水封槽V1305溢流排入澄清槽V1411,在开车期间,含渣水经过开工管线去真空闪蒸。洗涤冷却室底部的粗渣经破渣机X1304破渣后排入锁斗V1307,然后定时排放。在气化炉预热期间,利用顶置的预热烧嘴进行升温,直到气化炉内温度达到要求的温度。预热烧嘴有其单独的燃料供给和调节系统。洗涤冷却室出口气体经开工抽引器X1303排入大气。通过调节预热烧嘴风门和抽引蒸汽量控制气化炉的真空度在100~800mmH2O。
气化炉燃烧室装有若干直接测量反应温度的热电偶。
工艺烧嘴在高温下工作,为了保护烧嘴,在端部有冷却盘管和水夹套,通入的冷却水连续循环流动以冷却烧嘴,防止高温损坏。脱盐水首先送入烧嘴冷却水槽V1301,由烧嘴冷却水泵P1301加压后送入烧嘴冷却水换热器E1301,然后分多路分别进入对应的工艺烧嘴的冷却盘管。出烧嘴冷却盘管的水分别进入对应的烧
嘴冷却水回水分离罐V1306。烧嘴冷却水回水分离罐V1306通入低压氮气,作为CO分析的载气。V1306的气相经放空管排入大气。在四个放空管上分别安装CO监测器,通过监测CO含量来判断烧嘴是否被烧穿,正常CO含量为0ppm。分离器的冷却水依靠重力合流返回烧嘴冷却水槽。
烧嘴冷却水系统设置了一套单独的联锁系统,在判断烧嘴端部冷却盘管和水夹套泄漏的情况下,将引起烧嘴冷却水系统四选二联锁造成气化炉联锁停车,以保护工艺烧嘴(X1301A~F)不受损坏。烧嘴冷却水泵(P1301A/B)设置了自启动功能,当出口压力低(PSL1310)则备用泵自启动。如果备用泵启动后仍不能满足要求,出口压力低低(PSLL1310),则事故冷却水槽(V1302)的事故阀(KV1309)打开短时间向烧嘴提供烧嘴冷却水。
沉积在气化炉洗涤冷却室底部的粗渣及其他固体颗粒,通过循环水流的循环作用,经锁斗安全阀、锁斗进口阀进入锁斗V1307。锁斗安全阀处于常开状态,仅当洗涤冷却室液位低低引起的气化炉停车,安全阀才关闭。锁斗循环泵P1302从锁斗顶部抽取相对洁净的水送回洗涤冷却室底部水浴,建立的循环水流携带渣进入锁斗。
锁斗循环分为收渣、泄压、清洗、排渣和充压五个阶段,一个循环的时间大约为 30 分钟。锁斗程序启动后,当排渣时间到时,循环阀打开,锁斗循环泵入口关闭,锁斗进口阀关闭,锁斗泵自身循环。锁斗泄压阀打开,渣池溢流阀关闭,锁斗开始减压,锁斗内压力泄至渣池 V1303。减压后,清洗阀打开,清洗泄压管线,设定时间到后关闭清洗阀,关闭锁斗泄压阀,打开自锁斗冲洗水罐V1308至锁斗的锁斗冲洗阀及自锁斗至渣池的锁斗出口阀,锁斗开始排渣。排渣计时器开始计时,到达预定时间后,锁斗出口阀、锁斗冲洗阀关闭。锁斗充压阀打开,用来自含渣水处理工序高温热水泵 P1402 的高压灰水对锁斗进行充压。当锁斗与气化炉之间的压差小于设定值时,充压阀关闭,锁斗进口阀重新打开。与此同时,锁斗循环泵入口阀打开,循环阀关闭,锁斗开始收渣,渣池溢流阀在锁斗出口阀关闭5min打开。全部排渣循环(泄压、清洗、排渣、充压)时间大约 2 分钟。锁斗循环重新开始。
灰水由低压灰水泵P1406经灰水冷却器E1302冷却后,通过锁斗冲洗水罐加水阀,送入锁斗冲洗水罐。冲洗水罐设置有至渣池的溢流管线。
锁斗排放出的渣水,排放至渣池前仓。大约排放5分钟后,渣池溢流阀打开,较清的渣水溢流至渣池后仓,并由渣池泵P1303将渣水送往含渣水处理工序的真
空闪蒸罐V1402。排入渣池的粗渣在前仓由刮板输送机M1301送入粗渣斗V1304,由渣车运出界区。
从气化炉洗涤冷却室出来的饱和了水蒸汽的合成气进入混合器X1403,在这里与黑水循环泵 P1401来的水洗塔黑水混合,使合成气夹带的固体颗粒完全润湿,以便从合成气中快速除去。
从黑水循环泵P1401来的黑水,一路入混合器X1403,另一路经黑水过滤器V1309过滤后进入气化炉的洗涤水分布环。
水/合成气的混合物进入旋风分离器V1408,气相中的大部分细灰进入液相,连续排出旋风分离器,进入含渣水处理工序。
出旋风分离器的合成气进入水洗塔T1401的下部,合成气向上穿过泡罩塔板,与塔中部加入的蒸发热水塔加热的循环灰水和塔上部加入的来自外界的变换高温冷凝液逆流直接接触,洗涤剩余的固体颗粒。合成气在洗涤塔顶部经过旋流板除沫器,除去夹带在气体中的雾沫,基本上不含细灰的工艺气送出水洗塔。在水洗塔出口管线设置在线分析仪,分析CH4、CO、CO2及H2。
干净的合成气经过电动阀送往变换工序。开车和停车期间,合成气经压力调节排至火炬。火炬管线连续通入N2使火炬管线保持微正压。
水洗塔底部排出的黑水,通过流量控制经减压进入含渣水处理工序。含渣水处理工序再生的灰水,经过热水塔预热返回水洗塔。黑水循环泵从水洗塔底部抽取上层黑水,送至气化炉洗涤冷却室、混合器。
开车和停车时,原水或灰水可直接送入黑水循环泵入口。 3.1.3 含渣水处理工序
含渣水处理工序的作用是将多喷嘴对置式气化及煤气初步净化工序产生的黑水所含的固体和溶解的气体分离出来,并将黑水所含的热量加以回收。
进入含渣水处理工序的黑水共有四条路线:气化炉洗涤冷却室排放、旋风分离器排放、水洗塔排放及锁斗排放。来自气化炉洗涤冷却室、旋风分离器及水洗塔底部的黑水分别经过减压后送入蒸发热水塔T1402下部蒸发室。蒸发热水塔蒸发室中,一部分水蒸发为蒸汽,连同少量溶解气体,进入蒸发热水塔上部热水室,与低压灰水泵P1406来的灰水直接接触,加热灰水,自身大部分冷凝。热水室的热水流入高温热水罐V1407,经高温热水泵P1402进入水洗塔中部。热水室未冷凝的闪蒸气去变换装置汽提塔。蒸发热水塔蒸发室底部被浓缩的黑水经液位调节阀由底侧部排出,进入低压闪蒸罐V1406进一步闪蒸,蒸汽去除氧槽V1405除氧,浓
缩后的黑水进入真空闪蒸罐V1402,来自渣池的含渣水用渣池泵P1303经过流量调节也送入真空闪蒸罐。真空闪蒸罐内进行真空闪蒸,大量溶解的气体释放出来,黑水进一步浓缩,含固量增大,温度进一步降低。真空闪蒸汽进入真空闪蒸冷却器E1402,被循环水冷却,再送入真空闪蒸分离罐V1403,从分离器顶部出来的闪蒸汽送往水环式真空泵P1412。真空闪蒸分离器底部冷凝液依靠重力送往灰水槽V1412。真空闪蒸罐底部的黑水经液位控制依靠重力送至静态混合器X1402,与来自絮凝剂槽V1413经絮凝剂泵P1410加压的絮凝剂混合后流入澄清槽V1411。
来自真空闪蒸罐的黑水送入澄清槽V1411。为了加速固体在澄清槽V1411中的沉降速率,在系统中加入了絮凝剂。絮凝剂贮存在絮凝剂槽V1413中,由絮凝剂泵P1410调节至适当流量后,经静态混合器X1402和黑水充分混合后送入澄清槽V1411。澄清槽V1411上部设置一台缓慢转动的刮渣机X1401,将沉降的固体推到澄清槽底部出口。澄清槽上部澄清水溢流,依靠重力进入灰水槽V1412。灰水经低压灰水泵P1406去蒸发热水塔T1402、锁斗冲洗水罐V1308、气化炉预热水循环和废水处理。为防止溶解固体在黑水系统中的累积,需向界外连续送出一部分灰水进行处理。此外,为了防止管道及设备结垢,在系统中还加入分散剂,分散剂贮存在分散剂槽V1415内,经分散剂泵P1414调节适当流量,送至V1411至V1412管线入口。
密封的澄清槽V1411和灰水槽V1412通低压氮气,由共同的氮封水槽V1414排放。澄清槽V1411底部的细渣和水经澄清槽底流泵P1407送往真空过滤机M1401。滤饼通过卡车送至贮放区域。滤液进入滤液授槽V1416,经滤液泵P1409送至水煤浆制备工序的磨煤机M1101。
4.德士古工艺设计及计算
4.1德士古水煤浆加压气化原理和炉内流动过程特点
德士古水煤浆加压气化属气流床,氧气和水煤浆通过德士古烧嘴混合后喷射时立即雾化进入气化炉,在0.1秒内煤浆中水被气化,煤粒子被气体隔开,各煤粒独立的进行反应,气化炉在煤灰熔点以上温度发生反应,固体在气化炉内停留3~5秒钟,反应生成的粗合成气甲烷含量减少,一般仅为0.1%以下,碳转化率高达98%,由于反应温度高,不生成渣油、酚及高级烃等可凝聚的副产物。 4.1.1德士古水煤浆加压气化原理
气化炉内发生的化学反应是很多的,在火焰中可能同时进行以下化学反应:
CmHn+(m+n/4)O2=mCO2 +n/2H2O ① 2C+O2=2CO +246.6KJ ② C+O2=CO2 +409.1KJ ③ 2CO+O2=2CO2+573.2KJ ④ H2 +1/2O2=H2O ⑤ C+H2O=CO+H2-122.7KJ ⑥ CO2+H2=CO+H2O-42.3KJ ⑦ CH4+H2O=CO+3H2-412.8KJ ⑧ C+CO2=2CO -165.0KJ ⑨ CH4=C+2H2 ⑩
此时还可能发生如下副反应:
COS+H2O=H2S+CO2 ①
C+O2+H2=HCOOH ② N2+3H2=2NH3 ③ N2+H2+2C=2HCN ④
4.1.2炉内流动过程的特点
德士古水煤浆气化过程从流动特征上讲属受限对流反应过程,按流动过程可将炉内分为三个流动区域,即对流区、回流区和管流区,每个区域的流动特征各异。在对流区中物流流动速度大,不断地与回流区进行物质交换,喷口附近回流区中的高温气体大量地被卷吸到对流区,而远离喷口区域却有大量流体离开对流区进入回流区,未离开部分流体则进入到管流区。 1、射流区反应及特征
进入射流区的介质有水煤浆和来自回流区的高温烟气,发生的过程是:雾化后的水煤浆接受炉膛辐射热并与来自回流区的高温烟气迅速混合升温,水份蒸发,挥发份逐渐放出来,在气化温度下0.1秒左右,释放出的挥发份与来自回流区CO、H2等与CO2相遇达到着火条件即发生燃烧,温度持续升高,煤中难以挥发的碳氢化合物也开始裂解,脱挥发份的过程结束后,形成的残碳呈多孔的疏松状,若此时氧未消耗完,则残碳将进行燃烧反应。
由于此区中含大量水份及氧气等,究竟发生的部分氧化反应还是燃烧反应,依据动力学研究确定:在射流区中氧气消耗完之前的区域,以生成CO2的完全燃烧反应为主(C+O2=CO2),定义为一次反应区,在氧气消耗完之后的区域,碳的各种转化反应速率相当,即过程进入到气化反应阶段,此区域与管流区一并称为二次反应区。(气化反应区) 2、管流区反应及特征
进入管流区的介质为来自一次反应区的燃烧产物及CH4、残碳、水蒸气及惰性气体等,此区中进行的反应主要是碳的非均相气化反应,甲烷水蒸气转化反应,
逆变换反应等,对比二次反应区的反应进行方向研究结果在1350℃下,有下列特点:
? 反应⑥和反应⑨反应尚未到达平衡,反映将沿着生成CO和H2的方向进行。 ? 反应⑺沿着生成CO的方向进行,即逆变换反应,生成CO和H2O。 ? CH4转化反应⑧沿着生成CO+H2的方向进行。说明气化产品气中CH4存在是由于其与水蒸气转化反应警醒的不够完全的原因,而不是进行了甲烷化反应。不难发现,随着温度的升高,甲烷转化反应平衡常数升高转性,故有提高气化温度,出口气体中CH4含量降低的说法。 3、回流区反应及特征
回流区中的介质为在对流卷吸作用下来自对流区的燃烧产物残碳、水蒸汽和少量氧气等,因而其反应包括一次反应和二次反应,此区为一、二次反应共存区。
4.2工艺计算
气化过程中,进入气化炉内的碳主要是指原料带入的碳;带出气炉的碳,则包括煤气,焦油,轻质油,酚,煤气吹出物和灰渣等。气化过程中,氢的来源包括水蒸气和原料煤中的氢;带出气化炉中的氢则包括在煤气,焦油,轻质油,酚,氨和煤气中未分解的水煤气。对于加压而言气化剂中水蒸汽的含量远远高于常压气化,煤气中未分解的水煤气的量少,同时气化时产生甲烷的量叫常压气化也多。
气化过程中氧的来源,一是原料中的化合氧,二是气化剂带入的氧;带出气化炉的氧,主要是生成煤气中的氧,以及焦油,轻质油中微量的氢。
加压气化过程过程的衡算步骤和内容基本与常压的相同. 以100kg褐煤为计算基准,已知原始数据如下. 褐煤的工业分析(%):
Mar=19.5;Aar=27.3;Var=28.2;Sar=0.36 褐煤的元素分析(%):
w(Cdaf)=72.13;w(Hdaf)=5.5; w(Odaf)=19.70;
w(Ndaf)= 1.99; w(Sdaf)=0.68 换算为收到基:
由收到无灰基转变成收到基的转换系数: K=(100- Mar - Aar)\\100
=(100-19.5-27.3)\\100 =0.532
w (Car)=67.5X0.532=35.91 w (Har)=4X0.532=2.13
w (Oar)=10.2X0.532=5.43 w (Nar)=0.65X0.532=0.35 w (Sar)=0.34X0.53=0.18
褐煤分析(%):
W(半焦)=74.98 W(焦油)=6.5
W热水解)=11.04 W(煤气及损失)=7.48
灰渣熔点:
T1=1380度; T2>1400度; T3>1420度
粗煤气:
Φ(CO2)=31.65%; Φ(O2)=0.3%; Φ(C2H4)=0.2%; Φ(H2S)=0.15%
Φ(CO)=17.4%; Φ(H2)=37.2%; Φ(CO2)=12.1%; Φ(CH4)=31.65%; Φ(N2)=1.0%
高热值:11903KJ/m3
焦油组成:
w(C)=80.0;w( H)=9.0.;w( O)=8.7;w(N)=1.0;w( S)=1.3
轻质油组成:
W(C )=85.0%; W( H)=15.0%;
副产品产率:
W(焦油)=3.96%;W(轻质油) =0.794%;W(水溶性酚)=0.52%;W(氨) =0.66%
气化条件如下: 原料粒度:6-25mm
气化炉操作压力:1.96-2.45MPa 气化炉操作温度:1000-1050℃ 水蒸气、氧气压力:2.45-2.95MPa 水蒸气温度:450-500℃ 煤气出炉温度:300℃ 带出物比例:1% 灰渣含碳量:6%
在除去1%的带出物后,100kg褐煤实际入炉的物料如下: m(Car)=38.02kg; m(Har)=2.9kg; m(Oar)=10.3kg; m(Nar)=1.08kg; m(Sar)=0.36kg; m( Mar)=19.30kg; m( Aar)=27.02kg; 在除去带出物损失后,副产品产率如下(kg ):
m(焦油)=3.92; m(轻质油)=0.786 ; m(水溶性酚)=0.515; m(氨)=0.65 (1 )物料衡算
①碳的衡算。根据碳平衡计算求粗煤气的产率。射出煤气的产率为V粗,计算如下。
a. 计算粗煤气的碳量
m(C粗)=12\\22.4 *Φ(CO2)+ Φ(CO)+ Φ(CH4)+ 2Φ(C2H4) ] =0.5357x(31.65%+17.4%+12.1%+2x0.2%) =0.3297(kg\\ m3)
b. 计算灰渣中排出的碳量。
灰渣中的碳含量以6%计,硫含量以0.35%计,则灰渣的产量为: A=100XAa\\(100-6-0.35)
=100X27.3\\(100-6-0.35)=28.85 (kg) 从灰渣中排出的碳量为: m(CA)= Ax6%=28.85x6%=1.73(kg) c. 碳平衡计算
带入气化的碳量: m(C入)=38.02(kg)
带出气化炉的含量包括下面几项。
粗煤气带出的碳量: m(C粗)=0.3297x100V粗 灰渣带出的碳量: m=1.73(kg)
焦油带出的碳量: m(C焦油)=3.92x0.8=3.136(kg) 轻质油带出来的碳量: m(C轻质油)=0.786x0.85=0.66(kg)
酚带出的碳量: m(C酚)= 0.515x72÷94=0.394(kg) 根据碳平衡m(C入)= m(C出)得:
38.02=32.97V粗+1.73+3.136+0.668+0.394
得粗煤气的产率为:V粗=(38.02-5.928)/32.97=0.973(m3/kg煤) ②氢的衡算。根据氢平衡来计算水蒸汽的分解量。
a. 计算粗煤气中的氢量。
m(H粗)=2/22.4x [Φ(H2)+ 2Φ(CH4)+ Φm/2(CnHm)+ Φ(H2S)]x100V粗 =0.0893x(37.2%+2x12.4%+2x0.2%+0.15%)x100x0.973=5.384(kg) b. 计算热解水耗氢量。设煤中含氧量的50%生成热解水,则热解水的耗
氢量为: m'(H水)=0.510.32x2\\16=0.645(kg) c. 氢平衡的计算。
原料煤带入的氢量,m(H煤)=2.9(kg )
待求的水蒸气带入的氢量设为,m(H粗)=5.384(kg) 焦油带出的氢量,m(H焦油)=3.92*0.09=0.353(kg) 轻质油带出的氢量,m(H轻质)=0.785*0.15=0.118(kg) 酚带出的氢量,m(H酚)=0.151*6÷94=0.033(kg) 氨带出的氢量,m(H氨)=0.65*3÷17=0.155(kg) 热解水带出的氢量,m‘(H水)=0.645(kg) 带出的氨量共计: m(H
出
)= m(H
粗
)+ m(H
焦油
)+ m(H
轻质
)+ m(H
酚
)+ m(H
氨
)+ m‘(H
水
)=6.648
由氢平衡 m(H入)=m(H出)得 2.9+m(H水)=6.648 所以求得水蒸气带入气化炉氢量为:m(H水)=3.748(kg) 则,水蒸气的分解量为:
m(H2o)=3.748318/2=33.732(kg)
③ 氧的衡算。通过氧的衡算,可以计算出单位原料的耗氧量。 a. 粗煤气中的氧量计算。
m(O粗)=[ φ(O2)+φ(CO2)+0.5φ(CO)] 3100V粗
=0.0142863(0.3+31.65+0.5 317.4)310030.973=56.503(kg) b. 氧平衡计算 入方
原料煤带入的氧量,煤m(O)=10.32(kg)
已分解的水蒸气带入的氧量,水m(O)= 33.732316/18=29.984(kg) 设吹风带入的氧量,风m(O)
带入的氧量共计,入m(O)=风m(O)+40.302
出方
粗煤气带出的氧量 粗m(O)=56.503(kg)
焦油带出的氧量 焦油m(O)=3.9230.087=0.341(kg) 酚带出的氧量 酚=m(O)= 0.515316/94=0.088(kg) 热解水带出的氧量 热解水m(O)0.5310.32=5.16(kg)
带出的氧量共计 m(O出)= 粗m(O)+ 焦油m(O)+ 酚m(O)+ 热解水m(O)=62.092(kg)
根据氧平衡 入m(O)= 出m(O)得:
风m(O)+40.302=62.092 风m(O)=21.79(kg) 则氧气的耗量可以换算为:
V(O2)=21.79/32322.4=15.25[m3/(100kg)] 未分解水蒸气的量近似计算如下。
取汽氧比为7kg水蒸气/1m3氧气(标准),则入炉总水蒸气量为: m 水=V(O2)37=15.2537=107[kg水蒸气/(100kg煤)] 所以未分解水蒸气量为: 107—33.732=73.268(kg) 入炉水蒸气的分解情况如表所示。
表入炉水蒸气的分解情况(以100kg入炉煤计) 项 目 数值 氢含量 氧含量 107 95.111 总水蒸气量/kg 11.889 29.984 水蒸气分解量/kg 33.732 3.748 65.127 未分解水蒸气量73.268 /kg 31.52 8.141 水蒸气分解率/% ④ 氮的衡算。加压气化过程中,氮的来源除原料中含氮的部分外,用作气化剂的工业氧气中也要带进去一部分氮;而生成物中的氮,主要包含在生成气中的氮及焦油和氨中的氮
。通过氮平衡计算,可以确定工业氧气的纯度。 入方
原料煤带入的氮量,m(N煤)=1.08 工业氧气带入的氮量设为,m(N风)
共计,m(N入)=1.08+ m(N风) 出方
粗煤气带出的氮量,m(N粗)=1/1003(28310030.973)/22.4=1.216(kg) 焦油带出的氮量,m(N焦油)=3.9230.01=0.0392(kg) 氨带出的氮量,m(N氨)=0.65314÷17=0.5353(kg) 共计 m(N出)=1.7905(kg) 根据氮平衡 m(N入))=m(N出),得到 1.08+ m(N风)=1.7905 所以 m(N风)=0.7105(kg)
换算后得: V(N风)=0.7105÷28322.4=0.5684m3/100kg煤
由此求得工业氧的纯的为:k=15.25÷﹙15.25+0.5684﹚3100%=96.5%
气化过程的物料平衡 项目 m(C)m(H)m(O)/% /% /% 入原料煤 38.4 2.93 10.3方 2 工业氧 0 0 21.79 分解水0 3.7429.9蒸气 8 84 未分解0 0 0 水蒸气 共计 38.4 6.6762.08 94 出干煤气 32.05.3856.5方 92 4 03 煤中干0 0 0 燥水 未分解0 0 0 水蒸气 热解水 0 0.645.16 5 焦油 3.130.350.346 3 1 轻质油 0.660.110 8 8 酚 0.390.030.084 3 8 氨 0 0.110 5 煤气带0.38 0.03 0.1 出物 灰渣 1.73 0 0 3804 6.678 差额误差 0 0 0 0
共计 62.092 0 0 m(N)m(S)m(A)m(M)/% /% /% /% 1.09 0.36 27.3 19.5 0.7105 0 0 1.8005 1.216 0 0 0 0.0392 0 0 0.5353 0.01 0 1.8005 0 0 0 0 0 0 0 0 0 0 73.268 92.768 0 19.3 73.268 0 0 0 0 0 0.2 0 92.768 0 0 总质量/kg 100 22.5005 33.732 73.268 229.5005 95.405 19.3 73.268 5.805 3.9172 0.786 0.515 0.6503 1 28.582 229.5005 0 0 0.36 27.3 0.21 0 0 0 0.048 0 0 0 0 0 0 0 0 0 0 0 0 0.28 0.1027.02 2 0.36 27.3 0 0 0 0 (2)热量衡算 以1000kg收到基煤为计算基准,计算如下: 1:供热方
a. 气化原料的发热量Q1为: Q1=m1Q原料=100X15666=1566600
式中m1——气化的原料气,100kg,下同
Q燃料 ——气化原料的热值,15666kj/kg b. 气化原料的显热Q2为:
Q2=c2m2t2=1.256X100X25=3140kj
式中c2 ——气化原料的比热容,kj/kg,取为1.256 t2——入炉煤的温度,25℃ c.气化剂中工业氧的显热Q3为:
Q3=c3m3t3=0.9016X22.5005X30=608.6kj 式中c3——工业氧的比热容,0.9016kj/kg.℃
m3——工业氧的消耗量,kg
t3——工业氧入炉温度,取为30℃
c. 气化剂中水蒸气的热焓Q4。查有关水蒸气表,得450℃、30kg/cm2下,过热水蒸气的焓为3344.4kj/kg,所以 Q4=107X3344.4=357850.8kj d. 炉体夹套软水带入的热量Q5。 Q5=c5m5t5=4.18X8X30=1003.2kj
式中 c5——水的比热容,4.18kj/kg.℃
m5——加入气化炉的软水的质量,取8kg t5——软水的入炉温度,取为30℃. 由以上计算,供给气化炉的总热量为:
Q=Q1+Q2+Q3+Q4+Q5=1566600+3140+608.6+357850.8+1003.2=1929202.6kj 2:付热方
气化过程生成的各项有效热量与所有的热损失之和,为热量衡算的付热方,由以下几项组成:
a.生成的煤气热量Q6为:
Q6=100V粗X2843X4.178=100X0.973X11903=1158162kj 式中 V粗——粗煤气的产率,0.973m3/kg煤 11903——粗煤气的发热量,kj/m3
b.生成煤气的显热Q7为:
Q7=100c7V粗t7=100X1.5519X0.973X300=45300KJ 式中 1.5519——粗煤气的比热容,kj/kg.℃ t7——粗煤气的出口温度,℃
c.出炉煤气中水蒸气的热焓Q8为:
Q8=m8H水=98.305X3030=297864.2KJ 式中 m8——粗煤气夹带水蒸气量,kg
H水——粗煤气中水蒸气的热焓,kj/kg。粗煤气出口温度为30℃,粗煤气中水蒸气的分压.
d.生成的焦油热Q9为:
Q9=m9Q焦油=3.9172X33632.7=131746KJ 式中 m9——焦油产量,kg
Q焦油——焦油热量,33632.7kj/kg e. 焦油的显热和潜热Q10为:
Q10=m9(376.8+2.72t7)=2.9172X(376.8+2.72X300)=3480KJ 式中 376.8——焦油的潜热,kj/kg
2.72——焦油的比热容,kj/kg.℃
f. 生成轻质油的发热能Q11为:
Q11=m11Q轻质油=0.786X43652.5=34310.8KJ
式中 m11——生成轻质油的质量,kg Q轻质油——轻质油的热值,kj/kg g. 轻质油的显热和潜热Q12为:
Q12=m11(293+1.57t7)=0.786X(293+1.57X300)=600.5KJ 式中 293——轻质油的潜热,kj/kg
1.57——轻质油的比热容,kj/kg.℃ h.生成氨的发热能Q13为:
Q13=m13Q氨=0.6503X22190=14430KJ 式中 22190-氨的热值,kj/kg i.氨的显热和潜热Q14为:
Q14=m13(1557.49+2.31t7)=0.6503X(1557.49+2.31X300)=1463KJ 式中 1557.49——氨的潜热,kj/kg
2.31——氨的比热容,kj/kg.℃ J.生成的酚的发热能Q15为:
Q15=m15Q酚=0.515X32657=16818KJ 式中 Q酚——酚的热值,kj/kg
生成酚的显热和潜热很小,可以忽略不计。 k.煤气夹带煤粉的发热能Q16为:
Q16=m16Q煤=1.0X15666=15666KJ 式中 m16——煤气中带出的碳量,kg Q煤——煤的发热量,kj/kg l. 夹带出煤粉的显热Q17为:
Q17=c17m16t7=1.1723X1.0X300=351.7KJ 式中 c17——煤粉的比热容,kj/kg.℃ m.灰渣带出碳量的发热能Q18为:
Q18=m18Q碳=1.73X34045=58898KJ 式中 m18——灰渣中的碳量,kg Q18——碳的发热量,kj/kg n.灰渣带出的显热Q19为:
Q19=c19m18t19=0.9739X28.852X225=6322kj 式中 c19——灰渣比热容,kj/kg.℃ m18——灰渣量,kg
t19——灰渣出炉温度,取为225℃ o.炉体夹套产生的蒸气热焓Q20为: Q20=m5H20=8X2805=22440kj 式中 H20——饱和水蒸气的热焓,kj/kg p.其他热损Q21为:
气化过程中的其他热损由热量衡算确定。 付方总热量为:
Q付=Q6+Q7+…+Q21=1807852KJ
(2)热量衡算 以1000kg收到基煤为计算基准,计算如下。
1:供热方
气化原料的发热量Q1为:
Q1=m1Q原料=100X15666=1566600
式中m1——气化的原料气,100kg,下同 Q燃料 ——气化原料的热值,15666kj/kg 气化原料的显热Q2为:
Q2=c2m2t2=1.256X100X25=3140kj
式中c2 ——气化原料的比热容,kj/kg,取为1.256 t2——入炉煤的温度,25℃ c.气化剂中工业氧的显热Q3为:
Q3=c3m3t3=0.9016X22.5005X30=608.6kj 式中c3——工业氧的比热容,0.9016kj/kg.℃
m3——工业氧的消耗量,kg
t3——工业氧入炉温度,取为30℃
气化剂中水蒸气的热焓Q4。查有关水蒸气表,得450℃、30kg/cm2下,过热水蒸气的焓为3344.4kj/kg,所以 Q4=107X3344.4=357850.8kj 炉体夹套软水带入的热量Q5。 Q5=c5m5t5=4.18X8X30=1003.2kj
式中 c5——水的比热容,4.18kj/kg.℃
m5——加入气化炉的软水的质量,取8kg t5——软水的入炉温度,取为30℃. 由以上计算,供给气化炉的总热量为:
Q=Q1+Q2+Q3+Q4+Q5=1566600+3140+608.6+357850.8+1003.2=1929202.6kj 2:付热方
气化过程生成的各项有效热量与所有的热损失之和,为热量衡算的付热方,由以下几项组成:
生成的煤气热量Q6为:
Q6=100V粗X2843X4.178=100X0.973X11903=1158162kj 式中 V粗——粗煤气的产率,0.973m3/kg煤 11903——粗煤气的发热量,kj/m3
b.生成煤气的显热Q7为:
Q7=100c7V粗t7=100X1.5519X0.973X300=45300KJ 式中 1.5519——粗煤气的比热容,kj/kg.℃ t7——粗煤气的出口温度,℃
c.出炉煤气中水蒸气的热焓Q8为:
Q8=m8H水=98.305X3030=297864.2KJ 式中 m8——粗煤气夹带水蒸气量,kg
H水——粗煤气中水蒸气的热焓,kj/kg。粗煤气出口温度为30℃,粗煤气中水蒸气的分压.
d.生成的焦油热Q9为:
Q9=m9Q焦油=3.9172X33632.7=131746KJ 式中 m9——焦油产量,kg
Q焦油——焦油热量,33632.7kj/kg
焦油的显热和潜热Q10为:
Q10=m9(376.8+2.72t7)=2.9172X(376.8+2.72X300)=3480KJ 式中 376.8——焦油的潜热,kj/kg
2.72——焦油的比热容,kj/kg.℃ f. 生成轻质油的发热能Q11为:
Q11=m11Q轻质油=0.786X43652.5=34310.8KJ
式中 m11——生成轻质油的质量,kg Q轻质油——轻质油的热值,kj/kg g. 轻质油的显热和潜热Q12为:
Q12=m11(293+1.57t7)=0.786X(293+1.57X300)=600.5KJ 式中 293——轻质油的潜热,kj/kg
1.57——轻质油的比热容,kj/kg.℃ h.生成氨的发热能Q13为:
Q13=m13Q氨=0.6503X22190=14430KJ 式中 22190-氨的热值,kj/kg i.氨的显热和潜热Q14为:
Q14=m13(1557.49+2.31t7)=0.6503X(1557.49+2.31X300)=1463KJ 式中 1557.49——氨的潜热,kj/kg
2.31——氨的比热容,kj/kg.℃ J.生成的酚的发热能Q15为:
Q15=m15Q酚=0.515X32657=16818KJ 式中 Q酚——酚的热值,kj/kg
生成酚的显热和潜热很小,可以忽略不计。 k.煤气夹带煤粉的发热能Q16为:
Q16=m16Q煤=1.0X15666=15666KJ 式中 m16——煤气中带出的碳量,kg Q煤——煤的发热量,kj/kg l. 夹带出煤粉的显热Q17为:
Q17=c17m16t7=1.1723X1.0X300=351.7KJ 式中 c17——煤粉的比热容,kj/kg.℃ m.灰渣带出碳量的发热能Q18为:
Q18=m18Q碳=1.73X34045=58898KJ 式中 m18——灰渣中的碳量,kg Q18——碳的发热量,kj/kg n.灰渣带出的显热Q19为:
Q19=c19m18t19=0.9739X28.852X225=6322kj 式中 c19——灰渣比热容,kj/kg.℃ m18——灰渣量,kg
t19——灰渣出炉温度,取为225℃ o.炉体夹套产生的蒸气热焓Q20为: Q20=m5H20=8X2805=22440kj 式中 H20——饱和水蒸气的热焓,kj/kg p.其他热损Q21为:
气化过程中的其他热损由热量衡算确定。 付方总热量为:
Q付=Q6+Q7+…+Q21=1807852KJ
气化过程热平衡综合表(以100kg褐煤计 ) 项目 入 方 原料 发热量Q1 显热Q2 工业氧 显热量Q3 蒸汽 热焓Q4 夹套饮水 带入Q5 共计 出 方 氨 轻质油 焦油 粗煤气(干) 发热量Q6 显热Q7 出炉煤气携带蒸汽热Q8 发热能Q9 显热+潜热Q10 质量/kg 100.0 - 22.5005 107 8.0 237.5005 95.405 (97.3m3) 98.375 3.9172 - - - 0.515 - 1.73 28.852 8.0 - 237.4305 热量/kg 1566600 3410 608.6 357850.8 1003.2 1158162 45300 303782 131746 3481 34310.8 600.6 14430 1463 16818 15666 351.7 58898 6322 22440 1154.32 Ψ/% 81.20 0.18 0.03 18.55 0.05 60.03 2.35 15.75 6.83 0.18 1.78 0.03 0.75 0.08 0.87 0.81 0.02 3.05 0.33 1.16 5.98 1929202.6 100.00 发热能Q11 0.786 显热+潜热Q12 发热能Q13 0.6503 显热+潜热Q14 酚 发热能Q15 带出煤粉 灰渣 显热+潜热Q17 碳的发热能Q18 发热能Q16 1.0 显热Q19 夹套蒸汽 热焓Q20 热量损失 Q21 共计
1929202.6 100.00
2.1 选材原则
换热器用钢的标准、冶炼方法、热处理状态、许用应力、无损检测标准及检测项目均按GB150-1998第四章及其附录A的规定。
换热器的目的是为了传热,经常与腐蚀性介质接触的换热表面积很大,为了保护金属部受腐蚀,最根本的方法是选择耐腐蚀的金属或非金属材料。换热器主要部件材料选择见表2.1
表2.1材料
许用应
零部件
管箱封头 后封头 筒体 管箱圆筒短
15CrMoR
节 管板 换热管 壳程接管 管程接管 筒体法兰 管程接管兰 壳程接管兰 管箱法兰
0Cr18Ni10Ti 0Cr18Ni10Ti 15CrMo 0Cr18Ni10Ti 15CrMo 0Cr18Ni10Ti 15CrMo 15CrMo
4.5 8.0 PN16 PN16 PN6.4 PN16 PN16 PN6.4
323 323 273 273 273 323 273
112.62 100.4 105.86
GB4728 GB/T13296-2007
GB6479
GB470O-4703- 2000
HG20592-97 HG20592-97 GB470O-4703- 2000
8.0
323
128.24
GB6654
材料 15CrMoR 15CrMoR 15CrMoR
设计压力
8.0 8.5 8.5
设计温度
323 273 273
128.24 136.4 136.4 力 ???
GB6654 GB6654 GB6654
t
标准
3换热器结构设计
管壳式换热器的结构设计,必须考虑许多因素,如材料、压力、温度、比温差、结垢情况、流体的性质以及检修与清理等等来选择一些适合的结构型式。
对同一种型式的换热器,由于各种条件不同,往往采用的结构亦不相同。在工程设计中,除尽量选用定型系列产品外,也常按其特定的条件进行设计,以满足工艺上的需要。
U形管式换热器仅有一块管板,且无浮头,所以结构简单,造价比其它换热器便宜,管束可以从壳体内抽出,管外便于清洗,但管内清洗困难,所以管内介质必须清洁及不易结垢的物料。U形管的弯管部分曲率不通,管子长度不一。管
子因渗漏而堵死后,将造成传热面积的损失。
U型管式换热器,使用在压力较高的情况下,在弯管段的壁厚要加厚,以弥补弯管后管壁的减薄。
壳程内可按工艺要求装置折流板、纵向隔板等,折流板由拉杆固定,以提高换热设备的传热效果。纵向隔板是一矩形平板,安装在平行于传热管方向(纵向隔板按工艺要求决定)以增加壳侧介质流速。 符号:
C1 ---- 钢材厚度负偏差mm,应按相应钢材标准的规定选取; C2 ---- 钢材的腐蚀裕量,mm;
C ---- 厚度附加量(按[1]第三章取),mm;对多层包扎圆筒只考虑内筒的C
值,对热套圆筒只考虑内侧第一层套盒圆筒的C值;
Di ---- 圆筒或球壳的内直径,mm;
Do ---- 圆筒或球壳的外直径(Do?Di?2?n) ,mm; pc ---- 计算压力(按[1]第3章),MPa;
Pd ---- 设计压力,Mpa; Pt ---- 管程设计压力,Mpa; Ps ---- 壳程设计压力,Mpa;
??pw?? ---- 圆筒或球壳的最大允许工作压力,MPa;
? ---- 圆筒或球壳的计算厚度,mm;
?e ---- 圆筒或球壳的有效厚度,mm;
?n ---- 圆筒或球壳的名义厚度,mm;
?t ---- 设计温度下圆筒或球壳的计算应力,MPa;
??? ---- 设计温度下圆筒或球壳材料的许用应力(按[1]第4章),MPa;
t
??? ---- 试验温度下材料的许用应力(按[1]第4章),MPa;
? ---- 焊接接头系数(按[1]第3章);对热套圆筒取 ?= 1 .0; 3.1 壁厚的确定
壳体、管箱壳体和封头共同组成了管壳式换热器的外壳。管壳式换热器的壳体通常由管材或板材卷制而成。压力容器的公称直径按GB9019-88规定,当直径<400㎜时,通常采用管材做壳体和管箱壳体。当直径≥400㎜时,采用板材卷制壳体和管箱壳体。其直径系列应与封头、连接法兰的系列相匹配,以便于法兰、封头的选型。卷制圆筒的公称直径以400㎜为基数,一般情况下,当直径<1000㎜时,直径相差100㎜为一个系列,必要时也可采用50㎜;当直径>1000㎜时直径相差200㎜为一个系列,若采用旋压封头,其直径系列的间隔可以取为100
㎜。
圆筒的厚度按GB150-1998第5章计算,但碳素钢和低合金钢圆筒的最小厚度应不小于表3.1.1的规定,高合金钢圆筒的最小厚度应不小于3.1.2的规定。
表3.1.1
[2]
公称直径 400-700 700-1000 1000-1500 1500-2000 2000-2600mm 10 8
[2]
浮头式,U形管式 8 固定式管板式 公称 直径 最小 厚度
6
12 10
14 12
16 14
表3.1.2
400-500 3.5
500-700 700-1000 1000-1500 1500-2000 2000-2600mm 4.5
6
8
10
12
3.2 管箱圆筒短节设计
管箱圆筒(短节)计算按GB150-1998第五章的有关规定;其开孔补强计算按GB150-1998第八章有关规定。圆筒的最小厚度按表3.1.2的规定。设计条件见表3.1.3。
表3.1.3
部件
材料
设计温度℃ 323
设计压力Mpa 8.0
???
Mpa
t
???
Mpa
? 标准
GB6654
C1 C2
mm
mm 0
管箱圆
15CrMoR
筒短节
128.24 1.0 0
圆筒计算:
设计温度下圆筒的计算厚度按式(3-2-1)计算,公式的适用范围为
pc?0.4????。
t ??PCDi2?????PCtt (3-2-1)
其中PC?ps?8.0Mpa;Di?800mm;????128.24Mpa ;?=1.0带入上式得: 计算厚度:δ= 25.76mm
设计厚度:?d???C2???25.76mm
名义厚度: ?n??d?C1?25.76mm,经圆整取?n= 26mm 有效厚度:?e??n?C2?C1?26?0?26mm
设计温度下圆筒的计算应力按式(3-2-2)计算:
?t?PC?Di??e? (3-2-2)
2?e得 ?t?8.0??800?26??127Mpa
2?26?t < ????
满足强度要求,故取名义厚度?n= 26mm合适。
设计温度下圆筒的最大允许工作压力按式(3-2-3)计算: ?Pw??2?e????Di??ett
(3-2-3)
?Pw??2?26?128.24?1.0?8.07Mpa
800?26?Pw??Pwmax?7.5Mpa
满足压力要求,故取名义厚度?n= 26mm合适。 3.3 壳体圆筒设计
圆筒的厚度应按GB 150-1998第5章计算,但碳素钢和低合金钢圆筒的最小厚度应不小于表3-1的规定,高合金钢圆筒的最小厚度应不小于表3-2的规定。设计条件见表3-4:
表3-4
部件
材料
设计温
度℃
设计压力Mpa 8.5
???
Mpa 136.4
t???
Mpa
?
标准
C1 C2
mm
mm 0
壳体
15CrMoR 273
圆筒
1.0 GB6654 0
圆筒计算:
其中PC?pt?8.5Mpa;Di?800mm;????136.4Mpa ;?=1.0带入(3-2-1)得:
计算厚度:δ= 25.73mm
设计厚度:?d???C2???25.73mm
名义厚度: ?n??d?C1?25.73mm,经圆整取?n= 26mm 有效厚度:?e??n?C2?C1?26?0?26mm
t设计温度下圆筒的计算厚度按式(3-2-1)计算,
设计温度下圆筒的计算应力按式(3-2)计算:
得 ?t?8.5??800?26??135Mpa
2?26?t < ????
满足强度要求,故取名义厚度?n= 26mm合适。
设计温度下圆筒的最大允许工作压力按式(3-2-3)计算:
2?26?136.4?1.0?8.587Mpa ?Pw??800?26t?Pw??Pwmax?8.0Mpa
满足压力要求,故取名义厚度?n= 26mm合适。 3.4 封头设计[1~3]
压力容器封头的种类较多,分为凸形封头、锥壳、变径段、平盖及紧缩口等,其中凸形封头包括半球形封头、椭圆形封头、碟形封头和球冠形封头。采用什么样的封头要根据工艺条件的要求、制造的难易程度和材料的消耗等情况来决定。
此次设计采用标准椭圆形封头,它由半个椭球面和短圆筒组成,如图3.4所示。直边段的作用是避免封头和圆筒的连接焊缝出现经向曲率半径突变,以改善焊缝的受力状况。封头的椭球部分经线曲率变化平滑连续,故应力分布比较均匀,且椭圆形封头深度较半球形封头小得多,易于冲压成型,是目前中、低压容器中应用较多的封头之一。设计条件见表3.4-1,表3.4-2。
图3.4 表3.4-1
部件
材料
设计温
度℃
设计压力Mpa
???
Mpa
t???
Mpa
?
标准
C1 C2
mm
mm
bn ---- 垫片宽度,其值按表3-9选取,mm;
DL ---- 布管限定圆直径,mm;
Di ---- 圆筒内直径,mm;
d ---- 换热管外径,mm;
图3.5.5.1
图3.5.5.2 表3.5.5.1
[2]
Di
<1000
1000~2600
b >3 >4
Di= 800mm,取b = 28mm。
表3.5.5.2
[2]
Di
≤700 >700
bn
≥10 ≥13
b1
3 5
取bn= 30mm,b1= 5mm,则有b2?bn?1.5?30?1.5?31.5mm。 布管限定圆为管束最外层换热管中心圆直径,布管限定圆按表3.5.5.3确定。
表3.5.5.3
[2]
换热器型式 布管限定圆直径DL
固定管板式、U形管式 浮头式
Di?2b3
Di?2?b1?b2?b?
得:DL?Di?2b3?800?2?8?784mm。
除了考虑布管限定圆直径外,换热管与防冲板间的距离也许考虑。通常,换热管外表面与邻近防冲板表面间的距离,最小为6mm。换热管中心线与防冲板板厚中心线或上表面之间的距离,最大为换热管中心距的3/2。 3.5.6 换热管的排列原则
①换热管的排列应使整个管束完全对称;
②在满足布管限定圆直径和换热管与防冲板间的距离规定的范围内,应全部布满换热管;
③拉杆应尽量均匀布置在管束的外边缘在靠近折流板缺边位置处应布置拉杆,其间距小于或等于700mm,拉杆中心至折流板缺边的距离应尽量控制在换热管中心距地(0.5~1.5)3范围内;
④多管程的各管程数应尽量相等,其相对误差应控制在10%以内,最大不得超过20%。 3.6 管板设计 符号规定:
Ad ---- 在布管区范围内,因设置隔板槽和拉杆结构的需要,而未能被换热管
支承的面积,mm2;例如双管程管板,对于三角形排列:
Ad?n?S?Sn?0.866?25? (3-6-1)
n ---- U 形管根数,管板开孔数为2n;
n? ---- 沿隔板槽一侧的排管根数; S ---- 换热管中心距,mm;
Sn ---- 隔板槽两侧相邻管中心距,mm; At ---- 管板布管区面积,㎡;
三角形排列: At?1.732nS2?Ad (3-6-3)
a ---- 一根换热管管壁金属的横截面积,㎡;
~1和t,查图19[2]; Cc ---- 系数,按Kf?Ce ---- 系数,按
~1和t,查图20[2]; Kf?CM ---- 系数,按
~1和t,查图21[2]; Kf?Ep?3D ---- 管板开孔前的抗弯刚度,N2mm;
D?12?1??2? (3-6-5)
DG ---- 垫片压紧力作用中心圆直径,按[1]第9章,mm; Di ---- 壳程圆筒和管箱圆筒内直径,mm; Dt ---- 管板布管区当量直径,Mmm;
Dt?4At? (3-6-6)
d ---- 换热管外径,mm;
Ep ---- 管板材料的弹性模量,MPa;
Kf ---- 管板边缘旋转刚度参数,MPa;
Kf?Kf'?Kf'' ,对于a型连接 Kf?0
Kf' ---- 壳程圆筒与法兰(或凸缘)的旋转刚度参数,MPa; Kf'' ---- 管箱圆筒与法兰(或凸缘)的旋转刚度参数,MPa; ~~ ---- 旋转刚度无量纲参数;对于a型连接= 0 KfKfl ---- 换热管与管板胀接长度或焊脚高度,按5.8.2.3或5.8.3.2[2]规定,mm;
pd ---- 管板设计压力,MPa; Pt ---- 壳程设计压力,MPa; Ps ---- 管程设计压力,MPa;
q ---- 换热管与管板连接的拉脱力,MPa;
?q? ---- 许用拉脱力,按5.7.5
R[2]
规定,MPa; ;
对
a
型
连
接
:
---- 半径,mm
R?DG2
(3-6-7)
S ---- 换热管中心距,mm;
? ---- 管板计算厚度,mm;
?h ---- 管箱圆筒厚度,mm; ?s ---- 壳程圆筒厚度,mm; ?t ---- 换热管壁厚,mm;
? ---- 管板强度削弱系数,一般可取??0.4;
? ---- 管板材料泊松比,取??0.3;
?t ---- 布管区当量直径Dt与直径2R之比;
???r ---- 设计温度下,管板材料的许用应力,MPa; ???t ---- 设计温度下,换热管材料的许用应力,MPa;
管板是管壳式换热器的一个重要元件,它除了与管子和壳体等连接外,还是换热器中的一个重要受压元件。对管板的设计除了要满足强度要求外,同时应合理的考虑其结构设计。管板得合理设计对于正确选用和节约材料、减少加工制造的困难、降低成本、确保使用安全都具有重要意义。
U型管换热器仅有一块管板,采用可拆式连接,管板通过垫片与壳体法兰和管箱法兰连接。其连接形式见图3.6。
tt
图3.6
管板的最小厚度除满足强度设计要求外,当管板和换热器采用焊接时,应满足结构设计和制造的要求,且不小于12mm。若管板采用复合钢板,其复合层的厚度应不小于3mm。对于有腐蚀要求的复层,还应保证距复层表面深度不小于2mm的复层化学成分和金相组织符合复层材料的要求。
当管板与换热管采用胀接时,管板得最小厚度(不包括腐蚀裕度)应满足表3.6.1。若管板采用复合管板,其复层最小厚度应不小于10mm。并应保证距复层表面深度不小于8mm的复层化学成分和金相组织符合复层材料的要求。
表3.6.1
换热管外径d,mm 最小厚度,mm
用于易燃易爆及有毒介质等场合 用于无害介质的一般场合
≤25 ≥d ≥0.75d
≥0.70d
≥0.65d
>25~<50
≥50
3.6.1 管板连接设计 (1)管板与换热管的连接
对于换热管与管板的连接结构形式,主要有以下三种:①胀接;②焊接;③
胀焊并用,但也可采用其他可靠的连接形式。
a、强度胀接用于管壳之间介质渗漏不会引起不良后果的情况下,胀接结构简单,管子修不容易。由于胀接管端处在胀接时产生塑性变形,存在着残余应力,随着温度的上升,残余应力逐渐消失,这样使管端处降低密封和结合力的作用。一般适用设计压力≤4MPa;设计温度≤300℃;操作中无剧烈的振动,无过大的温度变化及明显的应力腐蚀场合。一般要求:1、换热管材料的硬度值一般需低于管板材料的硬度值;2、有应力腐蚀时,不应采用管端局部退火的方式来降低换热管的硬度。
b、强度焊是指保证换热管与管板连接的密封性能及抗拉脱强度的焊接。管子与管板的焊接,目前应用较为广泛,由于管孔不需开槽,而且管孔的粗糙度要求不高,管子端部不需退火和磨光,因此制造加工简单。焊接结构强度高,抗拉脱力强,当焊接部分渗漏时,可以补焊,如须调换管子,可采甩专用刀具拆卸焊接破漏管子,反而比拆卸胀管方便。不适用于有较大振动和有间隙腐蚀的场合。其结构形式和尺寸见图3.6.1和表3.6.1。
图3.6.1
换热管规格 d3δ 换热管l1 最小伸
出长度 l2 最小坡口深度l3
1.0
2
2.5
1231
1431.5 1.0 2.0
表3.6.1 1631931.5 2
1.5 2.5
[2]
131 0.5 1.5
2532 3232.5 2.0 3.0
3833 2.5 3.5
4533 5733.5 3.0 4.0
注:1 当工艺要求管端伸出长度列值(如立式换热器要求平齐或少低)时,可适当加大管板
坡口深度或改变结构型式
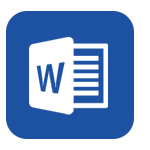





正在阅读:
甲醇气化工艺设计03-09
低温杜瓦瓶安全操作规程03-11
部编版六年级语文下册《北京的春节》课时练及答案【精选】04-12
会计学习题集05-31
墩柱施工方案03-29
高中语文优质课赛课教案06-23
美丽的妈妈作文300字07-04
印光大师开示念佛方法06-04
十大保命条例03-12
- 多层物业服务方案
- (审判实务)习惯法与少数民族地区民间纠纷解决问题(孙 潋)
- 人教版新课标六年级下册语文全册教案
- 词语打卡
- photoshop实习报告
- 钢结构设计原理综合测试2
- 2014年期末练习题
- 高中数学中的逆向思维解题方法探讨
- 名师原创 全国通用2014-2015学年高二寒假作业 政治(一)Word版
- 北航《建筑结构检测鉴定与加固》在线作业三
- XX县卫生监督所工程建设项目可行性研究报告
- 小学四年级观察作文经典评语
- 浅谈110KV变电站电气一次设计-程泉焱(1)
- 安全员考试题库
- 国家电网公司变电运维管理规定(试行)
- 义务教育课程标准稿征求意见提纲
- 教学秘书面试技巧
- 钢结构工程施工组织设计
- 水利工程概论论文
- 09届九年级数学第四次模拟试卷
- 气化
- 甲醇
- 工艺
- 设计
- 考研教育学专业基础综合题库(一)
- 工地安全黑板报内容
- UV BlueStar B型紫外可见分光光度计操作维护保养规程
- 清明节祭扫革命烈士墓活动通知
- 发展经济学的名词解释
- 大班年段上下学期5分钟安全教育内容
- 2015年高考历史真题汇编第11课物理学的重大进展新人教版必修3
- “红色记忆”活动策划书
- 幼儿园交通安全月工作总结与幼儿园亲子文娱活动邀请函汇编
- 高职升学语文模拟试题
- 会计诚信问题探索
- 装维个人工作总结
- 2018-2019年初中政治北京中考全真模拟考试含答案考点及解析
- 24、玩具柜台前的孩子
- 电力设施防外力破坏管理办法
- 生物上册514鱼教学设计新版新人教版01233111
- 二次函数最值经典例题收录
- 2019年担保公司年度工作总结范本
- 1984~85年事件
- 2015年度中国有色金属工业科学技术奖评审通过项目