工作研究教材资料
更新时间:2024-01-14 20:35:01 阅读量:1 教育文库 文档下载
- 研究教材工作的会议记录推荐度:
- 相关推荐
第 1 頁,共 41 頁
工業工程基礎
(工作研究)學習題綱
2 0 0 3. 1 0. 1 8
第一節 概 述
第 2 頁,共 41 頁
一、什麼是工作研究
工作研究(Job study或Work Study)是工業工程的基本組成部分,其內容是對人們所從事的工作進行分析,設計,改善和管理。早期主要是對工廠中的工作方法進行分析、調查研究,以制定科學中的工作方法和合理的標準時間(勞動定額)。故工作研究又稱為動作和工時研究(Motion and Time Study)。 1.工作研究的原理 它的基本原理是:
(1). 在做同一件事(或任務)時,通常總是有許多不同的做法(方案),然而,若對各種方法進行科學的研究和分析,如經過對人、財、設備、能源、廠房、信息等進行分析研究和綜合平衡后,總會發現有一種方法(方案)在當時、當地條件下是最可行、最可取的;
(2). 選取最佳方案后,在工作過程中,對從事這項工作的人,按科學方法訓練過與未經訓練者相比,總是經過訓練並掌握了科學方法者能取得較好的效果;
(3). 一旦采用了科學方法,則必然可以將工作中的操作、使用的工具,作業時間等確定出標準; (4). 有了統一的標準,就可以將工作實際與標準進行對比,發現問題,進而找出解決問題的辦法,並實行改正。
2.工作研究的任務
工作研究的任務可以概括為以下五個方面:
(1). 尋求最經濟、最有效的工作方法,以提高生產率。要提高生產率,主要是消除無效勞動和各種資源(時間、原材料、能源等)的浪費;
(2). 公正地評價和分配成果。通過制定最佳的工作程序、操作規程和合理的標準時間,職工的工作有所遵循。同時也能客觀地、定量地評價職工的工作,更好地實行按勞分配;
(3). 保證良好的工作環境。克服只重技術、輕管理,不重視環境的弊病,避免人為的危險和破壞環境的現象;
(4). 提高企業管理水平,有了工作標準和時間標準,就有了編制生產計劃、作業計劃、產品定額成本和考核生產成果、分配生產獎金的基礎; (5). 保障職工業餘時間。
第 3 頁,共 41 頁
3.工作研究的構成與範疇
工作研究是由方法研究與時間研究組成。方法研究又稱方法工程(Methods Engineering)。時間研究又稱工作衡量或作業測定(Work measurement)。 工作研究的範疇如圖3-1所示: 方法研究 程序分析 作業分析 1. 方法 材料 2. 工具,設3. 備 4. 工作環 設定工作標準 1.整個生產過程分析—操作程序圖 動作研究 2.成品或材料之流動—流動程序圖 3.布置與路徑分析—線圖 4.空閑時間分析一人一机程序圖 5.工作時間兩手之移動—雙手工作程序圖 動作經濟原則 影片分析 目視動作研究 1. 方法 2. 材料 3. 工具、設備 4. 工作環境與條件 工作衡量 (確定時間標準) 員工操作訓練 工作指導單 細微動作指導 秒表法 PTS法 統計分析法 工作抽樣法 工作現場講解指導 課堂講解 圖3-1. 工作研究的范疇
隨著科學技術和生產的發展,管理手段的更新,工作研究的具體內容也發生了巨大的變化。早期以個別人、個別作業的工作方法研究為主,現已發展為包括作業系統設計、作業方式設計以及生產線的組識設計等;早期以直接時間測定為主的時間研究,現已發展為包括直接時間定、預定動作時間制、標準時間和寬放時間的確定等;此外,現代工作研究還包括作業環境和疲勞的研究。
也可以從另一個角度將現代工作研究劃分為兩部分。一部分為工作研究的基本內容,包括
第 4 頁,共 41 頁
工序設計、作業改進、小組作業設計、人機作業設計、流水線組織設計、作業時間測定、標準時間的制定和寬放時間的確定等。另一部分為擴大的工作研究內容,包括隨著辦公事務自動化的發展,有關辦公事務的組織、事務信息處理系統、辦公事務環境、事務處理能力及時間等業務管理;原以作業人員為中心的生產線組織設計隨著機器人和自動化設備的引入,出現了自動化生產線、柔性制造系統和工廠自動化,其中的生產組織設計以及對機器人和自動化設備的微細動作分析設計等。
本章將僅介紹工作研究的基本內容。
4.方法研究與時間研究的關系。
方法研究與時間研究的關系非常密切。二者之間是相輔相成、互為滲透的。 一般說,時間研究應該在方法研究的基礎上進行。換句話說,只有經過方法研究,使得生產過程和操作(動作)方法合理后,時間研究才有意義。另一方面,“時間乃動作的影子”,時間是衡量工作方法优劣的主要尺度。所以,方法研究常用時間研究作為比較和選擇工作方法的依據。
方法研究要研究如何減少作業的工作量,而時間研究則要研究如何減少無效時間,並以方法研究所確定的工作量為基礎,進一步制定該作業的標準時間。
二、工作研究的職能
(1) 工作和作業的計劃和方法的改進與設計; (2) 作業方法、條件標準化的制定; (3) 對操作者進行培訓; (4) 指導現場改進工作;
(5) 根據標準時間進行作業管理; (6) 測定生產率; (7) 作業范圍的設計。
工作研究是導循的科學的方法,在無需增加投資或只需极少量費用情況下開展研究,尋求效率最高、成本最低的工作方法。實施“工作研究”,可以達到對人力、物力各項資源的有效利用。
第二節 方 法 研 究
一. 方法研究的目的
第 5 頁,共 41 頁
方法研究就是通過現行的工作系統進行系統進行科學的分析,在給定的制約條件下,開發出更有效、更經濟的工作方法,以達到提高生產率和經濟效率的目的。其具體目標主要有以下几個方面:
(1) 使作業變得容易、安全並減輕勞動強度; (2) 增加操作人員的工作興趣; (3) 降低成本; (4) 增加產量; (5) 縮短生產周期; (6) 提高產品質量; (7) 改進作業環境。
方法研究包括生產過程(程序)分析(process analysis)、作業分析(Operation analysis)與動作分析(Motion analysis)。生產過程分析是以整個工作系統為研究對象;作業分析與動作分析則縮小到以某個作業或操作動作為研究對象。顯然,應先做好程序研究,然後再做動作研究為宜。
二. 方法研究的程序(工作步驟)
完整的方法研究有以下五個步驟: (一) 選擇準備研究的工作對象
方法研究的對象十分廣泛。在工廠里,全部生產過程,即從原材料進廠到成品出廠的整個過程,以及企業管理的各項活動都可以成為方法研究的對象。 (二) 調查了解並詳細記錄現行方法
這是方法研究的基礎。方法研究能否收到效果,在一定程度上取決於記錄是否準確與詳盡。因為分析和開發新方法都是以此為基礎。記錄是在通過查閱資料,現場觀察之后,采用一些符號和圖表,把現行方法的全部事實表示出來,可一目了解。符號有生產過程的工序符號,動作要素的符號等。圖表有生產過程分工序分析圖表、工藝流程分析圖表、人—机聯合分析圖表等等。此外,還可用攝影機和錄象機對現行工作方法進行記錄。 (三) 嚴格分析記錄的事實,尋求新的方法
這是特別重要的一步。事實記錄下來后,就要各項考查,尋求改善的新方法。通常采用“5W1H”法(六何分析法)和“四種技巧”,並把它們結合起來進行分析研究。
第 6 頁,共 41 頁
“六何分析法”是一種詢問考查方法,如對一道工序或一項操作都是從原因、對象、地點、時間、人員、方法六個方面提出問題進行考查。如表3-1所示。
表3-1 “ 六 何 ”分 析 表 逐 “ 級 提 六 何 ” 原 因 對 象 地 點 時 間 人 員 方 法 干的必要性 干什麼 在什麼地方干 在什麼時間干 由何人干 怎樣干 理由是否充分 為何要干它 為何在此干 有無新的理由 能否干別的 能否在別的時間干 新的理由 應該干什麼 應該在什麼時間干 應該在什麼時間干 應該由誰干 應該如何干 第一次提問 現 狀 第二次提問 為 什 么 第三次提問 能 否 改 善 結 論 新 的 方 案 問 能否在別的時間為何在此時干 干 為何由他干 為何這樣干 能否由別人干 能否用別的方法干 在對上述六個方面經過認真考虙后,在構思新的工作方法時,可以運用“取消、合並、重排、簡化”四種技巧,考虙改善的可能性。
1.取消——取消一切不必要的工作。任何一項工作或活動如能取消的話,當然是最大的改善。 2.合並——合並必需而可能合並的工作。如不能取消,則應考虙可否將兩個或更多活動項目合並。
3.重排(或改變)——重排所有必需的工作的程序。通過改變工作程序,使工作的先后順序重新組合,達到改善工作的目的。
4.簡化——簡化所有必需的工作。在經過取消、合並、重組之后,再對該項工作進行深入的分析研究,使方法和動作盡量簡化,使新的工作方法效率更高,成本最低。
“四種技巧”與”六何分析法”在分析現行方法和建立新方法中的基本關係如圖3-2。 (四) 擬定並建立新的工作方法
在一項工作通過上述分析考查后,下列問題就可得到解答:應該做什么?應在何處做?應在何時做?應由何人做?應該如何做?為何這樣做?
第 7 頁,共 41 頁
方法研究的目的,在於制定出最佳方案。然而最佳方法是不能一蹴而就的,一般需設計若干方案(至少兩個方案),從中評選出最佳方案。
判斷最佳方案的願則是適用性。主要包括:(1)經濟性——應對新工作方法作技術經濟分析,並與舊的工作方法作對比,如計算新工作方法所節省的“動作次數”、“移動距離”、“工時”和費用,即視其能帶來多少經濟效益;(2)安全性——新的工作方法是否安全,勞動強度如何?(3)心理因素——新的工作方法能否取得現場主管和有關人員的同意和合作。
將評選出的最佳方案,正式繪制出工作改進圖表,寫出報告書,報經有關領導批準,作為標準化的工作方法實施。 (五) 貫徹實施新的工作方法
在開始推行一種新的工作方法時,一般存在兩種困難:一是不了解; 二是不習慣。所以需要廣泛宣傳新方法的內容、意義、好處,還要對職工進新方法的技術培訓,並加強現場指導。推行時,不要急於求成,要允許職工有一個熟悉和適應的過程。
三. 生產過(程序)分析
生產過程是一切生產活動的綜合。這些活動使原材料逐漸變為成品。生產過程的主要組成部份有:工藝過程(以機械廠為例,它是車、銑、刨、鉆、磨、鑄、鍛、焊、熱處理、電鍍、裝配等工序組成),運輸過程和檢驗過程。
生產過程分析是以產品(零件)制造過程為研究改進對象的一種分析技術。它主要是從經濟有效的角度,通過加工對象從原材料投入到制成成品的整個生產過程的分析,探討加工工藝(包括工序劃分,運輸路線,使用工具等)是否合理。此外,對加工對象所用的原材料、元器件也應進行價值分析,分析選用的原材料、元器件是否合適(是否有功能過剩或功能不足現象)?有沒有功能相同而價錢更低的代用品?原材料、毛坯的大小形狀是否適當?等等。
程序分析可根據不同的目的采用適當的技術。例如,分析整個制造過程采用生產程序圖;分析物料或產品的流動采用流動程序圖;有關工廠布置及搬運的分析采用線圖等。圖3-3為程序分析圖通用的符號。
圖3-3 生產過程分析的符號、符號說明及調查項目
第 8 頁,共 41 頁 生產過 程要素 基本符號 符號 應用符號 符號說明 表示原材料、半成品、零件發 調查項目 生物理、化學變化,或處於分解、? 批量的大小, 裝配的狀態。 ? 加工時間, ? 更換產品的準備 時間,設備名稱, ? 工、夾、模具名稱, ? 加工部位, ? 操作者(性別、人 5 表示第5道加工工序。 加工 A3 表示A零件第3道加工工序。 數、條件) ? 以及其他有關事 項。 表示以加工為主,同時進行檢驗。 表示原材料、半成品、零件或? 批量的大小, 產品從一處移至另一處的狀態。? 搬運手段, 符號“ ”的直徑,為加工符? 搬運時間、距離、號的1/2-1/3。 表示男子搬運。 表示叉車搬運。 重量、裝卸方法和用具, ? 搬運者(性別、人數、條件), ? 以及其他與搬運有關事項。 搬運 ( ) m 叉 表示原材料、半成品、零件、產? 批量的大小, 品的數量和質量進行檢驗。 ? 檢驗部位, ? 檢驗方法, ? 檢驗器具, ? 檢驗標準, ? 合格率, ? 檢驗者(性別、人表示質量檢驗。 數、條件、), ? 以及有關檢驗的事項。 表示數量檢查。 檢驗 第 9 頁,共 41 頁 ` 停留 表示原材料、半成品、零件、? 停留數量, 產品的停頓或保管的狀態。 ? 停留時間, 表示原材料的儲存。 表示零件、半成品、產品的保管理停頓。 表示工序停留,加工一批產品中的停頓。 表示批量停留,加工一批產品中的停頓。 ? 停留場所,容器,放置方法, ? 保管條件, ? 其他有關保管事項。 表示數量、質量檢查同時進行,以質量檢驗為主。 圖3-3
1. 生產過程的類型
生產過程的類型有三種:一是零件型,又稱單純型;二是裝配型,又稱集合型;三是分解型,又稱拆卸型,又稱拆卸型。這些生產過程類型的示意圖如圖3-4。
2.生產過程的調查方法和調查項目
對生產過程的調查,要首先查閱資料,如實物樣品、設計圖、零部件圖、使用說明書、工藝流程圖、廠區和車間平面布置圖等,並且聽取有關人員介紹,在大體了解情況的基礎上,再到現場調查。按工藝順序跟蹤被調查物的(工件)的移動,對每一個作業(工序)在觀察的同時,要向作業者或班長了解作業的情況,在理解了作業內容的基礎上,把調查結果記入分析表。為使調查了解的內容能滿足分析的需要,事先要對各個作業分別擬定調查項目。調查項目參見圖3-3。
3.作業程序圖
作業程序圖(Operation process chart)提供操作程序的全部概況及各制造程序(工序)間的相互關係。作業程序圖只包括操作與檢驗,一般用於對產品生產過程的總體分析。目的是了解產品從原料開始到成品形成的整個生產過程這一系統。這個系統是由哪些生產環節、多少工序組
第 10 頁,共 41 頁
成的, 經過一個什麼樣的加工順序,以便從全局出發來分析問題.
(零件型)
(裝配型) 圖3-4 生產過程類型示意圖 (分解型)
4.流動程序圖
流動程序圖(Folw process chart)簡稱流程圖,用於以零件為對象的局部分析,是總體分析的進一步具體化。它由操作、檢驗、遲延、儲存及搬運構成,反映出零件從毛坯開始到成品制與為止的按工藝順序流動流動的全部生產過程。它記錄的內容很詳盡,一般包括物品(工件)流動的數量、搬運的距離、消耗的時間、工藝方法、作業地點、作業人員、使用的機器設備、工夾具、容器等。圖3-5為某工廠車床尾座加工流程圖。
在現狀調查分析基礎上,著手提出改進方案。對流程分析考查的重點如下: (1) 所有活動的目的是什麼?改進的可能性? (2) 各工序使用的工裝是否合適?改進的可能性? (3) 工序劃分是否適當?能否調整和合並? (4) 加工檢驗時間能否減少?
(5) 停放次數、停放遲延時間是否過多?能否減少?
第 11 頁,共 41 頁
(6) 運輸路線和搬運方式是否合理?能否改進?運輸距離是否過長?能否縮短?
經過上述全面綜合考慮,新的流程方案將逐漸成。新方案同樣用圖表加以反映,對改進處應配以必要的文字說明。為了評價新方案的效果,還需要將新舊方案予以對比。用表格形式反映新方案比舊方案的优越性。如節省加工、檢驗的時間,減少搬運、停放和遲延的次數和時間等。
四、作業分析
工藝過程、運輸過程及檢驗過程都是由許多基本組成部分組成的,這些基本組成部份稱為作業或工序。它是指由一個工人或一組工人在同一個工作地上完成一定(一個或同時幾個)勞動對象的那部分工作活動。
作業分析主要是研究與分析其組成部份和影響作業時間的因素,重點在於改進操作方法,改消多於的和笨拙的動作,協調人和機器的配合,以及工作中各操作工人的配合,以達到提高作業效率和減輕工人勞動強度的目的。
1.作業的組成部份——作業要素
為了達到使作業結構合理,減輕勞動強度,減少作業時間,研究時必頇將一項作業細分為作業要素。作業要素是由一個或若干個勞動動作組成。作業要素根據其性質和作用可為基本要素與輔助要素。這種分類的目的在於尋求要素機械化和自動化的可能性,同時要盡量在機動時間內做手動工作。例如,半自動、自動機床的操作工人利用該機床機動時間去操作另外的機床,實行多機床管理。
任何作業都可以細分為許多要素,例如:“車某工件外園”工序可劃分為:安裝工件、開車、進刀、切削(走刀)、停車、退刀、檢驗(測量尺寸)、卸下零件並放在適當地方。
2.影響作業要素時間消耗的因素
影響作業要素時間消耗的因素主要有下列六類:
(1).與勞動對象有關的因素。如工件、原材料的性質、重量、尺寸、形狀等。
(2).與機器設備有關的因素。如機器的功率、運轉速度、最大負荷限度及其他性能等。例如車削加工,單件生產一般宜用普通車床,中小批生產宜用六角車床,大批和大量生產宜用高效的半自動(自動)車床。
(3).與工藝裝備有關的因素。工藝裝備簡稱工裝,是工具、夾具、量具和模具的總稱。采用的工裝是否合適,不僅影響產品(零件)的質量,而且對作業的效率影響很大。例如,可以使用粗銼
第 12 頁,共 41 頁
的作業,不要用細銼,因為用粗銼效率高。機加工中的鉆孔,單件生產一般采用劃線;批量大時,應采用高效的鉆模,不僅能大大提高效率,又能保證產品質量。又如在檢驗時,大批量生產中應使用專用量具(如圔規、環規等)。
(4).與工作地組織有關的因素。這方面的因素包括機器設備的布置、原材料(毛坯、半成品)和工具的放置位置等。高效率的生產只有在工作地合理組織和布置的條件下方有實現的可能。
廠內運輸也是工作地組織工作之一。在現代制造工業企業中,廠內運輸具有特別重要的意義。如能利用起重機、傳送帶等先進設備代替人力及手推車運材料及制件,就可縮短運輸作業時間,降低運輸成本和減輕工人勞動強度。
(5).與勞動條件有關的因素。勞動條件(工作環境)包括工作地的安全設施、照明、溫度、濕度、噪聲、清潔衛生等的狀況。勞動條件的好壞不僅對工人身體和心理健康有重大影響,而且對作業要素時間消耗也有很大影響。
(6).與工人有關的因素。作業要素時間消耗與工人的技術熟練程度、經驗、責任心、情緒等有關。
作業分析的任務就是分析並設計合理的作業結構,分析並改善各項影響作業要素時間消耗的因素,並使各項因素得到合理的配合,以達到縮短作業時間,提高勞動生產率的目的。
3.作業分析使用的圖表
作業分析用圖表主要有人一機程序圖和雙手工作程序圖。 (1).人一機程序圖
人一機程序圖(Man-machine chart)用於記錄作業者和機器在同一時間內的工作情況,以便分析尋求合理的操作方法,使人的操作和機器的運轉協調配合,以充分發揮人和機器和效率。圖3-8為某銑床工作人一機程序圖。
第 13 頁,共 41 頁
銑接觸支持杆頂端 2號銑床 取零件並夾緊於虎鉗中 開動機器 工作臺前進6cm並進刀 銑頂端 退回工作臺11cm 停止機器 鬆開虎鉗並取出零件置於旁邊 總額(每件時間) 0.08 0.02 0.10 0.11 0.02 0.06 0.64分 工人 機器 0.25 圖3-8 人一機程序圖
又如,某圕料壓鑄某制品的現行工作方法記錄於人一機程序圖中,如圖3-9。 時間(分) 2 4 閑 6 8 10 利用率
通過以上圖表,可清楚看出人、機都有空閑,利用率不高。單件時間為10分/秒,人和機器的利用率均為60%。
經初步改進,人一機程序如圖3-10,單件作業時間壓縮為8分/件,人和機器利用率上升為75%。
60% 圖3-9
60% 卸下零件 修整和存放零件 被卸下零件 閑 加 工 人 準備零件 裝上零件 機 閑 被裝上零件 第 14 頁,共 41 頁
時間(分) 2 4 6 8 利用率 人 裝上零件 閑 卸下零件 修整和存放零件 75% 圖3-10
機 被裝上零件 加 工 被卸下零件 閑 75% 再經改進,人一機程序如圖3-11,單件作業時間縮短為6分/件,比現行方法提高效率70%,人與機器的利用率達100%。
時間(分) 2 修整和存放零件 4 6 利用率 準備下一個零件 卸下零件 100% 圖3-11
被卸下零件 100% 加 工 人 裝上零件 機 被裝上零件 (1) 雙手程序圖
雙手工作程序圖將同一時間內左右手的工作和空閑情況分別記錄下來,以便於分析改進操作方法,提高效率。
圖3-12為裝配螺釘和墊圈的雙手工作程序圖。
第 15 頁,共 41 頁 工 人 雙 手 工 作 程 序 圖 作 業: 裝配螺釘與墊圈日 日期:1984年9月1日 部 門: 總 裝 制圖者:張亮 工 人: 李 明 圖頁數: 1 方 法: 現在方法一次裝配一件 工 作 地 布 置 L1:螺釘 L2 R2 摘 要 L2:橡皮襯 左手 右手 總計 套圈 動作 5 17 22 L1 R1 R3 總數 取 1 3 4 運輸 2 7 9 圖的符號: 作業 運輸 R1:鋼墊圈 定位 1 3 4 R2:橡皮墊圈 裝配 0 4 4 R3:最后工作 持住 1 0 1
第 16 頁,共 41 頁
圖3-12
左手 等待右手 1 2 3 1 2 3 4 5 移至中手心並用指定位 4 6 持握螺釘 10 釋 放 到L1 11 9 12 10右手 1到R1 2取鋼墊圈 3到左手螺釘 4把墊圈放在螺釘上 5把墊圈放在螺頂頭部 4到R2 6取橡皮墊圈 5到螺釘 7把墊圈放到螺釘上 8把墊圈推向螺釘頭部 7到L2 9取橡皮墊套圈 8到螺釘 10把橡皮襯套圈放在螺釘上 12把橡皮墊套圈推向橡皮墊圈處 10在R3裝配 13將成品釋放進盤內 13 取螺釘 5 7 8 7 9 8 圖3-12
五、動作分析
動作分析是以一項操作為對象,對動作活動進行詳細的分析研究。其基本思想是:對操作者手、眼及其它身體部位的動作,進行分析、比較、研究后,剔除多餘無效的動作,把必要的有效動作很好地組合成標準動作系列,並與之相配合設計適當的工具、工作地布置等。
第 17 頁,共 41 頁
(一) 動作分析方法的種類
動作分析由吉爾布雷斯(Fuank B.Gilbreth)首創。最初是研究手的動作,繼而總結出動作經濟原則。動作分析根據精確度要求,常采用下列三種方法: 1.目視動作分析法
這種方法一般用於比較簡單的操作活動,主要憑研究人員的觀察,用動作要素符號進行記錄,根據動作經濟原則分析改進。 2.動素分析法
將工作中所用之各動素逐項分析,謀求改進。一般用於具有重復性且周期較短的手工操作。 3.動作影片分析法
用攝影機或錄象機把操作者的動作拍攝下來,根據需要可以按正常速度拍攝,也可按高速度(用高攝影機)拍攝,由影片的放映而進行分析,提出改善意見。這種方法取得的資料準確,特別是對細微動作、速度快的動作、速度快的動作,更是一種分析研究的有效方法。
(二) 動素
吉爾布雷斯將人的操作活動分解為17種最小限度單位——基本動作要素,簡稱動素。17種動素符號如圖3-13
第一類是進行工作時必要的動素;第二類是為第一類動素作準備的動素,但它們使第一類動作延遲;第三類是不進行活動的動素。動作分析與研究時應盡可能將第二、三類動素排除,並把第一類動素合理配成系列,使操作速度加快。 圖3-14為動分析舉例,也是動素分析的基本形式。
(三) 動作經濟原則
動作有許多經濟原則,都是從經驗發展而來的。運用這些願則分析操作和動作可以改進工作。 動作經濟原則的基本思想是:以盡可能減少工人的疲勞、能發揮工人最高效率為準則制定操作方法,再配備適當的加工工具、工作區及機械設備。
吉爾布雷斯首創動作經濟與效率法則(Rules for motion economy and efficiency),后經若干學者發展,並加州大學巴恩斯(Ralph M.Barnes)綜合為22項,稱為動作經濟願則(The principles of motion econcmy)。這些願則和方法包括人的動作和工作地布置,工廠和辦公室均適用。它為提高手工勞動效率和減少疲勞提供了基礎的準則。
第 18 頁,共 41 頁
1. 關於身體使用原則
(1)雙手應同時開始並同時完成其動作。 (2)規定休息時間外,兩手不應同時進行。 (3)兩臂之動作應對稱、反向並同時進行。
(4)手之動作應盡可能用最低等級(見后面圖3-15)而又能獲得滿意結果者。 (5)凡是能利用動力的地方應用動力,如果必頇用體力,應減少到最低限度。
(6)手的動作以圓滑連續的曲線運動最好,不要采用折線或直線、突然或急劇改變方向的動作。 (7)自然帶弧形的運動比受限制或受控制的運動輕快和準確。
(8)動作應盡廳能具有輕鬆自然的節奏,節奏性對於自然地完成一項操作具有重大作用。 2. 工作地布置原則
(9)工具、物料應放於固定處所。
(10)工具、物料及操作裝置應放於工作者前方的近處。 (11)零件、物料應盡量利用重力墮送到靠近用料的地方。 (12)盡可能采用下滑式運送裝置。 (13)工具、物料應按操作順序放置。 (14)應有適當的照明設備,使視覺舒適。 (15)工作臺和椅高應使工作者坐、立方便適宜。 (16)工作椅的形狀和高度應使工作者保持良好姿勢。 3. 工具裝備
(17)盡量解除手的工作負擔,代之以夾具或腳踏裝置進行工作。 (18)盡可能用兩個或兩個以上工具的組合工具。 (19)工具和物料應盡可能預放在工作位置。
(20)手指分別工作時,各指的負荷應按照其固有能力分配。 (21)手柄設計時,應盡可能擴大它與手的接触面。
(22)機器的手柄、手輪及操縱杆應安置在很少轉動身體就能進行操縱的位置,且能得到最大的機械效率。
第 19 頁,共 41 頁 類別 動素名稱 文字符號 形象符號 定義 伸手(Reach) 第 一 類 抓取(Grasp) 移物(Move) 裝配(Assemble) 應用(Use) 拆卸(Disassemble) 釋放(Release) 檢驗(Inspect) 第 二 類 第 三 類 故延(Avoidable Delay) 遲延(unavoidable Delay) 持住(Hold) 休息(Rest) 尋找(Search) 選擇(Select) 計划(Plan) 定位(Position) RE G M A U DA RL I SH ST PN P 接近或離開目的物的動作 抓住目的物的動作 保持目的物由某位置移到另一位置 結合二個以上目的物的動作 借器具或設備改變目的物的動作 分解二個以上目的物的動作 放下目的物的動作 將目的物與規定標準比較的動作 確定目的物位置的動作 選定要抓取目的物的動作 計劃作業方法而遲延的動作 把目的物放置在所希望的正确位置的動作 預位(Preposition) PP 東西使用后,把它放在下次使用時最方便位置的動作 H RT 保持目的物的不動狀態 不含有用的動作,而以休養為目的動作 UD 不含有用的動作,而工作者本身所不能控制的遲延 AD 不含有用的動作,而工作者本身可以控制的遲延 圖3-13 動素表
(1)取材料 (2) 取物並改變動作(例如簽名)
第 20 頁,共 41 頁
編號 1 2 3 4 符 號 動 素 看材料同時伸手 抓取材料 移動同時看放置位置 定位釋放 編號 1 2 3 4 5 符 號 動素 看筆同時伸手 取筆 離筆套 移物同時定位 把筆放入筆套內 (3)放置產品
(4)釋放產品
編 號 編號 1 2 3 4 5 符 號 取物 移動同時看放置位置 定位置 釋放 手回原位 動 素 1 2 3 4 抓取 移物 釋放 手回原位 符 號 動 素
(5)工具放在易最處 (6)左手東西握於右手
動 素 左 1 手持材料 符 號 右 動 素 伸手 編號 1 2 3 4 5 6 符 號 動 素 抓取工具 移物同時看放置位置 定位 2 釋放 放於易取處 釋放 手回原位 抓取 3 手回原位 移物 圖3-14 動素分析舉例
第 21 頁,共 41 頁
簡言之,人體動作的基本要求是: (1) 動作應同時進行; (2) 動作應對稱; (3) 動作應自如; (4) 動作應有節奏; (5) 動作應考慮慣性;
吉爾布雷斯夫婦把人體動作分成下列五類(等級)。如圖3-15所示。 第一類 手指運動。
第二類 手指和手腕運動。 第三類 手指、手腕及前臂運動。
第四類 手指、手腕及前臂運動。
第五類 手指、手腕、前臂、上臂及肩部運動。
這五類運動移動的距離、所需時間、消耗熱量比如表3-2表示。
表3-2 手的動作分類 運動類別 時 移動距離 cm 時間(Mod) 消耗熱量比 2.5 1 5 5 2 10 15 3 20 30 4 80 37.5 5 100 1 1 2 2 3 6 4 12 5 15 注:1Mod=0.129秒
應盡量削減無用動作,如找工具的動作,走多餘的路等;應將動作盡量縮小到手指或手腕的範圍。一般說,正常活動領域不超過肘的范圍。如果動作到肩膀,以及蹲、彎腰等都超過正常的範圍,既浪費時間,又會很快疲勞。
第 22 頁,共 41 頁
第三節 時 間 研 究
一、 時間研究的意義
時間研究又稱作業測定。其根本目的是尋求在標準狀況下完成一項工作所需的時間。即一個合格工人(具有正常的體力和智力,在勞動技術方面受過良好訓練,並具有一定熟練程度的工人)在標準的作業方法和條件下,以正常的作業速度完成某一工作所需的時間, 這種時間稱標準時間,相當於我國企業的勞動定額時間。它是一項作業的純作業時間與寬放時間之和。 標準時間(勞動定額)是企業管理工作的基礎。以下幾個方面都需要以準確的標準時間作為依據:
(1) 制訂及評價生產計劃、工時計劃、作業計劃; (2) 工作場地布局、配置機械設備及配備設備的數量等; (3) 成本及價格的計算及經濟核算; (4) 配備人工數量及級別;
(5) 評價工人工作好壞,決定工資級別及獎金; (6) 改進操作方法及環境條件; (7) 訓練工人。
總之,勞動定額是合理組織勞動、實行計劃管理和貫徹執行按勞分配原則的重要依據;是實行經濟核算和成本管理的重要基礎;是組織、動員廣大職工努力提高勞動生產率和勞動競賽、推廣先進經驗的有力工具和手段。
二、 勞動定額的形式
勞動定額是產品生產過程中勞動消耗的數量標準,是指在一定的生產技術組織條件下,規定生產一件合格產品所需的勞動時間,或者規定在一定勞動時間(如分、小時、天)內生產的合格產品的數量。前者稱為“時間定額”,后者稱為“產量定額”。二者都是勞動計量標準它們之間可以互相轉換。
三、工時消耗分類
所謂工時,就是工作班的工作時間。工時消耗分類就是將勞動者在整個工作班中所消耗的時
第 23 頁,共 41 頁
間,根據其性質、範圍、作用、及當時的具體情況,明確地劃分為若干類,以便作為進一步分析研究的依據,從而制定勞動定額或改進勞動組織等。
在制定時間定額(標準時間)時,必頇對工人生產中的全部工是消耗進行分析研究,確定哪些工時消耗是必要的,應列入工時定額之內;哪些工時消耗不是必要的,不應列入工時定額,而應采取措施,減少和消除這部份工時損失。工時消耗分類如圖3-16所示。 全 部 工 時 消 耗 定額時間 基本 時間 機 動 輔助 時間 組織 性的 技術性的 休息時間 自然需要時間 作業 時間 準備與結 束時間 工作地 服務時間 非定額時間 休息與自然 需要時間 非生產 作業時間 停工 時間 機 手 並 動 的 手 動 的 與機 動 交 叉 的 與機 動不 交 叉 的 組 織 技 術 造 成 的 工人 造成 的 非 工人 造成 的 工人 造成 的 的 圖3-16 工時消耗分類 定額時間指完成某項工作必頇的時間消耗。 非定額時間指不是完成某項工作必需的時間消耗。它是由於企業管理工作上的缺點或工人違反勞動紀律等原因引起的時間損失。
第 24 頁,共 41 頁
作業時間指實現工作任務消耗的時間。它是定額時間中最主要的組成部分。
基本時間指為直接完成工藝目的消耗的時間,也就是使勞動對象發生物理變化或化學變化(即改變形狀或性質)消耗的時間。
基本時間又可以分機動時間、手動時間和機手並動時間。
輔助時間指不是直接完成工藝目的,而是為了保證完成工藝目的必頇消耗的時間。如機加工中裝卸工件所花的時間。
輔助時間也可分機動時間、手動時間和機手並動時間。另外,在大多數情況下,輔助時間又分與基本時間交叉和不交叉的時間。在制定定額時,交叉的輔助時間就不要計入定額時間內。 準備與結束時間又稱作業轉換時間,指完成某項工作或加工一批零件,在工作開始前的準備工作時間,以及工作完畢時的結束工作時間。例如,加工前了解圖紙和工藝要求,領取工夾具,調整機床等;一批零件加工結束時,拆卸工夾具、交檢工件等。與上述其它時間比較,這類時間的特點在於,它不是加工每一個零件和每一個輪班都要消耗的,而是對於同一批零件只消耗一次,與該批零件數量無關。在大量生產中,制定定額時對這類時間消耗可忽略不計。
工作地服務時間又稱照管工作地時間,它是指為了保證生產的正常進行,用於正確布置工作地、保證工作地良好狀態以及對工作地進行供應和照管消耗的時間。這類時間又分為技術性和組織性兩類。技術性服務時間是指更換刀具、檢查和調整機床、清除切屑等時間。這種時間隨加工時間的增加而增多。組織性服務時間是指消耗於班前準備工作和交接工作的時間。 如上班時領工作圖紙,整理工作地、下班時寫工票、記錄工時、收拾工具和交接班等。這部分時間也是隨整個作業時間的增加而相應增多。
休息與自然需要時間指為了消除疲勞,保證工人精力充沛而進行的必要休息,以及生理上的自然需要消耗的時間。
非生產工作時間指工人做了本身任務以外的工作消耗的時間。例如,按制定規定,研磨工具、領取材料等工作由輔助工人做,但由於某種原因,基本工人做了這些工作,就屬於非生產時間。若制度規定,這類工作由操作工自己做,它就應劃在定額時間內。其數值可估計一個百分比,按寬放時間處理。 停工時間包括兩類:
非工人造成的時間指由於企業技術工作和組織工作的缺點,或者由於企業外部條件影響,使工作發生中斷的時間。如等待分配工作、待料、待工裝、停電等。
第 25 頁,共 41 頁
工人造成的時間指由於工人違反勞動紀律造成的時間損失。如遲到、早退、擅自離開工作地、工作時間內閑談、辦私事,以及違反操作規定造成設備事故等而帶來的時間損失。 在制定定額時,工作地服務時間和休息與自然需要時間,一般用它們對作業時間所占的百分比攤入單位產品的工時定額內。
四、時間定額的構成
由於生產類型的不同,時間定額的組成也有所不同。
在大量生產條件下,由於產量大,分攤到一件產品上的準備結束時間很小,可忽略不計,故勞動定額的時間組成中沒有準備與結束時間,只包括作業時間、工作地服務時間和休息自然需要時間。
在成批生產條件下,時間定額中應包括準備結束時間。 時間定額以單位產品(零件)計算,或以一起加工的成批產品(零件)計算。前一種情況下的時間定額稱為單件時間定額,后一種情況下的時間定額稱為成批時間定額。
單件時間定額
單件時間定額的組成部分有:
(1) 作業時間(T作 )它是由基本時間(T基 )與輔助時間(T輔 )所組成。
(2) 工作地服務時間(T服)它是由組織性置與技術性兩部分組成,通常用占作業時間的一定
百分率來表示。
(3) 工人休息與自然需要時間(T休 )通常也是用占作業時間的一定百分率來表示。 因此,單件時間定額的計算公式為:
T單=T作+T服+T休 =(T基+T輔) (1+a+b) 式中 a-------工作地服務時間對作業時間的百分率; b-------休息與自然需要時間對作業時間的百分率; a . b一般稱為寬放率。 成批生產條件下的每批時間定額為:
T批=T準+T單*n
第 26 頁,共 41 頁
公式中 T批——零件成批的時間定額; T準——準備結束時間; N——該產品件數。
成批生產中的每一件產品的時間定額為:
T準
T單計=T單=
n
T準
=T作+T服+T休+
n
T準
=(T基+T輔)(1+a+b)+ n
在西方國家和日本的企業中,標準時間(時間定額)中還包括一項“現場寬放”或“不可避免的寬放時間”。它包括管理人員、技術人員、小組長因材料或其他有關問題找操作者商談,短時間的機械故障的排除等。顯然,他們這樣分類,是考慮了生產現場的實際情況,更為合理。
五、時間研究的方法
時間研究的方法主要有:經驗估工法、統計分析法、技術測定法與工作抽樣法。
(一) 經驗估工法
由定額人員、技術人員和有經驗的老工人組成估工小組,根據產品設計圖紙、工藝規程、工裝條件和設備狀況,以及生產組織形式,憑各自的實踐經驗來估計工時定額。估工有粗細之分。粗估工是按整個工序估算。細估是按工序各組成部分分別估算,然後匯總確定工序的工時定額。
此法的優點是簡便易行,工作量小,制定定額快,並有一定群眾基礎。缺點是單憑經驗,技術根據不足,受估工人員主觀因素的影響大,難免出現偏高或偏低等現象,因而定額的準確性較差。常用於單件小批生產,以及新產品詴制和臨時性生產中。
(二)統計分析法
根據過去生產的同類型產品(零件、工序)的實際工時消耗和完成定額的統計資料,並分析當前生產條件的變化,通過計算確定定額。
此法有較多的統計資料為依據,比經驗估工法更能反映實際情況。但是也存在一定缺點。由於它依據的是過去的統計資料,其中可能有某些不合理的因素,比如在實際消耗的工時中包括了一部分浪費工時、加班加點時間等,又如原始記錄不準等,必然要影響到制定定額的準確性,
第 27 頁,共 41 頁
使定額水平不夠先進合理。為提高統計分析法制定定額的準確程度,必頇建立和健全原始記錄,特別是要加強以對統計資料的整理、分析工作,剔除其不合理部分,還要考慮當前生產條件和過去條件相比發生了哪些變化,這些變化對定額有什麼影響。一定要把提高勞動生產率的各種可能因素,如推廣先進的操作方法,采用新工藝、新技術等考慮進去。此法常用於生產比較正常,產品比較穩定,品種較少,原始記錄和統計工作比較健全的情況下。
(1) 采用統計分析法制定勞動定額時,不能用算術平均法求取的總平均值作為定額。因為生產
數據存在一定的波動是不可避免的,但波動較大的情況往往是由於管理上存在問題所造成。如果用算術平均法或中位數法確定定額,等於默認存在這種問題是合理的,這樣會把勞動定額定得偏低。
(三)技術測定法
這種方法是在分析研究生產技術組織條件和挖掘生產潛力的基礎上,對組成定額的各部分時間,通過實際觀測或分析計算來制定定額。由於取得時間資料的方法不同,它又可分為兩種: 一種是直接時間測定法,即通過現場觀測記錄取得第一手資料來制定定額。它是作業測定是基本的方法。屬於這類方法最有代表性的有秒表法和影象法。另一種是間接時間測定法,即根據事先制定的工進定額標準來計算制定定額。屬於這類方法的主要是 PTS法(預定時間標準法)。采用這兩種方法制定的定額都稱為技術定額。技術測定法的優點是比較科學,有一定技術根據,較為準確。在實際工作中應根據不同情況采用不同的方法。如秒表法和影象法因工作量太大,只適用於大批量生產和單件小批生彥中的典型零件或工序。
以上三種制定定額的方法,各有優缺點和適用范圍。究竟采用哪一種方法,應從實際具體情況出發,根據需要和可能確定。不論采用哪種方法,都要堅持群眾路線、實行專群結合和加強思想工作。
這里僅著重介紹秒表與預定時間制中的模特法。
1. 秒表法
采用秒表測時可用於制定定額,也可用於檢查工人未完成定額或大大超過定額的原因,以及研究各工種的組織情況,找出尚未利用的工時潛力等。現將采用此法制定定額的方法與步驟分述於下。
(1)準備工作
第 28 頁,共 41 頁
A制定操作規程,使工序結構合理化
定額員、工藝人員及先進工人經過充分討論研究,將每道工序分解為若干個作業單元,並進行方法研究,取消不必要作業單元,改善不合理的作業單元,使作業結構合理化。作業單元時間長短要合適,為了便於記錄,不宜太短。 B制定標準操作方法
在上述方法研究和總結先進操作的基礎上,制定標準操作方法,並明確確定各作業單元的測時始點和終點(定時點)。 C選擇與訓練工人
一般認為,為了使測得的結果合理和有代表性,應選擇中等(平均)熟練程度的工人進行操作。在西方國家,不強調中等熟練程度的人,因為其一,這種人不容易選到;其二,將來測時后,還要進行效率評定。所以,往往就選工序的原來操作者。不論選誰作為操作測時對象,都要做好思想工作,取得他的配合,並按標準操作方法訓練。 D準備觀測工具
采用什麼記時工具,取決於工序時期和作業單元時間的長短,若時間太短,可用攝影機或錄象機,如對流水線裝配線很適用,不僅時間能算得很準,而且還可以重現。若時間較長(如作業單元最短時間不少於3-4秒)一般用十進位的分度值為1/100分(DM)的秒表)。此外,還頇準備鉛筆、橡皮、記錄表格(見后個人測時錶)及夾子等。 E確定觀測次數
作業測定是抽樣過程,必頇有足夠多的測時次數,以期從統計總體中得到合適的樣本。測的次數越多,結果就越合理(即精度越高)。觀測次數要根據生產類型、作業性質(機動、手動或機手並動)、工序和作業單元的延續時間長短等情況而定。生產類型高,要求所得資料精確,觀測次數要多些,反之可少些。在機動時間和工序及作業單元的延續時間比較長的情況下,工時消耗比較穩定,觀測次數可以少些。在手動和工序及作業單元延續時間比較短的情況下,工時消耗波動較大,觀測次數應多些。需要作多少次觀測才能保證要求的精確度。
(2) 正式測時
測時通常在工作班開始1-2小時、工作節奏穩定后進行。在進行正式觀測記錄之前,宜先作2-3次詴測,以證實標準的定時點是否正確無誤。測時整個過程如圖3-17所示。
第 29 頁,共 41 頁
效率評定 寬放時間 記錄時間 選擇時間 正常操 作時間 標準工時定額 圖3-17 測時過程
(1) 連續法(Continuos timing)。在觀察過程中,讀出並記下各作業單元定時點(一般采用終點)的瞬間時間值T截。在觀測結束后,再把記錄的T截逐次相減, 求出各作業單元的持續時間(T
持
)。記錄用表可參考表3-4。連續法是最常用的方法。
(2) 瞬時返零法(Snap back timing,snap back method)。在觀察過程中,讀出並記下各作業單元終點時間值,隨即立刻使表复零。此法的优點是直接得出各作業單元的時間值(T 缺點是容易出錯。
秒表測時中各作業單元持續時間一般以不少於5—6秒較為合适,此時測定誤差較小,若有的作業單元時間太短(例如1—2秒),甚至1秒以下單獨測定誤差很大,可與相鄰若干單元組成一具作業單元組,采用循環法(Cycle timing)定。
循環法的基本方法是:在一個周期系列作業單元中,每次去掉一個作業單元,測出其餘幾個單元的總時間,然后通過解聯立方程求得各作業單元的時間 (T 持 )。
例如,一個周期系列的作業單元依次為ABCDE五個單元,於是在反復勞動中出現ABCDEABCDE……。首先去掉A,測BCDE的時間,辦法是從B作業單元開始時按動秒表,而在E作業單元結束時按停秒表,記錄下BCDE的總時間;然后再去掉B,測CDEA的總時間;……。設依次測得:
B+C+D+E=7.3 (1) C+D+E+A=6.8 (2) D+E+A+B=6.0 (3) E+A+B+C=6.6 (4) A+B+C+D=5.7 (5)
持
第 30 頁,共 41 頁
然后用代數方法解此聯立方程。把各式相加,得4A+4B+4C+4D+4E=32.4秒 A+B+C+D+E=32.4/4=8.1秒 (6) 以(6)-(1) A=8.1-7.3=0.8秒 (6)-(2) B=1.3秒 (6)-(3) C=2.1秒 (6)-(4) D=1.5秒 (6)-(5) E=2.4秒
1) 選擇時間
選擇時間是將記錄時間中的異常時間(差別特大)數據剔除之后的平均時間。例如,測得某作業單元的時間數據(分)如下:
0.10 0.11 0.09 0.16 0.11 0.10 顯然,0.16為異常時間,應剔除。
2) 效率評定
由於被觀測者未必能代表該部門的平均技術與操作水平,且操作速度的快慢還受各種因素(如情緒)的影響,故需對所測得的時間進行修正。方法是對操作時間平均值(選擇時間)進行速度評價。所謂速度評價,就是經過訓練的觀測員在觀測時,將作業者的作業速度與自己的標準速度(又稱正常速度)概念在頭腦中進行比較的過程。
所謂“正常速度”,是指“在嚴格的管理和沒有獎金刺激作用的條件下,作業人員的平均操作速度”。正常速度的例子相當於在不負重的條件下,以27英吋的步長和每小時三英里(合4.8公里)的速度,在平坦的道路上行走的情況;或者相當於用手把一付52張的樸克牌,逐張擺在邊長為30 cm的正方形的四個角上,用30秒種擺完的速度。
將正常作業速度的系數定為1,然后把測得的實際作業速度與之比較,如果慢於正常速度則定一個小於1的系數(如0.95 0.90 0.85等),如果快於正常速度,則定一個大於1的系數(如1.05 1.10 1.15等)。
效率評定對於制定標準時間至關重要。因此,觀測員要具有經驗,並經過訓練,對評定要求:1.盡可能準;2.對本企業各工種、各工序時間的鬆緊掌握要一致;3.對每一個作業單元評定一個效率系數。
第 31 頁,共 41 頁
3)正常操作時間
正常操作時間是指以正常速度進行操作所需的作業時間,也就是選擇時間經過修正后的時間,即: 正常操作時間=選擇時間×效率系數
例如,被觀測者干A作業單元的速度相當快,相當正常速度的120%,測得的選擇時間為1分鐘;而干B作業單元的速度較慢,只相當於正常速度的90%,選擇時間為1.5分。那麼,A與B作業單元的正常操作時間分別為〆 A 1×1.20=1.2 B 1.5×0.90=1.35分
(2)寬放時間
正常時間只反映進行操作活動所需的時間,因此,還必需“寬放”。寬放時間包括〆 a. 自然需要。如渴水,上廁所的時間。一般取男3~5%,女5~7%。
b. 工作需要。如工作地服務的時間,———如磨刀、換刀、運輸材料等。這些工作不是經
常重複的,也不一定什麼時候發生。
c. 工作環境條件需要。如體力消耗大的、工作條件不好的要“寬放”。條件越差,“寬放”
應越大,如煉鋼爐、加熱爐的操作工人々照明不良,噪音太大的,必頇用不正常姿勢工作的(如汽車裝配線上有些工序的工人是站在地溝里里仰面向底盤焊接或螺絲)等等。 d. 枯燥乏味、簡單重復與特別需要腦力集中的工序,也應給以“寬放”。
e. 由於機器故障、停工待料、等待工裝、更換材料,以及其它操作者不能控制的原因,都
要進行時間寬放。這些寬放數值可通過工作日寫實或瞬時觀測(工作抽樣)確定。 “寬放時間”一般給出一個百分比。也有給出絕對值的。如我國有些手表廠給裝配工人上下午各15分鐘休息—做眼保健操。關於各種條件“寬放”多少〇表3-5可供參考。 表3-5 不同工作類別的寬放率(百分數)
???????????????????????????????????????_ 1〃固定的寬放率
a. 個人寬放(注)……………………………………………………………………………… b. 基本疲勞寬放………………………………………………………………………………
第 32 頁,共 41 頁
2〃變化的寬放率
A. 站立工作寬放……………………………………………………………………………… B.不正常姿勢的寬放……………………………………………………………………………… a. 輕度不正常………………………………………………………………………………… b. 不正常(彎曲)……………………………………………………………………………… c. 十分不正常(躺著、伸出身體)…………………………………………………………… C. 用力气或以體力為動力(舉、拉、推) 舉重(磅)
5…………………………………………………………………………………………… 0 10 …………………………………………………………………………………………… 1 15…………………………………………………………………………………………… 2 20…………………………………………………………………………………………… 3 25…………………………………………………………………………………………… 4 30…………………………………………………………………………………………… 5 35…………………………………………………………………………………………… 7 40…………………………………………………………………………………………… 9 45…………………………………………………………………………………………… 11 50…………………………………………………………………………………………… 13 60…………………………………………………………………………………………… 17 70…………………………………………………………………………………………… 22 D. 光線不好
a. 略低………………………………………………………………………………………… 0 b. 較低………………………………………………………………………………………… 2 c. 很不適合…………………………………………………………………………………… 5 E. 气候條件(熱和潮濕)
多變 ………………………………………………………………………………………… 1-10 F. 注意力集中程度
a. 一般的細緻工作 ………………………………………………………………………… 0
第 33 頁,共 41 頁
b. 細緻或精密的 ………………………………………………………………………… 2 c. 十分細致或十分精密的 ………………………………………………………………… 5 G. 音響程度
a. 均勻的 ………………………………………………………………………………… 0 b. 間斷的——大聲………………………………………………………………………… 2 c. 間斷的——十分大聲 ………………………………………………………………… 5 d. 高音調——大聲 ……………………………………………………………………… 5 H. 精神緊張
a. 一般復雜過程 ………………………………………………………………………… 1 b. 復雜或周圍要注意的 ………………………………………………………………… 4 c. 十分復雜 ……………………………………………………………………………… 8 I. 單調
a. 低 …………………………………………………………………………………… 0 b. 中等 …………………………………………………………………………………… 1 d. 高 ……………………………………………………………………………………… 4 J. 乏味的
a. 比較乏味 ………………………………………………………………………………… 0 b. 乏味 …………………………………………………………………………………… 2 c. 很乏味 …………………………………………………………………………………… 5 ???????????????????????????????????????
注〆個人寬放指工人休息及自然需要時間
7)標準工時定額
正常時間進行必要的“寬放”之后,就成為標準工時定額——即勞動技術定額。
T正常 T標準 =
1-A% 式中T標準———標準工時定額々 T正常———正常時間々 A%-----各種寬放時間之和。
應根據具體情況確定總寬放時間A,譬如,若有停工的寬放時間,這時人也休息,或者有時
第 34 頁,共 41 頁
只是看管機器,那麼,總的寬放時間A可適當減少。
2. 預定時間制
預定時間制(Predermined Time System)簡稱PTS法。它以每個預定的基本動作要素時間值為基礎,求得每道工序的標準時間(定額)。這種方法的原理是〆1).一項作業(工序)可分解為作業單元。一個作業單元又是由許多基本動作———動素組成的々2)當條件(如移動距離、物體重量)一定時,一個人進行一次基本動作的平均的時間也基本一定。只要知道各種具體條件下的動素標準時間和一項作業的基本動作,就可制定出作業的標準工時定額,而無需測時。這是一種把動作分析和時間分析結合為一體的時間研究方法,其最突出的優點是可對未投產的工序制定勞動定額。
目前西方和日本通常使用的有 WF法(Work Foctor----工作因素法)、MTM(Motion Time Analysis------動作時間分析法)和MODAPTS法(模特排序法或簡稱模特法)。現將MODAPTS法簡要介紹於下。
MODAPTS中,將人的動作分成21種基本動素,如表3-6
表中字母表示活動類別,如M-----移動,G------抓取,等々字母后的數字表示該活動所需時間值,單位為MOD(模數),如M1代表手指移動,所需時間為1MOD。 1MOD的時間值如下〆 普通速度〆
表3-6 MODAPTS
動 作 符 號 模 數 動 作 符 號 模 數 動 作 找出 指 手 手腕 臂 的 前臂 移 動 上臂 肩 M4 M5 4 5 定 位 不要目視 必要目視 P0 P2 0 2 步行 彎身 W5 B17 5 17 M3 3 復雜 G3 3 他 回轉 C4 4 M2 2 取 壓 A4 4 抓 單純 G1 1 其 踏 F3 3 考慮 D3 3 M1 1 接觸 G0 0 重抓 R2 2 符 號 模 數 E2 2 第 35 頁,共 41 頁 重量附加 L1 1 非對稱 P5 5 生下 S30 30 1MOD=0.129秒
=0.215DM(IDM=1/100分) 快的速度〆 1MOD=0.1秒
包括10%疲勞寬放后 1MOD=1/7秒
觀察或分析作業者身體的活動部位,就可以確定動作時間。 2、基本動作說明 1)移動動作
從手指到肩由於動作距離逐步加長,因此時間值也依次增加。如表3-7所示。 a. M1“手指”動作
這是到手指根為止的移動動作,每進行一次,需要1人模數。
例如,以食指撓額頭5次,如果只動手指,那麼就是M1的動作,手指來(撓)5次,回5次,合計為9MOD。
表3-7 移動動作分類
符號 (MO?S) M1 M2 M3 M4 M5 (M7) L1
2)M2“手腕”動作
這是以手腕開始的手指頭的移動動作,手腕位置不動,而只是轉動。這種動作每進行一次
說明 有節奏的手指動作 用指動作(約~4cm) 用手腕動作(約5~10cm) 用前臂動作(約11~25cm) 用上臂動作(約26~45cm) 用肩動作(約46~60cm) 上體彎曲動作 每增加4kg
MOD 0.5 1 2 3 4 5 7 1
第 36 頁,共 41 頁
需要2個MOD. 例如,使手腕動,在紙上用鉛筆劃一條長5~7.5 cm的線條。 3)M3“前臂”動作
這是胳膊肘前的移動,但肘不能動,每進行一次需3MOD。例如,在紙上用鉛筆劃出長度15厘米的線條。 4)M4“上臂”動作
這是以肩為軸心手的移動動作。這是常見的上肢動作,動作範圍比較廣,每進行一次需4MOD。
5)M5“肩”動作
這是包括使用肩肌肉在內的、伸出手臂的動作。這動作表現充分伸出手臂,但不能有身體的輔助動作,每次需5MOD。例如,伸手夠高架上的物體。 6)M7“上身彎曲”動作
這是手要伸得很長並有身體的輔助動作,取7MOD。 7)使用工具的反復動作
對於使用銼刀銼東西,鎯頭砸東西或拉鋸等這類快速、上下或前后的反復動作,不要給以過高值。只使用工具時可采用如下值〆 手腕以前的反復動作 1MOD(單程) 胳臂肘以前的反復動作 2MOD(單程) 肩以下的反復動作 3MOD(單程)
總之,要比普通的移動動作的時間值要少1個MOD。對於如用橡皮擦掉字時的手指來回多次反復動作,每個單程可給0.5MOD,表示為M0.5。 8)L1重量因子
搬運物體時,根據物體的輕重,在時間值上要加以區別。時間值中的重量因子用L1表示。物體有效重量每增加4公斤,就在該“移動動作”的模數上加1MOD。所謂有效重量,是指一只手所承擔的重量。(兩手搬動時為物體重量的1/2)。有效重量在4公斤以下時忽略不計。
讓物體滑動來進行搬動時,有效重量應為該物體重量的1/3。
例如用兩手搬動10公斤物體時,在該“移動動作”的模數上加1MOD,而讓其滑動時,則重量的影響可忽略不計。
第 37 頁,共 41 頁
2、抓取動作
抓取動作分類如表3-8所示。 1)G0“接觸”
它是指手指或手掌去接觸目的物,不是抓住物體,僅僅是觸及,所以它不具有作業動作時間。
表3-8 抓取動作分類
符號 G0 G1 G3 (G11) 說明 接觸 抓取 G0、G1以外的抓取 手全張開抓取 MOD 0 1 3 11 2)G1 “抓取”
它表示僅合攏手指的簡單的抓取動作。例如,輕輕抓住火柴盒的動作。 3)G3 “復雜的抓取”
它是僅以收攏手指不能完成的復雜的抓取動作。例如,拿起放在桌面上平滑的金屬墊圈或從零件盒內取出螺釘等。
4)G11 “特別的抓取”
它是需要手指充分張開,然后去抓的動作。
3. 放置動作
放置動作分類如表3-9
符號 P0 說明 放置 MOD 0 0.5 2 5 13 1)P0 “放置”
它是在不用眼看就能把物體放置到要放的地方。例如,把某物 “咚”地放在桌上。 2)P2 “放在給定的地方”
它是邊用眼看邊調整方位地把物體放在給定的地方的動作,要求一次就能定位。例如,在螺杆上放一個墊圈。 3)P5 “放置到正確位置”
(P0. 5) 放置到別人手中 P2 P5 (P13) 放到一定的地方 放到正確位置 需要嵌入 這是用眼盯著進行最復雜的 “放置”動作,這种動作因伴隨著明顯的舉棋不定的局面,因此很容易判定。
下面兩種是 “放置”動作的特殊情況。 4)P0.5 “放置到別人手中”
它是利用筋肉運動知覺,把物體放到別人手中的動作。 5)P13 “必頇吻合”
第 38 頁,共 41 頁
它是放置非常精密的零件的動作。例如,組裝靜配合的軸套。
4. 同時動作
它是指兩只手同時動的動作。例如,左手伸向筆記本,而右手伸向鉛筆,把筆記本和鉛筆同時拿來。只有在進行 “注意力不需要太集中的動作”時,兩只手才能同時動作。對同時動作應分析出 “時限動作”和 “被時限動作”。所謂時限動作是指較費時間的動作,反之,費時少的動作稱為被時限動作。
5. 其他動作 1)E2 “眼”的動作
眼的動作有眼的移動和眼的聚焦兩類,都用 “E2”表示,每發生一次,需要2MOD,但只是在不進行眼以外的其他動作時才如此。
圖3-18所示的範圍稱為正常視野,眼睛轉向正常視野以外時稱為 “眼的移動”。眼的移動時間最大為3個E2。超出此限的 “眼的移動”就要伴隨著頭的動作。
2)R2 “改抓”
這是一種改變抓法,以便很好地控制物體姿態的動作。與E2一樣,只有在沒有他動作進行時才能認定,每次動作需2MOD。
3)D3 “判斷與對應”
這是表現在動作之間的瞬間判斷和決定所需的時間,是為了判斷下一動作的進行方法所需的時間,只是在其他動作不進行時才能認定。
4)F3 “腳”的動作
這是腳跟著地不動或踏住和放開踏板的腳的動作。例如,踏住和放開汽車加速踏板需2個F3,即6MOD。
5)A4 “加壓”
加壓是在活動中為了控制、限制物體或克服阻力而在該物體上施加肌肉力量的行為。它只有在停止其他動作時才能認定。
第 39 頁,共 41 頁
6)C4 “轉動”
它是為了使物體做回轉運動時或胳膊回轉的動作。回轉1/2圈以上稱為轉動,以下都稱為 “移動動作”。更準確些可采用如下值: C3 以手腕子為中心的回轉動作; C4 以胳膊肘為中心的回轉動作。
7)W5 “步行”
往前或往后行走或橫向跨出一步這類腿腳的動作叫做 “步行”。如,用手去夠1米遠凳子上的物品時,不邁一步而只伸手是夠不著的。這時手的動作為M2,而且W5之后的手指、胳膊和手的 “移動動作”總是M2。踩踏板的動作為F3,但腳跟離開地面時就為W5。 8)B17 “彎曲身體后再起來”
這是改變上半身垂直方向位置的動作,如彎腰、雙膝跪和膝跪等。身體彎曲后再恢復到原來位置的往復時間為17MOD。B17后面接著進行的 “移動動作”也全為M2。 9)S30 “坐在椅子上再起來”
它是坐到椅子上再從坐的狀態站起來的動作,其中包括坐下時拉椅子和站起來時挪椅子的時間。
3.記錄方法
表3-10為記錄用表格。按動作的先后次序記錄下來。要素作業每項占一行地記錄。 例 求把三個螺母放入瓶中,蓋上蓋,然後將瓶放到左側的作業時間? 作業所需基本動作要素及所需時間如表3-10。 結果求得所需時間為7.03S。
表3-10 MODAPTS作業分析表
時間 基本動作要素 左手 右手 蓋瓶蓋 M0.5 5 2.5 記號 次數 (MOD) 取螺母裝入瓶內 M4 G1 M4 P2 M3 G1 M3 P2 3 1 33 9 第 40 頁,共 41 頁 放下瓶子,手還原 M5 P0 M5 MOD 時間合計 秒(S) 1 54.5 54.5×0.129=7.03 10 略圖(略) 4. 工作抽樣法
工作抽樣(Work SimpLing)又稱瞬時觀測。它首創於1934英國統計學家蒂皮特(L.H.C.Tippett)運用統計學與概率論的理論,在紡織廠采用抽樣技術調查織布機的開動率和工時利用率。並將他的研究成果公開發表,命名為快讀法(Snap-Reading Method)。由於當時工業師對數理統計學知道得不多,因而未能引起反響。1940年美國動時研究專家莫羅(R.L.Morrow)用此法代替傳統的工作日寫實,測定正常時間應加上多大的寬放系數。他稱為比例遲延研究(Ratio-Delay Study)。莫羅的研究和實踐引起了其他一些動時研究專家和巴恩斯將部分有關論文編輯成冊,命名 《工作抽查》出版,介紹了工作抽樣的基本原理和大量的應用實例。從此,工作抽樣成了一種應用十分廣泛的“工作研究”技術,並推動“工作研究”走出傳統領域,進入醫院、商店、學校、銀行及政府機關等單位。現工作抽樣法廣泛用於研究下述問題:
1)設備及人員的工時利用率; 2)勞動定額中的寬放率; 3)人員及設備的安排是否得當;
4)人員、設備及材料的組織是否還可改進,以提高效率。
工作抽樣的原理,就是從母體(總體)N中隨機取出子樣n個,如子樣(n)的數量足夠多,則可從子樣的性質推斷出母體的狀態或性質。工作抽樣的對象主要是重復性低、周期較長的隨機性事項。
第 41 頁,共 41 頁
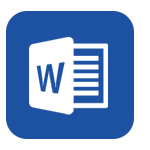





正在阅读:
工作研究教材资料01-14
美丽动人的英语名言07-25
那一次我玩得真高兴作文400字06-20
问卷调查报告怎么写12-12
最新的土地股权转让协议书范本05-22
二次函数应用题及压轴题03-17
IFix5.8 安装环境及新功能说明06-10
音乐毕业论文:浅谈农村小学音乐课教法研究10-24
大学生生态文明意识的教育与反思08-15
03任务10-19
- exercise2
- 铅锌矿详查地质设计 - 图文
- 厨余垃圾、餐厨垃圾堆肥系统设计方案
- 陈明珠开题报告
- 化工原理精选例题
- 政府形象宣传册营销案例
- 小学一至三年级语文阅读专项练习题
- 2014.民诉 期末考试 复习题
- 巅峰智业 - 做好顶层设计对建设城市的重要意义
- (三起)冀教版三年级英语上册Unit4 Lesson24练习题及答案
- 2017年实心轮胎现状及发展趋势分析(目录)
- 基于GIS的农用地定级技术研究定稿
- 2017-2022年中国医疗保健市场调查与市场前景预测报告(目录) - 图文
- 作业
- OFDM技术仿真(MATLAB代码) - 图文
- Android工程师笔试题及答案
- 生命密码联合密码
- 空间地上权若干法律问题探究
- 江苏学业水平测试《机械基础》模拟试题
- 选课走班实施方案
- 工作研究
- 教材
- 资料
- 西北大学《地史学》真题03-12
- 广西林氏大族谱
- 安徽省合肥市第二中学2018届高三上学期期中考试物理 含解析
- 《运用现代信息技术培养学生创新精神的实验研究》
- 学生课堂行为准则
- 安全文明行车心得体会
- 傅立叶变换红外光谱仪技术指标 - 33079解析
- 副词的用法
- 向狼借路
- 公路工程试验检测员业务考试复习资料(材料)
- 2016-2017年黑龙江省大庆市林甸四中八年级下学期期中物理试卷和答案
- 唐于阗国三藏沙门实叉难陀译
- 七年级下册数学期末考试知识点总结
- 南大网院审计学第二次作业题库
- 入警大学生岗位任职培训大队培训指南 - 图文
- 《项脊轩志》评课稿
- 药物合成反应复习题
- 评审因素索引表
- 山东垦利2017届九年级语文上学期期末考试(五四制)
- 公司实施GSP情况综述供参考