生产管理学教案
更新时间:2024-04-18 03:53:01 阅读量:1 综合文库 文档下载
生产管理学教案
李怀祖 主编
主讲:徐瑞园、李银满、刘满洲 机械工业出版社
第一章 生产管理概论 一、要点
⒈生产与生产管理
生产管理在企业中的作用和地位;市场经济体制下企业对生产管理提出的要求。 ⒉生产过程
工业企业生产过程的基本组成;生产过程的组织形式;加工对象在生产过程中的移动方式;生产过程的运作分析。 ⒊生产系统
生产系统的概念;生产系统的管理职能;生产系统的绩效评价。 ⒋生产类型
生产类型的分类准则及其基本类别;各基本生产类型的特征及其管理特点。 ⒌生产管理中的决策问题
生产管理中的主要决策问题;生产管理决策的主要方法。 二、基本要求
⒈理解生产管理在生产经营型企业中的地位和作用。 ⒉深刻理解生产过程的概念和分析方法。 ⒊理解生产系统的概念及其绩效评价。 ⒋深刻理解生产类型。
⒌了解生产管理中的决策问题。 三、重点与难点
⒈生产过程
⑴生产过程的组织形式 是指从事生产过程的各生产单位的组织形式。按分工协作关系的不同,可分为两种基本的组织形式:工艺专业化和对象专业化。
工艺专业化是按生产工艺的特点划分生产单位。这种单位集中同类设备和同工种工人进行同一工艺方法的加工。故只能完成产品生产过程中部分工艺阶段或部分工序。对象专业化则是按产品为对象划分生产单位。在一个生产单位内拥有制造生产对象所需的各种不同类型的设备和不同工种的工人。故能完成该种产品的全部或大部分工艺过程。这两种组织形式的优缺点与适用场合如表1-1所示。 表1-1 两种生产组织形式的对比 组织形式 优点 缺点 适用场合
工艺专业化 ①生产适应性强②设备利用率高③便于技术管理和技术指导 ①生产专业化程度低,生产效率较低②物流路线长,产品生产过程连续性差,使其生产周期长③单位之间联系关系复杂,管理工作困难 生产品种多,且变动大的生产部门
对象专业化 ①设备专用,生产效率高②物流路线短,产品生产周期短③简化管理工作,生产与经济责任明确 ①生产适应性差②设备利用率较低 生产品种固定,且产量大的生产部门
⑵生产过程中的移动方式 生产过程进行得是否有效可检查它的连续性和平行性,这些性能体现在工件的移动方式上,可用工件加工周期的长短来衡量。
有三种移动方式:顺序移动、平行移动和平行顺序移动。(参见教材图1-4、1-5、1-6)。 顺序移动方式的特点是整批工件完成一道工序的加工后,才移送到下道工序的工作地。这种方式下设备在加工过程中得到充分利用,但工件在每工作地的平均等待时间长。 平行移动方式是每加工完一件工件就移送到下个工作地进行下道工序的加工。这种方式使各工序平行进行,因而大大减少了工件的等待时间,缩短了工件的加工周期。但当上下工序时间不等时,会引起工序时间短的设备与工人经常停歇,降低设备的利用率。 平行顺序移动方式综合了平行移动和顺序移动的优点,一方面尽可能使上下工序平行进行,又尽量保证设备在加工过程中不发生停工。
对比三种移动方式的周期时间(参见教材式(1-1)、(1-2)、(1-3))可以看出,顺序移动方式的时间最长,平行移动方式的时间最短,平行顺序移动方式的时间居中。故应
结合工件批量,工序时间、重量与价值大小,以及生产单位的组织形式选择移动方式,使生产过程达到有效进行。
⑶生产过程的运作分析 任何生产过程都可抽象为从投入到产出的转换过程。要管理好生产过程必须掌握投入、转换和产出这三者在生产过程中的作用和管理要求。
生产过程的产出有产品和劳务两种。企业通过这些产出满足市场需求与社会需求,同时回收资金并获得盈利,以投入再生产。因此,产出不但是生产的成果,而更重要的还是生产过程的目标和依据。应从产量、质量、交货及成本上全面完成产品生产的目标要求,才能实现其应有的价值。
生产过程的投入包括劳力、材料、能源、设备、资金和信息等各种生产要素或生产资源。为完成一定的产出量必须投入必要的资源量。但获取这些资源需花费成本。生产过程中发生的这些成本称直接成本和制造费用。那些在产品中被全部消耗掉的资源成本,如直接材料、直接人工成本属于直接成本。另一些资源在生产产品中没有被全部消耗掉,如设备的使用、辅助工人的人工等。它们的成本属于制造费用。产品成本中这两部分成本的构成是否合理与生产规模和生产工艺技术水平有关。应适当选择与产量规模相应的工艺技术。 生产过程的转换就是产品制造的具体过程,包括作业、运输、贮存等三种活动。作业活动改变制造对象的性质、形状和大小,是形成产品并创造价值的基本活动,但同时也消耗资源而发生成本。其它两种则只花费成本不增加制件的附加值。管理转换过程应做到,尽量减少生产过程中的艺术和贮存活动,使作业之间连接紧密,尽少中断,从而使生产过程达到合理化。
⒉生产类型 生产类型是按生产重复程度,以及与之相联系的生产专业化程度对生产过程所做的分类。按这种分类准则可将工业企业生产过程分为大量生产、成批生产和单件生产。这三种生产类型在产品需求、生产工艺、物料供应、劳力、生产控制和职能管理作用等方面具有各自的特点,由此决定了它们需要采用不同的计划与控制方式。
大量生产由于生产重复程度高,可采用标准的生产作业计划,同时实行严格的质量控制与在制品控制。并必须有物料的大量供应以保证生产的顺利进行。
成批生产的产品品种较多,各品种产量较少,由于大部分为定型产品,故仍能保持一定的生产重复性。仍能按对象专业化原则建立生产单位和组织生产。它的管理重点是合理确定批量,协调成套出产产品零件与有效利用设备之间的矛盾。物料供应上要求按生产计划做好储备。
单件生产的产品很少重复,因此要求在生产设备,生产组织以及生产计划上有较强的适应性和灵活性。它的管理重点应在于尽量缩短产品生产周期、解决好生产能力的薄弱环节。物料供应虽不必事先储备,但仍应有稳定可靠的供应渠道,以保证生产的需要。 四、例题
⒈加工某零件需4道工序,批量为4件,工序时间分别为:t1=10min, t2=5min, t3=20min, =10min。试分别用平行移动和平行顺序移动两种方式计算它的全部加工周期。 (答案:T平=105 min;T平顺=120 min;)
⒉立山滤清器厂(详见教材第一章章末生产过程分析示例)决定产量为每周10000套。但由于材料供应以及管理不善,在本月的四周中生产合格品38000套,废品2000套。另外,在全月产量中有1000件冲压件是用加班生产出来的。试对该月生产的有效性进行评价。 (答案:E产=0.90; E成本=0.915;E生产率=0.915) 五、思考题
⒈分析比较工艺专业化和对象专业化两种生产组织形式的优缺点和适用场合?⒉平行顺序移动方式如何改进了顺序移动和平行移动方式的缺点?
⒊分析工业企业生产过程应从哪几方面着手,每方面应考虑那些问题? ⒋比较生产率与有效性的区别和用途?
⒌比较生产系统绩效的因素有哪些?说明各项因素的影响作用?
⒍机械工业企业的生产类型分哪几种基本类型,它们是依据什么特征划分的?⒎为什么说单件小批生产的技术经济效果不如大量大批生产类型的好? ⒏比较不同生产类型的生产计划与控制工作的特点? 六、计算题
⒈教材P22 16题和17题
⒉某街道工厂准备承揽编织毛衣的生产项目。有3种生产方法可以考虑,一是手工编织;二是手摇编织机;三是电动编织机。各方法的成本估计如表1-2所示。毛衣的原料由订货单位供应,不必计入成本。另外,估计全年需求量可能超过10000件。单价为5元。 表1-2
手工(元) 手摇(元) 电动(元)
人工成本(每件)设备使用费(年)管理费(年) 4010000 2300011000 11400011000
问:⑴若按年产10000件计算,应选何种方法有利,为什么? 若要求生产率达1.5以上,产量至少应为多少?
⒊某公司在年度1、2两季度的销售与成本资料如表1-3所示。 表1-3
第1季度 第2季度
单位售价(元/件)总销售量(件)人工工时人工成本(元/工时)材料用量(kg)材料成本(元/ kg)管理费用(元) 201000090001050001520000 2185007750104500 15.51800 问:⑴该两季度的利润与生产率分别为多少?比较这两项指标值在该两季度的变化。 ⑵以第1季度的产出与投入为基准,分析第2季度各项生产要素利用的有效性。 ⒋某工厂在近两年的销售额与主要成本资料如表1-4所示。 表1-4
1993年 1994年
产品销售量(t)产品售价(元/t)人工成本(元/年)能源成本(元/年)原料成本(元/年)管理费用(元/年) 100250018000050003000020000 140300035000060004000020000 求:⑴计算1993年、1994年度的利润与生产率? ⑵用增量分析方法评价1994年的经营效果?
第二章 生产技术准备组织 一、要点
⒈生产技术准备工作的意义和内容 ⒉新产品开发概述
新产品的概念,新产品开发的动力模式,产品生命周期,新产品的开发原则,新产品的开发方式.
⒊产品设计准备工作
对产品设计的要求;产品设计工作的种类;产品设计的程序;加快产品设计的途径和措施。 ⒋生产工艺的准备工作
工艺准备的工作程序;加快工艺准备的途径;工艺方案的经济分析。 ⒌新产品试制与鉴定 ⒍生产技术准备计划的编制
生产技术准备计划的种类;生产技术准备计划的编制;生产技术准备计划的执行和检查。 网络计划技术在生产技术准备计划工作中的应用
任务的分解;生产技术准备网络计划的编制;网络计划的调整与优化。 二、基本要点
⒈了解生产技术准备工作的意义和任务;
⒉理解新产品的概念、开发原则产品生命周期等。 ⒊理解产品设计准备工作; ⒋理解生产工艺准备工作; ⒌了解新产品试制与鉴定工作; ⒍了解生产技术准备计划的编制工作;
⒎掌握网络计划技术在生产技术准备工作中的应用方法。 三、重点与难点 ⒈产品设计准备工作
产品设计是生产技术准备工作的第一步。它包括从明确设计任务开始到确定产品具体结构、完成工作图为止的一系列工作。设计准备的质量决定了一个产品的技术水平、质量水平、劳动生产率水平和成本水平。因此是十分重要的一项准备工作。
对产品设计的根本要求是满足用户的使用要求。具体体现在产品有良好的使用性,可靠性、安全性、经济性、维修性等方面。
产品设计工作按其图样来源分为4种:①新产品的自行设计;②测绘仿制;③外来图样;④老产品的改进设计。不同的设计工作有不同的内容和要求。
自行设计应严格遵循设计程序,并应加强科研试验工作,把有效的科研成果应用到新产品中来,以提高它们的技术水平。测绘仿制则应作好选型工作;对外来图样必须进行认真的审查分析、弄清性能、结构和技术经济参数;对老产品的改进设计,要作好改进前后的对比分析,确保改进后的技术经济合理性。
产品设计的程序分为拟定技术任务书、技术设计和工作图设计,必须领会每一阶段的工作内容和所起的作用,以及必需的审核要求。
加快设计工作主要通过以下途径:提高\三化\程度,以扩大产品结构的继承性;合理分解产品;组织平行作业;采用各种快速设计手段。这些措施中着重掌握产品\三化\的概念。 ⒉生产工艺准备工作
生产工艺准备应解决产品如何制造的问题。由它保证产品生产达到设计要求,保证产品质量和生产效率,并指导工人操作。因此也是十分重要的一项准备工作。
工艺准备工作包括:工艺分析和审查、拟定工艺方案和制定工艺文件、编制工艺规程和工装设计制造等4个步骤。工艺分析和审查上检查产品设计是否符合本企业的制造条件,以保证产品能经济、高效地进行生产;工艺方案则要确定制定工艺的原则,以及产品制造中技术关键的解决方法,作为指导工艺设计的工作纲领;工艺文件是指导生产操作以及进行生产准备的具体技术资料,其中主要;是工艺规程。工艺规程按其详细程度又分为工艺过程卡片、工艺卡片、工序卡片等3种形式,应根据产品的产量规模与生产条件选择适当的工艺规程形式。工装设计制造工作中应着重处理好保证质量、提高生产效率和降低产品成本之间的关系。为此要合理确定工艺装备系数。
加快工艺准备的措施主要有提高工艺规程的典型化程度、以及提高工艺装备的标准化和规格化程度,以此来缩短准备周期、降低生产技术准备周期。 ⒊网络计划技术在生产技术准备工作中的应用 这是本章的难点。主要掌握以下问题:
⑴任务的分解和分析 这是把产品的生产技术准备工作分解为各项工序,并分析和确定工序间业务上和组织上相互联系和相互制约关系,最后应形成\工序逻辑关系表\。 ⑵网络图的绘制原则
①相邻两个结点之间唯有一条箭线; ②不许出现循环线路;
③网络图只能有一个起点和一个终点;
④每项活动(工序)只能有唯一的编号。为此需加虚线来表示平行工序和交叉工序。 ⑶网络计划的时间参数计算 网络计划中需计算的时间参数及计算公式为(设活动i-j的作业时间ti,j已给定): ①结点最早开始时间(ET) ETj=ETi+tij (i
当进入结点j的箭线有多条时,则有 ETj=max{ETik+tik,j}
K=1,2,...,n(n为进入结点j的箭线数) ②结点最迟结束时间(LT)
LTi=LTj-ti,j (i
当结点i后面的箭线有多条时,则有 LTi=min{LTjk-ti,jk}
K=1,2,...,n(n为结点i后面的箭线数)
③活动最早开始时间((ES)与最早结束时间(EF) ESi,j=ETi
EFi,j=ESi,j+ti,j= ETi+ti,j
④活动最迟开始时间(LS)与最迟结束时间(LF) LFi,j=LTJ
LSi,j=LFi,j-ti,j= LTj-ti,j
⑤总时差S,它是活动的最迟开始时间与最早开始时间之差。 Si,j=LSi,j-ESi,j=LTj-ETi-ti,j
⑥单时差SF,它是活动最迟开始时间与活动箭尾结点结点最迟结束时间之差。 SFi,j=LSi,j-LTi=LTj-LTi-ti,j
通过上述计算,一个重要用途是找出网络计划中的关键线路。所谓关键线路是指网络图上总时差为零的各项活动的连线。关键线路上各项活动为关键活动。它们作业时间之和构成工程的工期。
⑷网络计划的调整与优化 本章重点讨论时间-资源优化问题。它是在一定的资源条件下,使工期最短,或在一定的工期条件下,使投入资源量最少的优化问题。它的工作原理是,首先保证关键活动的资源需要量,以保证预期的最短工期。然后利用时差,调整非关键活动的进度来平衡资源需要量。即使每时段内的资源需要量不超过其供应量。 四、典型例题
⒈加工某种零件有两种工艺方案可供选择,第一种方案的设备与工具购置成本为3000元,材料与工时的单件成本为20元;第二种方案技术比较先进,设备与工具购置成本为14000元,而材料与工时的单件成本为10元,试确定在何种产量下应选择何种方案有利? (结论:临界产量为1100件,若产量小于1100件,则采用第一方案;若产量大于1100件,则采用第二方案)
⒉某化工厂正准备对一套化工设备进行更新。有两种方案可供选择,费用资料如表所示。 方案A、B的成本资料
方案 成本 A B
设备的购置成本(元) 80000 56000 设备使用寿命*(年) 8 8 其它间接费用(元) 1400 1600 单件可变费用(元/kg) 0.45 0.55 注:*按直线法对设备投资进行折旧。
预计今后8年内产量平均每季5t,请用临界点法确定: ①最佳决策方案。
②产量为多少时,方案发生变化。
(临界产量28t,①最佳决策方案为B;②当年产量大于28t时,A;当年产量小于28t时,B)
⒊上海工业大学附属工厂在安排某种电风扇生产时,对于专用工装费用开支的问题,提出了两种不同的方案:一为利用现有设备,依赖协作,不花钱,上马快,但可能成本较高,怕会得不偿失;二为制作专用工装,需投资6万元,但生产效率高,质量可以保证,经济上可能亦合算。有关资料如表2-3所示。试用临界点法进行分析比较。 方案 固定费用(F) 单件产品可变费用(V) 产量(Q) AB 060000 90元48元 2000台2000台 (临界产量1429台,采用B)
⒋根据表中所示的逻辑关系绘制网络图。 作业 a b c d e F
紧前作业 - - - a,b a,c a,b,c
⒌某项生产技术准备的各作业逻辑关系如表所示。试用表上计算法计算网络计划的时间值,并求工期和关键线路。 作业 A B C D E F G H I J 作业时间 4 8 2 3 5 6 8 15 4 6 紧前作业 - A A B B C C E,F D G
⒍图表示了某项生产技术准备工作的网络计划。箭线上标出了各作业项目的代号,括号中的数字,既表示该项工作的周期天数,同时表示该工作所需要的人员数,比如,工作项目
d的工作天数为4天,每天需要4人同时工作,求:
①假设人力不受限制,编制一份总准备周期最短的按时间坐标绘制的网络图。 ②假设每天只有10人工作,编制一份可行的使人力利用尽可能均衡的网络图。 ③绘制两种计划的人力负荷图。 五、思考题
⒈为做好生产技术准备工作,应重点抓好哪几项工作? ⒉什么是新产品?
⒊比较不同类别的产品设计工作的工作特点和要求? ⒋什么是产品设计的\三化\工作,为什么要实行\三化\? ⒌说明工艺准备工作的主要内容? ⒍比较三种工艺规程的特点和适用场合? ⒎如何加快工艺准备工作的进度? ⒏如何合理安排生产技术准备计划?
⒐说明年度生产技术准备计划,产品生产技术准备计划和科室生产技术准备计划的不同任务及三者之间的联系?
第三章 生产预测 一、 要点
⒈预测的作用及预测期
预测的作用;预测的前提条件;预测的时间期。 ⒉预测的工作步骤 ⒊预测方法 二、基本要求
⒈了解预测的作用及必要的前提条件,了解不同预测期所要求的预测内容。 ⒉了解预测的工作步骤。 ⒊熟练掌握预测方法 第四章 生产计划 一、要点
⒈工业企业生产计划体系
生产计划在企业管理中的作用:长、中、短期计划的内容与特点。 ⒉年度生产计划的制定
生产计划大纲的计划指标体系;年度生产计划的制定步骤;滚动计划的特点与原理;总产量指标的测算方法--盈亏平衡分析;品种指标的测算方法--产品寿命周期法。 ⒊生产能力的计算与调节
生产能力的基本概念;生产能力的计算;生产能力的调节因素;学习曲线。 ⒋需求变动的生产计划方法 ⒌产品出产进度计划的编制
产品出产进度计划的编制原则;产品出产进度计划的编制方法。 二、基本要求
⒈了解工业企业计划体系 ⒉了解年度生产计划的制定
⒊掌握盈亏平衡分析确定总产量指标的方法 ⒋深刻理解生产能力的计算与调节 ⒌熟练掌握需求变动的生产计划方法 ⒍了解产品出产进度计划的编制 三、重点与难点
⒈年度生产计划的定量决策方法--盈亏平衡分析法
年度生产大纲的总产量指标主要应用盈亏平衡分析法确定,就是利用产品成本中不同部分相对于产品产量的变化关系(固定成本、可变成本),对某产量计划方案的盈(取得利润)、亏(发生亏损)情况进行分析。
产品产量与产品成本、利润之间的变化关系可表示为图所示的盈亏平衡分析图。 图中A为临界点。N*为盈亏平衡产量,当产量大于N*时,才有利润。 产量、成本和利润之间变化关系的数学表达式为: R=PN=(F+VN)+E
其中:P-V称毛益贡献,它的作用是在产量≤N*时补偿固定成本,在超过了N*后,即转化为利润。
利用表达式,就能对计划的产量测算可能取得的利润,或在给定的利润指标下,确定应达
到的产量;或在给定的利润与产量规模下确定目标可变成本等多种制定生产计划时所要研究决策的问题。
⒉生产能力的计算与调节 生产能力时指:
从这个定义可以得到以下两个重要的概念:
⑴生产能力主要由设备的数量与设备的生产效率所决定: 式中:FE--设备的制度工作时间; S --设备数量;
T --生产产品的台时定额。
⑵生产能力受到生产条件、产品类别、工作时间等多种因素的影响,因此它是变动的,但又能通过利用或控制它的影响因素来调节生产能力,使它适应生产任务的需要。 调节生产能力的因素分为长、中、短期三类。年度生产计划的制定主要利用利用中期因素,这包括变动劳力数量、变动工作时间(加班加点)、外包加工以及利用库存调节生产能力等措施。
⑶生产效率对生产能力的影响还表现在学习曲线的现象上。就是,随着产量的增加,在不增加设备和人员的情况下,生产能力仍按一定速率增长的一种规律。这种现象的数学表达式为: Y=Kx-b
式中:Y--生产第x台产品的直接人工工时或成本; K--第一台产品的直接人工工时或成本; b--反映学习率的指数。
因此,若知学习率,就利用上式测算出达到若干产量时的产品工时或成本,从而有助于较可靠地制定生产计划。 ⒊需求变动的生产计划方法
在计划年度内,产品需求呈现出季节形变动时,需调节生产能力使之适应需求变动。不过,利用任何调节生产能力的因素都要花费额外成本。因此,制定需求变动的生产计划所要解决的问题是:在给定的产品需求情况下,如何为各计划周期(季、月)配置满足需求的生产能力,而又能使调节生产能力所花费的成本总和最少。 适应产品需求变动的计划策略:
⑴跟踪策略 各期的计划产量完全随需求而变化。这种策略的主要措施是增减劳力数量、增加工作时间(加班加点)与利用外包加工。为此,会引起上述三方面的成本增加。 ⑵均匀策略 各期的计划产量保持不变。利用库存来补充或吸收生产能力以适应变动需求的需要,这种策略会引起较高的库存成本。
⑶混合策略 以上两种策略只利用了个别或一部分生产能力调节因素。往往造成较高的成本,将这两种策略结合起来运用,适当地调整各期产量水平又利用一定的库存调节作用来适应变动需求。混合策略可以预期取得总成本最低的效果。
有三种解决这类计划问题的方法:列表计算法、线性规划法和运输问题扩展法。三种方法的目标都是使调节能力的总成本最小。
列表计算法通过计算各方案的有关成本,并比较其结果从中选出总成本最小的方案作为最佳方案。方法简单,但只能从非常有限的几个方案中作出选择,因此不能达到最优。 线性规划法是将计划问题建立线性规划模型,然后寻找最优解。这种方法能考虑所有的资源约束条件,能保证达到最优解,但计算复杂,一般需借助计算机才能进行。
运输问题扩展法适用于各周期正常班产量水平不发生变化的情况,它能用手算求解,且亦能找到最优解。
区别计划工作的条件与资源情况,选用适当的计划方法。 四、典型例题
1、 某企业在计划期内,用本企业自备原材料生产的产品2000件,成品率90%,每件单价350元,外销95%,5%企业自用。用定货者来料生产的产品销售额5000元,其中,定货者来料价值3500元;外销半成品300件,单价150元,完成对外承作工业性作业价值3000元,其中,工业性作业原材料价值1500元;非工业性作业价值1800元,废品出售每件200元,计算商品产值。(646500元)
2、 已知某企业的生产成本及产品资料如表所示。 固定成本 50000元/年 单价可变成本 2元/台 生产能力 20000台/年 销售价格 7元/台
3、 设某厂目前产量为年产4000件产品,单位产品售价为175元。产品可以全部卖出。工厂的年固定成本为300000元,全部可变成本为360000元。据销售部门测算,若售价降
低10%,销量可以增加25%。但由于现有能力所限,增加产量后会增加单件可变成本10%(发生在增加的产量部分)并增加固定成本5%,试决定产量为多少有利?(4257─5000件)
4、 某企业计划的年销售收入2400万元、固定成本920万元、计划利润为280万元。试问该计划方案能否较可靠地保证利润目标?(安全边际率23.3%,一定能保证) 5、 有一个生产A产品的企业,年生产能力为10000台,固定成本300万元,本年度接到国内订货7000台,售价2000元/台,预计将亏损20万元,现有一外商愿以1800元/台订购3000台,试用盈亏分析法做出决策,是否接受此项订货?(V=1600元/台,利润40万元,故接受订货)
6、 某企业承接两台新型导航器的订货。第一台用4000工时,材料成本与设备使用成本为30000元。第二台用3200工时,材料与设备成本为21000元。人工成本为每小时18元。这以后原用户又订制20台,并要求为新制的20台导航器提出成本报价。问:①最后一台成本应达多少?(32708元)②这20台产品的平均生产工时是多少?(1912小时)③这20台产品的平均单台成本为多少?(44192元)
7、 某工厂要为下一年的1-6月制定总产量计划,根据以下资料,请拟定一份合理的产量计划。
① 产品需求情况如表所示。 1 2 3 4 5 6 期初库存 200
预测需求 500 600 650 800 500 600 ② 成本资料:
保管成本:10元/台月;缺货成本:20元/台月;正常班人工成本:12.5元/工时;加班人工成本:18。75元/工时;裁减成本:100元/人。 ③ 生产方面的资料:
人工工时:4工时/台;工作日数:22天/日;现有工人数:10人。
每个工人在一个月内加班生产的产品不超过11台,外包生产一台的成本为100元。每月不超过5台。(根据线性规划中运输问题的模型求解) 五、思考题
1、 多品种生产的企业,应如何计量总产量指标?
2、 比较三种产值的含义、作用和计算中使用的价值特点? 3、 什么是毛益贡献,它在盈亏平衡分析中起什么作用? 4、 说明中期计划的任务、特点和应做好的决策问题?
5、 不同生产类型企业,在安排产品出产进度计划上各有什么特点? 六、计算题
某企业计划生产A、B、C、D四种结构工艺相似的产品,单位产品在某设备上的总劳动量分别为20、40、50和60台时,该设备组共有56台设备,两班制生产,年制度工作254天,设备停修率为5%,若以B产品为代表产品,则该设备组的生产能力应为多少? 答案:
设备组生产能力= 56×254×2×8×(1-5%)/40 =5405(台)
第五章 生产作业计划 一、要点
1生产作业计划的概念 2大量流水生产的期量标准
节拍、标准计划、在制品占用量定额
3大量流水生产的生产作业计划的编制方法-在制品定额法 4批量生产的期量标准
批量、生产提前期、生产周期、在制品占用量定额
5批量生产的(厂级)生产作业计划的编制方法-累计编号法 6 批量生产的车间内部生产作业计划的编制。 7单件生产的期量标准 生产周期、总日历进度计划
8单件生产的(厂级)生产作业计划的编制方法-生产周期进度表法 9作业排序
作业排序的评价标准;作业排序的方法; 二、基本要求
1了解生产作业计划的概念
2 掌握各种生产类型的期量标准概念 3 了解各种生产类型的期量标准的确定方法 4 掌握在制品定额法、累计编号法。
5 掌握批量生产车间内部生产作业计划的编制方法
6 掌握作业排序的评价标准和单设备的排序方法、Johnson-Bellman法。 三、重点与难点
(一)生产作业计划的概念
生产作业计划是生产计划的具体执行计划,是企业组织日常生产活动的依据。它把全年的生产任务,在空间上具体落实到车间、工段、班组和工作地,在时间上具体分配到了月、旬、周、日以至轮班、小时。生产作业计划是根据生产计划,依照一定的期量标准来编制的。
这样就有多种形式的生产作业计划。如,车间月计划,车间周计划,班组周计划,班组日计划,班组轮班计划。 (二) 流水生产
流水生产是指劳动对象依照一定的工艺顺序和规定的速度,流水般地通过各工作地,进行连续生产的一种高效率的生产组织形式。
特点:工作地专业化程度高;整个工艺过程是封闭的;按照统一的节拍进行生产 组织流水生产需要具备一定的条件。 流水线的设计包括组织设计和技术设计。
流水线的技术设计是指工艺路线、工艺规程的制订、专用设备的设计、设备改装设计、专用工夹具设计、运输传送装置的设计以及信号装置的设计。
组织设计的准备工作包括:1)明确零件的分类;2)改进产品结构;3)审查与修改工艺规程4)收集整理流水线资料。 单一对象流水线的组织设计的步骤: 1 确定流水线的节拍
节拍:流水线上前后出产两个相同制品的时间间隔。 流水线节拍=计划期有效工作时间(分)/计划期产品产量
计划期产量=计划中规定任务+不可避免的废品;有效工作时间=制度工作时间*有效利用系数。
节奏:按批运输时,流水线上相邻两次运输的时间间隔 2 工序同期化
工序同期化就是采取技术组织措施使流水线上各工序的单件加工时间等于节拍或成为节拍的整数倍,以便提高工作地负荷和降低其超负荷。 机械加工流水线主要靠技术措施来实现。主要有: (1)设备。更新改造设备
(2)工艺装备。快速安装(减少装夹时间、换刀时间)
(3)改变加工方法,减少切削时间,提高切削用量,采用高效刃具,多件加工。 (4)改进工作地布置,减少辅助操作时间 (5)提高工人的熟练程度和工作效率 、操作方法 (6)建立在制品储备
阶位法是一种装配流水线平衡的方法。 3 确定最少工作地数
工作地数应越少越好。当然不会过小。
需要工作地(设备)数 =单件时间定额/流水线节拍
流水线的总负荷系数=单位产品总装配时间/(实际工作地数*节拍) 流水线的总负荷系数一般应在0.85---0.9。 4 配备工人
流水线配备工人时,要保证各工作地都能正常工作,还要考虑缺勤率(病、事假等),为流水线准备一部分后备工人 5 选择运输装置 6 流水线平面布置
流水线布置的形状,一般有直线形、直角形、S形、O形、U形和其他不规则形状等。 (三)大量流水生产的期量标准
期量标准是指在一定的生产技术及组织条件下对生产对象在生产期限和生产数量方面所规定的标准。它对于保证各生产环节之间的衔接配合,加强生产计划管理,合理利用人力、物力及财力资源,提高生产经济效益,具有积极作用。 1节拍
单一对象和多对象的流水线节拍的确定方法。
2标准计划。
标准计划主要是规定整个流水线的工作和中断时间及程序。
对于连续流水线,每个工作地的工作制度基本一致。所以规定的是整个流水线的工作制度。对于间断流水线,规定的是每一个工作地的工作时间程序。 流水线标准工作指示图表的编制步骤: (1).确定看管周期
规定一段时间(看管周期),各工序在该时间内生产数量相同。看管周期过大,在制品占用多。看管周期过小,无法使他们生产数量相同。一般取一个班,或1/2班,或1/4班的时间。
(2) 计算工作地的计划工作时间。即工作地在看管周期内的工作延续时间。 (3) 确定时间分配、起始时间点。
(4)计算工作地看管周期产量。即工作地在一个看管周期内应生产的制品的数量。 3 在制品占用量定额
在制品是指从原材料投入到成品入库为止,处于生产过程中尚未完工的所有毛坏、零部件、半成品及产品的总称。
在制品定额是在一定的技术组织条件下,为了保证生产正常进行必须保有的在制品数量标准。
它可分为流水线内在制品占用数量和流水线之间在制品占用数量。 (1)工艺占用量Z1
流水线内各工作地上正在加工、装配或检验的在制品数量。取决于:流水线内工序数目;每道工序的工作地数目;每个工作地同时加工的在制品数量。将流水线内所有工序的在制品数量汇总。减少工艺占用量,靠技术措施。 (2)周转占用量Z2
间断生产条件下的流水线上两个相邻工序之间,由于生产率不同,在工序之间存放的在制品数量。仅在间断流水线上。 数值呈周期性变化。它的计算按每相邻两道工序分别计算。通常将工序之间看管期初周转在制品占用量之和,作为流水线周转占用量定额。 (3)运输占用量Z3
流水线内各工序之间运输装置上被运送的在制品数量。
Z3一般对连续流水线。而在间断流水线上,若周转在制品能满足运输需要时,就不考虑
运输在制品占用量。 (4)保险占用量Z4
防备意外,而保证连续生产正常进行而储备。不因局部而影响整体。应针对原因,加强管理。Z4动用后,应让该工序及时补齐(利用非工作班时间或提高工作强度) (四)批量生产的期量标准 1批量和生产间隔期。
批量是同时投入生产并消耗一次准备结束时间所加工、装配同种产品的数量,生产间隔期是指相邻两批同种产品投入或出产的时间间隔。
正确选择批量和生产间隔期,对成批生产的经济效果有很大影响。
确定批量和生产间隔期的方法:先确定批量后计算生产间隔期的方法称为以量定期法。先确定生产间隔期再计算批量的方法叫以期定量法。 2生产周期
生产周期是指从原材料投入到成品出产所经过的整个生产过程的全部日历时间。生产提前期是指产品在各工艺阶段出产或投入的日期,比成品出产日期所提前的时间。它是以产品最后完工时间为起点,根据各工艺阶段的生产周期和保险期,反工艺过程的顺序进行计算的。 2生产提前期
生产提前期是指毛坯、零件或部件在各个工艺阶段出产或投入的日期比产品出产的日期应提前的时间长度。
生产提前期分为出产提前期和投入提前期。 某车间出产提前期=后续车间投入提前期+保险期 某车间投入提前期=该车间出产提前期+该车间生产周期 当不同的工艺阶段的批量不同时,需用下列公式: 某车间出产提前期=后续车间投入提前期+保险期 +(本车间生产间隔期-后车间生产间隔期) (五)单件小批生产的期量标准
1生产周期。只确定企业的主要产品和代表产品的生产周期,而其他产品可根据代表产品的生产周期加以比较。
确定方法:产品生产周期图表。主要考虑产品零件中的主要件和关键件在工艺上的逻辑关
系。
(六)生产作业计划的编制
生产作业计划分为厂级作业计划和车间内部生产作业计划。厂级作业计划是把全厂任务和出产进度具体落实到车间。车间内部生产作业计划则是把车间的生产任务和出产进度具体落实到工段、班组以至每个工人。他们的编制方法基本相同。其编制方法主要取决于车间生产组织形式和生产类型。 1在制品定额法
在大批大量生产条件下,车间之间生产上的联系,主要表现在数量上,而且大批大量生产的在制品占用量较稳定,故可用在制品定额法计算各车间的出产量和投入量。
在计算出各车间的投入与产出任务后,即可编制出每个车间的月度生产作业计划。各车间的月度计划作业计划确定后,还需要编制车间的日历进度计划,即按工作日分配生产任务。日计划投入量与出产量可用月度除以每月工作日数得到,但对于可变流水线,应考虑到不同制品的投入先后与分配给各个制品的工作日数。日历作业进度计划同时可以用于统计车间生产作业计划实际完成情况,为作业计划的控制提供信息和标准。 2 累计编号法
生产任务的计划单位:(1)以台份为计划单位。(2)成套零件为计划单位 (3)零件组为计划单位
在多品种成批轮番生产条件下,可从产品的完工日期推算出各工艺阶段需要投入和出产日期,以期的衔接达到量的衔接。累计编号法是将各种产品分别编号,每一成品及其对应的全部零部件都编为同一号码,并随着生产的进行,依次将号数累计,不同累计号的产品可以表明各车间出产或投入该产品的任务数量。
用累计编号法确定各车间的生产任务有以下特点:在确定装配车间的出产累计编号后,可同时计算各车间的任务,而不必按照反工艺顺序方向依次计算;由于生产任务用累计编号表示,无需计算在制品数量,也不必按计划期初实际完成情况修正计划。若上期没有完成计划,其拖欠部分自然结转到下一期计划的任务中,所以简化了计划编制工作。由于同一台产品的所有零件都属于一个累计编号,因而每个车间只要按照规定的累计编号生产,就能保证零件的成套出产。
3批量生产车间内部生产作业计划的编制方法 编制步骤如下:
1)准备编制计划所需资料 (1)零件的工艺路线 (2)工作中心资料 (3)外协件外购件资料
2)计算作业任务的工序进度日程 3)计算生产能力需求量
将同一时间段内所有生产任务对同一工作中心需求的加工汇总起来,就可得到这一段时间内生产任务对该工作中心的生产能力需求量。 4)调整工作中心负荷,使负荷和能力平衡
5) 制订正式的作业进度计划和工作中心生产能力需求计划 (七)作业排序
1生产作业排序的概念和分类。
将不同的工件安排在不同的设备上或同一设备上进行加工的顺序安排。
分类:按设备分,单台设备排序问题和多台设备排序问题。按工件情况分:静态排序问题和动态排序问题。按目标函数分:单目标排序问题和多目标排序问题。 2作业排序的评价标准
总流程时间最短;平均流程时间最短;最大误期最短;平均误期最短。 3作业排序的方法 1) 单设备排序
定理1 对于单设备排序问题,SPT规则使平均流程时间最小。 定理2对于单设备排序问题,EDD规则使最大误期最短。
定理3 对于单设备排序问题,若存在使最大误期为0的排序方案,则在交货期不小于考虑中的工件的作业时间之和的工件中,将作业时间最大的工件安排在最后位置,如此反复进行,可得到使平均流程时间最小的最优工件顺序。 2)Johnson-Bellman排序法
当几种零件在两台设备上加工,且工艺顺序相同,即为两台设备的流水型排序问题,可使用Johnson-Bellman排序法,确定出加工排序,使总流程时间最小。但这个定理无法具体确定这个流程时间的大小。确定这个流程时间的大小,可用甘特图。 四、例题
(一) 某部件A拟用流水线装配。它有11项作业元素。元素的先后顺序与时间如图。假定节拍为0.55小时。制订流水线设计方案。 答案: 1 计算阶位值
元素 作业时间 0 1 2 3 4 5 6 7 8 9 10 阶位值 0 0.32 1 + + + + + + 1.72 1 0.1 1 1 + + + + + + + 1.66 2 0.2 1 + + + + + 1.40 3 0.05 1 1 + + 0.87 4 0.1 1 + + 0.82 5 0.23 1 1 + + + 1.20 6 0.2 1 + + 0.92 7 0.05 1 + 0.45 8 0.32 1 + 0.72 9 0.1 1 0.40 10 0.3 0.39
例如,第0项元素的阶位值=该元素时间与其所有后续作业元素时间之和。 t1=0.32+0.2+0.23+0.2+0.05+0.32+0.1+0.3=1.72 2将作业元素按阶位值的大小排列,编出阶位表 元素 0 1 2 5 6 3 4 8 7 9 10 总计
阶位 1.72 1.65 1.4 1.2 0.92 0.87 0.82 0.45 0.72 0.40 0.3 作业时间 0.32 0.1 0.2 0.23 0.2 0.05 0.1 0.05 0..32 0.1 0.3 1.97 紧前工序 0和1 2 5 1 3 4和6 5 7和8 9 3 分配作业元素(给工作地)。依阶位的高低顺序
工作地 作业元素 阶位值 紧前作业 作业时间 累计 剩余时间 1 0 1.72 0.32 0.32 0.23
1 1.65 0.1 0.42 0.13 3 0.87 1 0.05 0.47 0.08 2 2 1.4 0和1 0.2 0.2 0.35 5 1.2 2 0.23 0.43 0.12 4 0.82 3 0.1 0.53 0.02 3 6 0.92 5 0.2 0.2 0.35 8 0.72 4和6 0.32 0.52 0.03 4 7 0.45 5 0.05 0.05 0.50 9 0.4 7和8 0.1 0.15 0.40 10 0.3 9 0.3 0.45 0.10 3 确定最少工作地数
最少工作地数为1.97/0.55=[3.6]=4
本例实际的工作地数为4,可以说方案是适当的。 4 流水线的总负荷系数一般应在0.85---0.9。 本例中,1.97/(4*0.55)=89.6%
也可以计算出各工作地的负荷系数。工作地1的负荷系数为0.47/0.55=85.5%
(二)某流水线上计划生产甲乙丙丁四种产品。其计划产量分别为3000、2500、2400、2200。每种产品在流水线上各工序单件作业时间之和分别为50、45、45、40min。流水线按两班制生产,每月有效工作时间为2400min。试计算每种产品的节拍。
解:(1)选择产品甲为代表产品,产量大,劳动量大,工艺过程复杂的,换算为代表产品的全部产品产量。
即N=3000+2500*45/50+2400*45/50+2200*40/50=9170 则代表产品甲的节拍为24000/9170=2.6min 乙的节拍为2.6*45/50=2.34min
丙的节拍为2.6*45/50=2.34min 丁的节拍为2.6*40/50=2.08min
(三)对于某批产品,装配车间的批量为40件,生产周期为30天。生产间隔期10天,机加工车间的批量为120件,生产周期为50天。生产间隔期30天,保险期为10天。毛
坯车间的批量为240件,生产周期为20天。生产间隔期60天,保险期为5天。试确定各车间的投入出产提前期。 解:计算如下:
装配车间投入提前期=30+5=35天
机加车间出产提前期= 35+10+(30-10)=65天 机加车间投入提前期=60+50=115天
毛坯车间出产提前期= 115+5+(60-30)=150天 机加车间投入提前期=150+20=170天
(四)依据制品定额法,在表中空白处填写合适的数据。 表 各车间某月份投入量和出产量计算表 产品数量(台) 10000 零件编号 01-33 01-34 每台件数 1 4 装配车间 出产量 废品 0 0
在制品占用量定额 1000 5000 期初预计在制品数 600 3500 投入量 10400 41500 零件库 外销量 0 2000 占用量定额 800 6000 期初预计占用量 1000 7100 加工车间 出产量 10200 42400 废品 100 1400
在制品占用量定额 1800 4500 期初预计在制品数 600 3400 投入量 11500 44900
(五)假设工厂要加工A、B、C三种零件。A零件批量为400件;它的工序10、工序30在工作中心1上进行;其中在工序10中调整时间为1小时,单件加工时间为0.25小时;
工序30的调整时间为1小时,单件加工时间为0.4小时。B零件批量为1300件;B零件只有工序10且在工作中心1上进行,其调整时间为6小时,单件加工时间为0.2小时。C零件批量为800件;它只有工序30在工作中心1上进行,其调整时间为1小时,单件加工时间为0.125小时。假定正常情况下工作中心1的第10周的有效能力为350台时。那么,假设第10周安排加工中心1完成A零件的工序10加工任务和B零件;第11周安排加工中心1 完成A零件的工序30加工任务和C零件。 试问:工作中心1的生产能力能否满足第10周的任务要求?
答:工作中心1的第10周的任务为(1+400*0.25)+(6+0.2*1300)=367小时 ;其大于工作中心1的第10周的有效能力为350台时。 所以不能完成任务。
(六)已知5个工件的单机作业资料如表所示。
工件号 J1 J2 J3 J4 J5 作业时间 3 7 1 5 4 交货期 23 20 8 6 14 依SPT规则加工顺序 工件排序 J3 J1 J5 J4 J2 作业时间 1 3 4 5 7 交货期 8 23 14 6 20 开始时间 0 2 5 9 14 结束时间 1 4 8 13 20 延迟 -7 -19 -6 7 0 误期 0 0 0 7 0
依据SPT规则排序,其平均流程时间最短。 本例平均流程时间为(1+4+8+13+20)/5=9.2 最大误期为:MAX(0,0,0,7,0)=7 工件号 J4 J3 J5 J2 J1 作业时间 5 1 4 7 3
交货期 6 8 14 20 23 开始时间 0 6 7 11 18 结束时间 5 6 10 17 20 延迟 -1 -2 -4 -3 -3 误期 0 0 0 0 0
排序的最大误期为MAX(0,0,0,0,0)=0 但平均流程时间为: (5+6+10+17+20)/5=11.6
(七)5个工件在两台设备的流水型排序问题资料如表。试用Johnson-Bellman法排序。并计算最短流程时间。 工件 J1 J2 J3 J4 J5 工序1 12 4 5 15 10 工序2 22 5 3 16 8 解:计算步骤:
1从未排序的工件中找出作业时间最小的工件
2如果属于前工序,往前排(但放在已前排的后面);如果属于后工序,往后排(但放在已后排的前面)。 3将已排序的工件删去。 4 重复进行,直至排序结束。 排序结果为:J2-J1-J4-J5-J3 最短流程时间为34。 五思考题
1 在制品定额法适用于什么类型企业的生产作业计划编制? 2 累计编号法的优点是什么? 3 合理的批量,其经济意义有哪些? 4 如何降低各种在制品占用量? 5 研究作业排序的作用? 第六章 生产过程控制 一、要点
1生产作业控制的内容
生产作业控制是对产品生产的数量和进度的控制,主要包括生产调度、生产作业核算和在制品管理等内容。
2 生产调度的内容、原则、工作制度与方法
生产调度工作的内容主要包括:控制生产进度和在制品流转;督促有关部门做好生产准备和生产服务;检查生产过程中的物资供应;督促设备的运转;合理调配劳动力;调整厂内运输;组织厂部和车间的生产调度会议;做好生产完成情况的检查、记录、统计分析工作。 生产调度在保证全面地、均衡地完成生产作业计划的前提下应遵循以下原则:1、计划性。2、统一性。3、预见性。4、及时性。5.群众性。
调度工作制度与方法包括:1.调度值班制度。2、调度会议。3、调度报告制度。 调度工作中常用的工具有:工票、加工路线单、调度板等。 3 生产统计的概念与内容以及统计方法 二、基本要求
1 深刻理解生产作业控制的内容 2 理解调度工作的原则 3 了解调度工作的制度
4 了解调度工作中常用工具的适用场合 5 深刻理解生产统计的内容与统计方法 三、重点与难点
(一)生产作业控制的具体内容:
1.检查生产作业准备工作的进行情况,督促和协助有关部门作好工作。
2.检查生产作业计划的执行情况,掌握生产动态,了解实际生产进度与计划之间的偏差,根据偏差产生的原因,采取相应的措施。 3.根据生产需要,合理调配劳动力。
4.检查与调整厂内运输工作,使厂内运输通畅。 (二)生产调度的原则
生产调度在保证全面地、均衡地完成生产作业计划的前提下应遵循以下原则:
1、计划性。保证生产作业计划规定的任务和进度。对实际与计划的偏差,采取措施予以克服,必要时对原计划进行调整和补充。调度人员应积极向计划人员反映情况
2、统一性。各级调度部门根据生产作业计划和上级指示行使调度权力,下一级生产单位和同级的有关职能部门必须坚决执行。保证统一指挥,既干好现有计划又干好追加计划。 3、预见性。积极采取措施预防或缩小生产作业计划中可能发生的偏差和障碍造成的影响。尽量消灭在萌芽。勤检查,勤分析,果断和敢于负责。注意准备工作,关键件生产,配套工作,防止抓前忘抓后。
4、及时性。生产调度部门对生产中出现的有关问题及时采取措施解决,避免造成损失。 5.群众性。善于倾听群众意见,依靠职工的积极性。向群众讲明任务的意义和变化的原因。了解第一手资料。动员群众自觉克服和防止生产脱节。从群众那里取得办法。 (三)、生产调度系统
厂级调度机构:总调度室(值班调度) 厂级调度员分工方式:
1.按车间分工。避免多头指挥,但对工艺专业化车间不易掌握产品进度。 2.按产品分工。当车间生产多个产品时,容易命令冲突。 3.两者兼有。但以某一个为主。 (四)调度工作制度与方法。
1.调度值班制度:连续系统掌握生产情况,及时处理临时问题。
值班调度员工作:按班(小时)检查产品的出产情况,检查调度决议和重点任务的执行情况,
记录和发出生产指标,并检查其执行情况。及时处理临时问题,并详细记录调度日记、交接班。
2、调度会议:发扬民主、集思广益、统一指挥是调度的工作方法。
厂级调度会议:厂级一般每周一次,不同于日常的碰头会,专题会议,应相互结合。先总结上次的决议执行情况,再提出本次要解决的主要关键问题,主要讨论横向协调,会前有调查准备,会完有记录、决议。无法解决的交厂生产会议。会后有检查。
车间调度会议:内容一般是上旬抓短线件,中旬抓成套。下旬抓出产成品以及下旬准备。 工段的班前班后会:布置、总结。 现场调度会
3、调度报告制度:让领导掌握产品进度、生产情况及存在问题和采取措施。一般逐级报告,调度员口头或书面向上级调度部门报告。调度部门一般以生产日报形式报厂级领导。
(五)生产作业统计的概念与要求、内容
生产作业统计:对产品生产过程中的材料投入、工件移动、劳动成果和产品出产所作的记录整理和分析工作。反映生产(成品、在制品)资源利用情况,以便发现不足和问题,有助于调度,有助于计划。
要求:要根据实际分析应正确。准确及时记录分析整理能力,而且应该内容合理。全面反映生产的全面情况,反映企业的全面情况。
条件:专职统计员,设计好原始凭证(数出一源,凭证适量)有合适的原始凭证。依靠群众填好原始凭证,改进信息。
内容:生产进度(投入日期、投入数量、出产的以及废品数、返修品数)库存在制品(在制品、半成品以及资金占用量)的生产作业完成情况(产品零部件完工统计,各单位各个人完成任务统计)。
(六)调度常用的工具和统计的原始凭证
原始凭证:用数字或文字对生产活动进行最初的直接记录的单卡或票据。既考虑管理有考虑方便。凭证要有种类、记录内容、表格形式、份数及传递路线。
1、加工路线单。按零件设置,适用于成批生产的机加工车间,毛坯库送毛坯领毛坯时,毛坯收料员第一副券交返毛坯库,以便在仓库作为凭证,并在发料台帐上登记。第二副券交车间调度以便安排投产计划,登记投产台帐以及作为车间凭证。然后计划员填写投料日期,投入数量等,开始前,由调度填好工序、工时等内容。或临时计算机打印也有直接印刷好的。送检入库,成品第一副券交返毛坯库,拒以登记台帐,车间统计员以第二副券作为原始凭证并登记入台帐。加工路线单正联返回计划调度组以便和计划对比。
可见,加工路线单是一单多用。(既是计划,又是统计)写上工序有利于工艺纪律的执行。原始数据唯一,有助于生产控制。
2、单工序工票,简称工票。一序一票,适用于批量大的零件加工。零件名、单件定额、加工时间、完成数量、合格、回用、返修、工废、料废。
3、工作班任务报告。按工段进行作业统计。一班能完成多种作业任务。
以上三种既作调度文件,又作统计文件,厂根据实际情况确定原始记录。其余原始凭证有领料单、废品通知单、停工单、个人生产记录、入库单、返修通知单、产量报告表、仓库里有盈亏单、报废单。
生产过程原始记录包括的方面:产品生产方面、劳动力、劳动时间利用情况、原材料、动
力消耗、设备利用和安全方面。
原材料统计的内容主要有:领用、结存、消耗情况。
劳动统计的内容主要有:劳动力的数量、出勤率工时利用率及劳动效率。 设备统计的内容主要有:设备数量、设备利用情况及设备事故和维修情况。 统计工作是在原始记录的基础上进行整理和汇总,建立统计台帐和填报统计报表。 统计台帐有汇总性的(按某一特征)、积累性(按时间顺序)两类。便于工作,便于查找、保存,在原始记录和台帐基础上,企业要按期填报生产报表,有内部报表,部门间传递信息,如物资处向生产部报的月底库存明细,以及对外报表(向部门或国家报送) (七)生产进度的统计
包括产品投入、出产进度及工序进度。比较可比较数量,也可比较时间,如比较某一时刻数量上的差异,当数量单件小批时,比较时间上的差异。形式图表直观。大量生产检查产品出产进度的比较是计划累计与实际累计数量差值。单件生产中检查产品各工艺阶段投入和出产进度比较的是时间。
在成批生产和单件小批中,有时还要控制其工序生产进度以保生产。建立工序进度统计卡。格式如14-3、14-4。工序进度统计卡由统计人员根据加工路线单、工票、入库单等原始凭证逐日填写。
(八)库存在制品统计。
主要是指毛坯库中的零件库中已经加工完毕的零件。包括内容:在制品数量统计和成套性的检查。
1、库存在制品的数量统计:编制生产计划时要用这个数值。
零件统计台帐由库管员根据完工入库单领用单过加工路线单副券等原始记录填写。为了保证在制品数量统计的准确性,要做好一系列管理工作:
(1)、建立健全在制品出入库制度和手续,由于工人进入库房,注意单据和实物对照,防止多拿、及时入帐。错拿小零件也要有计量有凭证。
(2)、加强保管,防止丢失和损坏。先进先出,防潮防晒,密封等。 (3)、运输认真,防止碰伤零件。
(4)、定期清点盘存:以便能及时发现问题找到原因。成批生产中,采用累计编号法计算生产任务,如果生产报废、废件回用等在制品变化,都要求从发生单位起,反工艺顺序修改各台帐中累计数。
2在制品成套性检查
检查零件,根据投入装配的日期与批量、生产作业计划规定的零件投入加工日期和数量。检查后,发现短缺品种和数量,应填写缺件表,提交有关部门,让其根据原因采取相应措施。成批及单件生产中,成套性检查极为重要。在成批生产中,检查时,用零件的库存累计数来衡量。如书上的例子。大量生产中,只要每天按计划生产就能保证配套,即只要按出产量生产。因此,搞好出产统计即可。 (九)生产作业核算
生产作业核算是生产作业控制的重要内容。它是记录和核算生产作业计划的完成情况,如产品、零部件的投入量、出产量,工序进度,在制品占用量等。它的主要作用是为生产调度工作反馈生产信息,对于计划进度与实际进展之间的偏差,在生产调度中迅速地予以解决。
生产作业核算的基本方法是把有关生产活动记录在原始凭证上,根据一定的目的,把原始记录汇总起来记到有关台帐上。把实际发生数和计划数进行比较,通过各种图表显示出来,使生产管理人员和工人一目了然,了解生产进度的具体情况。 (十)生产统计核算指标 生产统计核算指标包括:
1、产量指标的统计:考核不是绝对数,用相对数。 产量计划完成率= *100% Q实-考核期的实际产量
2、品种指标的统计,完成的品种数保证成套性保证合同执行。
第一种方法:品种计划完成率= *100% 式中:P表示完成计划产量的品种数。
第二种方法:LP= *100% Q实I取值不大于Q计。P表示实现生产的品种数。P计表示零件品种数。
3、成套性指标的统计:(按统计时段计算)
为了促使车间按规定的品种生产足够的数量,以保证最终产品按时出产。 成套率= = B实-实际成套数。 B计-计划台份
P实-完成计划产量的零件品种数 P套-成套零件组的零件品种数 4、生产均衡性指标的统计: 均衡率法 LJ= *100%
进度对比法:用各时间阶段的产量与总体时间的产量进行对比。考虑较概略,常用于单件
生产和成批生产的企业或实行均衡生产的初期。理想的均衡性是三三四。 不同的方法肯定得到不同的结论,因此要注意统计口径。 以上指标对不同的生产类型,选的内容不一样。 四、计算题
已知:某厂计划期生产5种零件各100台,实际月产量(台)为95、100、107、108和100,该种零件按产量计算的零件品种计划完成率为多少?(答案:99% ) 五、思考题
1 生产调度的作用?
2 生产作业控制和生产作业计划的关系? 3 生产统计核算指标的重要性?
第七章 生产绩效控制 一、要点
1 成本控制的意义 2 成本控制的内容
3 基于作业的成本控制与传统成本计算的区别 4 目标成本的确定方法 5 生产率控制的作用 6 生产率的影响因素 7 如何提高生产率 二、基本要求
1 深刻理解成本控制的意义 2 了解成本控制的内容
3 理解基于作业的成本控制与传统成本计算的主要区别 4了解目标成本的确定方法 5理解生产率控制的作用 6 深刻理解生产率的影响因素 7 掌握提高生产率的方法 三、重点与难点
1成本控制的意义
降低成本是企业产品具有竞争能力的保证;是企业利润的源泉;有助于提高管理能力;是节约社会资源的基础。
2 基于作业的成本控制与传统成本计算的主要区别
基于作业的成本控制在计算产品成本时,将着眼点从传统的注意产品转移到作业上,以作业为核算对象,首先根据作业对资源的消耗情况,将资源的成本分配到作业,再由作业成本追踪到产品成本的形成和积累过程,最终得出产品成本。 3 目标成本的确定方法
根据目标利润确定目标成本;根据竞争对手的先进成本水平确定目标成本;根据本产品历史成本水平确定; 4 生产率控制的作用
生产率控制能促进生产系统的改善和发展;是评价生产者工作的一个综合依据。 5 生产率的影响因素
人力资源;技术水平;管理水平。 6 提高生产率的方法
从人力资源方面,可以采取改进工作设计、教育和培训、加强工时定额管理和奖惩制度、建立良好的工作环境。
从技术水平方面,可以采取先进的设计手段、自动化程度高的生产技术、先进的营销工具等。
从管理水平方面,可以改善管理体制、改善管理手段和工具等。 四、思考题
1 生产成本的高低对产品销售的影响? 2 降低产品成本的途径?
3 工作设计和物质激励的区别与联系? 4 如何提高生产率水平?
5 生产率控制和成本控制的区别与联系?
第八章 设备管理 一、要点
⒈\\的含义及分类、特点
主要是指企业生产所需要的除土地和建筑物以外的有形固定资产。工业企业的设备是用以直接开采自然财富或把自然财富加工成为社会必需品的固定资产。它是直接将投入的劳动对象加以处理,使之转化为预期产品的机器和设施以及维持这些机器和设施正常运行的附属装置,即生产设备和辅助设备。 设备的分类:5类 (注意分类标准) 设备的特点:高速化 连续化 自动化 电子化 多能化 精密化 两极化
⒉设备管理的概念、任务、发展阶段
设备管理是指根据企业的生产经营目标,通过一系列的技术、经济和组织措施,对设备寿命周期内的所有设备的物质运动形态和价值运动形态进行的综合管理工作。
设备管理的任务是为企业的生产提供最良好的技术装备,使企业的生产建立在技术上先进、经济上合理的物质技术基础之上。
设备管理的发展大致经历了事后维修、预防维修、设备综合管理三个阶段。 ⒊设备的初期管理(选择、评价、安装、调试) 选择设备应考虑的因素 设备的经济评价 设备的维护与维修理论 设备的检查与修理 ⒋设备的改造与更新 设备的改造的定义与特点 设备的更新的类型与方法 二、基本要求
⒈理解设备管理的定义及其在制造企业中的地位和作用。 ⒉理解设备选择应该考虑的因素及设备经济评价的方法。 ⒊深刻理解设备故障规律的浴盆曲线。 ⒋深刻理解设备的修理定额。
⒌了解设备改造和更新的问题。 6.理解设备的磨损规律 7.设备的折旧及有效利用率 三、重点与难点 ⒈设备管理的概念
⑴ 设备管理是指根据企业的生产经营目标,通过一系列的技术、经济和组织措施,对设备寿命周期内的所有设备的物质运动形态和价值运动形态进行的综合管理工作。 设备寿命周期概念指的是设备从规划、购置、安装、调试、使用、维修直至改造、更新及报废的全过程所经历的全部时间。 ⒉设备的选择与评价
⑴ 设备的选择是设备管理的第一环节。其目的是为生产选择最优的技术装备。因此,选择和评价设备应遵循技术上先进、经济上合理、生产上适用的基本原则。 选择设备应考虑的因素: 设备的使用寿命和购置费 设备的环境保护性 设备的可靠性和安全性 设备使用与维修的方便性 设备的生产效率
设备对产品(工程)质量的保证程度
⑵影响设备选择的因素之间是相互联系、相互影响的。往往难以面面俱全。因此,除考虑上述因素外,还应着重进行经济效益分析,考察它在经济上是否合理,以经济效益为基本点对设备进行综合评价。为企业选择最佳的设备。 设备经济评价的方法: 费用效益法
设备综合效益分析法 投资回收期法 3.设备的安装与调试
⑴设备购置或自制完成后,即进入安装与调试阶段,需要按照设备工艺平面布置图及有关技术要求,将外购或自制的设备安装在基础上,进行找平、灌浆稳固,使设备安装精度达
到安装规范的要求,并经调整、试运转、验收后移交生产。
可能有人认为设备的安装与调试工作是技术部门的事情,与管理无关,实际上这是不全面的。应该认识到,设备的安装与调式亦是设备前期管理工作的重要内容,组织好坏与否,直接影响设备能否交付使用。
在组织设备的安装工作时,应考虑下列因素: 安装应与生产组织的要求相符合,并满足工艺要求 方便工件的存放、运输和切屑的清理 满足空间的要求
设备安装、维修及操作安全方面的要求 动力供应和劳动保护的要求
设备的调试工作包括清洗、检查、调整和试运转。当设备安装就位后,应由设备的使用部门组织 设备管理部门与工艺技术部门协同进行设备的调试工作。 4.设备的磨损与磨损规律 ⑴设备磨损的分类: 有形磨损 第一型有形磨损 第二型有形磨损 无形磨损 第一型无形磨损 第二型无形磨损 ⑵设备的磨损规律: Ⅰ Ⅱ Ⅲ
⑶设备的故障规律的浴盆曲线 5.设备的修理 ⑴设备的点检
所谓\点检制\是指按照一定的规范或标准,通过直观或检测工具,对影响设备正常运行的一些关键部位的外观、状态与精度进行制度化、规范化的检测。 ⑵设备的修理定额
修理周期、修理周期结构和修理间隔期 设备修理停歇时间定额 修理劳动量定额 修理复杂系数 ⑶设备修理的原则
贯彻专群结合群管群修的原则 贯彻先维修、后生产的原则
贯彻以预防为主,维、修并重的原则 6.设备的改造与更新
⑴设备技术改造的特点及范围 针对性强 经济性好 适应性强 ⑵设备的更新
设备的更新是对在技术上或经济上不宜继续使用的设备,用较先进和较经济的新设备更换。是消除设备的有形磨损和无形磨损的重要手段。 ⑶设备的更新的方法分类 四、例题
⒈简述设备故障规律的浴盆曲线? (答案:参见课本148页) ⒉什么是无维修设计? (答案:参见课本155页)
⒊设备的修理周期、修理周期结构和修理间隔期的区别? (答案:参见课本152页) 4.设备有形磨损和无形磨损的区别? (答案:参见课本146页) 五、思考题
⒈设备与固定资产的区别?
⒉设备管理与其它管理的共同点与不同点? ⒊设备的选择时要考虑的因素? ⒋设备点检的定义?
⒌设备的维修的原则?
⒍设备的有形磨损与无形磨损得区别? ⒎设备磨损规律?
⒏设备的安装工作应考虑的因素有哪些? 六、计算题
⒈某设备从投入使用到运行5000小时为止,据统计共发生5次故障,其故障检修时间为150小时,设其故障率λ为常数(这里的故障率是指单位时间内发生故障的概率),求其有效利用率?
⒉某机械厂有一台普通机床,其原值与使用期间的重置价值均为8000元,按照折旧率0.45%进行折旧.每年机床生产的零件为5000只,工厂每年生产零件为5000只,工厂的工时成本按照每个工时3元计算。
问:当机床使用8年以后,需要一次大修理.设备修理后大修周期缩短为7年,生产率保持不变,每年的维修费用平均比上一修理周期的年维修费用增加100元.第一次大修预算费用是4500元.如果该机床不修理转让给其它单位可以得到4000元.试分析该机床第一次大修理的经济性?
⒊某台设备经过8000小时的观察,共发生故障10次,由于故障造成的停机时间(包括检修时间)为200小时,求该台设备的有效利用率(假设故障率为常数)?
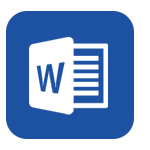





正在阅读:
生产管理学教案04-18
全市科级领导干部党风廉政教育大会主持词01-17
我眼中的女生作文550字06-25
自体脂肪隆胸是应用注射的方式05-26
TCPIP协议电子科技大学-A2卷09-12
马哲论文01-05
相亲大会主持词02-23
- 多层物业服务方案
- (审判实务)习惯法与少数民族地区民间纠纷解决问题(孙 潋)
- 人教版新课标六年级下册语文全册教案
- 词语打卡
- photoshop实习报告
- 钢结构设计原理综合测试2
- 2014年期末练习题
- 高中数学中的逆向思维解题方法探讨
- 名师原创 全国通用2014-2015学年高二寒假作业 政治(一)Word版
- 北航《建筑结构检测鉴定与加固》在线作业三
- XX县卫生监督所工程建设项目可行性研究报告
- 小学四年级观察作文经典评语
- 浅谈110KV变电站电气一次设计-程泉焱(1)
- 安全员考试题库
- 国家电网公司变电运维管理规定(试行)
- 义务教育课程标准稿征求意见提纲
- 教学秘书面试技巧
- 钢结构工程施工组织设计
- 水利工程概论论文
- 09届九年级数学第四次模拟试卷
- 管理学
- 教案
- 生产
- 项目一围手术期护理(1)
- 紫微斗数入门基本格局
- 育才中学物理一模选择题答案
- 建筑地基基础工程施工质量验收规范
- 新闻学概论(李良荣)-(考研)超全版笔记
- 提升机电控通用要求
- 社会学概论思考题
- XX县国税局传达贯彻县委政法委工作会议精神情况汇报
- 长方体和正方体体积容积练习题
- 报价承诺法招标文件范本(2014) - 图文
- 江苏省张家港市2013-2014学年第二学期期末调研测试初一数学试卷
- 网络信息对抗试题
- 《管理学原理》作业与练习
- 苏教版二年级数学第一单元100以内的加法和减法(三)
- 世界经济概论教案 - 图文
- 最新冀教版2018-2019学年小学数学六年级上册《已知圆的直径求面
- Linux学习练习命令
- 2014学年浦东新区教育局第四教育署幼儿园招生地段 - 图文
- 学校管理工作存在的问题及整改方案
- 石油化工企业可燃气体和有毒气体检测报警设计规范(GB50493-2009)