自由锻造工艺规程
更新时间:2023-11-23 13:19:01 阅读量: 教育文库 文档下载
第八章 自由锻造工艺规程编制
本章将主要介绍自由锻造工艺规程编制过程并举例进行说明。自由锻造工艺规程主要由锻件图的设计,计算锻件重量,确定坯料规格或钢锭规格;设计锻造工步,计算变形程度;确定锻造温度以及加热火次、确定锻件复杂程度;确定锻造设备、工装及工具;确定坯料加热规范、锻件冷却及热处理规范、锻件表面清理规范;确定锻件理化检验规范等等。
编制工艺过程时应注意下述两个原则
1)根据车间现有的条件,所编制的工艺技术先进,能满足产品的全部技术要求。
2)在保证优质的基础上,提高生产率,节约金属材料消耗,经济合理。
8.1.设计锻件图
锻件图是编制锻造工艺、设计工具、指导生产和验收锻件的主要依据,也是联系其它后续加工工艺的重要技术资料,它是根据零件图考虑了加工余量,锻件公差、锻造余块、检验试样及工艺卡头等绘制而成。
一般锻件的尺寸和表面粗糙度,达不到零件图的要求,锻件表面应留有一定的机械加工余量(以下简称余量)。余量的大小主要取决于:零件的形状尺寸和加工精度、表面粗糙度要求、锻件加热质量、设备工具精度和操作技术水平等。零件的公称尺寸加上余量即为锻件公称尺寸,对于非加工表面,则无需加放余量。
在锻造生产实际中,由于各种因素的影响,如终锻温度的差异、锻压设备工具的精度和工人操作技术上的差异、锻件实际尺寸不可能达到公称尺寸,允许有一定的误差,称为锻造公差。锻件上不论是否需经机械加工,都应注明锻造公差。通常公差约为余量的1/4~1/3。
锻件的余量和公差具体数值可查阅有关手册、标准或工厂标准确定。
余量余面余块余量余面余块余量余块试样试样热缓冲区或工艺夹头
图8.1 锻件的各种余块
为了简化锻件外形或根据锻造工艺需要,在零件上较小的孔、狭窄的凹档、直径差较小而长度不大的台阶等
1
难于锻造的地方,通常都需填满金属(这部分金属叫做锻造余块),但这样做增加了机械加工工时和金属损耗。因此,是否加放余块,应根据零件形状、锻造技术水平、加工成本等综合考虑确定。
除了锻造工艺要求加放余块之外,对于有特殊要求的锻件,尚需在锻件的适当位置添加试样余块(供检验锻件内部组织和力学性能试验用等)、热处理或机械加工用夹头等。见图8.1示例。
当余量、公差和余块等确定之后,便可绘制锻件图。锻件图上锻件形状用粗实线描绘。为了便于了解零件的形状和检查锻后的实际余量,在锻件图内用假想线画出零件简单形状。锻件的尺寸和公差标注在尺寸线上面。零件的尺寸加括号标注在尺寸线下面。如锻件带有检验试样、热处理夹头时,锻件图上应注明其尺寸和位置。在图上无法表示的某些条件,可以技术条件方式加以说明。图8.2为一法兰带试样的锻件图。
φ300±6(φ273)
图8.2 法兰锻件图
50零件与试样区分割线φ350±6(φ335)8.2计算锻件重量、确定锻造坯料规格
自由锻用原材料有两种:一种是钢材、钢坯、多用于中小型锻件;另一种是钢锭,主要用于大中型锻件。
8.2.1.毛坯重量的计算
锻制锻件所需用的毛坯重量为锻件重量与锻造时金属损耗的重量之和,计算重量的公式如下;
G毛坯=G锻件+G切头+G烧损
式中 G毛坯---所需的原毛坯重量; G锻件---锻件的重量;
G切头---锻造过程中切掉的料头等重量; G烧损---烧损的重量;
2
32±4(20)试样
112±4(90)
φ170±8(φ227)
当用钢锭作原毛坯时,上式中还应加上冒口重量G冒口和底部重量G底部。
锻件重量G锻件根据锻件图决定。对于复杂形状的锻件,一般先将锻件分成形状简单的几个单元体,然后按公称尺寸计算每个单元体的体积,G锻件可按下式求得;
G锻件=γ(V1+V2+?+Vn) 式中 γ----金属的密度;
V1+V2+?+Vn-----各单元体体积。
对轴类锻件需考虑台阶处之余面(图8.3、8.4)所需的重量。
d余面≈10° 图8.3 台阶轴类锻件余面
其计算公式为:G余面=0.2(D-d)(D+2d)(尺寸以dm计算);
2
图8.4 曲轴类锻件余面
其计算公式为:G余面=hB(尺寸以dm计算)。
G切头包括修切锻件端部时的料头重量和冲孔芯料等,端部料头重量的计算方法见表8.1。
表8.1是一种最简单的端部切料情况的计算方法,而实际上切料的数值与锻件的复杂程度有关。例如锻造台阶时,为防止内凹和夹层现象,压痕和压肩时端部所留的最短长度应大于0.3D。如果台阶轴的轴颈较短时,则切区的料头重量便要 较多。因此,复杂件切料的数值根据具体工艺来定。
3
2
≈15°余面BhD
表8.1 端部料头的计算公式
毛坯形状 端部料头重量/kg G=1.8D BD3G=2.36HB 2 H 冲孔芯料决定于冲孔方法和锻件尺寸,计算方法见表8.2.
表8.2冲孔芯料的计算
冲孔方法 芯料体积(mm) 3芯料重量(kg) 实心孔冲孔 在垫环上冲孔 V芯=(0.15~0.20)dH V芯=(0.55~0.60)dH 22G芯=(1.18~1.57)dH G芯=(4.32~4.71)dH 22注:表中d --------实心孔之直径(mm) H --------冲孔前坯料的高度(mm)
表8.3 火耗与加热次数所占锻件重量的百分比
加热次数 材料 加热介质 第一火 一般碳钢及合金钢 Cr12、Cr12Mo, 煤、天然气 高速钢、不锈钢 烧损的重量G烧损与炉子的类型,毛坯的性质和加热次数等有关,一般用所占的百分数表示。见表8.3。 钢锭冒口和底部切区的重量G冒口和G底部占整个钢锭重量百分比见表8.4。
1.5% 1.0% 煤、天然气 2.5% 第二、三、??火 2% 8.2.2.毛坯尺寸的确定
4
毛坯尺寸的确定与所采用的第一个基本工步(镦粗或拔长)有关,所采用的工步不同,确定的方法也不一样。
表8.4钢锭冒口和底部切去的重量百分比(%)
原材料种类 切去重量 冒 口 底 部
(1) 采用镦粗法锻制锻件时,毛坯尺寸的确定
对于钢坯,为避免镦粗时产生弯曲,应使毛坯高度H不超过其直径D(或方形边长A)的2.5倍,但为了在截料时便于操作,毛坯高度H不应小于1.25D(或A),即
1.25D(A)≤H≤2.5D(A) 对圆毛坯; D=(0.8~1)3 对方毛坯; A=(0.75~0.8)3 14~25 5~7 碳素钢锭 合金钢锭或锻 重要零件时 25~30 7~10 V坯
V坯
初步确定了D(或A)之后,应根据国家标准选用标准 直径或边长。
最后根据毛坯体积V坯和毛坯的截面积F坯,即可求得毛坯的高度(或长度)
H=V坯/F坯
对算的的毛坯H,还需按下式进行检验; H<0.75H行程 式中 H行程-------锤头的行程。
此外,毛坯高度,还应小于加热炉底的有效长度。 对于锭料,根据所需的毛坯重量和钢锭规格来选择 (2) 采用拔长法锻制锻件时,毛坯尺寸的确定
对于钢坯,拔长时所用截面F坯的大小应保证能够得到所要求的锻造比。
F坯= KL F锻
即式中KL ----锻造比。
5
F锻-------锻件的最大横截面积。
按上式求出钢坯的最小横截面积,并可进一步求出钢坯的直径(或边长)。
然后,根据国家标准或厂标选用标准直径(或边长),若没有所需的尺寸时,则取相邻的较大标准尺寸。 最后,根据毛坯体积V坯和确定的毛坯横截面积求出钢坯的长度L坯
L坯=V坯/F坯
8.2.3.钢锭规格的选择
当选用钢锭为原材料时,选择钢锭规格的方法有两种。 第一种方法:首先确定各种金属损耗,求出钢锭利用率η:
δ
η=[1-(δ
冒口
冒口
+δ
锭底
+δ
烧损
)]3100%
式中
、δ
烧损
锭底
分别为切去冒口和锭底的重量占钢锭重量的百分数;可参照表12-2估算。
δ为加热烧损率。
然后计算钢锭的计算重量G锭=(G锻+G损)/η
式中G锻为锻件重量,G损为除冒口、锭底及烧损以外的损耗重量。
根据钢锭的计算重量,参照有关钢锭规格表,选取重量相等或稍大的钢锭规格即可。
第二种方法:根据锻件类型参照经验资料先定出概略的钢锭利用率η,然后求得钢锭的计算重量G锭=G锻/η,
再从有关钢锭规格表,选取所需的钢锭规格。
8.3.设计锻造工步、计算变形程度
设计锻造工步是编制工艺中最重要的部分,也是难度较大的部分,因为影响的因素很多,例如工人的经验、技术水平、车间设备条件、坯料情况、生产批量,工具辅具情况,锻件的技术要求等。决定变形工艺时,在结合车间具体生产条件的情况下应尽量采用先进技术,以保证获得好的锻件质量、高的生产率和较少的材料消耗。
各类锻件变形工步的选择可根据各变形工步的变形特点,锻件的形状、尺寸,技术要求和参考有关典型工艺具体确定。
对具体工件确定锻造方法时应根据各厂的经验和工具情况具体确定。因为甚至对同一锻件,在同一车间各人的锻造方法也不完全一样,尤其对位于分界线上或其附近的空心锻件可能有几种锻造方法。例对批量较大、尺寸较小的空心锻件,也可以采用胎模锻造;对环形件还可以在冲口后用扩孔机扩孔。具体可参见前面章节。
工步尺寸设计和工步选择是同时进行的,具体确定工步尺寸时应注意下列各点:
(1)工步尺寸必须符合各工步的规则,例如镦粗时毛坯高度与直径比值应小于2.5~3。拔长时截面变换经验计算公式见表8.5。
6
表8.5 拔长过程坯料截面变换经验计算公式
截面变换内容 变形简图 计算公式 由圆变方 DA当l=b时:D=(1.35-1.45)A; l:送进量;b:砧宽。 由方变圆 ADA=(0.88-1.0)D 由圆变扁方 ABH(1)当H<0.5B: D=(2B+H)/3; (2)当H≥0.5B: D=H2+B2 由方变扁方 ABA≥1.5H(1?1.8B-1) HH 由八角变圆 CDD= 1.03C 由扁方变方 BA 当砧宽b≥1-1.4时: B=(1.4-1.65)A 锻件宽HH H=(0.75-0.8)A 7
工步尺寸设计和工步选择是同时进行的,具体确定工步尺寸时应注意下列各点:
(1)工步尺寸必须符合各工步的规则,例如镦粗时毛坯高度与直径比值应小于2.5~3。拔长时截面变换经验计算公式见表8.5
(2)必须估计到各工步中毛坯尺寸的变化,例如冲孔时毛坯高度有些减小,扩孔时高度有些增加等等。 (3)必须保证各部分有足够的体积,这在使用分锻工步(压痕、压肩)时必须估计到。 (4)多火次锻打时必须注意中间各火次加热的可能性。
(5)必须保证在最后修光时有足够的修整留量,因为在压肩、错移、冲孔等工步中毛坯上有拉缩现象,这就必须在中间工步中留有一定的修整留量。
(6)有些长轴类零件长度方向尺寸要求很准确,但沿长度方向又不允许进行镦粗(例如曲轴等),设计工步尺寸时,必须估计到长度方向的尺寸在修整时会略有延伸。
图8.5、8.6、8.7、8.8、8.8、8.10、8.11、简单的描述了一些典型锻件的锻造变形工步。 图8.5 齿轮锻造变形过程
图8.7圆环锻造变形过程
8
图8.6 锤头锻造变形过程
图8.8圆筒锻造变形过程
Ⅱ15ⅠⅢⅡⅠⅢⅢ2ⅠⅡⅢⅡ6ⅠⅢ转90°37Ⅱ Ⅰ30°ⅠⅡⅢⅢ4ⅠⅡⅢ8 ⅡⅠ 30°图8.8 三拐曲轴锻造变形过程
1) 2)
3) 4) 5) 6) 7)
8)9)8.10 20吨吊钩锻造变形过程 图8.11 卡瓦锻造变形过程
9
图
表8.6锻造比的计算方法
序号 锻造工步 变形简图 工步锻造比 1 钢锭或坯料拔长 D12KL?2D2D1D2 D0D1l02 拔长-镦粗-拔长或镦粗-拔长-镦粗 l1D2l22D12D3llKL?KL1?KL2?2?2?2?4D2D4l1l3D3h3D4或K?K?K?l0?l2LN1N2l1l3 l4 D0d1d0D14 芯轴拔长 l0l1 22D0?d0lKL?22?1 D1?d1l0D0D1d0l0d1 l15 马杠扩孔 KL?D0?d0l0 ?D1?d1l1轮缘K?H0 HHH16 镦粗 H0H2H1轮毂K?H0 HH2
10
1. 钢锭开坯倒棱锻造比不计入总锻比 说2. 连续拔长或连续镦粗,总锻造比等于工步锻比的乘积K?KL1KL2KL3?,K?KN1KN2KN3? 总锻造比等于两次拔长(或镦粗)工步锻造比之和,明 3. 两次拔长之间有镦粗或两次镦粗之间有拔长,KL?KL1?KL2或KL?KN1?KN2并且要求工步锻造比KL1,KL2,KN1,KN2≥2
锻造比是表示变形程度的一种方法,是衡量锻件质量的一个重要指标。锻件比的计算方法,各国家、各行业均不一致。锻造过程锻造比的我国的一般计算方法是按拔长或镦粗前后锻件的截面比或高度比计算,即锻比KL =S0/S=D0/D12或KL=H0/H1(S0、S、D0、D1、 H0、H1分别是锻造前、后的截面积、直径和高度)。如果采用两次镦粗、拔长,或者两次镦粗间有拔长时,按总锻造比等于两次分锻造比之和计算,即KL总=KL1+ KL2。如果是连续拔长或镦粗时,按总锻造比等于两次分锻造比之积计算,即KL总=KL13 KL2。表8.6列出了我国大锻件行业常用的锻造比计算方法。
锻造比大小反映了锻造对锻件组织和力学性能的影响,一般规律是:锻造过程随着锻造比增大,由于内部孔隙焊合,铸态树枝晶被打碎,锻件的纵向和横向的力学性能均得到明显提高。当锻造比超过一定数值后,由于形成纤维组织,横向力学性能(塑性、韧性)急剧下降,导致锻件出现各向异性。因此制订锻造工艺规程时,应合理地选择锻造比的大小。
对于用钢材锻制的锻件(莱氏体钢锻件除外),由于钢材经过了大变形的锻或轧,其组织和性能已得到改善,一般不需要考虑锻造比;用钢锭(包括有色金属铸锭)锻制的大型锻件,必须考虑锻造比,可参照表8.7选用。零件技术条件提出有锻造比要求,则以技术条件要求选择锻造比;如零件技术条件没有要求锻造比,则应根据零件化学成分、零件受力情况、以及所用钢锭大小等因素综合考虑。
表8.7 典型锻件的锻造比
锻件名称 碳素钢轴 合金钢轴 热轧辊 冷轧辊 船用轴 水轮机空心轴 曲轴 计算部位 最大截面 辊身 法兰 轴身 法兰 轴身 曲拐 轴颈 总锻造比 2.0~2.5 2.5~3.0 2.5~3.0 3.5~5.0 >1.5 ≥3.0 >1.5 ≥2.5 >2.0 ≥3.0 锻件名称 模块 汽轮机转子 发电机转子 汽轮机叶轮 涡轮盘 航空用大锻件 计算部位 最大截面 轴身 轮毂 轮缘 最大截面 总锻造比 ≥3.0 3.5~6.0 4.0~6.0 6.0~8.0 6.0~8.0 2
一般情况下,合金结构钢比碳素结构钢钢锭的铸造缺陷严重,所需锻造比应大些。如拔长5吨、15吨、和30吨以上的钢锭时,碳素结构钢锻件的最佳锻比相应为2、2.5、3,而合金结构钢锻件的最佳锻造比为3~4。
对一般结构钢锻件,当零件受力方向与纤维方向不一致时,为了保证锻件的横向性能,避免产生各向异性,
11
应取锻比2~2.5。当零件受力方向与纤维方向一致时,为使纵向纵向力学性能提高,可将锻造比选取为4。对于一些重要零件(如航空锻件、高合金锻件)为了充分破碎铸态组织,获得较高的综合机械性能,常用镦粗拔长联合工艺,锻造比要求达到6~8。
8.4.确定锻造温度和加热火次、确定锻件复杂程度
8.4.1确定锻造温度。
即控制锻件材料锻造时的始端温度和终端温度。主要根据文件手册、标准以及工厂实际经验进行控制。表8.8列出了常用钢料的锻造温度范围,包括始锻温度和终锻温度。
8.4.2加热火次。
加热火次与炉子的类型,毛坯的性质和操作水平等有关,有关火耗的具体算法见本章第二节。
8.4.3确定锻件复杂程度
表8.8 常用钢号的始锻、终锻(精锻)加热温度
组别 Ⅰ Q185~Q255,10~30 35~45,15Mn~35Mn,15Cr~35Cr 50, 55, 40Mn~50Mn, 35Mn2~50Mn2, 40Cr~55Cr, 20SiMn~35SiMn, 12CrMo~50CrMo, 30CrMnSi, 20CrMnTi, 20MnMo, 12CrMoV~35CrMoV, 34CrMo1A, 20MnMoNb, 14MnMoV~42MnMoV, 38CrMoAlA, 38CrMnMo 34CrNiMo~34CrNi3Mo, 30Cr1Mo1V, 25Cr2Ni4MoV, PCrNi1Mo~ PcrNi3Mo, 22Cr2Ni4MoV, 5CrNiMo 30Cr2MoV, 40CrNiMo, 18CrNiW, 50Si2~60Si2, 65Mn, 50CrNiW, 50CrMnMo, 60CrMnMo, 60CrMnV Ⅲ T7~T10, 8Cr, 8Cr2, 8Cr2Mo, 8Cr2V, 8CrSi, 70Cr3Mo, 1Cr13~4Cr13, 86Cr2MoV, Cr5Mo, 0Cr18Ni8~2Cr18Ni8, 0Cr18Ni8Ti, Cr17Ni2 50Mn18Cr4, 50Mn18Cr4N, 50Mn18Cr4WN, GCr15, GCr15SiMn, 3Cr2W8V, CrWMo, 4CrW2Si~6CrW2Si Cr12 MoV1, 4Cr15MoVSi(H11), W18Cr4 锻件的复杂系数分为锤上锻造和水压机锻造。参照JB/T4385.2-1888《锤上自由锻件 复杂程度分类及折合系数》、JB/T8178.2-1888《水压机上自由锻件 复杂程度分类及折合系数》、取复杂程度相近似的等级。
1240 1220 850 800 钢号 始锻温度℃ 钢坯 1280 1260 钢坯 1260 1240 终端温度℃ 终锻 750 750 精整 700 700 Ⅱ 1250 1220 800 750 1220 1200 850 800 1200 1180 1180 1160 850 850 800 800 12
8.5 确定锻造设备、工装及工具
自由锻常用的设备为锻锤和水压机。这些设备虽无过载损坏问题,但若设备吨位选得过小,则锻件内部锻不透,而且生产率低,反之,若设备吨位选得过大,不仅浪费动力,而且由于大设备工作速度低,同样也影响生产率和锻件成本。因此,正确确定设备吨位是编制工艺规程的重要环节之一。
锻造所需设备吨位,主要与变形面积、锻件材质、变形温度等因素有关。在自由锻中变形面积由锻件大小和变形工步性质而定。镦粗时锻件与工件的接触面积相对于其它变形工步要大得多,而很多锻造过程均与镦粗有关,因此,常以镦粗力的大小来选择设备。
确定设备吨位的方法有:理论计算法和经验类比法两种。 1. 理论计算法
理论计算法是根据塑性成形理论建立的公式来计算设备的吨位。尽管目前这些计算公式还不够精确,但仍能给设备确定吨位提供一定的参考依据。
水压机锻造时,由于压力变化比较平稳,故可根据锻件成形所需的最大变形力来选择设备吨位。 水压机锻造时,锻件成形所需最大变形力可按以下公式计算:
F=P2A
(式中 A:锻件与工具的接触面在水平方向上的投影面积;P:锻件与工具接触面上的单位流动压力,即评均单位压力)。
用锻锤锻造,由于其打击力是不定的,所以应根据锻件成形所需变形功来选择设备打击能量或吨位。 圆柱体锻件镦粗变形功为:
W=RelV[In(H0/H)+((D/H)-(D0/H))/8]
(式中D0、H0:为坯料的直径和高度;D、H:为锻件的直径和高度;V:锻件的体积。) 长板形锻件镦粗变形功为
W=RelV[In(H0/H)+((b/H)-(b0/H))/8]
(式中b0、H0:为坯料的宽度和高度;b、H:为镦粗后宽度和高度;V:锻件的体积。) 根据最后一击的变形功W,考虑锻锤的打击效率η,便可算出所需打击能量E(J),即
E=W/η
通常锻锤吨位是以落下重量G(kg)表示,与打击能量有如下关系:
G=2g/υ- W/η
2
(式中g:重力加速度,g=8.8m/s;υ:为锻锤打击速度,一般取υ=6~7m/s;η:打击效率)。 如取υ=6.5m/s, η=0.8,则得
13
G=W/1.72
2. 经验类比法
经验类比法是在统计分析生产实践数据的基础上,总结归纳出的经验公式或图表来估算锻造所需设备吨位的一种方法,应用时只需根据锻件的某些主要参数(如重量、尺寸、材质)便可迅速确定设备吨位。
锻锤吨位(kg)可按如下公式计算: 镦粗时 G=(0.002~0.003)K2S
(式中K :与材料强度极限Rm有关的系数,按表8-8确定;S:锻件镦粗后的横截面积(cm2))。
拔长时 G=2.5S
800 (式中S:坯料的横截面积(cm))。 自由锻用锻锤的锻造能力范围可参照表8.10。
表8.10 自由锻造锻锤能力
设备吨位 锻件类型 圆饼 圆环 圆筒 D(mm) H(mm) D(mm) H(mm) D(mm) d(mm) H(mm) 圆轴 方块 扁方 锻件成型 吊钩 D(mm) G(kg) H(mm) G(kg) B(mm) H(mm) G(kg) 起重量(t) 0.25 0.5 0.75 1.0 2.0 3.0 5.0 2
表8.8 系数K
Rm(MPa) 400 600 K 3~5 5~8 8~13 <200 <35 <150 ≤60 <150 ≥100 ≤150 <80 <100 ≤80 <25 ≤100 ≥7 6 3 125 100 <250 <50 <350 ≤75 <175 ≥125 ≤200 <125 <200 ≤150 <50 ≤160 ≥15 20 5 200 175 <300 <100 <400 <100 <250 >125 ≤275 <150 <300 ≤175 <70 <175 ≥20 35 10 250 225 ≤400 <150 ≤500 <150 <275 ≥125 ≤300 ≤175 <500 ≤200 ≤100 ≤200 ≥25 50 20 300 275 ≤500 ≤250 ≤600 ≤200 <300 >125 ≤350 ≤225 ≤750 ≤250 ≤350 <400 ≥40 70 30 400 350 ≤600 ≤300 ≤1000 <250 <360 >150 ≤400 ≤275 ≤1000 ≤300 ≤800 ≤600 ≥50 100 50 450 400 ≤750 ≤300 ≤1200 ≤300 ≤700 >500 ≤550 ≤350 ≤1500 ≤450 ≤1000 ≤700 ≥70 300 75 600 550 钢锭直径(mm) 钢锭边长(mm) 自由锻液压机能力及配套设备,见表8.11。
14
表8-11 液压机能力及配套设备
镦粗最大钢锭 液压机公称压力/MN 平均对质量/t 径/mm 2.5 5 488 634 拔长最大钢锭 质量/t 5 8 平均对径/mm 634 751 起重量/t 5 10 操作机 倾翻力矩台数 /(KN2m) 100 250 1 1 锻造吊车、翻料机 运输吊车 加热炉 炉底总面积/㎡ 24.3 36.45 台数 3 3 4 103 热处理炉 起重量/t 台数 起重量/t 台数 台数 炉底总面积/㎡ 8 12.5 15/3 20/5 80/30 60 (翻料机自重10) 80/30 65 (翻料机自重10) 150/50/10 130 (翻料机自重25) 300/100/5 250 (翻料机自重64) 1 1 1 1 50/10 50/10 30/5 1 1 1 2 3 5 1 (保温) 5 1 (保温) 7 1 (保温) 30.25 67.56 120 25 24 1063 48 1406 10~20 250~500 1 30 32 1178 52 1406 20~40 500~1000 1 1 1 50/10 2 4 122 146.25 60 60 1486 130 1886 50~80 1300~2000 2 2 150/30 150/50 1 1 8 230.42 1~2 306.6 120 150 2105 300 >2404 100~150 2500~3500 2 2 250/50 1~2 1 5 1 (保温) 6 333.8 383.6
15
8.6 确定坯料加热规范、锻件冷却及热处理规范、锻件表面清理规范
8.6.1确定坯料的加热规范
钢锭与钢坯锻造前的加热是锻造生产中十分重要的环节。合理的锻前加热,不仅能改善锻压成形过程,防止裂纹、过烧、温度不均匀等缺陷,而且对提高锻件组织性能有重要的影响。
表8.8 列出了常用钢料的锻造温度范围,包括最高加热温度及终锻温度。确定钢料的锻造温度范围,一般按钢的化学成分选定。但合理的锻造温度还应该考虑工厂具体的生产条件(如钢锭的冶金质量、加热设备性能、锻后热处理技术等)、锻件技术要求和大型锻造特点等因素进行适当的调整。重要的特殊钢锻件往往要求制订专门的加热制度。
1) 冷钢锭加热。冷钢锭塑性低,当加热速度超过允许值时,热应力大,容易产生加热裂纹。对于大型钢锭应限速升温、分段加热。对于组织结构复杂、残余应力较大的合金钢钢锭,应采用低温装炉。以允许的加热速度升温。并在400℃~600℃和700℃~850℃阶段保温,以防加热时钢锭脆性开裂。在进入塑性状态后。方可按加热炉最大升温速度加热至锻造温度。
2) 热钢锭加热。表面温度高于550℃~600℃的钢锭称为热钢锭。热钢锭处于高温、高塑性状态,可以高温装炉,快速加热。
3) 严禁冷、热钢锭同炉进行加热。
4) 为了配炉,不同钢号、不同规格的钢锭同炉加热时,应按最低的温度,最长的加热时间,制订加热规范。其中始锻温度低、保温时间较短者,可出炉锻造,其余可适当延长保温时间。
5) 高温保温时间。无论冷锭、热锭加热至锻造温度后,都应保温一定的时间,以达到均匀、热透和高温扩散的目的。
6) 加热温度。加热炉的炉温应比料温高30~50℃。钢料最高加热温度,应考虑不同钢种的过热敏感的钢料或组织结构,最高的加热温度可以适当降低。
7) 坯料重复加热的规定。锻件锻造中需要重复加热时,其加热温度应按剩余锻造比(K)确定。当K≥1.5时,可加热至最高温度,并正常保温。当K<1.5时,则应降低加热温度(1050℃)或装入高温炉保温。但保温时间比正常减少1/3,以防工步变形小,锻件晶粒粗化。如果锻后热处理可矫正锻件粗晶组织,也可不考虑工步锻造比对加热粗晶的影响。
具体的锻件加热规范的制订可参考JB/T 6052 《钢质自由锻件加热通用技术条件》。
随着钢锭冶金质量的提高和锻压、热处理技术的进步,大锻件加热工艺的发展趋势是提高加热温度,扩大锻压温度范围,缩短加热时间,节省燃料消耗,提高生产效率。因而,现有的加热制度,将会
16
不断进行调整和修订。
8.6.2锻件冷却及热处理规范
锻件锻后冷却和热处理方式,包括锻后冷却、退火(低温退火、中间退火、完全退火等温退火等)、正火及回火、调质、等温冷却及起伏等温退火等。
锻件冷却和热处理规范是根据钢的化学成分、传热截面尺寸、锻件技术要求并考虑白点敏感性及回火脆性倾向而制订。
用钢坯锻制锻件的冷却方式见表8.12。
表8.12钢坯锻制锻件的冷却方式
用轧材、锻坯锻制的锻件锻后冷却方法 锻件截面尺寸(mm) <50 A0~A7,Q185~Q275,Q285~Q460,15MnTi,10~70,15CrMn~60Mn,15Cr~30Cr 35Cr~50Cr,60Si2Mn,65Mn~70Mn,20Mn2~50Mn2,35CrMn,30CrMo,35CrMo,42CrMo,35SiMn, 34CrMo1A,25SiMn2MoV,25Cr2MoVA,25Cr2Mo1VA, 20CrNi~50CrNi,12Cr1MoV,12Cr3MoA,12CrNi3,12Cr2Ni4,20Crni3,20Cr2Ni4A,25Cr2MoVA,20CrMn~50CrMn,20CrMo,30CrNi3,21/4Cr-1Mo,20CrNiMo,20Cr3NiMoA,20CrMnMo,18CrMnTi,18CrMnMo,40Cr2MoV,40CrMnMo,40CrNiMoA,8630,4040,4340,A4345,A4145,18MnMoNb,40MnB,14CrMnMoVB,Cr5Mo,38CrMoAI CrMn,CrWMn,8CrSi,MnCrWV,8CrSi2,3Cr2W8V 5CrNiMo,5CrMnMo,4Cr5MoSiV1(H13) W18Cr4V,W6Mo5Cr4V2,6W6Mo5Cr4V,65Nb,Cr12,Cr12MoV 用钢锭锻制锻件的冷却方式见表8.13。
锻件的热处理规范,主要依据锻件技术要求而制订,表8.14,主要列出了一些常见材料的锻后热处理方法。
17
材质 空冷 空冷 51~100 101~150 空冷 151~200 201~300 空冷 空冷 空冷 空冷 空冷 堆冷 坑冷 空冷 空冷 炉冷 700℃前在空气中冷却然后入保温坑冷却 坑冷 炉冷 炉冷 炉冷 炉冷 炉冷 炉冷 炉冷 炉冷 炉冷
表8.13 钢锭锻制锻件的冷却方式
锻件有效截面最大尺寸 钢号举例 15-30 35-45 ≤50 51-100 101-400 炉冷 401-500 坑冷 空冷 55Cr、55Mn2、35CrMo、20MnMo、35CrMnSi、T8、38SiMnMo、60Si2 GCr15、8Cr2、5CrMnMo、60CrNi
表8.14 不同材质锻件的锻后热处理方法
序号 热处理方法 锻件钢号 35、40、45、50、55、60、A5、A6、A7、15Mn-40Mn、20CrNi-40CrNi、 12CrNi2、12CrNi3、12CrNi4、20CrNi2、20CrNi4、30Cr-50Cr、 20CrMo、35CrMo、42CrMo、20CrMn-40CrMn、18CrMnTi、18CrMnMo、 40CrMnMo、35SiMn、20CrMoV、35CrMoV、25Cr2MoV、45Mn2、 50Mn2、Cr5Mo、50Mn 1 正火 2 退火 65、70、60Mn-70Mn、T7-T13、5CrMnMo、5CrNiMo、5CrNiW、5CrNiSi、 5CrWMn、5CrNiTi、7Cr3、8Cr3、Cr、CrMn 、CrWMn 、Cr12、Cr12Mo、 W8Cr4V、W18Cr4V、8CrSi、55SiMn、60SiMn、55SiMn、60SiMn、 55Si、15CrMoV、GCr6、GCr8、GCr15、GCr15SiMn 3 4
固溶 不处理 0Cr18Ni8、1Cr18Ni8、2Cr18Ni8、1Cr18Ni8Ti、Cr18Ni12Mo2Ti、Cr18Ni12Mo3Ti A0-A4、08-30、15Cr 8.6.3锻件表面清理规范
1) 清理的目的。
在生产过程中,由于毛坯加热、锻造和锻后热处理时被氧化和损伤,锻件表面会形成氧化皮、表面缺陷或存在油污、润滑剂或残留物,这些都是必须要通过清理加以清除。清理的目的在于:
1提高锻件表面质量,保证后续工步的顺利进行。对于需要冷校正或锻件本身不便加工的锻件,为了避○
免氧化皮压入锻件或影响锻件精度和表面粗糙度,必须进行表面清理。 2改善锻件切削加工条件。 ○
3显露锻件表面缺陷(如折叠、裂纹、凹坑等)以便消除这些缺陷。 ○
18
锻件和毛坯的清理包括热毛坯、冷锻件或冷毛坯、锻件或毛坯的局部表面缺陷清理等三种清理。 2) 热毛坯的清理
锻造前清理热毛坯的氧化皮,除了锻工常用的轻镦一下清除部分氧化皮的简单方法外,专门的清理方法有三种。
1手工清理和机械清理 ○
2高压水清理。 ○
3水中放电清理 ○
3) 冷锻件或冷毛坯的清理
根据冷锻件或冷毛坯的材料、形状和大小以及氧化皮的厚度,除挤压铝棒表层的粗晶环和钛合金毛坯表面的污染层外,均可采用多种方法进行清理,这些清理的方法是:滚筒清理、振动光饰、吹砂(喷丸)、抛丸、化学清理等。 4) 锻件局部表面缺陷的清理
锻件生产过程中,由于各种原因,在原始毛坯或中间毛坯或锻件上,都可能有一些局部表面缺陷,例如裂纹、折叠、拉伤、起皮、残余毛刺等。
局部表面缺陷常用打磨、风铲和火焰切割等方法清除。
8.6确定锻件的理化检验规范
理化检验主要包括材料的金相组织、低倍组织、化学成分分析、晶粒度评定、非金属物夹杂评定、机械性能检验、抗H2S腐蚀开裂评定等。
理化检验规范以及验收标准的确定主要依据技术图纸要求或技术规范规定或相关标准要求,通过按照一定的标准规定检验并验收。要求在检验规范中明确检验项目以及检验方法和验收标准等。
8.7.自由锻锻造工艺规程编制举例
8.7.1环类锻件的自由锻造工艺规程编制
该零件材料为45钢,零件交货图如图8.12所示,锻件正火粗加工状态交货。 1) 设计绘制锻件图
根据《热轧环形件机械加工余量及公差》(JB/T 10478-2004)查得锻件外径、内径、高度方向余量与公差a、b、c=20±7,于是便可绘出锻件图(图8.13)。
19
φ2111φ1984图8.12 导向环交货图
φ2131±6(φ2111)φ329(φ309)φ1964±8 (φ1984)图8.13 导向环锻件图
2) 计算锻件重量、确定坯料规格(尺寸均以mm计算) G锻件=7.853V锻310=1387.16kg
初步设定锻件镦粗至约H=370mm后冲孔,依据锻件净重估算锻件此时外径D≈780mm,取冲孔直径D芯=260mm。由表12-2,V芯=(0.15~0.20)dH。取V芯=0.20dH,得G芯=0.23D芯 3H37.85310=31kg。 锻件估计需要三火次,δ
烧损
2
2
2
-6
-6
取6.5%。故G坯=(1387.16+31)3(1+6.5%)≈1510kg。
由于第一道工步为镦粗,坯料直径按以下公式计算: 坯料直径D坯=(0.8~1.0)3
V坯=461~577mm,取D坯=480mm
2
则坯料高度H坯= H=V坯/(D坯3π/4)=1063mm 3) 设计锻造工步,计算锻造比
其变形工步为:镦粗-冲孔-马架扩孔-辗环机轧制。锻件壁厚为Bh锻件=83.5,高度约有35mm轧制量,
设定锻件马架扩孔扩到内径约为φ800mm,高度制到约365mm上辗环机轧制。
工步为:毛坯镦粗到高度约370mm,冲孔φ260(此时外径约为φ840),上马架,扩孔至φ800,高度至365(此时外径约为φ1135),上辗环机轧制至工艺尺寸。
锻造比K=1063/370+[(840-260)/(1135-800)]3[(1135-800)/(2131-1864)]≈6.3 4) 确定锻造设备及工装
20
309
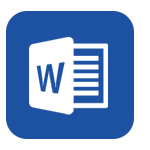





正在阅读:
自由锻造工艺规程11-23
唐朝重阳节的诗歌鉴赏12-11
广东省揭阳一中2014届高三上学期开学摸底考试数学理试题04-16
宝岛台湾02-13
(豫安监管办〔2018〕78号)附件1:安全风险分级管控与事故隐患排查治理双重预防机制构建实施指南09-16
项目实施管理及质量保障体系方案03-12
万科华南微信营销案例分析08-17
高考鉴赏诗歌的修辞手法09-07
- exercise2
- 铅锌矿详查地质设计 - 图文
- 厨余垃圾、餐厨垃圾堆肥系统设计方案
- 陈明珠开题报告
- 化工原理精选例题
- 政府形象宣传册营销案例
- 小学一至三年级语文阅读专项练习题
- 2014.民诉 期末考试 复习题
- 巅峰智业 - 做好顶层设计对建设城市的重要意义
- (三起)冀教版三年级英语上册Unit4 Lesson24练习题及答案
- 2017年实心轮胎现状及发展趋势分析(目录)
- 基于GIS的农用地定级技术研究定稿
- 2017-2022年中国医疗保健市场调查与市场前景预测报告(目录) - 图文
- 作业
- OFDM技术仿真(MATLAB代码) - 图文
- Android工程师笔试题及答案
- 生命密码联合密码
- 空间地上权若干法律问题探究
- 江苏学业水平测试《机械基础》模拟试题
- 选课走班实施方案
- 锻造
- 规程
- 工艺
- 自由
- 61850规约SCL文件工程实施介绍
- 湖北省武汉市四校联合体2017-2018学年高二上学期期末考试物理试题
- 温馨一刻,幸福之家- 暨南大学图书馆
- ARM汇编指令 对比记忆(整理)
- 试题题库-—2016年公安机关人民警察基本级执法资格考试题库及参考答案-综合类精华版
- ps实用技巧 2 - 图文
- 2010年一级建造师实务《通信与广电工程》真题
- 2013版用于立项大型冷藏保鲜设施项目可行性研究报告(甲级资质)审查要求及编制方案 - 图文
- 第二章 单相可控整流电路
- 中考物理试题分类汇编压强与浮力(共20页,有答案) - 图文
- 2013-2014年甘肃省兰州十一中九年级上学期10月月考语文试卷(纯word解析版)
- 广州版三年级上册英语期末试卷
- 物理化学考试秘籍
- 基坑支护要点 - 图文
- 中考数学二轮复习专题一选填重难点题型突破题型三规律探索问题试题
- 混凝土路面施工技术交底
- 设计心理学个人整理知识点
- 中国出口信用信用保险存在的问题及对策
- 医学微生物学与免疫学
- 2014高考英语阅读理解展望训练(12)