手机充电器的模具设计+李留松+机械工程学院2011届
更新时间:2023-10-07 15:57:01 阅读量: 综合文库 文档下载
编码 专业代码
2015-JXLW 080202-141
本科毕业论文(设计)
手机充电器的模具设计
学 院 专 业 学 号 学生姓名 指导教师 提交日期
机械工程学院 机械设计制造及其自动化 6111030142 李留松 李孟源 李香燕 2015年 04 月 10 日
诚 信 承 诺 书
本人郑重承诺和声明:
我承诺在毕业论文撰写过程中遵守学校有关规定,恪守学术规范,此毕业论文(设计)中均系本人在指导教师指导下独立完成,没有剽窃、抄袭他人的学术观点、思想和成果,没有篡改研究数据,凡涉及其他作者的观点和材料,均作了注释,如有违规行为发生,我愿承担一切责任,接受学校的处理,并承担相应的法律责任。
毕业论文(设计)作者签名: 年 月 日
摘 要
这套设计是精心从图书馆查资料、和指导老师讨论、分析和整理成文,做出了这个手机充电器外壳的设计。该课题从产品的材料选取,结构工艺性,具体模具结构出发,采用AutoCAD2010软件绘制零件的2D造型、成型零件中分型面确定与开模、浇注系统与冷却系统设计,顶出系统和模架的选择与参数的设置。另外该套模具巧妙的设计了拉料杆,保证了凝料在第一次分型时留在凹模板一侧,顶杆推动推杆固定板时凝料自动脱落,实现了从注射到塑件被顶出的全自动化,提高了生产效率。有利于提高模具的生产效率和节约了生产成本,并大大缩短了生产的周期。该副模具的开合模动作完全符合设计要求,适于大批量生产。
关键词:手机充电器外壳;塑料注射模;AutoCAD2010;一模二腔
I
ABSTRACT
This nested design is carefully looks up the material from the library, and instructs teacher to discuss, to analyze and reorganizes the article, has made this handset battery charger outer covering design.This topic from the product material selection, the structure technology capability, the concrete mold structure embarks, uses Auto CAD2007 the software plan components in the 2D modelling, the formation components is divided the profile to determine with operates the mold, the casting system and the cooling system design, goes against the system and the pould frame choice and the parameter establishment.Moreover this set of mold ingenious design has pulled the material pole, had guaranteed congeals the material when the first minute kept concave template one side, the roof bar impelled when the throwout lever dead plate congeals the material to fall off automatically, realizes from has injected to models the entire automation which went against, enhanced the production efficiency.Was advantageous in enhances the mold the production efficiency and saved the production cost, and reduced greatly the production cycle.This mold opens and closes the mold movement to conform to the design requirement completely, is suitable for the mass production.
Key word: Handset battery charger outer covering; plastic injection mold;AutoCAD 2010; a mold cavity
II
目 录
1 引 言 ................................................................ 1 2 工艺分析 .............................................................. 2
2.1 材料的选择 ....................................................... 2 2.2 塑件收缩率 ....................................................... 2 2.3 塑件的壁厚 ....................................................... 2 2.4 塑件的拔模斜度 ................................................... 2 2.5 塑件的尺寸精度及表面质量 ......................................... 3
2.5.1 尺寸精度 .................................................... 3 2.5.2 塑件的表面质量 .............................................. 4
3产品介绍 ............................................................... 5 3.1 产品分析 ......................................................... 5 3.2 计算塑件的体积和重量 ............................................. 5 4注塑机的选择 ........................................................... 7 4.1 注塑机简介 ....................................................... 7 4.2 注塑机的选择要求 ................................................. 7
4.2.1 注射重量 .................................................... 7 4.2.2 注射量的确定 ................................................ 8 4.2.3 选择一台足够注射重量的注塑机 ................................ 8 4.2.4 注射压力 .................................................. 9 4.2.5 注射行程、容积和速度 ...................................... 9 4.2.6 注射速率 ................................................. 10 4.2.7 螺杆转速和塑化能力 ......................................... 10 4.2.8 锁模力和开模行程 ........................................... 11 4.2.9 模具高度和模板最大开拒 ..................................... 11 4..3 电动机的选择 ................................................... 12 4.3.1 电动机的额定功率 ........................................... 12 4.3.2 电热额定功率 ............................................... 12 4.3.3 液压油箱容量 ............................................... 13 4.3.4 料斗容量 ................................................... 13 4.3.5 系统压力 ................................................... 13 4.3.6 注塑机重量 ................................................. 13
5塑件注射工艺参数的确定 ................................................ 15 6注射模的结构设计 ...................................................... 16 6.1 确定分型面 ...................................................... 16 6.2 确定浇注系统 .................................................... 16
6.2.1 主流道设计 ................................................. 16 6.2.2 冷料穴设计 ................................................. 17 6.2.3 浇口设计 ................................................... 17 6.3 确定型腔、型芯的结构及固定方式 .................................. 18 6.3.1 型腔、型芯的结构设计 ....................................... 18 6.3.2 固定方式 ................................................... 19 6.4 型腔和型芯的工作尺寸计算 ........................................ 19
III
6.5 型腔壁厚和底板厚度计算 .......................................... 21
6.5.1 动模垫板厚度理论计算公式如下: ............................. 21 6.5.2计算型腔侧壁和底板厚度 ...................................... 21 6.6推出方式的设计 ................................................... 22 6.7确定导向机构 ..................................................... 24 7 冷却系统设计 ......................................................... 26 7.1 温度调节对塑件质量的影响 ........................................ 26 7.2 对温度调节系统的要求 ............................................ 26 7.3 冷却系统设计: .................................................. 26 7.4 模具的加热 ...................................................... 27 7.5 模具的冷却 ...................................................... 27 8 试模及注塑机的详细使用方法介绍 ....................................... 29 9校核计算 .............................................................. 31 9.1 注塑机的校核 .................................................... 31 9.2 模具厚度H与注射机闭合高度的校核 ................................ 32 9.3 顶出行程的校核 .................................................. 32 总 结 ............................................................... 34 参考文献 ............................................................... 35
IV
引言
1 引 言
现在,模具生产技术水平的高低,已成为衡量一个国家产品制造水平高低的重要标志之一,因为模具在很大程度上决定着产品的质量、效益和新产品的开发能力。塑料模具的发展是随着塑料工业的发展而发展的。近年来,人们对各种设备和用品轻量化及美观和手感的要求越来越高,这就为塑料制品提供了更为广阔的市场。塑料制品要发展,必然要求塑料模具随之发展。汽车、家电、办公用品、工业电器、建筑材料、电子通信等塑料制品主要用户行业近年来都高位运行,发展迅速,因此,塑料模具也快速发展。在生产量高速增长的情况下,中国塑料模具水平也有很大提高。国内目前已能生产单套重量达60吨的大型模具、型腔精度达0.5μm的精密模具、一模7800腔的多腔模具及4m/min以上挤出速度的高速模具。模具寿命也有很大提高,己可以达到100万模次以上.模具产品将向着更大型、更精密、更复杂及更经济快速方向发展;模具生产将朝着信息化、无图化、精细化、自动化方向发展;模具企业将向着技术集成化、设备精良化、产品品牌化、管理信息化、经营国际化方向发展。
模具CAD/CAE/CAM/PDM正向集成化、三维化、智能化、网络化和信息化方向发展。快捷高速的信息化时代将带领模具行业进入新时代。模具的质量、周期、价格、服务四要素中,已有越来越多的用户将周期放在首位,要求模具尽快交货,因此模具生产周期将继续不断缩短。大力提高开发能力,将开发工作尽量往前推,直至介入到模具用户的产品开发中去,甚至在尚无明确的用户对象之前进行开发(这需要在有较大把握和敢冒一定风险的情况下进行),变被动为主动。以及“你给我一个概念,我还你一个产品”的一站式服务模式都已成为发展趋势。随着模具企业设计和加工水平的提高,过去以钳工为核心,大量依靠技艺的现象已有了很大变化。在某种意义上说:“模具是一种工艺品”的概念正在被“模具是一种高新技术工业产品”所替代,模具“上下模单配成套”的概念正在被“只装不配\的概念所替代。模具正从长期以来主要依靠技艺而变为今后主要依靠技术。这不但是一种生产手段的改变,也是一种生产方式的改变,更是一种观念的改变。这一趋向使得模具标准化程度不断提高,模具精度越来越高,生产周期越来越短,钳工比例越来越低,最终促使整个模具工业水平不断提高。高速加工、复合加工、精益生产、敏捷制造及新材料、新工艺、新技术将不断得到发展。
由于本人的实践经验有限,处于模具设计的底层水平,在设计中出现的瑕疵和漏洞,恳请老师和评委们加以提出指正,并提出宝贵的意见,我定会吸取教训,进取自己的技能和设计水平。
1
2 工艺分析
2.1 材料的选择
ABS树脂是微黄色固体,有一定的韧性,密度约为1.02 ~1.05g/cm3。它抗酸、碱、盐的腐蚀能力比较强,也可以在一定的程度上耐受有机溶剂溶解。ABS 吸湿性强,用于注射成型的塑料原料应充分干燥。使其含水量低于0.3%;与聚乙烯相比,较难成型,料温比较高但又必须在成型范围之内。模温应根据制品的用途和精度要求在50~800C内选择,ABS有很好的成型性,加工出的产品表面光洁,易于染色和电镀。ABS缺点是可燃、耐热性低。热变形温度一般在930C左右,连续工作温度为700C左右只能在不高的温度下使用。因此可以被用于家电外壳、玩具等日常用品。
ABS树脂具有刚性好,冲击强度高、耐热、耐低温、耐化学药品性、机械强度和电器性能优良,易于加工,加工尺寸稳定性和表面光泽好,容易涂装,着色,还可以进行喷涂金属、电镀、焊接和粘接等二次加工。因为其强度高、耐腐蚀、耐高温,所以常被用于制造仪器的塑料外壳。主要应用:汽车、器具、电子/电器、建材。 ABS树脂在日用消费品领域亦具有广泛的应用,比如建材管材、板材或片材。ABS树脂用于与建筑有关的领域,其中挤出片材用于卫生器具如澡盒、游泳池衬里等,另外注塑成型的管材和管件,少量由挤出机挤出成型的电话电缆管线。
2.2 塑件收缩率
根据以上选用的材料为ABS,查相关资料可知,ABS的收缩率为0.004~0.007,这里选择偏中值,为0.005。
2.3 塑件的壁厚
一般说来,塑件的厚度越厚就越能满足产品的强度和刚度的性能要求,但是从塑件的成型过程看来,塑件的壁厚越厚,冷却的时间就越长,整个塑件的成型周期就要延长,提高了生产的成本,降低了生产的效率,同时,塑件的壁厚越厚,收缩率就增大,这样使的得产品的尺寸不稳定性增加,降低了产品的质量。因此产品的厚度必须得适中,根据材料的的特性,查阅相关的资料,查得ABS制品的壁厚通常为1、1.2、1.5、2、2.5、3mm。
本次设计中,塑件的壁厚为1.5mm。
2.4 塑件的拔模斜度
由于塑件成型时冷却过程中产生收缩,使其紧箍在凸模或型芯上,为了便于脱模,防止因脱模力过大而拉坏塑件或使其表面受损,与脱模方向平行的塑件内,外表面都应具有合理的斜度.以下是ABS的脱模斜度推荐值: 制件外表面35′~1.35°制件内表面 30′~1°。
2
商丘工学院本科毕业设计(论文)
的差异)。测试所用的胶料通常是比重1.05的一般ABS硬胶,当塑件的塑料有别于ABS时,规格上的注射重量要经以下换算后才可使用。非ABS塑料的注塑重量= Wx × Vx/1.05,(Vx =塑料的比重 Wx =以ABS计的注射重量。)
4.2.2 注射量的确定
首先计算制品的重量:W=制品重+浇口系统重量,式中:(W=注射所需的重量)。在本公司的产品样本上,所有实际注射量参数都是以聚苯乙烯作为例子来计算的,因此在实际情况中也分两种情况来考虑。当注塑制品是用ABS制造时,注塑机应具备的注射量为Wps;Wps=(1.2~3)×(制品重+浇口系统总重),其中,当制品的品质要求较高,或周期较短时,上式中的系数应取大值,反之可取小值。当制品是其他塑料(命名为X塑料)要仿照上法,先计算出其应具有该种塑料的理论注塑量为Wx;Wx=(1.2~3)×(制品重+浇口系统总重);然后根据此塑料(X)的密度换算成ABS材料的实际重量Wps,换算公式是:Wps=Wx × 1.05/Vx;根据计算结果Wps与产品样本对比,选用适合的注塑机。注射重量并非注射容量乘以ABS的比重:注射重量是测量出来的而注射容量是理论性的。注射容量乘以ABS的比重较注射重量为大,因为注塑时塑料会流入料筒与螺杆的空隙裏。还有,止回阀需往后移动才抵达关闭的位置。所以厂商一般用注射容量作计算注射重量的起点,理论的注射重量= 注射容量×原料的熔融密度×注射效率系数。(一般取0.86)
4.2.3 选择一台足够注射重量的注塑机
不应选择注射重量刚好等於塑件重量加流道塑料重量的注塑机。在要求不高的注塑中,如玩具人像:总重量应是注射重量的85%;在要求高的注塑中;则用70%以下较好。(塑化较均匀,较不会有生料)。塑件及流道塑料的总重量一般是注射重量的30%到85%之间。下限是由於下以三种考虑:模板的弯曲;塑料在料筒的驻留时间及每公斤注塑件的耗电量。小的注塑件使用小的模具会使模板有过份的弯曲,使他挠起(影响产品品质),甚至使模板破裂。用过大的注塑机注塑小的塑件,熔融驻留时间太长会引致塑料分解。在料筒的驻留时间可以引用以下公式估计。 在料筒的驻留时间=(料筒内塑料重量x注塑周期时间/每模注射重量。料筒内的塑料重量大约是注射容量的2倍估计。
在一台机器的注射装置上,很多厂商都提供多种螺杆直径可选。螺杆直径直接影响长径比,注射压力,及注射容量 (因此也影响注射重量)。螺杆有效长度与螺杆直径之比为螺杆长径比。若注塑机有可选的螺杆,螺杆长径比是选择过程的一个重要参数。一个22:1或更大的长径比提供在螺杆的压缩区较佳的混和及较均匀的加热。要求高的注塑件,如注塑工程塑料,或在0.01毫米公差内高精度的注塑,都该选大的长径比。在给定的螺杆长度,较大的长径比等于较小的螺杆直径。因此注射压力增加,而注射容量及注射重量降低。20:1的长径比属中等,适合一般要求的注塑;而18:1
8
注塑机的选择
或更小的长径比适用於要求不高的注塑而较大的注射重量是更重要的。此时注射压力不高。当螺杆直径一定时,大的长径比相应可增加螺杆各段的长度,提高塑化质量,长径比过大,螺杆长度较长,增加了螺杆自重,使螺杆前部下垂而造成螺杆与机筒间隙的不均匀、甚至在螺杆转动时与机筒刮磨,降低其使用寿命。(理论上是这样,但由材料及工艺可克服)长径比的大小同时会与使用的原料有关系,一般高黏度类、热敏性类等原料不建议使用大的长径比,一般取到22:1以下。
4.2.4 注射压力
螺杆为了克服溶料流经喷嘴、浇道和模腔等处的流动阻力而在溶料上施加压力;在注塑机规格表里的注射压力是注射时料筒前端的最高压力,而非油压的最高压力。注射压力与油压的关系是反比於螺杆横切面面积与注射缸面积之比。
通常,注射压力是最高油压的10倍左右。若注射装置有螺杆可选,较小的螺杆直径产生较高的注射压力。较高的注射压力有助於工程塑料的注塑。因为工程塑料粘度都较高,而粘度越高流动阻力就越大。对于某一种机型的一定螺杆,最大注射压力是一定的。 注射压力设定如果过高,制品可能产生毛边,脱模困难,影响制品的光洁度,制品产生较大内应力。注射压力过低,则易产生物料充填不满模腔,甚至不能成型。一般加工精度低,流动性好的低密度如聚乙烯、聚酰胺之类的塑料,注射压力可选小于或等于70-110Mpa:加工中等粘度的塑料如改性聚苯乙烯,聚碳酸酯等,形状一般但有一定的精度要求的制品,注射压力选100-160Mpa;加工高粘度工程塑料如聚砜、聚苯醚之类等,薄壁长流程,厚度不均和精度要求严格的制品,注射压力大约在140-200Mpa;加工优质精密微型制品时,注射压力可用到200-250Mpa以上。
4.2.5 注射行程、容积和速度
在给定的螺杆直径下,增加注射行程可以增加注射容量。但增加注射行程会增长注射时间,因此而增长注射周期。它亦降低有效螺杆长度,因此降低长径比。高长径比的优点便失去了。从长径比18:1的注塑机规格,统计显示注射行程约是螺杆直径的4倍。在长径比增大时,注射行程可以适当的加长。一般注塑机的注射行程建议不能大于5.5D。
注射容积是理论性的,它等於螺杆的横切面面积乘以注射行程。注射容积(厘米3)=(d2/4) ×i;(d=螺杆直径等于料筒内孔直径,i=注射行程以厘米计算)。由於溶融回流及止流阀的后移,实际注射容量约是理论的97%。从实际注射容量计算注射重量,应考虑塑料在固态与溶态的比容积变化。一般情况下,实际重量为理论容积的85% X 比重(固态重量)。
注射速度影响注射时间。注塑薄壁件时需要高的注射速度,以防止模腔未注满时,溶融已冷却凝固。通过控制压力油的流量,注塑机都可在注射时有多段注射速度。恒速前缘理论指出最优良的注塑是当溶融前端在模腔内以恒定的速度前进。因模腔的断
9
商丘工学院本科毕业设计(论文)
面面积并不一致,注射时需要多段射速来能达到恒速前缘流动。有些注塑机有多达10段的射速。有些注塑机可加蓄能器来加快注射速度。蓄能器在注射周期的低用油阶段储存高压的压力油,来给高用油的注射阶段使用。它均化电马达的负载及减低其过荷。虽然加大马达及油泵(有些注塑机厂商提供的替代装置)可以增加注射速度约25%,蓄能器一般能增加注射速度约3倍。注射速度越高,所需的液压系统控制能力就要越高,否则会造成失控或不稳定。
一般来说,射速在150mm/S以下的,可用一般开环控制。射速150mm/S到200mm/S。以下,用方向比例闭环控制,200mm/S以上用伺服阀控制较好。有些客户在选机器时,会要求多大的注射速度,但从本质上来说,真正需要的是注射速率,因为从注射充填来说,产品要的是多少时间内能完成充填。而在同样的注射速度下,螺杆越小,注射速率就越小,反之则越大。
4.2.6 注射速率
注射速率是指在单位时间内从喷嘴射出的溶料量(容积)。其计算值是机筒截面积与速度的乘积。有些注塑机厂商在规格表里不用注射速度而用注射速率。注射速率是螺杆在注射时每秒射出的最大容量·它以cm3/秒或以G/S计算。注射速率=注射速度×3.1416×(d/2)2×原料的熔融密度×注射效率系数(d=螺杆直径)注射速率低,溶料充模时间长,制品易残生冷接缝、前后密度不均、应力大等弊病。注射制品,同时高速注射时,可采用低温模具,缩短成型周期,在不形成过填充的条件下,高速注射也能使所需的合模力减少。但注射速度过高,溶料经浇口等处时,产生较大的剪切热,易形成不规则的流动、物料烧焦以及吸入气体和排气不良等现象,同时在一般开环控制下,高速注射也不能保证注射与保压稳定的切换,形成不稳定而使制品出现溢边或缺料。注射速率的最低要求是:在塑料通道未凝固前,充填完成。
4.2.7 螺杆转速和塑化能力
螺杆转速是以转/分(rpm)表示的一个上下限。螺杆转速不及螺杆表面速度重要。两者与螺杆直径关连。螺杆表面速度(cm/min。)=3.1416×螺杆直径(cm)x螺杆转速(转/分)。每种塑料都有它的推荐最高螺杆表面速度(线速度),不应超越。如硬性众氯乙烯叫PVC)的表面速度不应超过12 m/min,聚丙烯PP可达60 m/min。PC可允许30 m/min。
例如:使用60毫米螺杆注塑硬性众氯乙烯(UPVC)时,最大的螺杆转速是多少?最大的螺杆转速=1200/(3.1416?6) = 64 rpm。加大螺杆转速可大幅度地提高生产效率,但也会加大溶料的剪切热,可能造成溶料过热。同时螺杆转动的提高要配合以大排量的液压泵及加大电机,对液压系统也要有通过流量变大的要求,大幅度提高整体的成本。(个别低粘度塑料可降低油压马达排量来提高转速)
10
注塑机的选择
塑化能力是一台注塑机在最高螺杆转速及零背压下於单位时间内能够均匀地塑化或提升到均匀的溶化温度的一般硬胶(PS)重量。单位以克/秒,或 kg/ hr.表示.塑化能力(kg/hr.) = 1.29 × D2×h1×密度×rpm×60÷1000×效率D = 螺杆直径(cm), h1 = 计量段深度(cm),效率一般取 85%所以,ABS以外的材料塑化能力,可依比重的不同来换算.塑化能力的大小与螺杆直径, 螺杆设计, 螺杆转速等有关系。机器上标示的塑化能力为最大值(PS),但因每种材料容许的线速度(螺杆转速)不等,所以每种材料的塑化能力也是不一样的。为了提高生产量,降低周期,塑化时间(储料)最好在冷却时间内完成。而为了降低能耗,塑化时间不用比冷却时间短太多,如何取舍要依具体或大部份生产的产品而定。
4.2.8 锁模力和开模行程
锁模力又称合模力,是注塑机的重要参数,即注塑机施加于模具的夹紧力。锁模力与注射量一样,在一定程度上反映了机器加工制品的能力的大小;并用来作为表示机器规格的大小的主要参数。机器在选型时应尽量使用在最大锁模力以下的数值。足够的锁模力与模腔的投影面积成正比,模腔投影面积是模腔投影在模具分离面的面积。需要注意的是:锁模力不足,会使制品在生产过程中产生飞边(披锋)或不能成型;而如果锁模力太大,造成系统资源的浪费,如果合模力及模板远大于模具所需,会使模板变型量加大,而使机器及模具寿命降低。一般合模力的标示,用公吨(等於1000公斤)或千牛力来表示,1公吨约等于10千牛。
一开模行程是移 动模板从合模到开模的位移距离。开模行程断定了注塑件的最大高度H。其关系是:开模行程≥2H+水口长度L。如使用热流道系统时L=0。以上的不等式提供空位给地心吸力、机械手或人手将注塑件拿走。
4.2.9 模具高度和模板最大开拒
模具高度是从垂直合模装置时代遗留下来的。在水平的合模装置中,更贴切的名称是模具厚度。在一台机铰式的注塑机的规格中,容模量以一个范围表示,代表注塑机能容纳的最小至最大模具厚度。他们的相差便是注塑机的调模量。在一台直接油压锁模的注塑机的规格中,容模量是以一个数字表示,代表注塑机能容纳的最小模具厚度。可用的模具厚度应比最小容模量大,使注塑机能合模及锁模。否则,该用一台较小的注塑机(其实该是较小的合模装置)。可用的模具厚度应比最大容模量小,模具才能放得下。否则,该用一台较大的注塑机。此参数决定了模具开模空间大小,制品深度。容模量大,则制品深度越深,反之,制品深度越浅。模板最大开距是合模装置退尽时固定模板与移动模板的最大距离。它与开模行程及最大/最小容模量的关系如后在机铰式注塑机上,模板最大开距 = 开模行程+ 最大容模量。在直压式油压锁模注塑机上 ,模板最大开距 = 开模行程+ 最小容模量。导柱内间距决定模具的外形尺寸大小,
11
商丘工学院本科毕业设计(论文)
模具能容於拉杆空间内才能使用。若模具是从上面吊入,它的宽度该小於水平的拉杆空间。若模具是从旁边推入,则它的长度该小於垂直的拉杆空间。推荐在模具两侧多留25毫米空间,在大模具两侧多留50毫米空间。还要避免沉重的模具在安装时碰撞拉杆,使他凹陷,影响后继的移动模板的顺滑移动。
4.3 电动机的选择
4.3.1 电动机的额定功率
一油压系统是由电动机带动油泵驱动。它以某一效率将电能转换成动能。电动机的额定功率以千瓦或马力计算,它代表在指定的条件下,如线圈温度,马达输出的最大功率。有些厂商提供加大的油泵;此时也应加大电动机。电动机的额定功率不应与效率混淆。一个较低的额定功率本身并不代表注塑机更有效率。他只意味著在注塑周期内,它会经历更大过载。三相电机马达在广阔的功率范围内效率都是大约90%。注塑周期的不同阶段所需的压油功率参差不齐。对电动机来讲,所需的功率也是参差不齐。注射阶段和储料阶段通常是对电动机考良的阶段,电动机的额定功率都比他低,以致在注射阶段和储料阶段时电马达都超额运行,一般超载能力设计在1.4倍左右。在一台没有蓄能器的注塑机上,电动机在注射阶段是过载的(在最大注射压力下)。大多数电动机都能有短暂时间内过载两倍以上的能力。在一台有蓄能器的注塑机上,情况可就不一样。有了蓄能器,可使用较低功率的电动机。蓄能器在低流量需要时储起压力油,以备高流量需要时用。总之,它在周期内平均了电动机的负载并减低其过载。三相电动机在额定功率时每相所需的电流是:im(安培)=马达额定功率(千瓦) ×1000/(3×单相电压(伏特) ×效率×功率因子)= 电动机额定功率(马力) ×746/(3×单相电压(伏特) ×效率×功率因子)。大多数的三相电动机的效率=0.88-0.91,功率因子=0.84-0.880例如:海天HTF250W2注塑机使用30KW电动机。当单相电压是220伏特时,每相电流是多少?假设效率=0.91,功率因子=0.88,im(安培)=30×1000/(3×220×0.91×0.88)=57(A)安培=40×746/(3?220×0.91×0.88)。
4.3.2 电热额定功率
料筒上的电热在开机时提升塑料温度。它亦辅助注塑周期内螺杆转动的塑化。一个高的电热功率有助於缩短加温时间。每个加热区通常有一至两个电热器。发热器尽量是平均分配在三相上的。发热器在每相所需的最大电流是:in =发热器额定功率(千瓦)×1000/(3×单相电压(伏特))。例如:海天HTF250W2有6个发热器,每个1.2千瓦功率。6个发热器平均分布在三相上,每相有两个发热器。当单相电压是220伏特时,每相电流是多少?in=6×1.2×1000/(3×220)=10.9安培。注塑机工作时所消耗的总能量,主要有电机功率,各发热圈的总功率及一些辅助设备消耗的功率。它
12
校核计算
因此满足要求。
结论:根据校核注射机,完全能够满足该模具的使用要求。
33
总结
总 结
从大四上学期开始做准备工作至今完成毕业设计,期间是查阅了大量的文献。通过对手机充电器外壳塑料模具的设计,对常用塑料在成型过程中对模具的工艺要求有了更深一层的理解,掌握了塑料成型模具的结构特点及加工工艺设计,也可说是一次全面展现自己大学生涯对模具设计的了解程度。也是一次很好很有意义的锻炼。为即将参加工作来个热身。
在搞设计过程中,我发现自己是遗忘了当初学习的专业基础知识。比如:机械制图,机械设计,热处理,计算机辅助设计等专业基础科目。在指导老师庄老师的精心指导下,同时查阅了很多相关资料,并亲手拆装了一些典型的模具,明确了模具的一半工作原理,制造,加工工艺。并上网查阅了很多资料,使我塑料模具有了一个更全面更深的认识。通过查阅大量文献之后,我运用了AutoCAD等制图软件开始绘图,起初是很久没使用过,很多功能是忘记了,通过边画图边查阅教程,使我重新学习了下这些软件,这些计算机软件大大提高了我们的设计效率尤其是系列化或类似注塑模具设计效率更为提高。在设计过程中,我还学会了自己独立细心思考的,让我深深体会到毕业之际搞毕业设计是必不可少的,他能加深我对以前学习的知识再次理解和巩固,能让我将所学的知识融会贯通,锻炼我的思维能力。总之,通过此次的设计,我明白要搞模具这块还有很多知识等待着我继续学习,也明白了各种计算机制图软件之间的优势,充分利用这些优势,搭配好,掌握好,能让我们更具创新,更具优势。设计步伐也大为加快。
在此次毕业设计的完成过程中,我的指导老师李香燕老师给予了我悉心指导和热情鼓励,使我顺利完成了毕业设计。她严谨的治学态度、渊博的知识和执着的敬业精神给我留下了深刻印象。激励我克服困难,广泛涉猎新思想、新理论,不断地探求新的科学发展。同时,也让我懂得如何去踏踏实实地工作、勤勤恳恳地做人。毕业设计工作量很大,没有试验条件,加之我的模具设计实践操作知识很少,在做课题的过程中遇到了很多困难,论文在庄教授的热心帮助下才得以顺利完成,在此,谨向李教授表示衷心的感谢和诚挚的敬意。同时,感谢在做课题过程中为我提供便利和帮助的老师和同学们;感谢班上的所有同学们;感谢我们在一起度过的这段忙碌又偷快的时光。在此,向所有关心和帮助过我的领导、老师、同学和朋友表示由衷的谢意!也衷心地感谢在百忙之中评阅论文和参加答辩的各位。
34
参考文献
参考文献
[1]张荣清主编.模具设计与制造[M]. 高等教育出版社, 2008年 [2]冉新成主编.塑料成型模具[M]. 中国轻工业出版社,2009年 [3]屈华昌主编.塑料成型工艺与模具设计[M]. 高等教育出版社,2001年 [4]黄毅宏主编.模具制造工艺学[M]. 机械工业出版社,1996年
[5]王树勋主编.注塑模具设计与制造实用技术[M].华南理工大学出版社,1996年 [6]卢日时,郭民.我国机械自动化若干发展技术浅析[J].黑龙江科技信息,2007年. [7]史铁梁主编.模具设计指导[M]. 机械工业出版社,2007年
[8]彭建声主编.简明模具工实用技术手册[M]. 机械工业出版社,1993年 [9]胡石玉主编.模具制造技术[M].东南大学出版社,1997年 [10]陆宁主编.使用注射模具设计[M].中国轻工业出版社,1997年 [11]高锦张主编.塑性成型工艺与模具设计[M].机械工业出版社,2001年 [12]孙凤勤主编.模具制造工艺与设备[M].机械工业出版社,2002年 [13]申树义,高济.塑料模具设计[M].机械工业出版社,1993年 [14]高佩福主编.实用模具制造设计[M].中国轻工业出版社,1999年 [15]金涤尘,宋放之.现代模具制造技术[M].机械工业出版社,2001年
35
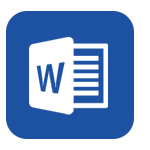





正在阅读:
手机充电器的模具设计+李留松+机械工程学院2011届10-07
中国铜镍合金行业市场调查研究报告(目录) - 图文05-27
会员管理系统使用说明书12-30
争做新时代的好少年06-16
留在记忆里的冬天作文700字06-30
模块7_汇票贴现、转贴现与再贴现的操作07-24
新昌教体网02-15
“十三五”重点项目-无纺布西服套项目可行性研究报告 - 图文09-25
法律服务调研报告03-27
怎样写一份能“融到钱”的商业计划书?04-19
- 多层物业服务方案
- (审判实务)习惯法与少数民族地区民间纠纷解决问题(孙 潋)
- 人教版新课标六年级下册语文全册教案
- 词语打卡
- photoshop实习报告
- 钢结构设计原理综合测试2
- 2014年期末练习题
- 高中数学中的逆向思维解题方法探讨
- 名师原创 全国通用2014-2015学年高二寒假作业 政治(一)Word版
- 北航《建筑结构检测鉴定与加固》在线作业三
- XX县卫生监督所工程建设项目可行性研究报告
- 小学四年级观察作文经典评语
- 浅谈110KV变电站电气一次设计-程泉焱(1)
- 安全员考试题库
- 国家电网公司变电运维管理规定(试行)
- 义务教育课程标准稿征求意见提纲
- 教学秘书面试技巧
- 钢结构工程施工组织设计
- 水利工程概论论文
- 09届九年级数学第四次模拟试卷
- 模具设计
- 工程学院
- 充电器
- 机械
- 手机
- 李留松
- 2011