加强筋板料的理论分析
更新时间:2024-06-15 02:17:01 阅读量: 综合文库 文档下载
- 加强筋板图片推荐度:
- 相关推荐
3.4 Patran分析的基本理论
3.4.1 Patran分析的三个基本阶段
本文以带加强筋的S型弧面板弹簧作为研究对象,以MSC. PATRAN/NASTRAN为建模和计算工具,对其整体结构进行有限元分析,得到在各种工况下较为精确的应力及位移情况。
MSC.Patran有限元软件在解决静力问题时的三个基本阶段:
(1)前处理:读入或创建几何模型,设定材料和单元属性,施加载荷以及边界条件,进行有限元网格的划分。Patran软件能自动地划分大部分有限元网格,但必须提供相应的指令和设置参数。前处理过程中,每进行下一步操作前,都必须确保输入数据的正确性。
(2)数值分析:软件自动生成描述单元性能的矩阵,并把这些矩阵组合成表示有限元结构的大型矩阵方程,然后进行求解,得到每个节点上的场量值。
(3)后处理:有限元解和由它得到的数值被列出来或者用图示的形式显示出来。Patran后处理过程中除了列出或显示的变量外,其他操作都是自动的。在应力分析中,典型的显示包括动画、等值线、X-Y曲线图、云纹图等后处理功能。
3.4.2 Patran分析的一般流程
Patran建模和分析的一般流程,归纳如图3-2所示。
图 3-2静力分析流程图
3.5板弹簧静载有限元模拟过程
3.5.1单位制的选择
在有限元分析之前,首先要选择一套封闭的单位制,否则无法得到准确的结果,失去应有的意义。表3-1提供了PATRAN最常用的两套单位制。
表3-1两套常见的单位制
本次分析选择的一套封闭的单位制为“mm,MPa,N”。
3.5.2分析解算器的确定
在创建分析模型前,首先要确定分析的类型,再根据所要进行的分析类型选用合适的解算器。MSC.PATRAN/NASTRAN软件提供了多种解算器,如ABAQUS、ANSYS 5、MSC.Marc、MSC.Nastran、MSC.Dytran、LS-DYNA3D等。MSC.Nastran解算器是软件默认的解算器,本次模拟过程中也选用该解算器作为计算工具。
Nastran的静力分析功能支持全范围的材料模式,包括各向同性材料、正交各向异性材料、各向异性材料和随温度变化的材料等。分析类型除了最基本的线性分析、还有非线性分析、塑性、蠕变等。
3.5.3有限元模型的建立
建立贴近实际的几何模型是进行有限元分析的基础,同时对有限元分析结果的精确性也具有重要的意义。为获得较高精度的几何模型,要严格按照尺寸图的规格建立。S型弧面板弹簧板宽为150.00mm,展开总长为227.00mm,厚度为0.70mm,形状如图3-3所示。
a) 原始形状 b) 起筋形状
图3-3 S型弧面板弹簧
基于材料是均匀且各向同性、没有任何缺陷和损坏的假设条件下建立有限元分析模型。材料表面的划痕或加工痕迹等因素可能导致在分析过程中出现额外的应力,影响分析结果。
在有限元分析中,网格划分是一个非常重要的环节。网格划分的合理性有利于提高模拟结果的准确性和减少计算时间。确定划分方法,输入划分网格参数,首先对整个对象进行粗略划分。由于S弯处是主要的分析部位,在粗划分的基础上进一步细划分。有限元模型的创建可以通过网格划分参数的改变而发生改变。如果网格尺寸过大,则有可能分析的精度不高导致结果不够精确;如果尺寸过小,则计算时间将会延长,浪费资源。因此,细化的网格尺寸适中是确保计算准确又不失资源的前提。
c图为经过Patran软件划分的整体有限元模型,为了查看该网格划分的质量,通过Tool工具栏中check elems检查的网格均为六面体网格,由此可判断出网格质量较好,网格划分如图3-4所示。
(a) S弯未细化网格 (b) S弯细化网格
(c)细化网格的有限元整体结构
图3-4有限元模型
3.5.4材料属性
任何实体都是由各种材料构成的,材料是实际结构的承载体,Patran软件支持多种材料本构关系的定义。在静载分析过程中,需要定义材料的弹性模量和泊松比。这两个参数可由单向拉伸试验测得,如表3-2所示0Cr17Ni7Al不锈钢主要的性能参数 [56]。
表3-2 0Cr17Ni7Al不锈钢各项材料性能参数
为了与建模时的单位制保持一致,与之相对应的弹性模量E?2.1?105MPa,泊松比??0.3,屈服应力?s?1600MPa。
3.5.5边界条件与载荷的设置
边界条件是对模型的某一部分施加约束,使其保持不变(零位移)或移动给出量的位移(非零位移)。在静态分析工程中需要设置足够的边界条件,以防止模型在任意方向上产生移动或转动,否则,在计算过程中求解器将会中断而使模拟过程过早结束。
载荷是指直接或间接作用于结构上,使结构内部产生内力(如轴力,弯矩,剪力,扭矩等)和变形(如转角,裂缝等)。只有施加与实际相符的受力情况才能得到正确的分析结果。
如图3-3所示,板料上端面通过四个螺栓孔与汽车轮毂相连接,为了简化模型,在建模时将上部端面的四个螺栓孔补充完整,对应位置进行相应的约束。由于固定于轮毂上,所以上部端面在 、 、 三个方向的位移和转动均为零。下端曲面与地接触是主要承力端面,因此,将载荷施加在整个曲面。
3.6静强度结果及分析
3.6.1未减薄的结果分析
在曲面施加3000N均布载荷,得到S型弧面板弹簧的位移云图和应力云图,如图3-5所示:
a)应力分布图 b)位移分布图
图3-5应力与位移云图分布
由图a可以看出,S型弧面板弹簧主要承力部位位于与下端面弧连接过渡处,其最大应力值为169 MPa,此值远远小于屈服强度1600MPa;由b图可知板料边缘部分产生了最大变形为9.43mm。上述的变形值和应力值结果均符合实际情况。
3.6.2减薄后的结果分析
当所有条件不变,只有厚度依次减薄到0.6mm、0.5mm、0.4mm、0.3mm时,该结构的静力分布云图如图3-6、图3-7、图3-8、图3-9所示。
a)应力分布图 b)位移分布图
图3-6厚度为0.6mm时应力与位移云图分布
a)应力分布图 b)位移分布图
图3-7厚度为0.5mm时应力与位移云图分布
a)应力分布图 b)位移分布图
图3-8厚度为0.4mm时应力与位移云图分布
a)应力分布图 b)位移分布图
图3-9厚度为0.3mm时应力与位移云图分布
对不同厚度情况下的分析,可以看到S型弧面板弹簧随着厚度的减薄,应力和位移均呈现增大的趋势,具体变化如图3-10所示。
a)应力变化图
b)位移变化图
图3-10应力和位移的趋势图
由图中可以看出:厚度减薄为0.5 mm时,最大应力值和位移值的变化不是很明显。当厚度减薄到0.3 mm时,最大应力值和位移值陡然上升,此时,轮胎发生较为明显的变形。
3.7本章小结
详细介绍了用MSC.PATRAN建立起筋S型弧面板弹簧有限元模型的步骤,并对主要研究部位进行了细化网格的处理,将理论和实际结合起来,进行静强度分析,求出不同厚度的应力值和变形值。整个建模过程经历了创建几何模型、有限元模型,在模型上施加约束和作用力,求解等阶段。这几个阶段相互影响、交替进行,期间还要经过反复地修改和调试。根据计算结果,分析静强度是否满足要求,并比较厚度依次减薄的变化趋势。
第4章S型弧面板弹簧的疲劳寿命分析
4.1引言
随着计算机技术的发展,有限元法、可靠性法、优化设计、动态仿真设计等现代设计理论已经在金属结构的疲劳分析方面得到了深入的研究和应用,并取得了令人满意的效果。根据有限元获得的应力应变结果进行进一步的疲劳寿命设计方法己经在一些重要的工业领域(如飞行器、汽车、铁路、桥梁、船舶等)开始得到了应用。与传统试验相比,基于有限元方法的疲劳计算能够提供结构表面的疲劳寿命分布图,并可以直接判断出疲劳寿命薄弱位置,这样就可以预先避免不合理的寿命分布,从而减小技术创新的风险,降低开发成本,提高设计质量和效率,以追求最大的经济效益。
4.2有限元软件MSC.FATIGUE的介绍
许多有限元软件中已经添加了专门的疲劳处理模块,常用的包括ANSYS-SAFE、MSC.FATIGUE以及FE-Fatigue。本文采用较为先进的有限元疲劳分析软件MSC.FATIGUE对S型弧面板弹簧进行疲劳分析。
MSC.FATIGUE是MSC. PATRAN/NASTRAN其中的一个子模块,是专业的耐久性疲劳寿命分析软件系统。它的通用性很强,可以灵活预测各种疲劳寿命,
如全寿命分析、应变寿命分析、振动疲劳分析、多轴疲劳分析等。MSC.FATIGUE需要的几何和有限元结果从MSC.PATRAN中可直接获得,载荷工况从MSC.ADAMS或物理试验中获得,材料信息从MSC.FATIGUE的标准库或MSC.MVISION材料数据库中获得。
MSC.FATIGUE可以真实的预测产品的疲劳寿命,降低产品重设计的成本,避免过于保守的设计,最大程度满足客户长寿命设计要求,大大缩减了测试成本[55,57]。
4.3疲劳寿命分析基础理论
4.3.1疲劳理论
金属材料在应力或应变的反复作用下所发生的性能变化叫做疲劳。疲劳破坏是指结构在承受低于其极限载荷的反复作用下发生破裂的现象。
从微观上看,疲劳裂纹的萌生与发展都与局部微观塑性有关,但从宏观上看,在循环应力水平较低时,弹性变形占主要作用,此时疲劳寿命较长,称为应力疲劳或高周疲劳;在循环应力水平较高时,塑性应变起主导作用,此时疲劳寿命较短,称为应变疲劳或低周疲劳[58,59]。
4.3.2全寿命分析法
在制造质量良好、正常使用条件的情况下,S型弧面板弹簧的疲劳属于高周疲劳,因此,本文在运用MSC.FATIGUE软件对其进行有限元分析时,采用的是S-N总寿命分析法。它以零件的应力为基础,采用雨流循环计数法和Palmgren-Miner线性累积损伤理论(简称为Miner理论)进行全寿命分析。Miner理论认为损伤与应力循环数成线性关系,当总损伤度 时,材料即发生疲劳破坏。
全寿命分析过程中可以设置平均应力修正和置信参数等不同的分析参数,还可以指定表面抛光和热处理方法。
运用全寿命分析方法,通过计算机模拟仿真,从疲劳云图上得到结构的疲劳寿命分布,计算出结构的使用寿命,确定结构的允许使用周期。另外还可以为设计人员快速比较不同设计方案、疲劳性能的优劣或改进设计提供较直观、全面的依据。
4.3.4疲劳寿命分析步骤
疲劳分析一般在有限元分析结束之后进行。将MSC.FATIGUE界面启动,设置疲劳分析方法为S-N法,将应力结果的单位改成MPa。
在疲劳分析之前要设置三个方面的基本数据输入,包括:
(1)材料信息:描述材料和部件的循环疲劳特性,主要包括材料的静力学特性、材料的S-N曲线、以及表面处理等,由MSC.FATIGUE材料数据库管理器PFMAT生成。
(2)载荷信息:指的是构件承受随时间变化的交变载荷,包括对称循环载荷、脉动循环载荷以及随机载荷。疲劳载荷对于寿命分析的结果至关重要, MSC.FATIGUE是通过时间历程数据库管理器PTIME生成。
(3)几何信息:是指有限元模型以及应力应变计算结果。准确的应力应变结果是保证寿命分析正确的前提。
MSC.FATIGUE具体分析过程如图4-1所示:
图4-1疲劳寿命分析流程图
4.4疲劳寿命分析参数的设置
4.4.1循环载荷
在进行静强度分析时,所受载荷为常数。在实际的工作中,S型弧面板弹簧所受的载荷具有随机性,但从统计学的角度来看,依然具有某种循环特征,因此可以用循环载荷来代替。S弯板在工作时,接触橡胶皮带的一侧受到拉应力而另一侧受到压应力,当受载应力为零时退出工作,因此,循环载荷确定为脉动循环应力。假设载荷为弦周期函数变化,波形如图4-2所示。
图4-2循环载荷图
建立的循环载荷要与有限元载荷工况关联起来才能把载荷真正的施加在有限元模型上,从而才可正确进行求解,相应关联设置如图4-3所示。
图4-3载荷谱与相应工况关联
4.4.2材料的S-N曲线
4.4.2.1材料属性的介绍
S型弧面板弹簧选用的是631不锈钢(0Cr17Ni7Al不锈钢)材料,这是一种弥散强化不锈钢,其化学成分中有沉淀强化元素,其具有稳定的弹性、很高的抗拉强度、良好的耐腐蚀性能、较好的耐疲劳性。
631不锈钢的力学性能参数见表3-2,屈服强度为1600MPa,弹性模量为210000MPa。在第五章中,由实验确定了材料的抗拉强度为1800MPa。 4.4.2.2 S-N曲线的建立
本课题采用的是0Cr17Ni7Al不锈钢材料,材料库中没有相对应的材料信息,所以必须新建此材料的性能数据库。S型弧面板弹簧的疲劳特性参数如表4-1所示。根据表4-1的数据在材料数据库管理器PFMAT中添加材料的S-N曲线,具体形状如图4-4所示。
表4-1 631不锈钢材料的特性参数
图4-4 材料的S-N曲线
传统的S-N曲线理论认为,低于疲劳极限的应力循环将不影响疲劳寿命。但试验己证明,一旦在结构或部件中萌生了裂纹,低于疲劳极限的应力循环也能导致裂纹扩展,并产生疲劳损伤,从而使寿命大大降低。同时低于疲劳极限的应力循环在载荷谱中所占的百分比较高,对疲劳寿命肯定时有影响的。因此,在计算疲劳寿命时必须将S-N曲线进行修正,修正后的S-N曲线及相应的关联设置如图4-5和图4-6所示。
图4-5修正后的S-N曲线
图4-6材料属性与相应工况关联
在建立S-N曲线过程中会出现一系列材料断裂力学特性参数,具体如图4-7所示。图中表明了在两种不同环境下,起筋板弹簧的裂纹拓展性能参数。根据此参数可以在研究发生裂纹后利用疲劳裂纹扩展数据对疲劳裂纹进行分析,推导出裂纹扩展寿命的分布规律。 a)大气环境下 b)水环境下
图4-7裂纹拓展参数图
4.4.3平均应力
在有限元计算结果中,由于所有节点处应力的整体分布都能够得到,并可以直接提供给MSC.FATIGUE进行疲劳分析,所以应力集中系数取为1。
多数疲劳数据是根据试验方法采集到的,而实验室条件是包含平均应力的影响。本次的有限元分析采用理想的条件,不考虑平均应力,同时结构无表面抛光和热处理情况,平均应力修正和应力组合方式的设置如图4-8所示。
图4-8平均应力修正
4.5疲劳寿命分析结果
4.5.1未减薄的结果分析
通常,疲劳损伤首先发生在最大局部应力节点上,由于循环载荷的作用,疲劳裂纹也产生于此处,裂纹扩展最终导致板料疲劳失效。因此,对应力最大位置进行疲劳分析是重要的。
第三章已经给出材料在静载荷作用下的应力云图,从图3-5中可以看出,S弯板的最大弯曲应力发生在承力部位与下端弧面连接过渡区域,因此,该过渡区域被认为是疲劳分析的研究对象。
经过疲劳寿命分析之后,得到该模型的疲劳计算结果,图4-9为该模型的疲劳寿命云图,单位为循环周数。
图4-9疲劳寿命云图
从图4-9中可以看出:该S型弧面板弹簧结构的最小寿命为3.58E8次循环,出现在承力部位与下端弧面连接过渡处,出现在应力最大部位,在正常的工作环境下可以工作将近7.5年,下端弧面过渡处为薄弱环节。该S型弧面板弹簧除下端弧面过渡处以外的结构在载荷作用下为都具有无限寿命。
4.5.2减薄后的结果分析
当厚度依次减薄到0.6mm、0.5mm、0.4mm、0.3mm时,该结构的疲劳寿命分布云图如图4-10、图4-11、图4-12、图4-13所示。
图4-10 厚度为0.6mm时疲劳寿命云图
图4-11厚度为0.5mm时疲劳寿命云图
图4-12厚度为0.4mm时疲劳寿命云图
图4-13厚度为0.3mm时疲劳寿命云图
从图4-10至图4-13中可以看出:S型弧面板弹簧的薄弱环节均为承力部位与下端弧面连接过渡处,随着厚度的减薄,其受损情况越来越严重。同时还可以观察到疲劳寿命的大致区域与静力分析中较大应力的分布相类似。
根据累积疲劳准则,不同厚度的S板的弯曲疲劳寿命如图4-14所示。从图4-14中可以看出,开始随着厚度的增加寿命会有一个较大的上升的趋势,而最终将趋于平缓。
图4-14疲劳寿命趋势图
4.6本章小结
在介绍有限元疲劳分析软件MSC.FATIGUE的基础上,利用该软件对不同厚度下的S型弧面板弹簧进行了指定循环载荷历程下的疲劳分析。通过分析,得出该结构的疲劳寿命分布云图,直观显示出各个部分的疲劳寿命,为结构设计改进和完善以及疲劳研究提供了直观的理论依据。
第5章 拉伸试验
5.1引言
MSC.Fatigue材料数据管理库中没有0Cr17Ni7A1不锈钢材料的疲劳寿命曲线,因此,在模拟寿命过程中需建立该材料的性能参数。而在建立疲劳寿命曲线过程中需要用到材料相关的一些数据,其中最主要的是强度极限(UTS),该参数通过单向拉伸试验方可得到。
常温、静载下的拉伸试验是金属材料力学性能最基本、应用最广泛的试验,也是了解材料力学性能最全面、最方便的试验。通过拉伸试验,可以比较全面地测定材料的力学性能,如弹性、塑性、强度、断裂等力学性能指标。这些性能指
标对工程应用具有极其重要的作用。本试验主要是测定0Cr17Ni7A1不锈钢在静载拉伸过程中的强度极限值[60]。
5.2试验前的准备
5.2.1试验设备的选择
(1)VF1600高温真空炉 此炉型号为VF-1600,加热腔体采用极低热导率和比热容的氧化铝纤维制品,保证了炉膛快速升温和低储热;加热元件选用U型硅钼棒,加热棒分布炉膛两侧,有利于炉内温度场的均匀分布。此炉最高温度可达1650℃,其工作室尺寸为450mm×200mm×200mm,实物如图5-1所示。
(2)Inspekt100kN电子万能高温试验机 此试验机的型号为Inspekt Table,测量范围为1-100kN,拥有高速智能化电控系统,可自动精确地控制试验过程,具有强大的数据采集功能,可实现等速率加荷、等速率变形以及等速率位移等试验,实物如图所示。
(3)夹持装置的选择 试样的装夹要选择适合的夹具,以便装卸。由于试验板料的强度较高,普通的靠摩擦力作为拉力的夹具不足以支撑试件被拉断时试件就已脱落,因此,此拉伸试件在两端设计了10mm的圆孔。既而,选择了带有螺栓的夹具进行固定,实物如图5-2所示。
图5-1箱形高温电炉
a)电子万能试验机 b)夹具
图5-2拉伸试验装置
5.2.2试样的准备
拉伸试样由夹持部分、过渡部分和平行部分构成。试样两端较粗部分为夹持部分,其形状和尺寸可根据试验机夹头情况而定;试样两夹持段之间的均匀部分为平行部分,即为试验段部分;夹持部分和均匀分间为过渡部分,常用圆弧进行光滑链接,以减少应力集中 [61] 。
0Cr17Ni7A1不锈钢的化学成分见表5-1。
表5-1 0Cr17Ni7A1不锈钢的主要化学成分(%) [62]
进行试验前,首先将板料制成标准试样。试验表明,试样的形状和尺寸、表面粗糙度和形位偏差等因素对试验的结果具有一定的影响。为了避免这些影响和便于机械性质的数值可互相比较,所以试件的尺寸依据国标GB3076-82标准制作,拉伸试样尺寸图如图5-3所示。和以往的拉伸件不同,此试件在末端设计了两个圆孔,经过多次模拟设计确定了其位置和尺寸,以保证对材料性能的影响达到最小值。按照图5-3的尺寸将0Cr17Ni7A1不锈钢钢板线切割成标准试样。其次,将试件同时进行加热处理,温度为480℃,并保温一小时,空冷,实物如图5-4所示。加热及保温过程均在真空炉内进行。在热处理之前,要将试件擦拭干净,避免杂物侵入试件中,影响实验结果。[59-62]
图5-3拉伸试样尺寸图
图5-4拉伸试验前坯料
5.3试验过程
5.3.1试样的安装
首先将试验机的上横梁向上移动一段距离,留出足够的空间安装试件。试件一端安装在卡具内,并用螺栓固定。缓慢降下上横梁到适合的夹持位置,将试件另一端夹紧在卡具内。开动试验机,预加少量载荷(当位移显示稍大于零时即可),然后将位移归零。
在安装时要尽量保持试样的垂直,因为在进行拉伸试验时,外力只有通过试样轴线才能确保材料处于单向应力状态。
5.3.2进行试验
开动试验机,以缓慢的速率均匀加载,直至试件被拉断,拉断后的实物如图5-5所示。记录并整理试验数据。
图5-5拉伸试验后坯料
5.3.3结束试验
关闭机器,取下试件,清理试验现场,并将试验机及相关工具复原。
5.4试验数据的处理
根据整理的数据,用Origin 8画出两试件的应力-应变图以及真实应力-应变图,分别如图5-6和图5-7所示。 从两图中可以看出,拉伸图最初一段都是曲线,这是由于试件在开始受力时,其两端的夹紧部分在试验机的夹头内有一定的滑动,但是这种滑动不会影响材料抗拉强度值。
a)试件1 b)试件2
图5-6名义应力-应变曲线
a)试件1 b)试件2
图5-7真实应力-应变曲线
由图5-6可知,试件1的名义抗拉强度 ,试件2的名义抗拉强度 ,两者的平均值 。由图5-7可知,试件1的真实抗拉强度 ,试件2的真实抗拉强度 ,两者的平均值 。通过比较,虽然两平均值相差不大,但是图5-7中的数据更能反映出材料的真实抗拉强度大小,所以在进行寿命模拟过程中,抗拉强度的值选择 。
5.5本章小节
本章采用试验的方法确定了0Cr17Ni7A1不锈钢材料的抗拉强度,为疲劳寿命分析提供了材料设置参数,从而新建符合实际的S-N曲线。
本章详细介绍了试验的各项工作,用Origin对数据进行了处理,同时对名义应力-应变曲线和真实应力-应变曲线进行了比较,虽然两者得到的抗拉强度值相差不大,但后者更能体现材料性能的真实情况,因此,选用后者并对其取近似,最终选定材料的抗拉强度 。
第二章 大型齿轮热模锻成形工艺分析 2.1引言
一般情况下,尺寸、参数及重量比常规情况都大的齿轮称为大型齿轮,通常认为其外径大于500mm。大型齿轮可分为大模数齿轮与大尺寸齿轮两类。大模数齿轮模数大、齿槽深、展成长度长,多为轴齿轮,且一般为人字齿轮或斜齿轮,在轧钢机械中应用较为广泛;大尺寸齿轮主要是指其外径大,这类齿轮通常模数不是很大,但齿数较多、重量也较大,外形多为盘形。本文主要针对大尺寸齿轮进行研究和探讨。
在齿轮的生产中,大型齿轮通常是由大钢锭直接锻造而成,其锻造工序一般为:钢锭拔长-下料-镦粗-冲孔-整形。但由于钢锭吨位较大,为保证锻件内部充分锻透,锻造时需要足够大的力才能使材料成形,而液压机的公称压力又有限,所以锻造的尺寸和截面厚度都受到限制。
2.2镦挤工艺
齿轮镦挤成形工艺是指将圆柱形坯料放入带有齿形的凹模型腔中,凸模施加轴向载荷,从而使坯料发生镦粗变形在径向上产生流动并逐渐充满整个型腔,其工艺简图如图2.1所示。此工艺为最基本的外齿轮成形方法,坯料金属通过轴向自由镦粗、开始充填齿腔及齿形充满三个阶段完成齿轮的最终成形。
图2.1 直齿圆柱齿轮镦挤工艺简图
采用镦挤工艺时,径向流动的金属与轴向的力相垂直,所受沿程阻力较大,金属自由流动面积越来越小,在成形终了阶段,金属可以自由流动的区域几乎接近于零,齿形充填也更加困难,便会出现成形力陡增的现象,如图2.2所示。根据金属塑性成形特点,可用减缩比R的变化来表示金属的流动状况,其公式为: (2-1) 式中,A表示坯料的全面积;F表示不与模具发生接触的自由面积。
图2.2 镦挤成形时成形力与成形时间关系图
由此可见,F越小,减缩比R越大,金属流动也就越困难。随着坯料镦挤过程的进行,F越来越小,R最后接近1,齿轮成形越来越困难,成形力陡升。此时,成形力的增加对齿形的充填并没有太大的意义,反而使得模具磨损加剧,寿命降低。所以,镦挤工艺成形齿轮不但成形力较大,而且在齿轮端部由于充填不足会有塌角产生,齿根也会有微裂纹。
2.3分流锻造思想
20世纪80年代,日本学者Kondo将分流锻造理论引入到齿轮锻造成形工艺中,使齿轮锻造技术的发展迈上了一个新的台阶[46]。分流的主要原理就是在坯料与模具组成的闭式模腔中设置分流通道,使得金属具有自由流动表面,从而控制减缩比的增加,有效降低成形力,促使锻件更易成形。对于齿轮锻造而言,分流可大大减缓成形终了时载荷的陡增,还能促进齿轮端部角隅的填充。 2.3.1孔分流与轴分流
在传统镦挤工艺的基础上,应用分流法可成形出良好的齿轮。目前,齿轮锻造采用较多的主要为孔分流法与轴分流法,其工艺简图如图2.3所示。孔分流是在坯料上留有中心孔,锻造时金属在流向齿形型腔的同时仍有向心的流动,使内孔趋于闭合;轴分流是在凸模上预留有中心孔,使得金属填充型腔时也会沿着轴向向外部流动。
图2.3 直齿圆柱齿轮孔分流与轴分流成形工艺
孔分流或轴分流的实质是增加了金属的自由流动面积,降低了减缩比与成形力,使得齿形充填更加饱满,但分流孔或分流轴的直径大小也会影响齿轮的成形质量。分流孔直径若太大,由最小阻力定律可知金属会优先流向阻力小的分流通道,导致齿形充填不完整;分流孔直径若太小,就会先于齿形闭合,从而达不到分流减压的目的,成形力依然很大。对于分流轴直径而言,也存在同样的情况,除此之外,由于分流通道开在凸模上,变形过程中会使得凸模受力很大,从而加剧了凸模的损坏。 2.3.2约束分流
孔分流或轴分流虽然可以使成形力大幅度降低,但在相对较低的工作压力下依然很难保证齿形充填饱满,而且变形过程中金属要流向分流口,不仅会造成材料浪费,而且还需增加后续去除工序。于是,后人在孔分流和轴分流的基础上提出了约束分流。其实质是通过在分流口处施加一定的约束阻力,迫使金属更多的流向齿形型腔,保证齿形完全充满时金属仍有自由流动面积,即减缩比不等于1,而且越小越好。目前人们采用较多的约束分流为约束孔分流与约束轴分流,其工艺简图如图2.4所示。
图2.4 直齿圆柱齿轮约束孔分流与约束轴分流成形工艺
约束孔分流通过在凸模上设置上下对称的凸台来限制金属的流动,调节凸台机构的约束直径D和约束深度L可以控制约束力的大小,使得齿形易于充满;约束轴分流通过在分流口处设置小芯棒来限制金属的轴向分流,调整分流轴直径
D和芯棒直径d来改变约束力的大小,促使齿形易于充满。
2.4局部加载方式及其特点
目前,对于齿轮锻造工艺虽然采取了分流减压的思想,但其加载方式却局限于整体加载,锻造时所需的成形载荷数值还是很大,制约着该工艺的发展。
局部加载是指成形过程中仅对坯料的某一部位施加压力,从而完成整个工件的成形。采用局部加载方式时,坯料内部沿主作用力方向上的受力面积不断增加,其应力的绝对值越来越小。在齿轮坯料的齿形部位进行局部加载,其受力接触面积相比整体加载时要小得多,因而成形力可得到大幅度降低,更易于齿形的填充。从某种意义上来说,局部加载就是所谓的轴向分流。
2.5大齿轮热模锻成形工艺原理
本课题将对大尺寸渐开线标准直齿圆柱齿轮锻件进行研究,表2-1所示为其基本尺寸参数。
表2-1 齿轮尺寸参数
齿轮材料选用42CrMo合金钢,对应的美国标准为
AISI-4140[70-2200F(20-1200C)],其化学成分、热性能与力学性能分别见表2-2、表2-3、表2-4。
表2-2 42CrMo主要元素的化学成分(%)表2-2(续表)
表2-3 42CrMo的热性能参数 表2-4 42CrMo的力学性能参数
42CrMo钢属于超高强度钢,具有高强度和韧性,淬透性也较好,无明显的回火脆性,淬火时变形也很小,调质处理后有较高的疲劳极限和抗多次冲击能力,低温冲击韧度良好,高温时有高的蠕变强度和持久强度,用于制造强度高和调质截面更大的锻件。该钢通常将调质后表面淬火作为热处理方案。 2.5.1热模锻成形工艺方案
所研究齿轮直径在一米以上,属于大尺寸锻件,因此锻造过程中需要的变形力是非常大的。鉴于此,本文优先采用热锻成形方式对该齿轮进行加工。除此之外,综合考虑各种因素,最终决定在传统镦挤工艺上进行改进,灌输进分流锻造技术思想,主要以设计坯料形状及尺寸参数为主,具体成形工艺简图如图2.5所示。
1— 凹模 2—坯料 3—上凸模 4—下凸模
图2.5 工艺简图
成形过程中,中低边高的半空心坯料成为整个工艺的关键控制因素。随着凸模下行,坯料金属在充填齿形型腔的同时也流向中心低凹处,当齿形完全充满时最好希望坯料中部正好填平,与齿形端保持一致的高度。若中间低凹处先于齿形充满,借助预留有中心孔的凸模,金属仍有自由流动的地方,能够确保齿形完全充满。这样的坯料形状决定采用局部加载的方式,可以使成形载荷得到大幅度降低。因此,合理设计坯料形状、控制好坯料各个尺寸参数,以便于得到最好的成形效果是本文研究的重点。
锻造时,坯料从加热设备中取出,迅速放入模膛,不考虑过程中的热传导以及热量散失,一次性锻出成形件,最后再对齿形进行机加工修整。该过程没有预锻、终锻工序之分,可称之为“一火一锻”。
42CrMo合金钢的锻造温度范围在20—1200℃之间,始锻温度定为1000℃,该温度下材料的变形抗力较低,齿轮的成形可全部完成。
其工艺流程如下:坯料一加热至1000℃一除氧化皮一锻造一热切飞边一去氧化皮一空冷到室温一机加工。 2.5.2一工序一火锻造工艺的优点
根据上述工艺分析,本课题研究决定采用半空心形状毛坯闭式镦挤热锻工艺来成形大尺寸齿轮,其工艺具有如下几个优点:
1、此工艺只须用一套模具就能完成以往两套模具才能完成的齿轮锻造成形,缩短了工艺过程,减少了模具用量,降低了生产成本;
2、借助分流锻造思想设计半空心毛坯形状,同时凸模上预留中心孔,使金属在锻造过程中始终具有自由流动的地方,保证齿形很好的填充;
3、采用局部加载的方式,有效降低成形载荷,增加了模具寿命。
2.6本章小结
本章分析介绍了分流锻造技术以及传统直齿圆柱齿轮镦挤工艺,针对所要研究的大尺寸齿轮,确定了在传统镦挤工艺上引进分流锻造思想的一火一锻成形工艺方案,该工艺主要以坯料形状尺寸参数作为主要控制因素,并采用可以降低成形力的局部加载方式,最后分析了该工艺的优点,为之后所要进行的有限元数值模拟提供了可靠的依据。 (1)冷锻
冷锻技术是使金属在室温下体积发生塑性变形,其变形方式有冷挤压和冷镦挤。近年来冷精锻技术发展迅速,其原理是采用闭塞锻造技术成形。闭塞锻造指
的是在上下模间隙不变、通过合模而形成四周封闭的型腔中,借助两个以上凸模的相对运动,使金属坯料成形为具有一定形状的零件的锻造成形技术。我国冷精锻技术起步于20世纪50年代末。1990年以来,为了满足汽车、摩托车产量快速增长的需求,多工位冷精锻、闭式模锻等技术被陆续使用到生产中。
河南科技大学的于静针对齿轮冷精锻成形中成形载荷过大和齿形充填不足等主要问题,运用空心毛坯闭式镦锻—空心分流一模两击式镦挤工艺冷锻成形直齿圆柱齿轮,并通过数值模拟对其可行性进行验证,分析了成形过程中的金属流动规律以及齿轮分流孔的临界点,得到了模数为2的直齿圆柱齿轮在模具极限载荷范围内的理论成形范围曲线,最后还优化得出该工艺下毛坯体积的计算公式,为直齿轮的实际生产提供了可行性参考依据。
合肥工业大学的龚冬梅利用浮动凹模与孔径向分流耦合的工艺方法对大模数直齿圆柱齿轮进行冷锻成形,并为其设计了相应的冷精锻模具结构。数值模拟结果显示该工艺可使齿形充填完整,而且成形力大大降低。但由于时间与试验条件的限制,该工艺并未通过试验验证其可行性,距离最终的实用化还需进一步努力与完善。
J.H.Song等人对锥齿轮的冷精锻工艺进行三维有限元数值模拟,对比分析了不同加载方式、冲头位置、坯料直径下齿轮的成形状况,为该工艺设计了相应的模具并通过试验进行验证,结果证明还需补充额外的夹紧装置以提高模具寿命。
Nagai.Y为具有较大沉孔的直齿圆柱齿轮设计开发出一种成形新工艺,即将杯形件作为预制坯,通过拉延、整形、变薄拉延和压缩四步对其实现多工步冷锻成形。
近20年以来,齿轮热模锻生产有了很大发展,尤其是基于开式模锻改进而来的热精锻工艺应用越来越多。普通模锻时会在水平方向产生较大飞边,热精锻通过对坯料体积进行精确计算,将其改变为在垂直方向上产生较小飞边,或者是在封闭的模膛内不产生飞边。生产设备主要有热模锻压力机、螺旋压力机、摩擦压力机等,生产工艺也由最初的开式模锻、两火两锻发展成闭式热模锻、一火两锻成形。
Taylan.Altan等人借助DEFORM软件对空心直齿圆柱齿轮毛坯的三工位热锻成形过程进行有限元数值模拟,根据模拟结果分析预测了可能出现的折叠缺陷,并在此基础上改进成形工艺参数,最终得到无缺陷零件。
温锻内容与冷锻大致相同,通常是指将坯料加热到室温以上再结晶温度以下
而进行锻造的一种锻造方法。图1-5给出了不同变形方式的温度范围,温锻成形主要发生在温变形区的非蓝脆区和非相变区。采用温锻工艺时,锻件无需经过磷化处理和中间处理便可满足精度及表面粗糙度要求。
温锻时材料温度范围要根据钢材的不同化学成分来决定。该温度应在保证金属塑性有明显提高的同时变形抗力显著下降,还要兼顾金属未发生强烈氧化。采用碳钢与合金结构钢作为温锻材料时,一般温锻温度为550-750℃,采用奥氏体不锈钢时温锻温度为250-350℃,为保持温锻的顺利进行,温锻时可采用胶体石墨剂作为润滑剂。
齿轮是有齿的能相互啮合的轮状机件,是机器上最常用、最重要的零件之一。齿轮的分类有很多种,由于其传动是靠主动轮齿廓推动从动轮齿廓而实现,所以将其主要按齿廓进行分类的话,可分为渐开线齿轮,其次是摆线齿轮和变态摆线齿轮,还有圆弧齿轮和抛物线齿轮等。
冲压法多用于薄齿材料的冲裁,采用精冲模直接冲裁一些外形结构简单的小模数齿轮,可得到满足生产要求的齿轮。对于板状齿轮的冲裁,首先应将所要冲制齿轮的尺寸形状作为标准加工出冲模。冲裁时,位于凸凹模之间的板料在厚度方向上发生剪切变形而冲出齿轮。这种方法目前多用于板型材料,由于冲裁过程中成形件受到较大的冲击载荷,导致齿顶部位有塌角出现,板料厚度明显减薄,模具寿命较低。
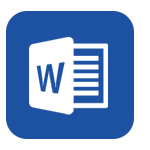





正在阅读:
加强筋板料的理论分析06-15
浅谈小学体育的创新式教学方法03-04
深基坑安全监理细则06-22
与父亲离别的作文500字06-26
华为手机环境分析05-01
《祖国,我终于回来了》教案(第一课时)04-17
2011年特岗教师面试题及参考答案108-18
第5章 宏观经济学 复习总结及课后答案08-18
资源分配与映射 - 图文04-20
- 高一物理牛顿运动定律全套学习学案
- 水处理一级反渗透加还原剂亚硫酸氢钠后为什么ORP会升高
- 毕业设计(论文)-正文董家口 - 图文
- 荣盛酒店经营管理公司录用通知及入职承诺书II
- 第二讲 大学英语四级快速阅读技巧
- 质量管理体系文件(2015年委托第三方医药物流配送企业专用版本)
- 214071收款办法
- 苏轼对《文选》选文的评价
- 《诊断学基础B》1-8作业
- 广东省东莞市高一数学下学期期末教学质量检查试题
- 海南电网公司VIS推广应用管理办法
- 红星照耀中国习题
- 苏教版小学语文六年级上册期末复习资料之生字词整理
- 局域网组建与应用—王向东
- 税务稽查内部管理文书样式
- 环保社会实践调查表
- 九年级思品第一单元复习
- 2016年全国注册咨询工程师继续教育公路路线设计规范试卷
- 毕业设计-青岛港董家口港区防波堤设计
- 撞背锻炼方法与益处
- 强筋
- 板料
- 理论
- 分析
- 中国汽车国家标准和行业标准
- 演讲稿《一位务林人的笑容》等三篇
- 名师指导:12月四六级冲刺备考
- 江苏省南京市鼓楼区2018年中考一模物理试题(WORD,有答案)
- 20090713钱建民同志在绍兴市城市管理委员会第二次成员单位会议上
- 殷毅杰一调研报告 - 图文
- 2017江苏高考对联题目精选精炼
- 课后习题
- 项目产值及工程信息填报管理办法(汇编版)
- 英文-MSDS水泥基防水材料
- 2012年自主招生安徽录取名单
- 最新审定青岛版小学数学六年级上册百分数与分数小数的互化(精编
- 2011届高考复习最新3年高考2年模拟(课改):专题二十+近
- 孔子的75句名言及注释
- 2008年四川初中数学联赛(初二组)决赛试题 参考解答及评分细则
- 哲学与人生第一课练习题
- 《感恩老师》主题班会活动程序和主持人串词
- 《建筑施工高处作业安全技术规范》(JGJ80-91)条文说明
- 道路及广场工程施工组织设计 - 图文
- 高中化学会考复习重点资料罗平三中袁攀