热电课件
更新时间:2024-01-02 08:13:01 阅读量: 教育文库 文档下载
- 热电课题组推荐度:
- 相关推荐
热电课件
一、整体流程介绍
热电站的工艺目的:将脱盐水转变成合格的蒸汽,通过管道输送至各用户;公司蒸汽分5个等级分别是9.8MPa、3.8MPa过热蒸汽,4.0MPa、1.0MPa、0.5MPa饱和蒸汽。下面先简单介绍下热电站的主要工艺流程:
脱盐水(0.6MPa、30℃,进热电界区后分三路:冷渣机、汽轮机轴封加热器、疏水箱及疏水扩容器;0.6MPa、90℃净化换热器(E2005)来)进低压除氧器,初步除氧后由4台中继水泵送到中继水母管进高压除氧器,深度除氧后由4台锅炉给水泵送至高压冷给水母管,冷给水母管的水经过高压加热器后进入高压热给水母管,也可以通过高压加热器旁路进入高压热给水母管,由高压热给水母管引出4路分别进入4台由无锡锅炉厂制造的150t高温高压循环流化床锅炉省煤器的进口集箱,再到省煤器出口集箱,通过8(76*6)根管子进入汽包,再由汽包上的2根下降管进入锅炉水冷壁下联箱,再通过水冷壁进入汽包,水在水冷壁中受热汽化,进入汽包后进行汽水分离,分离后的水再通过下降管进入水冷壁吸热汽化,而分离出来的汽体通过汽包中上部的6根管道进入旋风分离器下集箱,再从上集箱出来进入左右包墙过热器,再到后包墙下集箱,之后进入前包墙上集箱,再进低温过热器,低温过热器出来,通过一级减温水调节温度后再进入3片屏式过热器,屏式过热器出来有二级减温水调节温度,再进入高温过热器,再到集汽集箱,之后依次经过主蒸汽阀、并汽阀进入9.8MPa蒸汽母管,9.8MPa蒸汽分三路走:1、通过9.8MPa蒸汽外管送到气化减温减压站和合成气压缩机;2、通过2根管道进入汽轮发电机组发电后,进入3.8MPa蒸汽母管;3、经过一号减温减压器减温减压后进入3.8MPa蒸汽母管。
3.8MPa管网之后分五路:一、经2#减温器减温后成4.0MPa、252℃的饱和蒸汽,与外网合成废锅及硫回收来的4.0MPa饱和蒸汽汇合进高加,高加用汽大约在35~50t左右,设计上是45t。二、汽动锅炉给水泵,用汽大约20t左右,对汽轮机做功后成0.6MPa、158℃的饱和蒸汽与外网净化低变废锅和气化水冷壁废锅来的0.5MPa返网蒸汽以及4.0MPa蒸汽通过机械减压阀减压后的0.5MPa饱和蒸汽汇合进低除。三、经3#减温减压器(A/B)后成1.0MPa、185℃的饱和蒸汽与外网净化二变废锅来的1.0MPa饱和蒸汽汇合进高除。四、经4#减温减压器后成0.5MPa、158℃的饱和蒸汽进0.5MPa蒸汽管网。
煤通过给煤机进入炉膛燃烧,燃烧后的渣通过炉膛下部的2个下渣口进入冷渣机,最后由皮带送到渣仓外运;燃烧后的烟气夹带大量的灰尘进入左右旋风分离器进行分离,大颗粒的灰尘被分离下来,在返料风的作用下,再次进入炉膛燃烧,分离后的烟气在引风机的抽引下依次经过尾部烟道中的高温过热器、低温过热器、省煤器、空预器、除尘器、引风机,最后通过烟囱外排;在除尘器中被拦截下来的灰采用气力输灰方式送到灰库,最后外运。 二、主要设备介绍 1、锅炉及其辅机
锅炉:公司所用锅炉是由无锡华光锅炉制造厂生产的4台150t循环流化床锅炉,采用π型布置,单汽包自然循环系统,一二次风配比(50:40)燃烧,床下柴油点火工艺,其型号为UG-9.8/150-M5,锅炉为高温高压,单汽包横置式,单炉膛,全悬吊结构。锅炉运转层以上露天,运转层以下封闭,在运转层 8m标高设置混凝土平台。炉膛采用膜式水冷壁,锅炉中部是蜗壳式汽冷旋风分离器,尾部竖井烟道布置两级三组对流过热器,过热器下方布置三组膜式省煤器及一、二次风各三组空气预热器。
本锅炉采用中国科学院工程热物理研究所的循环流化床燃烧技术,在燃烧系统中,给煤机将煤送入落煤管进入炉膛,锅炉燃烧所需空气分别由一、二次风机提供。一次风机送出的空气
经一次风空气预热器(一、四、五层)预热后由左右两侧风道引入炉下水冷风室,通过水冷布风板上的风帽进入燃烧室;二次风机送出的风经二次风空气预热器(二、三、六层)预热后,通过分布在炉膛前后墙上的喷口喷入炉膛,补充空气,加强扰动与混合。燃料和空气在炉膛内流化状态下掺混燃烧,并与受热面进行热交换。炉膛内的烟气(携带大量未燃尽碳粒子)在炉膛上部进一步燃烧放热。离开炉膛并夹带大量物料的烟气经蜗壳式汽冷旋风分离器之后,绝大部分物料被分离出来,经返料器返回炉膛,实现循环燃烧。分离后的烟气经转向室、高温过热器、低温过热器、省煤器、一、二次风空气预热器由尾部烟道排出。
炉膛水冷壁
炉膛断面尺寸设计成7010mm×5330mm,炉膛四周由管子和扁钢焊成全密封膜式水冷壁。前后及两侧水冷壁分别各有 87-φ60×5与66-φ60×5根管子。前后水冷壁下部密相区处的管子与垂直线成一夹角,构成上大下小的锥体。锥体底部是水冷布风板,布风板下面由后水冷壁管片向前弯与二侧墙组成水冷风室。布风板至炉膛顶部高度为29m,炉膛烟气截面流速~5m/s。
后水冷壁上部管子在炉膛出口处向分离器侧外突出形成导流加速段,下部锥体处部分管子让出一只返料口。前水冷壁下方有4只加煤口,侧水冷壁下部设置供检修用的专用人孔,炉膛密相区前后侧水冷壁还布置有一排二次风喷口。前、后、侧水冷壁分成四个循环回路,由锅筒底部水空间引出2根φ426×28集中下降管,通过18根φ159×12的分散下降管向炉膛水冷壁供水。其中两侧水冷壁下集箱分别由4根分散下降管引入,前后墙水冷壁下集箱分别由5根分散下降管引入。两侧水冷壁上集箱相应各有4根φ159×12连接管引至锅筒,前后墙水冷壁上集箱有10根φ159×12引出。
水冷壁系统的集箱除前后上集箱合并成φ325的集箱外,其余均为φ219×25。水冷壁、集箱、连接管的材料均为20G/GB5310。
为了运行、检修需要,水冷壁上设置了人孔、看火孔、温度测点、炉膛压力测量孔。整个水冷壁重量由水冷壁上集箱的吊杆装置悬吊在顶板上,锅炉运行时水冷壁向下热膨胀,最大膨胀量140mm。
高效蜗壳式汽冷旋风分离器
(1)分离器是循环流化床锅炉的重要组成部件,本锅炉采用的是中科院工程热物理研究所的高效蜗壳式汽冷旋风分离器专利技术,在炉膛出口布置两只汽冷旋风分离器,分离器直径Ф3600mm,用Ф34×5的管子和鳍片组成膜式壁作为旋风分离器的外壳,并采用蜗壳进口的方式形成结构独特的旋风分离器。具有分离效率高和强化燃烧的优点。旋风分离器将被烟气夹带离开炉膛的物料分离下来。通过返料口返回炉膛,烟气则流向尾部对流受热面。整个物料分离和返料回路的工作温度为900℃左右。
(2)包覆分离器的汽冷受热面能够有效吸收物料后燃所产生的热量,防止返料器内高温结焦,扩大煤种的适应性,同时由于耐火层薄还可以缩短锅炉的启动时间。
(3)分离器内表面焊有密排抓钉,并浇注一层60mm厚的特种耐磨可塑料,使整个分离器的内表面得到保护,从而使分离器具有较长的使用寿命。
(4)分离器出口管采用高温耐热合金制造,材质为 1Cr25Ni20Si2。 (5)分离器入口开设检修门,并保证其密封性。
(6)返料器和立管内设有热电偶插孔及观察窗,以监视物料流动情况。
(7)汽冷旋风分离器做为过热器受热面的一部分。
锅筒及锅筒内部设备
锅筒内径Ф1600mm,厚度为100mm,封头厚度为100mm,筒身长约9000mm,全长约10860 mm,材料为P355GH(19Mn6)。
锅筒正常水位在锅筒中心线以下180mm,最高水位和最低水位离正常水位各50mm。 锅筒内采用单段蒸发系统布置有旋风分离器、清洗孔板和顶部百叶窗等内部设备。
锅筒给水管座采用套管结构,避免进入锅筒的给水与温度较高的锅筒壁直接接触,降低锅筒壁温温差与热应力。
锅筒内装有 30只直径为Ф315mm的旋风分离器,分前后两排沿锅筒筒身全长布置,汽水混合物采用分集箱式系统引入旋风分离器。每只旋风分离器平均负荷为5吨/时。
汽水混合物切向进入旋风分离器,进行一次分离,汽水分离后蒸汽向上流动经旋风分离器顶部的梯形波形板分离器,进入锅筒的汽空间进行重力分离,然后蒸汽通过清洗孔板以降低蒸汽中携带的盐份和硅酸根含量,经过清洗后的蒸汽再经过顶部百叶窗和多孔板又进行二次汽水分离,最后通过锅筒顶部饱和蒸汽引出管进入过热器系统。清洗水量取百分之百的锅筒给水,清洗后的水进入锅筒的水空间。
为防止大口径下降管入口产生旋涡和造成下降管带汽,在下降管入口处装有栅格及十字板。
此外,为保证良好的蒸汽品质,在锅筒内装有磷酸盐加药管和连续排污管,为防止锅筒满水,还装有紧急放水管。
锅筒上设有上下壁温的测量点,在锅炉启动点火升压过程中,锅筒上下壁温差允许最大不得超过50℃。同样,启动前锅炉上水时为避免锅筒产生较大的热应力,进水温度不得超过70℃,并且上水速度不能太快,尤其在进水初期更应缓慢。
锅筒采用两个U型曲链片吊架,悬吊在顶板梁下,吊点对称布置在锅筒两端,相距7010mm。
燃烧设备
燃烧设备主要有给煤装置、排渣装置、给石灰石装置、布风装置和点火系统 及返料回灰系统。 (1)给煤装置
锅炉给煤机为耐压式计量皮带给煤机,型号:NJGC-30型。
给煤机与落煤管通过膨胀节相连,解决给煤机与炉膛水冷壁之间的膨胀差 (膨胀值 122mm)。给煤装置的给煤量能够满足在二台给煤装置故障时,其余2台给煤装置仍能保证锅炉100%额定出力。一定粒度的燃煤经给煤机进入布置在前墙的四根320×280间距为~1.6m的落煤管,落煤管上端有送煤风,下端靠近水冷壁处有播煤风,给煤借助自身重力和引入的送煤风沿着落煤管滑落到下端在距布风板 1800mm处进入炉膛。给煤量通过改变给煤机的转速来调整,给煤机内通入一次风冷风作为密封风,由于给煤管内为正压(约有 5000Pa的正压),给煤机必须具有良好的密封,在给煤机上设置密封风。
播煤风管连接在每个落煤管的端口,配备风门以控制入口风量。 (2)布风装置
风室由向前弯的后水冷壁及两侧水冷壁组成,燃烧室一次风从左右两侧风道引入风室。
风室与炉膛被布风板相隔,布风板系水冷壁与扁钢焊制而成,布风板的横断面为6850×2450,其上均匀布置风帽。一次风通过这些风帽均匀进入炉膛,流化床料。风帽采用耐磨耐高温铸钢,风帽横向纵向节距均为160mm。为了保护布风板,布风板上的耐火浇注料厚度为150mm。 (3)排渣装置
底渣从水冷布风板上的三根φ219水冷放渣管排出炉膛,其中两根接冷渣机,每台冷渣机按 10t/h冷渣量配置,中间一根做事故排渣管,冷渣机的冷却水为脱盐水。
底渣通过冷却输送装置,可实现连续排渣。出渣量以维持合适的风室压力为准。通常运行时的风室压力为13000Pa。 (4)给石灰石
本台锅炉按添加石灰石脱硫设计,石灰石通过气力输送经二次风口送入炉膛。脱硫的石灰石耗量每小时4.87吨,按钙硫比2.2计算。脱硫效率为80%。 (5)二次风装置
二次风通过分布在炉膛前后墙上的二次风管喷嘴分别送入炉膛下部不同高度的空间。喷口风速>70m/s。运行时二次风压一般不小于6000Pa。 (6)床下点火燃烧器
两台床下点火燃烧器并列布置在炉膛水冷风室后侧。由点火油枪、高能电子点火器及火检装置组成。点火油枪为机械雾化,燃料为0#轻柴油。每支油枪出力600kg/h,油压2.5Mpa,油枪所需助燃空气为一次风。空气和油燃烧后形成850℃左右的热烟气。从水冷风室上的布风板均匀送入炉膛。为了便于了解油枪点火情况,点火燃烧器设有观察孔。
点火用油量及风量:
点火油枪油压: 2.5MPa 每只油枪喷油量: Q=600Kg/h 点火总风量: 38000Nm3/h 其中混合风: 14300Nm3/h
点火启动时,风室内温度监视采用直读式数字温度计,冷态启动时间一般6小时。 (7)返料回灰系统
旋风分离器下接有返料器,均由钢外壳与耐火材料衬里组成,耐火材料分内、外二层结构,里层为高强度耐磨浇注料,外层为保温浇注料。返料器内的松动风与返料风采用高压冷风,由小风帽送入,松动风与返料风的风帽开孔数量有差别,返料风大,松动风小,并采用分风室送风。小风帽的材质为ZGCr25Ni20。返料器的布风板还设有一根φ108×4放灰管。
过热器系统及其调温装置
锅炉采用辐射和对流相结合,并配以二级喷水减温器的过热器系统。
饱和蒸汽从锅筒由6根Φ159×12的管子引至旋风分离器下环行集箱,蒸汽经膜式壁上行到上环行集箱后引至尾部包墙的两侧上集箱,随后下行,流经两侧过热器包墙。再由转角集箱进入后包墙、顶包墙和前包墙(包墙管均为Φ51×5),前包墙出口下集箱作为低温过热器入口集箱,低温过热器Φ38×5光管顺列布置。为减少磨损,一方面控制烟速,另一方面加盖防磨盖板。过热蒸汽从低温过热器出来后,经连接管进入一级喷水减温器进行粗调,减温可以通过调节减温水量来实现。过热蒸汽经一级减温后进入屏式过热器,屏式过热器布置在炉膛上部,采用Φ42×6,12Cr1MoVG的管子,wing-wall结构形式,使屏过不会产生磨损,再经连接管交叉后引至二级喷水减温器进行细调,最后经高温过热器加热后引入出口集箱,高温过热器采用Φ38×5,12Cr1MoVG与T91的管子。两级减温器的喷水量分别为
4.128t/h、1.612t/h。减温水调节范围控制在减温水设计值的50~150%以内。
省煤器
(1)尾部竖井烟道中设有三组光管省煤器,均采用φ32×4的管子,错列布置,横向节距 86mm,具有较好的抗磨性能。省煤器管的材质为20G/GB5310高压锅炉管。
(2)省煤器管束最上排装设防磨盖板,蛇形管每个弯头与四周墙壁间装设防磨罩。省煤器的平均烟气流速控制在高原修正后 8.2m/s以下。 (3)在锅筒和下级省煤器之间设有再循环管道,以确保锅炉在启动过程中省煤器有必要的冷却。
(4)锅炉尾部烟道内的省煤器管组之间,均留有人孔门,以供检修之用。 (5)省煤器出口集箱设有排放空气的管座和阀门,省煤器入口集箱上设有两只串联 DN20的放水阀。
空气预热器
(1)在省煤器后布置3组空气预热器,分别加热一次风和二次风。采用卧式顺列布置。两组之间均留有800mm以上的空间,便于检修和更换。
(2)空气预热器管子迎风面前三排管子采用φ42×3.5的厚壁管。 (3)每级空气预热器及相应的连通箱均采用全焊接的密封框架,以确保空气预热器的严密性。
(4)空气预热器低温段采用耐腐蚀的ND钢材。
辅机:锅炉辅机主要有一次风机、二次风机、引风机和高压返料风机
(1)一次风机:主要是为锅炉提供主流化风和煤一次燃烧所需的氧气,其安装条件和性能参数如下:
安装和运行条件:
安装在锅炉房零米层。 冷却水条件: 冷却水工作温度≤32℃ 供水压力大于0.3MPa 调速装置:液力耦合器 名 称 型 式 型 号 数 量 风机入口工作介质温度 通过风机的容积流量 风机全压 一次风机 离心式、单吸单支撑 SFG21.5D-C9A 4台 0~30℃ 102350 m/h 24496Pa 3
工作介质粉尘含量 调速装置 风机轴功率 电动机电压 电动机功率 转速
微量 液力耦合器 819KW 10000V 1000KW 1450r/min (2)二次风机:主要是增强炉膛内的扰动,提供煤二次燃烧所需的氧气。其安装条件和性能参数如下:
安装在锅炉房零米层。
冷却水条件: 冷却水工作温度≤32℃ 供水压力大于0.3MPa 调速装置:液力耦合器 名 称 型 式 型 号 数 量 风机出口角度 风机进口角度 风机入口工作介质温度 通过风机的容积流量 风机全压 工作介质粉尘含量 调速装置 风机轴功率 电动机电压 电动机功率
(3)引风机:主要是调节炉膛负压,使旋风分离器分离的含尘烟气以一定流速经过尾部烟
二次风机 离心式 SFG16D-9B 4台 右旋90° 0° 0-30℃ 87190 m/h 13965 Pa 微量 液力耦合器 410KW 10000V 500 KW 3道,进入除尘系统,最后送入烟囱外排,其性能参数如下:
型式 型号 风机入口角度 风机出口角度 风机入口工作介质温度 通过风机的容积流量 风机全压 风机轴功率 工作介质比重 电动机电压 电动机防护等级 电动机功率 引风机 离心式(左右旋各二台) CY150-1№34F 45° 135° 138℃ 320000 m/h 11500Pa 1200 KW 0.785kg/m 10000V IP54 1400KW(六极) 33(4)高压返料风机:提供返料器所需返料动力,其参数如下:
输送介质 进气容积流量(m/h) 工况条件 进气温度(℃) 进口压力(kpa) 出口压力(kpa) 风机型号 设计点的保证效率 进口流量(m/min) 风机转速(r/min) 传动形式 风机性能 升压(kPa) 密封形式 轴功率(kW) 风机重量(kg) 传动方式 距设备外壳1米处的噪音 风机轴承 配套电机 型号 功率(kW) CS33空气 2000 常温 0 71.58 3HE-145 82% 34.9(标态空气)(进气温度20℃,进气压力为101.325kPa时的流量) 1450 联轴器传动 71.58 迷宫密封 59.2 1670 直联 ﹤85dB 6308(日本NACHI)/NU316(日本NSK) Y280S-4 75 CS同步转速(r/min) 电压值(V) 防护等级 绝缘等级 机壳 叶轮 材料 墙板、侧板 主、从动齿轮 主、从动轴 轴承 进口水压(Mpa) 冷却水 进水温度(℃) 1500 380 IP54 F HT200 HT200 HT200 20CrMnTi 45# GCr15 0.30 ≤ 32 冷却水量(L/min) 10-13 此外还有207m3的炉前仓、钢筋混泥土结构,直径8m,容积600m3的渣仓、2个钢筋混泥土结构,直径10m,容积800m3的灰库、容积为400m3,系统出力为13.0t/h,输送风压为0.15MPa的石灰石中转仓以及容积为20m3的石灰石炉前仓。渣5.5万吨/年(6.4吨/小时),灰12.7万吨/年(14.7吨/小时)。 2、汽轮发电机组及其辅机 汽轮机系统主要流程 A、热力系统流程 (1)主蒸汽系统
来自锅炉的高压新蒸汽经由电动隔离门进入主汽阀。主汽阀内装有蒸汽滤网,以分离蒸汽中水滴和防止杂物进入汽轮机。蒸汽在通过调节阀后进入汽轮机内膨胀做功,做功后的4.12MPa背压排汽由两根排汽管道引向热用户。
汽轮机与热用户之间的排汽管道上用电动闸阀隔离,并设有旁路门,便于开启电动闸阀。
在排汽管路上设有保护装置,由弹簧式安全阀组成。当排汽压力超过一定数值时,该阀动作向空排汽,降低压力。 (2) 汽封系统
本机组前汽封有四段漏汽,后汽封有四段漏汽,前汽封第一段漏汽及后汽封第一段漏汽送至高压除氧器主加热蒸汽,前汽封第二段漏汽和后汽封第二段漏汽送至高压除氧器汽平衡管,前汽封第三段漏汽和后汽封第三段漏汽接至汽封加热器(205),前汽封第四段和后汽封第四段的漏汽及主汽阀和调节汽门阀杆低压漏汽被汽封加热器(204)抽走,主汽阀和调节汽门阀杆高压漏汽接至低压除氧器。 (3) 疏水系统
汽轮机本体疏水均疏至疏水扩容器(216),在疏水扩容器内扩容后的蒸汽送至低压除氧器,疏水送至低位疏水箱。高﹑低除氧器溢放水均送至疏水箱,疏水均接至低位疏水箱。 B、油路系统流程 (1) 供油系统
普通供油系统由主油泵、射油器、高压启动油泵、交直流润滑油泵、滤油器及冷油器等组成。在普通供油系统中,主油泵供给高压油、复位油压(挂闸油压),并通过节流降压形成润滑油、保安油、附加保安油和试验油。射油器是由两级并连组成,第一级压力油经冷油
器冷却、滤油器过滤后供给机组的润滑系统,第二级压力油供主油泵进口。另外油系统还有三台油泵:高压启动油泵、交、直流润滑油泵,高压启动油泵在开机时(主油泵未投入运行前)投入运行向系统提供高压油;交流润滑油泵是在汽机停车时盘车或系统润滑油压低到一定数值时自启动;直流润滑油泵在交流润滑油压过低或故障(厂用电源中断)时自启动,来 保证系统润滑油压稳定和机组的安全运行;此外,为了排出系统回油产生的烟气以保证油系统的安全,在油箱上装有排油烟装置。 (2) 调节系统
本汽轮机采用DEH电液调节系统对汽轮机进行调节,电液调节系统由DEH控制系统、电液转换器、一只主汽门油动机和四只高压调节阀油动机组成。每只油动机由一只电液转换器控制。DEH控制系统接收转速信号、背压信号、主蒸汽压力信号等,经运算放大输出0~±10mA 的电流信号,至电液转换器,电液转换器为直动式电反馈电液伺服阀,电液转换器控制脉冲油压,从而控制高压油动机。油动机的位移通过LVDT反馈至DEH控制系统。
高压油通过油动机错油门的动反馈窗口形成脉冲油,脉冲油的压力为高压油的一半,电液转换器是通过改变脉冲油的压力大小来控制油动机的。
当停机信号动作后,通过危急遮断油门泄掉脉冲油或OPC电磁阀动作(OPC电磁阀的动作信号由DEH控制系统提供)泄掉脉冲油时,均可使油动机快速关闭。 (3) 保安系统
保安系统由危急遮断器、危急遮断器滑阀和保安操纵箱组成。保安系统在下述情况下切断汽轮机的新汽供应:
机组转速超过额定转速(3000r/min)11~12%(即3330~3360r/min)时,危急遮断器动作,关闭主汽门、调节汽门而停机。
当转子轴向位移超过1.4mm 准许值时;润滑油压降低到0.02MPa 时;轴承回油温度高于75℃时;背压压力低于正常值的0.2 MPa 时;转速超过3420 r/min(可调)时;DEH系统电源故障时,磁力断路油门动作,关闭主汽门、调节汽门而停机。 汽轮机
汽轮机型号: B15-8.83/4.12 序号 1 2 3 4 5 6 7 8 9 10 项目 新蒸汽初压 新蒸汽初温 背压汽压力 进汽量 热耗 背压蒸汽温度 额定功率 危急保安器动作转速 负荷控制范围 转速控制范围 单位 MPa ℃ MPa T/h KJ/kwh ℃ MW r/min Kw r/min 最小值 8.33 525 3.92 317 4890.7 440 15 3300 0-17000 5-3400 正常值 8.83 535 4.12 318 4927.3 445 15 3300 0-17000 5-3400 最大值 9.33 540 4.32 321 4964.7 450 15 3300 0-17000 5-3400 绝压 备注 11 12 13 14 15 16 17 18 主油泵出口油压 主油泵入口油压 脉冲油压 轴承润滑油压 轴承进油温度 轴承回油温度 汽封均压箱内压力 旋向 MPa MPa MPa MPa ℃ ℃ MPa 2 0.098 0.98 0.08-0.12 45 55 0.1-0.12 2 0.098 0.98 0.08-0.12 45 55 0.1-0.12 2 0.098 0.98 0.08-0.12 45 55 0.1-0.12 从汽机头部方向看为顺时针 1、汽轮机结构及性能
(1)B15-8.83/4.12型汽轮机为高压单缸、单轴、冲动背压式,由单缸、单轴组成通过刚性联轴器直接带动发电机,属于热电联供机组。
(2)汽轮机采用喷嘴调节,配汽部分有四个蒸汽室,每个蒸汽室装有一个调节阀,各自控制一组喷嘴,新蒸汽通过φ320(2-φ273×22)主汽阀后由四根主汽管(φ168×14)分别引入四个调节阀进入汽轮机。随着负荷的改变,各调节阀依次开启或关闭。
调节阀的动作由油动机通过齿条及凸轮配汽机构而控制,控制信号由电液转换器给出。 (3)主汽阀及调节阀
主汽阀及调节阀均为单座形式。主汽阀上装有自动关闭器,及自动关闭信号灯,当保安系统动作后必须再操作启动阀上手轮才能使自动关闭器重新开启。为了减少调节汽阀提升力,对采用的四只φ125口径阀都带有卸荷阀。
(4)喷嘴组采用焊接结构,材料为 Cr11MoV,焊接加工后汽道型线部分进行氮化处理。 (5)汽缸
汽轮机汽缸上、下两半用螺栓连接,材料为ZG15CrZMo1浇铸而成,排汽由两根φ273×8的排汽管引出。汽缸与蒸汽室、蒸汽室与调节阀喷嘴室均焊接成一体。其中1# 、2#调节阀安装在下半汽缸,3#、4#调节阀安装在上半汽缸。汽缸中分面连接螺栓为M120×4,材料采用25CrMo1VA。汽缸用下半汽缸猫爪型式支承在前后轴承座上。汽缸中分面法兰为高窄法兰。
在纵向及垂直方向均有定位的膨胀滑销以保证轴承座在热膨胀时中心不致变动。 汽封体由二只搭子和一个键直接固定在汽缸中,在搭子下装有垫片,用配准垫片的方法来定中心。
(6)汽轮机转子为整锻结构,材料为30Cr1Mo1VE,通流部分由一个单列速度级和三个压力级组成,轴上推力盘、汽机端联轴器均与轴整锻为一体。叶根采用“T”型,压力级叶片采用全三维型线。 (7)轴封
前后汽封外环采用蜂窝汽封,其余前后汽封环、隔板汽封均为梳齿式,汽封间隙为0.30~ 0.45mm。
叶轮均设有径向汽封,用以减少因热膨胀轴向间隙改变时的漏汽损失。径向汽封间隙为1.5mm。
(8)前轴承座
前轴承座可以在机架上沿纵向滑动。内部装有推力支持轴承、主油泵、危急遮断滑阀、保安操纵箱、(轴向位移等)测量支架、测速装置、启动阀等。
(9)后轴承座
后轴承座用螺栓和后座架相联,内部装有汽机后轴承、发电机前轴承、联轴器、相对膨胀发讯器、回转设备等部套。
回转设备装于后轴承座盖上,由电动机传动,通过蜗轮蜗杆及齿轮减速,盘车速度为5.4r/min。当主轴的转速高于盘车速度时,回转设备能自动退出工作位置。
汽轮机膨胀的死点在后轴承座下半的纵向键和横向圆销的交点上,受热后机组由此向前膨胀,在前座架上装有热膨胀指示器,指示机组热胀值。转子则以前轴承座内的推力轴承定位整体向后膨胀,汽缸与转子的相对膨胀差由装在后轴承座内的相对膨胀发讯器进行测量并自动指示差胀值。 (10)轴承
前后轴承采用相同的轴径(φ200)。排油温度是衡量轴承工作是否正常的主要标准。在运行时应注意各轴承排油温度是否一致,其差值不应大于5℃,如果相差过大,可能是各主轴承的油量分配不当,应在停机后进行调整,把温升偏高的主轴瓦的进油节流孔予以扩大,以增加其进油量。
汽机在运行时,当冷油器冷却水温小于等于33℃,轴承进油压力为0.08~0.12(表压)MPa,进油温度为45℃时,各轴承之回油温度应为55℃左右,若回油温度高于75℃时,保安系统应动作,否则会引起烧瓦事故。
机组各轴承的润滑油均由第二射油器供给,润滑油压0.08~0.12(表压)MPa。运行时轴承座振动之振幅应小于等于0.03mm。 发电机
发电机主要性能参数 序号 1 2 3 4 5 8 9 10 11 12 项 目 发电机型号 额定容量 额定电压 额定转速 功率因数 频率 效率 定子接线 定、转子绝缘 台数 MW KV r/min Hz % 单位 QF-15-2 15 10.5 3000 0.80 50 ≥97.2 YY接线 F级绝缘B级考核 1 数据 备注 低压除氧器
运行方式:定压 额定出力:400t/h 工作压力(表压):0.02MPa 工作温度:104℃
除氧水箱:120m3(有效容积) 中继水泵 序号 设备名称 型号 工艺参数 (流量单位:m3/h;扬程单位:m H2O) 1 锅炉中 ESB125-100-流量:160m/h 扬程: 120m 介质:104℃脱氧水,3 数量 3台 继水泵 315(Ⅰ)A 最高110℃,气蚀余量:4.0m 进口压力:P≤0.2MPa, 轴功率80.5KW 配套电机:Y280M-2-90KW/IP54/380V高原电机 2 锅炉中 继水泵 ESB125-100-315(Ⅰ)A 流量:160m/h 扬程: 120m 介质:104℃脱氧水,最高110℃,气蚀余量:4.0m 进口压力:P≤0.2MPa,轴功率80.5KW 配套电机:Y315S-2-110KW/IP54/380V高原变频电机 31台 3 疏水泵 ESB80-50-200 流量:50m/h 扬程:53 m 介质:≤90℃清水 气蚀余量:2.2m ,进口压力:常压 配套电机:Y160L-2-18.5KW/IP54/380V高原电机 3 2台 4 低位疏水泵 ESB65-40-200A 流量: 15m/h 扬程:40 m 介质:≤90℃清水 气蚀余量: 进口压力:常压 配套电机:Y132S1-2-5.5KW/IP54/380V高原电机 3 1台 高压除氧器
运行方式:定压 额定出力:270t/h 工作压力: 0.49MPa. 工作温度:158℃ 除氧水箱
给水箱型式及有效容积:卧式,双支座;80m3 水箱安装层高度: 15 m 给水泵
锅炉给水泵:锅炉给水泵共有四台,其中汽托泵一台,电动泵三台,。 给水泵流量要求
(1) 给水泵流量:168t/h--作为给水泵组的设计工况点。
(2) 给水泵最小流量:泵最小流量不超过额定流量的30%. 50.4t/h 设备规范
1 给水泵的技术数据
运 行 工 况 项 目 泵型号 进水温度 介质密度 进水流量 单 位 设计工况 ℃ kg/m t/h 3QDG185-1500 (1DG-12) 158 ≈909.9 168 运 行 工 况 项 目 单 位 设计工况 m/h t/h 出水流量 m/h 扬程 转速 轴功率 轴承座处的振动 进口 接口管子规格 出口 电机功率 电机电压 mm kW DN 100 1120 10000V mH2O r/min kW mm mm 33185 168 185 1500 2980 916.5 ≤0.03 DN 150 汽托泵
性能参数:
汽轮机型号参数: 形 式: 背压式
汽轮机型号:B1.12-3.92/437/0.7 设计参数 序号 1 2 3 4 5 6 7 8 9 项目 被驱动设备最大功率 汽轮机额定功率 汽轮机转速 转速调节范围 跳闸转速 进汽压力 进汽温度 排汽压力 排汽温度 单位 KW KW r/min r/min r/min MPa(a) (绝压) ℃ MPa(a) (绝压) ℃ 设计参数 916.5 1120 2980 2086~3280 3340 3.92+0.3-0.5 437 0.7+0.2-0.3 298 序号 10 11 12 13 14 15 额定点汽耗率 汽机额定进汽量 项目 单位 Kg/kw.h t/h MPa MPa ℃ ℃ 设计参数 14.6 16 0.6 0.08~1.5 35~45 60~65 螺杆油泵出口油压 轴承润滑油压 轴承进油温度 轴承回油温度 高压加热器
型式:立式盘管形 工艺参数
(1) 高压加热器数量: 两台(并列运行) 被加热水流量: 250 t/h(每台)
(2) 加热蒸汽参数: 加热蒸汽压力 3.82MPa(G)饱和蒸汽(合成废锅来的4.0MPa官网,温度为252℃)
加热蒸汽温度 247℃ 加热蒸汽量: 37.6 t/h 高加放空接到低除。
(3) 被加热水进口压力:15.0MPa 被加热水进口温度:158℃ 被加热水出口温度:210℃ 布袋除尘系统
锅炉尾部烟道排出的烟气,在引风机的抽引下进入布袋除尘器,除尘器中有12个腔室,在腔室前均有阀门,当要求烟气走旁路时,这些阀门关闭,旁通阀打开,则烟气直接通过引风机到烟囱排走。除尘器正常工作时,旁通阀关闭,12个腔室进口阀打开,烟气从布袋外侧进入布袋,灰尘被拦截,过滤后的烟气通过引风机进入总烟道,也称为原烟道。布袋拦截下来的灰尘,由空气压缩机提供的压缩空气以脉冲的方式进行清理,清理下来的灰尘落入除尘器下部,进入6个仓泵,再由空压机提供的压缩空气送到灰库,最后用罐车外运。 除尘器主要性能参数 设备型号:XLDM5680 设备名称:低压脉冲袋式除尘器 设备技术参数(单台): 序号 1 2 3 项 目 布袋除尘器出口烟气浓度保证值 布袋除尘器出口烟气浓度设计值 本体总阻力 单位 mg/Nm mg/Nm Pa 33内容 ≤50 ≤30 ≤1500 4 5 6 7 8 9 12 13 14 15 16 17 18 19 20 21 22 23 24 25 26 27 28 29 30 31 除尘器允许入口烟气温度 本体漏风率 壳体设计压力 每台除尘器室数 过滤面积 过滤速度 滤袋数量 滤袋滤料厚度 布袋使用寿命 脉冲阀数量 脉冲阀型式及规格 机械开阀时间 滤袋规格 滤袋允许连续使用温度 滤袋允许最高使用温度 滤笼材质 清灰形式 气源压力 气源品质 耗气量 灰斗接口规格 除尘器每个灰斗容积 灰斗加热型式 保温层/保护层材料 保护层厚度 除尘器本体使用寿命 3℃ % Pa 个 m/台 m/min 条 mm 小时 个 S ℃ ℃ Mpa m/min mm m 年 32140-180 ≤2.5 9100 12 5680 0.99 1512 2 ≥30000 108 进口、大于100万次 0.1 ф165×7250 120-180 200(瞬间) 20# 离线(可切换在线) 0.7 无油、无尘、无水 3 300×300 满足8小时贮灰 电加热(按120℃设计) 80mm岩棉/彩钢板 0.5 30 烟气氨法脱硫系统 1 工艺原理
氨法烟气脱硫技术以水溶液中的 NH3和 SO2反应为基础,在多功能烟气脱硫塔的吸收段氨水将锅炉烟气中的 SO2吸收,得到脱硫中间产品亚硫酸铵(简称亚硫铵,下同)或亚
硫酸氢铵的水溶液,见反应方程式为(1);在脱硫塔的氧化段,鼓入空气进行亚硫铵的氧化反应,将亚硫铵直接氧化成硫酸铵(简称硫铵,下同),见反应方程式。
SO2+H2O+xNH3=(NH4)xH2-xSO3 (1)
(NH4)xH2-xSO3+1/2O2+(2-x)NH3=(NH4)2SO4 (2)
在脱硫塔的浓缩段,利用高温烟气的热量将硫铵溶液浓缩,得到一定固体含量的硫铵浆液,硫铵浆液经旋流浓缩、离心分离、干燥、包装等工序,得到固体硫铵产品。 2 工艺流程简述
本装置烟气脱硫系统工艺采用氨-肥法,利用合成氨生产的液氨及生产过程中回收的 9.5%氨水吸收锅炉烟气中的二氧化硫,生成硫铵浆液,硫铵浆液在硫铵处理系统经浓缩并干燥后得到硫铵产品;脱硫后的净烟气由 150m 烟囱直接排放;脱硫过程蒸发的水分由工艺水系统以及氨水中的水补充。五台锅炉合用一套副产品硫铵处理装置,脱硫塔设置两台分别布置在烟囱水平砼烟道的外侧;一台脱硫塔(2#塔 T2201)承担三台锅炉脱硫负荷,另一台脱硫塔(1#塔 T2101)承担两台锅炉脱硫负荷。
脱硫工艺系统可分为两个大系统,即:脱硫吸收系统、硫铵处理系统。又可分为九个子系统,工艺子系统主要包括:
(1) 烟气系统;
(2) 脱硫吸收循环系统; (3) 氧化空气系统; (4) 吸收剂供给系统; (5) 硫铵处理系统; (6) 检修排空系统; (7) 工艺水系统; (8) 压缩空气系统; (9) 循环冷却水系统。 烟气系统
烟气系统的作用是:为烟气流经脱硫装置系统提供通道。烟气系统主要包括:烟道、原烟气挡板门、净烟气挡板门、旁路挡板门、隔断挡板门、密封风机、烟道膨胀节等。整个脱硫装置烟气系统的压降由位于脱硫系统上游的锅炉引风机来克服。脱硫装置运行时,原烟气挡板门、净烟气挡板门保持开启状态,旁路挡板门保持关闭状态。锅炉烟气经原烟气烟道进入脱硫塔进行脱硫化学反应,脱除 SO2后的净烟气经除雾器去除水雾后,经净气烟道返回烟囱两侧主烟道并经烟囱排放,原烟气和净烟气之间设置 100%烟气容量的旁路挡板门。在锅炉启动阶段和脱硫装置停止运行时,原烟气挡板门、净烟气挡板门关闭,旁路挡板门打开,使锅炉烟气通过旁路挡板门直接进入烟囱排放。脱硫装置共设置一套密封风系统,包括两台密封风机,一用一备。向七台烟气挡板门提供密封气。 脱硫吸收循环系统
吸收循环系统的作用是:从烟气中除去二氧化硫和其他酸性气体;将脱硫塔内形成的亚硫酸(氢)铵氧化成硫酸铵;利用原烟气热量进行硫酸铵溶液蒸发使之达饱和结晶生产出一定浓度的硫酸铵浆液;分离出烟气中夹带的水滴。每个脱硫系统均配置有一座多功能烟气脱硫塔、四台一级循环泵(二运二备)、一个循环槽、二台二级循环泵(一运一备)和二台结晶泵(一运一备)。烟气从脱硫塔中部浓缩段进入,经洗涤、降温后进入脱硫塔上部吸收段,在吸收段用含氨的循环液吸收烟气中的 SO2,反应生成亚硫铵;含亚硫铵的液体再进入塔底氧化段,被强制鼓入的氧化空气进一步氧化,氧化后的吸收液大部分补氨后继续参加吸收反应;部分回流至循环槽,通过二级循环泵送入脱硫塔的浓缩段,被 138℃的烟气加热,通过蒸发、浓缩后自流进入循环槽,得到过饱和的浆液,由硫铵结晶泵送入硫铵处理系统。脱硫后的清
洁烟气进入除雾器段,经除雾器除去烟气中携带的液沫和雾滴,使烟气中含水量小于 75mg/Nm3,然后由脱硫塔顶经净烟道排入 150m 烟囱排放。工艺水不断从塔顶补入,保持系统的水平衡。 氧化空气系统
氧化空气系统的作用是:将满足压力和温度要求的氧化空气送往脱硫塔的氧化段,将亚硫酸(氢)铵氧化为硫酸(氢)铵。本脱硫装置 1#、2#脱硫吸收循环系统共设置一套氧化空气系统。氧化风机共设置六台(五运一备,其中一期上四台,二期预留二台)。从大气中吸入的空气经氧化风机升压后经管路系统分配后送入 1#、2#脱硫塔氧化段,与溶液反应,将亚硫铵、亚硫酸氢铵溶液强制氧化成硫铵溶液,氧化后的空气进入浓缩段鼓泡混入到烟气中。氧化空气的量根据氧化反应需要计算,并考虑足够的过剩系数以确保氧化反应的完成。氧化段设置一定的液位以确保一定的停留时间。进入氧化段底部的氧化空气经汽液混合器被分散成无数微细的气泡并充分混合在浆液中,增大气液接触界面,保证氧化反应完成以提高亚硫铵的氧化率,本方案亚硫铵氧化率可达 99%以上。 吸收剂供给系统
吸收剂供应系统的作用是:将 9.5%的氨水、99.9%的液氨送到多功能烟气脱硫塔,满足脱硫的需要。
本脱硫工程设置一套硫铵处理系统,两塔共用。主要设备有旋流器、双级活塞推料离心机、振动流化床干燥机(预热风机、加热风机、冷风机、空气加热器、流化床干燥机、旋风分离器、引风机、螺旋输送机、旋转卸料阀等)、料液缓冲槽、尾气吸收塔、洗涤循环泵、包装机、码垛机以及连接管道等。循环槽的硫铵浆液浓度约为 5~30%(固体含量),通过结晶泵送入旋流器浓缩至浓度为 20~40%,依靠重力进入双级活塞推料离心机,经离心机分离后得到含水率~4%的固体硫铵,经螺旋输送机送入振动流化床干燥机,干燥后含水小于 0.2%,干燥后的硫铵经包装机后即可得到商品硫铵;旋流器、离心机的分离母液自流进入脱硫吸收循环系统循环槽重复使用;干燥尾气排入尾气吸收塔洗涤掉携带的硫铵粉尘后排入大气。硫铵综合楼设置硫铵库一座,容积按 5 台锅炉 BMCR 时尾气脱硫产生的 2 天(每天 24 小时计)的硫铵量设计。 检修排空系统
本脱硫工程设置一套检修排空系统。主要设备有:一座检修槽、一台检修泵、两个地坑以及相应的两台地坑泵等。当脱硫塔出现故障需要检修时,脱硫塔内的浆液通过一级循环泵或结晶泵输送至检修槽中。在脱硫塔重新启动前,通过检修泵将检修槽里的浆液送回脱硫塔。 脱硫塔区地坑用于收集、贮存脱硫塔区脱硫装置在运行扰动、检修、取样、冲洗过程中产生或泄漏的液体。脱硫装置正常运行时的浆液管和浆泵在停运时需冲洗,冲洗水通过地沟收集至地坑中,地坑的收集液通过自吸地坑泵送至脱硫塔循环使用,不外排。 工艺水系统
工艺水系统的作用是:接收工艺补充水,按工艺需求量进行补水,以维持系统内的水平衡。
本脱硫装置所需要的工艺水由界区外来的高压生产给水管线(W2b)引入,经计量后进入工艺水槽储存,经工艺水泵输送至各用水点。工艺水主要用户为: (1) 脱硫塔工艺补水;
(2) 脱硫塔除雾器冲洗水;
(3) 所有浆液输送设备、管路的冲洗水; (4) 脱硫塔烟气入口处的冲洗水。
主要设备有工艺水槽、工艺水泵以及配套管道等。 工艺水的消耗途径:随烟气蒸发、副产物带走水分。
界区外来的工艺水经计量后进入工艺水槽,工艺水经工艺水泵送至各用水点。 压缩空气系统
本装置的压缩空气系统为仪用气,气源由仪表空气管网提供,压力 0.4~0.7MPa,脱硫内压缩空气用量约为 4.5Nm3/min。 循环冷却水系统
设备冷却水采用闭式循环水,自循环水站Ⅰ引入,从热电站主厂房循环水管网(W7)接入,最终返回热电站主体装置(W8)。
设备冷却水的主要用户为:
(1) 所有泵的机封水(本部分用水排入地坑、槽罐后供脱硫系统使用)。 (2) 氧化风机、离心机等设备的冷却水。 3 装置主要设计参数
A 烟气进脱硫装置 SO2浓度
烟气进入脱硫装置分三种工况(设计):
(1) 烟气中 SO2 炉内脱硫 1.19%,炉外脱硫 4%(正常运行时),烟气含 SO2:12824mg/Nm3 ,含尘浓度≤50mg/Nm3。
(2) 烟气中 SO2采用炉内脱硫,脱硫率 80%,烟气含 SO2:3206 mg/Nm3,含尘浓度≤50mg/Nm3。
(3) 烟气中 SO2全部采用炉外脱硫,烟气含 SO2:16030 mg/Nm3,含尘浓度≤50mg/Nm3。 注:正常运行工况采用(1)或(3);事故工况采用(2)。 B 装置主要设计参数 序号 项目 1 2 3 4 5 6 7 8 9 10 11 12 13 14 15 16 17 18 装置容量 设计处理烟气量 设计煤种含硫量 脱硫效率 脱硫塔进口烟气尘含量 脱硫塔进口烟气温度 脱硫塔出口烟气温度 出口烟气 SO2浓度 出口烟气 NH3浓度 脱硫岛烟气压降 旋流器进料固体含量 旋流器进料流量 旋流器底流固体含量 硫铵成品含水率 硫铵含氮量(干)基 装置设计硫铵产能 单位 t/h Nm3/h % % ℃ ℃ mg/Nm3 Pa % m3/h % % % t/h 参数或指标 5×130 5×144076 5.19 ≥98 ≤138 ~60 16030 ≤400 ≤1500 5~30 250 20~40 ≤4 ≤0.2 ≥21 23.375(合18.7万吨/年) 8000 备注 锅炉蒸发量 故障温度180℃≤30min 循环槽出料浓度 100/150 GB535 GB535 硫铵实际产量视锅炉烟气量、燃煤含硫量而定 mg/Nm3 ≤50 设计进口烟气 SO2浓度 mg/Nm3 mg/Nm3 ≤10 离心机出料硫铵含水率 % 19 机组年利用小时数 h 20 21 年利用率 污水排放量 % t/h 98 0 C 主要原材料来源及其消耗
在设计条件,五台锅炉 BMCR 工况下,脱硫装置主要原料、辅助材料来源及消耗指标如下:
主要原材料来源及其消耗(设计、五炉两塔) 序号 1 名称 液氨 来源 单位 消耗量 备注 合成氨库 t/h P7303A/B 合成氨回收P7401A/B 1.0 MPa 低压蒸汽管网 高压生产给水管网(W2b) t/h t/h t/h 5.313联压力:≥0.6MPa 合使用 浓度:≥99.6%(wt) 5.937 t/h 单独使用 6.5 联合使用 57.5 50联合使用 56单独使用 140 压力:≥0.4MPa 浓度:9.5%(wt) 压力:1.0MPa温度:185℃ 压力:≥0.3MPa 温度:环境温度 浊度:≤1NTU 供水温度:32℃ 供水压力:0.5MPa 回水温度:42℃ 回水压力:0.25MPa 压力:0.4~0.7MPa 温度:环境温度 2 3 4 氨水 蒸汽 工艺水 5 循环水 循环水站Ⅰ t/h 6 仪表空气 仪表空气管网 Nm3/min 4.5 注:(1) 氨水:P7401A/B,流量 10.4m3/h、功率 18.5kW、扬程 210m,合成至热电管道系统配有减压阀,减压后压力约 0.7MPa。
(2) 液氨:P7303A/B,流量 11m3/h、功率 4kW、扬程 60m。该泵前压力0.4MPa,泵后压力约 1.0MPa。
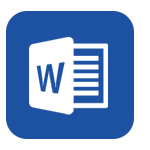





正在阅读:
热电课件01-02
数据结构试题2009~2010年度12-21
保安员工个人工作总结范文(汇总49篇)03-26
花的世界手抄报02-20
科技型中小企业技术创新的资金支持——基于生命周期视角的研究04-20
城轨行车课程设计资料06-07
001,项目安全检查整改督办管理办法实施细则(一)07-31
桩基检测施工方案 - 图文12-14
主风机检修安排及安全措施05-08
电化学噪声在腐蚀领域中的研究进展05-16
- exercise2
- 铅锌矿详查地质设计 - 图文
- 厨余垃圾、餐厨垃圾堆肥系统设计方案
- 陈明珠开题报告
- 化工原理精选例题
- 政府形象宣传册营销案例
- 小学一至三年级语文阅读专项练习题
- 2014.民诉 期末考试 复习题
- 巅峰智业 - 做好顶层设计对建设城市的重要意义
- (三起)冀教版三年级英语上册Unit4 Lesson24练习题及答案
- 2017年实心轮胎现状及发展趋势分析(目录)
- 基于GIS的农用地定级技术研究定稿
- 2017-2022年中国医疗保健市场调查与市场前景预测报告(目录) - 图文
- 作业
- OFDM技术仿真(MATLAB代码) - 图文
- Android工程师笔试题及答案
- 生命密码联合密码
- 空间地上权若干法律问题探究
- 江苏学业水平测试《机械基础》模拟试题
- 选课走班实施方案
- 热电
- 课件
- 大学生市场调查与分析题库及答案
- 外币会计练习及答案
- 圣地亚哥
- 上海财经大学硕士西方经济学真题2001年
- 工程力学复习题1
- 浅析提升中职生职业生涯规划能力的方法2011.6.15
- 自动化控制技术在煤矿通风设备维护中的应用
- 图形的联想教案
- 苏宁易购客服实习报告 - 图文
- 2014年人口和计划生育工作完成情况专题报告
- 甲级单位编制应急照明灯项目可行性报告(立项可研+贷款+用地+2013案例)设计方案
- 通风空调考试题及答案
- 三会一课制度
- 医师定考简易程序人员模拟卷子5
- 高中物理 第十七章 波粒二象性章末学案 新人教版选修3-5高品质版
- 关于支持中小企业技术创新的若干政策
- 五年级音乐上册教案
- 云南彝族服饰文化特点 - 图文
- 小学生数学口算练习110以内 43
- 基金业协会补充法律书意见书样稿