TJJW 012-2014 HXD3B型电力机车总体技术规范(报批稿)
更新时间:2024-04-19 04:32:01 阅读量: 综合文库 文档下载
- 天津教委推荐度:
- 相关推荐
TJ/JW012—2014
HXD3B型电力机车总体技术规范
TJ/JW012—2014
目 次
前言................................................................................................................................................ II 1 范围 ............................................................................................................................................ 1 2 规范性引用文件 ........................................................................................................................ 1 3 用途及应用环境 ........................................................................................................................ 3 4 基本技术要求 ............................................................................................................................ 3 5 电气部分技术要求 .................................................................................................................... 7 6 机械部分技术要求 .................................................................................................................. 22 7 制动及供风系统技术要求 ...................................................................................................... 29 8 司机室技术要求 ...................................................................................................................... 37 9 其他技术要求 .......................................................................................................................... 39 10 检验要求 ................................................................................................................................ 41 11 RAMS要求 ............................................................................................................................... 41
I
TJ/JW012—2014
前 言
本标准性技术文件参照GB/T 1.1—2009给出的规则起草。 本标准性技术文件由中国铁路总公司提出并归口。
本标准性技术文件由中国北车集团大连机车车辆有限公司负责起草。
本标准性技术文件主要起草人:代兴军、李群锋、杨守君、高洪光、臧玉军、慕元鹏。
II
TJ/JW012—2014
HXD3B型电力机车总体技术规范
1 范围
本文件规定了HXD3B型电力机车(以下简称为机车)的用途及应用环境、基本技术要求、电气部分技术要求、机械部分技术要求、制动及供风系统技术要求、司机室技术要求、其他技术要求、检验要求、RAMS要求等要求。
本文件适用于轨距1435 mm,单相交流25 kV/50 Hz的新造HXD3B型电力机车。 2 规范性引用文件
下列文件对于本文件的应用是必不可少的。凡是注日期的引用文件,仅注日期的版本适用于本文件。凡是不注日期的引用文件,其最新版本(包括所有的修改单)适用于本文件。
GB 146.1—1983 标准轨距铁路机车车辆限界 GB/T 700—2006 碳素结构钢
GB/T 1591—2008 低合金高强度结构钢
GB/T 3323—2005 金属熔化焊焊接接头射线照相(EN 1435:1997,MOD) GB 5068—1999 铁路机车、车辆车轴用钢 GB/T 5118—1995 低合金钢焊条
GB/T 5599—1985 铁道车辆动力学性能评定和试验鉴定规范 GB 5914.1—2000 机车司机室了望条件
GB 5914.2—2000 机车司机室前窗、侧窗及其他窗的配置 GB/T 6417.1—2005 金属溶化焊接头缺欠分类及说明 GB/T 6417.2—2005 金属压力焊接关缺欠分类及说明
GB 6770—2000 机车司机室特殊安全规则(idt UIC 617-5 OR:1977) GB 6771—2000 电力机车防火和消防措施的规程
GB/T 11345—1989 钢焊缝手工超声波探伤方法和控伤结果分级 GB/T 25333—2010 内燃、电力机车标记 TB/T 304—2011 机车用总风缸技术条件 TB/T 449—2003 机车车辆车轮轮缘踏面外形 TB/T 1463 机车轮对组装技术条件
TB/T 1979—2003 铁道车辆用耐大气腐蚀钢订货技术条件 TB/T 2011—1987 机车司机室照明测量方法 TB/T 2072—1989 50钢车轴技术条件
TB/T 2325.1—2006 机车、动车组前照灯、辅助照明灯和标志灯技术条件 第1部分:前照灯
TB/T 2325.2—2006 机车、动车组前照灯、辅助照明灯和标志灯技术条件 第2部分:辅助照明灯和标志灯
TB/T 2360—1993 铁道机车动力学性能试验鉴定方法及评定标准 TB/T 2368—2005 动力转向架构架强度试验方法 TB/T 2393—2001 铁路机车车辆用面漆 TB/T 2541—2010 机车车体静强度试验规范
TB/T 2879—1998(所有部分) 铁路机车车辆 涂料及涂装 TB/T 2942—1999 铁路用铸钢件采购与验收技术条件 TB/T 3044—2002 13号车钩基本尺寸和性能 TB/T 3046—2002 15号车钩基本尺寸和性能
TB/T 3051.1—2013 机车、动车用电笛、风笛 第1部分:电笛 TB/T 3051.2—2013 机车、动车用电笛、风笛 第2部分:风笛 TB/T 3138—2006 机车车辆阻燃材料技术条件 TB/T 3254—2011 机动、动车用撒砂装置
TJ/JW 001—2011 机车车载安全防护系统(6A系统)总体暂行技术条件
1
TJ/JW012—2014
TJ/JW 001-A~G—2012 机车车载安全防护系统(6A系统)中央处理平台及六个子系统暂行技术条件
ISO 1940:2003 机械振动恒态刚性转子平衡品质要求(Mechanical vibration. Balance quality requirements for rotors in a constant (rigid) state Specification and verification of balance tolerances)
ISO 3095:2005 铁路设施 声学 有轨车辆发出的噪音的测量(Railway applications—acoustics—Measurement of noise emitted by railbound vehicles)
ISO 3381:2005 铁路设施 声学 有轨车辆车内的噪声(Railway applications— Acoustics—Measurement of noise inside railbound vehicles)
ISO 8573-1:2010 压缩空气 第1部分 杂质和质量等级(Compressed air—Part1: Contaminants and purity classes)
IEC 60296:2012 电工用液体 变压器和开关设备用的未使用过的矿物绝缘油
(Specification for unused mineral insulating oils for transformers and switchgear)
IEC 60300-3-3 可靠性管理 第3-3部分:应用指南 生命周期成本 (Dependability management—Part 3-3: Application guide—Life cycle costing )
IEC 60310:2004 铁路应用 铁路机车用牵引变压器和电感器(Railway application—Traction transformers and inductors on board rolling stock)
IEC 60349-2:2002 铁路机车车辆和公路车辆用旋转电机 第2部分:电子变流器供电的交流电动机(Electric traction—Rotating—Part 2:Electronic converter-fed alternating current mortors)
IEC 60571:2012 铁路机车车辆电子装置(Electronic equipment used on rail vehicles)
IEC 61287-1:2005 铁路应用 安装在铁路机车上的电力变流器 第1部分:特性和试验方法(Railway applications— Power convertors installed on board rolling stock—Part 1:Characteristics and test methods)
DIN EN 10084:2008 渗碳钢 技术交货条件(Case hardening steels—Technical delivery conditions)
EN 1563:2005 铸造 球墨铸铁(Founding—Spheroidal graphit cast irons)
EN 13104 铁路应用 轮对和转向架 动轴 设计方法(Railway applications - Wheelsets and bogies - Powered axles - Design method)EN 14420-7:2007 带夹头的软管配件 第7部分:凸轮锁紧接头(Hose fittings with clamp units—Part 7:Cam locking couplings)
EN 50121-1:2008 铁路设施 电磁兼容 第1部分:总则(Railway applications— Electromagnetic compatibility—Part1:General)
EN 50121-2:2008 铁路设施 电磁兼容 第2部分:整个铁路系统对外界的辐射Railway applications—Electromagnetic compatibility—Part 2:Emissions of the whole railway system to the outside world )
EN 50121-3-1:2008 铁路设施 电磁兼容 第3-1部分:机车车辆火车和设备完整的车辆(Railway applications—Electromagnetic compatibility—Part 3-1:Rolling stock—Train and complete vehicle )
EN 50121-3-2:2008 铁路设施 电磁兼容 第3-2部分:机车车辆装置(Railway applications—Electromagnetic compatibility—Part 3-2:Rolling stock—Apparatus)
EN 50126:1999 铁路设施可靠性、可用性、可维修性和安全性的规范和论证(Railway applications—The specification and demonstration of Reliability, Availability, Maintainability and Safety (RAMS) )
EN 55015:2006 电子照明和类似设备的无线电干扰特性测量方法和限值(Limits and methods of measurement of radio disturbance characteristics of electrical lighting and similar equipment)
UIC 564-2 国际载客轨道车辆防火和消防规范(Coaches windows made from safety glass)
UIC 651:2002 机车、动车、动车组和驾驶拖车的司机室设计(Layout of driver's cabs
2
TJ/JW012—2014
in locomotives, railcars, multiple-unit trains and driving trailers)
UIC 617-6:1977 机车动车司机室布置规则(Regulations governing the layout of drivers cabs of locomotives)
UIC 812-3:1984 非合金钢整体车轮技术规范(Technical specification for the supply of solid wheels in rolled non-alloy steel for tractive and trailing stock) 3 用途及应用环境 3.1 用途
铁路干线牵引货运列车。 3.2 环境温度
环境温度(遮荫处)为-40 ℃ ~+40 ℃。
机车基础结构按照-40 ℃运用环境设计,并预留加强防寒设备安装接口和布线空间。机车能在-40 ℃环境下存放,加强防寒后能够在-40 ℃环境下正常运用,但是在运用前需要预热。
机车蓄电池充电器、微机控制系统、主辅变流器及其控制单元、升弓系统部件、空气制动系统等在满足-25 ℃~+40 ℃环境下正常运用的前提下,可通过应用加强防寒和预热(可以采用蓄电池供电和接触网供电两种方式)的可选配置方案使机车达到-40 ℃~-25 ℃环境下正常运用的要求。 3.3 海拔
海拔不超过2500 m。 在海拔高于1200 m、环境温度接近+40 ℃且连续在最大功率状态下运行时允许出现功率限制。 3.4 湿度
月平均最大相对湿度95%(该月月平均最低温度不低于25 ℃)。 3.5 其他
能适应风、沙、雨、雪、盐雾、粉尘、偶有雾霾的侵袭。
4 基本技术要求
4.1 电流制式
单相25 kV,50 Hz,网压波动范围17.5 kV~31 kV。 4.2 机车功率发挥基本要求
机车功率发挥不低于图1所示的曲线。在22.5 kV~29 kV网压下,功率为9600 kW; 在19 kV网压下,功率为8064 kW;在网压低于19 kV直到17.5 kV时,牵引功率线性降为0,但辅助功率仍然有效。网压高于29 kV直到31 kV时,牵引功率线性地降为0。
3
TJ/JW012—2014
图1 机车功率发挥曲线
4.3 轨距
机车轨距为1435 mm。 4.4 轴式
机车轴式为Co - Co。 4.5 机车重量及要求
4.5.1 机车整备重量为150 t,允差为-3%~1%。 4.5.2 机车轴重为25 t。 4.5.3 同一机车,每根动轴的实际轴重与该机车实际平均轴重之差,不大于该机车实际平均轴重的±2%。
4.5.4 各个车轮轮重与该轴平均轮重之差不超过该轴平均轮重的±4%。 4.5.5 整车左右两侧轮重差之代数和不超过机车总重的±1%。 4.6 尺寸限界
机车在受电弓完全降弓状态时,在平直道上,其外界尺寸符合GB 146.1—1983的电力机车限界要求,具体尺寸如下:
? 车钩中心线距轨面高度(新轮)为880 mm±10 mm;
? 受电弓降弓状态时滑板距轨面高度(新轮)为不大于4622 mm; ? 受电弓降下时机车最高处距轨面工作高度为5200 mm~6500 mm; ? 齿轮箱最低点距轨面高度不小于(新轮)为120 mm;
?10? 车排障器距轨面高度(在踏面允许磨耗范围内可调)为1100 mm;
?
转向架扫石器距轨面高度(在踏面允许磨耗范围内可调)为30 mm。
4.7 主要技术参数 4.7.1 机车主要尺寸
符合下列要求 :
? 机车前后车钩中心距为22781 mm; ? 机车车体宽度为2950 mm;
? 机车最大宽度(车体外附属设备处于工作状态)为3270 mm; ? 机车车顶距轨面高度为4250 mm;
? 机车转向架中心距为12950 mm; ? 机车转向架固定轴距为231950 mm。 4.7.2 机车速度
符合下列要求:
? 机车最高运营速度为120 km/h; ? 恒功区最低速度为68.2 km/h; ? 机车最高试验速度为132 km/h。
4
TJ/JW012—2014
4.7.3 机车轮周牵引功率
机车轮周牵引功率(持续制,车轮半磨耗)为9600 kW。 4.7.4 机车再生制动轮周功率
机车再生制动轮周功率(持续制,车轮半磨耗)为9600 kW。 4.7.5 牵引特性
牵引曲线见图2,制动曲线见图3。
600500400牵引力(kN)30020010000102030405060708090100110120130速度(km/h) 图2 牵引曲线 600500电制动力 (kN)40030020010000102030405060708090100110120130速度 (km/h) 图3 制动曲线 ? ? ? ?
起动牵引力为570 kN;
恒功率速度范围(轴功率1600 kW)为68.2 km/h~120 km/h; 最大再生制动力(车钩处)为最大480 kN;
速度低于5 km/h时,再生制动力线性下降至0。
4.7.6 机车功率因数
当接触网电压不高于27.5 kV、机车功率大于10%额定功率时,机车功率因数(λ)不小于
5
TJ/JW012—2014 0.98。
4.7.7 等效干扰电流和谐波含量
机车在持续工况下,距离牵引变电所10 km处测量,接触网每公里0.83 Ω,65°22'。 4.7.7.1 机车正常工作时等效干扰电流:
? 等效干扰电流不大于0.8 A; ? 谐波含量不大于0.4%。
4.7.7.2 一台电机被切除时等效干扰电流:
? 等效干扰电流不大于2.6 A; ? 谐波含量不大于1.5%。
4.7.7.3 一台变流器被切除时等效干扰电流:
? 等效干扰电流不大于2.5 A; ? 谐波含量不大于1.3%。 4.7.8 机车传动型式
机车采用“交-直-交”电传动型式,电源侧采用四象限斩波型变流器,电机侧采用变压变频式逆变器向三相交流异步牵引电机供电。每个电机由各自的逆变器供电(轴控)。 4.7.9 机车总效率
机车设备的重量、容量、成本将进行经济的优化设计,机车总效率值将会变化,最大可达到0.88。这个参数依赖于不同的工作条件,如原边电压、实际功率和速度。最佳值在额定点70 km/h附近,原边电压范围为25 kV~28 kV。 4.7.10 动力学性能
4.7.10.1 机车动力学性能试验最高试验速度为132 km/h。
4.7.10.2 线路最小曲线半径为300 m±20 m,试验线路和试验测量条件的其它要求按TB/T 2360—1993执行。
4.7.10.3 机车在整个试验速度范围内是稳定的,机车的横向失稳采用构架上的横向加速度
2
进行评判,条件为滤波 0.5 Hz~10 Hz下连续出现6次以上的横向加速度值不超过10 m/s。 4.7.10.4 机车安全性指标包括脱轨系数、轮重减载率等,其中脱轨系数不大于0.9;轮轴横向力等按TB/T 2360—1993评定,轮重减载率按GB/T 5599—1985评定。
4.7.10.5 机车舒适度指标包括车体垂向和横向振动加速度、垂向和横向平稳性指标,舒适度指标按TB/T 2360—1993中合格指标评定。
4.7.10.6 机车起动状态下轴重转移不大于±10%。
4.7.10.7 机车具有轴重转移的电气补偿功能(电机转矩不超过电机启动转矩限值)。
4.7.10.8 机车能以5 km/h速度安全通过半径为125 m的曲线;并能在半径为250 m的曲线上进行正常摘挂作业。 4.7.11 机车重联控制
机车能够由TCN/WTB列车控制总线来实现3台机车的重联控制。在本务机车上能够显示重联机车的状态。
机车预留安装远程控制系统(LOCOTROL)的安装位置和布线空间。 机车制动机应具备重联功能,并可与各型制动系统兼容。 4.7.12 机车过分相控制
机车装有自动通过分相区的设备。 4.7.13 机车电源
机车具有采用外接电源的功能。 4.8 防火及安全
4.8.1 机车的设计有良好的防火性能,以便最大限度地防止火灾发生。机车的设计、制造及
6
TJ/JW012—2014
所选用的材料、部件的防火要求符合GB 6771—2000。 4.8.2 机车安装车载安全防护系统(6A系统),包含中央处理平台(含音、视频终端)和空气制动安全监测、防火监控、高压绝缘检测、列车供电监测、走行部故障监测、自动视频监控及记录六个子系统。总体技术条件符合TJ/JW 001的要求。平台及子系统符合TJ/JW 001A~D、F、G的要求。
4.8.3 机车上采用非延燃性材料和防火材料,不允许使用燃烧后产生毒气的材料。 4.8.4 机车所使用无卤低烟阻燃的电线和电缆。
4.8.5 高压电气设备具有人身安全防护措施和警示标识。
4.8.6 机车配有灭火器,每个司机室采用两个MSWZC3型手提式水雾灭火器。 4.9 外部噪声要求
测量采用的标准为ISO 3095:2005和ISO 3381:2005。所有的外部测量在距轨道中心7.5 m处进行。
4.9.1 机车应采取措施来降低机车附近的噪音等级至最低。
4.9.2 机车符合TSI噪声要求,按照ISO 3095:2005要求进行测量。 4.9.3 无论静止还是运行,外部噪音都没有任何听得见的异常的刺耳声。 4.9.4 当通过曲率小到只有80 m水平路轨曲线时,噪音辐射减至最小。 4.9.5 当机车静止时,尽可能的自动降低噪音设备的影响。 4.10 风笛和电笛
4.10.1 机车每端安装电笛和高低音风笛,并可单独控制。
4.10.2 机车电笛和风笛均分别符合TB/T 3051.1—2009、TB/T 3051.2—2009的规定。 4.11 其他
机车具有地面电源移车功能。
5 电气部分技术要求
5.1 综述
5.1.1 机车主电路采用由IGBT模块组成的四象限变流器和逆变器对牵引、再生制动实行连续控制。主电路原理框图见图4。
7
TJ/JW012—2014
25kV受电弓车顶避雷器受电弓隔离开关主断路器车内避雷器牵引电机1 变流器 1牵引电机2滤波柜主变压器牵引电机3变流器 2牵引电机4牵引电机5变流器 3牵引电机6 图4 主电路原理框图
5.1.2 机车辅助电源为三相交流460 V/60 Hz,采用由IGBT元件组成的辅助变流机组。机车控制电源为直流110 V。
机车主电路、辅助电路、控制电路在各种工况下均有完善而可靠的短路、过载、接地、过电压、欠压、过热、空转、滑行以及通风、油流系统的故障保护装置,并在司机室微机显示屏上显示故障内容及有关故障处理提示。
5.1.3 机车上保护装置和变流机组的变流元件能承受从故障发生时起到其保护装置起作用时止,这段时间内短路电流的冲击。
5.1.4 当机车局部发生故障时,可自动或在司机室内方便地手动切除有关电路,维持运行。 5.1.5 机车具有智能化诊断功能,能对主电路、辅助电路、控制系统以及空气制动系统的故障进行诊断和安全导向。在重联状态下,故障信息通过TCN-WTB由受控机车传送到主控司机室。
5.1.6 机车保证只有当主断路器断开,受电弓已降弓以及接地开关处于接地位置才能接近高压区域。
5.1.7 机车设有联锁控制系统,其作用为:当高压间的门打开或者可接近高压设备时防止升起受电弓或闭合主断路器。 5.2 电磁兼容
5.2.1 机车电磁兼容满足EN 50121-1:2008、EN 50121-2:2008、EN 50121-3-1:2008的要求。
机车保证不会干扰铁路沿线的通信、信号等设备的正常工作。
机车车载电子设备和电气设备满足EN 50121-3-2:2008的要求,避免相互干扰。 5.2.2 车载信号设备满足EN 50121-3-2:2008的要求,不受由机车设备产生的任何磁场的影响。
8
TJ/JW012—2014
5.2.3 机车的所有部件不受任何干扰地发挥其功能,符合IEC 60571:2012的要求。 5.3 高压电器 5.3.1 受电弓
每台机车装有两架相同的单臂受电弓,具备弓网故障自动降弓保护装置及快速分断主断路器的保护功能,受电弓升降弓时对接触网和车顶不能造成有害冲击。机车采用单弓受流运行,当运行的受电弓故障时,可通过受电弓隔离开关切除,用另一架受电弓维持运行。
受电弓主要技术参数如下: ? 额定电压为25 kV;
? 正常工作电压范围为17.5 kV ~31 kV; ? 额定电流为1000 A; ? 最大速度为200 km/h;
? 静态接触压力(调整量±5 N)为70 N;
? ? ? ? ? ? ? ?
100最大升弓高度(带绝缘子)为3081??25 mm;
工作高度(包括绝缘子)为969 mm~2881 mm; 弓头长度为1950 mm;
滑板有效长度为1250 mm; 滑板类型为碳滑板;
工作空气压力为4 bar~10 bar; 升弓时间不大于5.4 s或6 s~10 s; 降弓时间不大于4 s。
5.3.2 主断路器
机车主断路器采用真空主断路器,主断路器的分断容量和动作时间在所有条件下提供相关设备的保护,带有动作次数计数器。
主要技术参数如下: ? 额定电压为25 kV;
? 正常工作电压范围为17.5 kV~31 kV; ? 额定电流为1000 A; ? 最大分断电流为20 kA; ? 辅助触点数为7个;
? 20℃时固有分闸时间 25 ms~60 ms; ? 工作压力为4.5 bar~10 bar。 5.3.3 高压电压互感器
主要参数为:
? 输入电压为25 kV/50 Hz;
? 正常工作电压范围为17.5 kV ~31 kV; ? 输出电压为200 V; ? 容量为3315 VA; ? 精度等级为0.5;
? 次边额定电流为0.05 A。 5.3.4 高压电流传感器
主要参数为:
? 原边名义电流为1000 A;
? 正常工作电压范围为17.5 kV ~31 kV ? 原边电流测量范围为0~±1600 A; ? 次边名义电流为0.2 A; ? 精度等级为0.5;
9
TJ/JW012—2014
?
重量为1.5 kg。
5.3.5 接地侧电流传感器
主要参数为:
? 原边名义电流为1000 A;
? 正常工作电压范围为17.5 kV ~31 kV ? 原边电流测量范围为0~±2000 A; ? 次边名义电流为0.2 A; ? 精度等级为0.4; ? 重量为1.5 kg。 5.3.6 车顶避雷器
主要参数为:
? 持续运行电压为31.5 kV; ? 标称电流为10 kA; ? 外套材料为硅橡胶。 5.3.7 高压柜内避雷器
主要参数为:
? 持续运行电压为34 kV; ? 放电电流为10 kA; ? 外套材料为硅橡胶。 5.3.8 受电弓隔离开关
主要参数为:
? 标称电压为25 kV; ? 额定电流为530 A;
? 短时耐受电流为16 kA,1 s; ? 重量为45 kg。 5.3.9 接地开关和联锁钥匙箱
机车安装一个手动操作的接地开关实现高压联锁保护。 机车所有高压设备可以通过操作接地开关进行接地,并且在操作时与主断路器机械联锁。 接地开关和联锁钥匙箱具有以下功能:
? 接地开关能对网侧及原边电路进行接地; ? 当接地开关从“开”位转到“合”位之前,保证受电弓已经降下,受电弓供风中断,
并且受电弓供风管路中的风压已经排出;
? 当接地开关处于“合”位时,受电弓供风管路被中断,受电弓不能升起,主断路器
不能闭合;
? 机车高压电器柜有可靠的安全装置,并与联锁钥匙箱和接地开关有联锁; ? 只有当接地开关处于“接地”位时,才可能打开高压电器柜;
? 当高压电器柜打开时,接地开关在“接地”位,受电弓不能升起,主断路器不能闭
合;
? 只有当高压电器柜关闭,才有可能断开接地开关,升起受电弓。 5.3.10 车顶绝缘子(含受电弓支持绝缘子)
高度不低于400 mm,爬电距离不小于1000 mm,芯棒与伞裙之间采用分子联结。 车顶高压电器的绝缘水平不低于车顶绝缘子的水平。 5.4 主变压器(含谐振电抗器) 5.4.1 综述
10
TJ/JW012—2014
主变压器是由1个原边绕组、6个次边牵引绕组构成的单相变压器。主变压器和谐振电抗器安装在钢制主变压器油箱内,冷却方式为油循环、强迫风冷。主变压器具有温度、油流、压力等保护,安装温度传感器、油流继电器、压力释放阀、布赫继电器等设备。主变压器有可靠的油循环、油温及油干燥等保护装置。
机车主变压器和电抗器应满足IEC 60310:2004的要求。 5.4.2 主变压器和谐振电抗器
主要技术参数如下: a) 原边绕组:
? 额定容量为11622 kVA; ? 额定电压为25 kV/50 Hz; ? 额定电流为464.9 A。 b) 牵引绕组:
? 额定容量为1937 kVA; ? 额定电压为1500 V; ? 额定电流为1291.3 A; ? 短路电压为48.12%±10%; ? 标称功率时的损耗为319 kW。 c) 谐振电抗器:
? 数量为3;
? 电感值为0.55 mH; ? 额定电流为1040 A; ? 最大电流为1470 A; ? 频率为100 Hz;
? 标称功率时的损耗为5.2 kW。
d) 其他参数:
? 变压器的绝缘等级为A级, 电抗器的绝缘等级为H级;
? 冷却油类型为适合低温的矿物油,符合IEC 60296:2012标准;
3
? 冷却油流量为144 m/h; ? 冷却油入口温度为85 ℃; ? 冷却油出口温度不大于90 ℃; ? 额定效率不小于96%;
? 变压器重量(包括谐振电抗器)为13800 kg,其中油量为2300 kg; ? 变压器尺寸为2900 mm32634 mm31400 mm; ? 安装方式为车体下部悬挂。 5.4.3 变压器保护 5.4.3.1 变压器油温检测
系统设有3个PT100温度传感器,分别检测2路主变压器油路循环支路的出口油温和油箱顶层油温。
主变压器的温度保护和牵引变流器控制共同实现,油温高于90 ℃时,牵引变流器开始线性降低功率,油温为100 ℃时降为额定功率的70%。当油温超过100 ℃时牵引变流器封锁,当油温超过105 ℃时,停止输出功率,当油温超过105 ℃时系统自动分断主断路器。油温高于90 ℃降功运行后,直至油温低于88 ℃时,牵引变流器重新恢复额定功率运行。 5.4.3.2 变压器油流检测
主变压器两路油路循环支路各设有一个油流继电器来监测油是正确地循环进入变压器,具体情况如下:
如果一个油流继电器检测到无油循环,则功率下降40%; 如果两路油路循环装置和检测到无油循环,机车将被隔离。
11
TJ/JW012—2014 5.4.3.3 压力保护
主变压器装有安全压力释放阀。当变压器内部压力达到95 kPa±15 kPa时,压力释放阀动作,释放压力,机车分主断,并在显示屏上显示故障信息。
主变压器安装有用于箱体内部过热和闪络等故障产生的气体检测的2级的布赫继电器。第一级在司机显示器上产生报警,第二级跳主断路器。 主要技术参数:
? 一级保护:当气体体积达到250 ml~300 ml报警; ? 二级保护:气体流速达到1 m/s跳主断。 5.4.4 电抗器结构
电抗器采用油对流冷却。由空心盘式绕组制成。 5.4.5 主变压器用材料
主变压器是采用层式绕组形式,每柱线圈是由三个牵引绕组及其相应的原边绕组部分组成。使用常用的DIN套管。
主变压器用到的材料如下: ? 纸板为T4;
? 钢(箱体)为Q345E; ? 油为Diala BX。 5.5 牵引电传动系统
牵引设备由带有6个独立二次绕组、3个谐振电抗器、采用油冷却的主变压器和三组采用现代模块化、已验证的IGBT技术、采用水冷方式的电压型变流器组成。主变压器的两个二次绕组向一个变流器供电,一个变流器给两个牵引电机和一个辅助电路供电。6个牵引电机分别由独立的VVVF逆变器供电。 5.5.1 牵引变流器 5.5.1.1 综述
牵引变流器输入端(网侧变流器)与主变压器的次边牵引绕组相连,并可通过接触器分离。通过四象限变流器将单相交流电压转变为稳定的中间直流电压。中间直流回路设有支撑电容、2次谐振电容、接地检测模块和保护模块等。对于牵引,中间电压经过PWM逆变器转换成三相频率和电压可变的输出电压独立地供给三相异步牵引电机。对于辅助电源,中间电压经过一个PWM逆变器转换成三相频率和电压可变的输出电压,PWM逆变器通过滤波器-变压器系统提供辅助电源。
牵引变流器由以下几个功能模块组成: ? 模块1,包括 一个四象限整流器、过电压保护、 一个中间支撑电容、辅助逆变器的
一相、门驱动装置、电流传感器;
? 模块2,包括一个四象限整流器、辅助逆变器的两相、一个中间支撑电容、门驱动
装置、电流传感器;
? 模块3,包括两个电机逆变器、一个中间支撑电容、门驱动装置、电流传感器; ? 主要结构,包括开关、导线和母排、带管路和水泵的冷却回路、带DCU的控制箱中
间支撑电容、谐振滤波电容器、接地故障检测、中间环节传感器。 5.5.1.2 牵引变流器
主要技术参数:
? 每台机车使用数量为3个;
? 额定输入电压为1500 V/ 50 Hz; ? 额定输入电流为231300 A rms; ? 额定输入频率为50 Hz; ? 中间电压为DC 2800 V;
12
TJ/JW012—2014
? ? ? ? ? ? ? ?
最高运用中间电压为DC 2900 V; 额定输出电压为3AC 0~2183 V; 额定输出电流为550 A rms; 最大输出电流为660 A rms; 效率不小于98%;
控制电压为DC 110 V;
外形尺寸为2300 mm31050 mm32020 mm (L3W3H); 质量为2050(1±4%) kg。
5.5.1.3 牵引变流器功率模块
组成与参数:
a) TC3300型牵引变流器由一个主构架构成,另外,还包括本身的柜子构架、内部风扇、
水泵、管、母线、电缆。主构架包括5个主要隔断空间: ? 开关区:左下侧,主要连线和开关区域;
? 模块区:中间和右下侧,此区是用来安装和连接CM-M功率模块; ? 控制区:左侧和中上部,装有DCU控制板的卡槽; ? 中间回路传感器区:右上部,装有中间电压传感器;
? 柜后区:变流器柜的后半区域,装有一部分中间电容和全部的谐振 电容器。 b) 四象限变流器功率模块技术参数:
? 额定输入电压为AC 1500 V; ? 额定输出电压为DC 2800 V; ? 额定电流为1300 A; ? 最大电流为1450 A; ? 质量为180 kg ?5 kg;
? 外形尺寸为366.6 mm3695.2 mm31054.5 mm (L3W3H); ? IGBT元件参数为4.5 kV/900 A; ? IGBT元件开关频率为350 Hz; ? IGBT门极驱动消耗功率为5 W;
? IGBT门极驱动单元原、次边绝缘电压为6700 V; ? 车上更换时间不大于60 min。
c) 中间电压保护功率模块技术参数(包含在第一变流器模块内):
? 标称电压为2800 V; ? 最大电流为1066 A;
? IGBT元件参数为4.5 kV/900 A; ? IGBT门极驱动消耗功率为5 W;
? IGBT门极驱动单元原、次边绝缘电压为6700 V; ? 车上更换随模块一起更换。 5.5.1.4 谐振电容器
主要技术参数:
? 电容值为4.5 mF(331.2 mF+0.7531.2 mF); ? 额定电压为2800 V;
? 最高可重复电压(可持续时间)为3800 V/50 ms/h; ? 额定电流为215 A;
? 最大可重复电流为160 kA ; ? 质量为60 kg;
? 外形尺寸为175 mm3370 mm3800 mm (L3W3H)。 5.5.1.5 支撑电容器
主要技术参数:
? 全部电容值为13.2 mF;
13
TJ/JW012—2014
? ? ? ? ? ? ? ?
每个模块上电容值为332 mF;
构架电容安装区电容值为23231.2 mF; 额定电压为2800 V;
最高可重复电压(可持续时间)为3000 V 50 ms/h; 额定电流为290 A (2mF)/23100 A(231.2mF);
最大可重复电流为小于300 kA peak (2mF)/小于170 kA peak (231.2 mF); 质量为小于50 kg (2 mF)/小于60 kg (231.2 mF);
外形尺寸为175 mm (2 mF的为135 mm )3370 mm3800 mm (L3W3H)。
5.5.1.6 牵引变流器冷却方式
冷却方式为强迫水循环冷却(有添加剂)。主要要求: ? 水和添加剂的体积比例为47:53; ? 添加剂成份为乙二醇;
? 模块入口水温不高于59℃; ? 模块出口水温不高于63℃;
? 每个模块额定水流量为100 L/min; ? 冷却方式满足环保要求。 5.5.1.7 牵引变流器保护
变流器的保护分为5级保护,1~5级发生机率逐渐减少,但影响逐渐增加。规定如下: ? 1级保护:对于开关动作错误的保护; ? 2级保护:对热过载的保护;
? 3级保护:对中间电路过压的保护; ? 4级保护:对电气损坏的预保护; ? 5级保护:对电气损害的即时保护。 5.5.1.8 牵引变流器试验
牵引变流器试验符合IEC 61287-1:2005规定。牵引变流器首次装车前,应随牵引电机进行地面联调试验,试验按照IEC 61377-3执行。 5.5.2 牵引电机 5.5.2.1 综述
牵引电机为三相鼠笼式异步电机。
该电机须根据电压型PWM逆变器供电的特点进行特殊设计,以保证在PWM逆变器的整个输出电压、频率范围内电机的脉动转矩、损耗和噪声均满足铁路牵引运用要求。
牵引电机的设计主要目的之一是使用最少数量的元件,减少用户的维修时间并提高电机的可靠性。
同一种类电机间的所有部件,包括转子、端罩、轴承等具有互换性。
牵引电机是4极、三相、鼠笼式结构、强迫风冷、单轴承式异步电机,专为适应逆变器供电而进行特殊设计,减少了脉动转矩、损耗和噪声水平。
电机能承受由于机车运行时所产生的振动和冲击,以及由于电气突然短路时产生的短路转矩。
电机在规定的条件下(满载、最小满载电网电压、轮径变化范围内、最高环境温度)下正常运行。
在电机机座上设有防落安全托。
电机采用强迫通风冷却。电机的允许温升符合IEC 60349-2:2002的相关规定。
所有电机,在其外形尺寸、安装尺寸和电气性能方面,均满足完全互换。所有维修期间需更换的零部件,也完全互换。
电机非驱动端有一个滚动轴承,利用油脂润滑。在非驱动侧端盖处设有注油口,允许补加润滑脂。轴承密封通过非接触的迷宫式油脂密封完成。在A(驱动)端电机带有薄膜联轴节。
14
TJ/JW012—2014
电机采取措施防止电机轴电流 (绝缘轴承)。 电机采用抱轴悬挂。
电机的设计、制造和试验符合IEC 60349-2:2002的规定。 5.5.2.2 牵引电机特性
电机特性满足IEC 60349-2:2002和机车牵引和制动特性的要求。
电机所有特性计算及电阻的参考温度为150℃,且在特性曲线中标明该温度。
特性曲线包括在整个机车运行范围内电机转矩、定子频率、定子电压、定子电流、功率、功率因数、效率、转差率等与电机转速(机车速度)之间的关系。除效率外,各参数为基波值。对于效率,不仅需提供基波损耗与电机转速之间的关系,而且须提供考虑谐波损耗之后的效率与电机转速之间的关系。 5.5.2.3 牵引电机主要技术参数
以下为车轮半磨耗情况下的数值: ? 额定功率为1632 kW; ? 额定电压为2183 V; ? 额定电流为498 A; ? 额定频率为50 Hz; ? 额定转矩为10434 Nm; ? 额定转速为1494 r/m;
? 恒功率转速范围为1483 r/m~3065 r/m; ? 起动转矩为11745 N2m; ? 最大起动电流为555 A; ? 最高转速为2627 r/m;
? 超速试验转速(2 min)(IEC 60349-2:2002) 为3640 r/m; ? 极数为4;
? 工作频率范围为0~103.4 Hz; ? 控制方法为矢量控制; ? 绝缘等级为200级;
? 额定效率(持续点)为95%; ? 重量为2300 kg;
? 冷却方式为强迫风冷;
? 冷却通风量为1.8 m3/min。 5.5.2.4 安装方式
驱动装置半悬挂,驱动单元通过两个抱轴承(轴悬)支撑在车轴上,在电机端通过吊杆连接到转向架上。
5.5.2.5 电机结构、材料和制造要求
具体要求: a) 定子:
? 定子机座定子机座以叠片形式构成,由两个铸钢压板压在一起。两个压板通过
钢套焊接构成机座,机座结构紧凑并有足够的抗扭刚度。
? 定子叠片是由绝缘的高渗透导电钢片组成。叠片铁心两端由端盖固定。 ? 定子绕组的匝间绝缘符合IEC 60349-2:2002标准,绝缘等级为200级。定子绕
组在真空状态下进行绝缘处理(Veridur?)。
? 定子绕组由成形线圈构成。线圈在定子的A端连接,所有连接部分使用铜焊。 b) 转子:
? 转子为短路鼠笼式设计。叠片由两个压环连接在一起,收缩至电机轴。 ? 鼠笼设计成用铜焊接的结构形式。
收缩环消除了鼠笼的离心负荷。
15
TJ/JW012—2014
? 转子动平衡的平衡量要求达到ISO 1940:2003的G1.0或更高的要求。 c) 在没有负荷周期信息的情况下,轴承的最大寿命L10可保证150万公里。要保证200
万公里的轴承寿命,必需根据明确的负荷周期进行计算。油脂在运行150万公里或6年后更换,以先到者为限。驱动端轴承是齿轮的一部分,不属于电机。轴承加油、更换周期:
? 轴承加油周期为25万公里; ? 轴承更换周期为150万公里。 d) 速度传感器技术参数:
? 霍尔元件传感器为非接触式 ; ? DC 15 V(DCU供电); ? 2通道90°转换; ? 数字信号; ? 单极; ? 方波;
? -40℃~+120℃;
? 测速齿轮((EN-GJS-400-18-LT)装在电机轴上,模数为1; ? 最少每转300脉冲。
e) 电机温度保护:电机带有2个PT100(双重传感器)传感器,安装在定子上。这些传
感器由DCU监测,能够连续测量定子的温升。
f) 设计上不使用分离的接线盒。电机导线和定子绕组间采用铜焊连接。 g) 铭牌和标示:
? 电机上带有铭牌,铭牌符合IEC 60349-2:2002的规定。铭牌位置便于电机装车
后观察和检查。
? 电机有接地螺栓和接地标志。
? 所有的加油说明、更换间隔和润滑脂型号在维护说明书中描述。
? 铭牌和所有标志上的数据清晰和不易磨灭,且在整个使用期间内能正确辩认。 5.5.2.6 牵引电机试验
电机按照IEC 60349-2:2002的要求进行试验。型式试验时影响电机通风、发热的部件安装到位,例如齿轮箱等。试验电源是实际装车的变流器。
牵引电机首次装车前,应随牵引电传动系统进行地面联调试验,试验按照IEC 61377-3执行。
5.5.2.7 牵引电机及其部件从外形尺寸到电气性能有良好的互换性,所有电机的特性允差符合IEC 60349-2:2002的相关要求。 5.6 辅助系统
采用三相交流460 V/60 Hz供电制式。 5.6.1 辅助电源
辅助电源采用最新的IGBT逆变技术。 辅助变流器采用最新的IGBT元件。与两个牵引逆变器一起连接到中间直流回路。三个牵引变流器的中每一个都含有一个三相辅助逆变器,每个辅助逆变器向自己的变压器和滤波电路供电。变压器将中间回路的2800 V与辅助回路的460 V相隔离。
滤波器对逆变器的输出进行滤波,保证在所有条件下输出电源的畸变率小于10%。 系统能够提供三路的辅助电源,电源从115 V/15 Hz 到460 V/60 Hz,在一路故障时,提供完全的冗余保证。在过分相时或其它短时正常操作断电时,辅助系统由牵引电机的再生能量供电。
辅助电源技术参数如下: ? 输入电压为DC 2800 V;
? 输出电压谐波含量(滤波后)为不大于10%。 5.6.1.1 辅助电源1-2 输出(变频变压逆变器):
16
TJ/JW012—2014
? ? ?
输出电压(可变)为115 V~460 V; 输出频率(可变)为15 Hz~60 Hz;
辅助逆变器1、2可以在15 Hz~60 Hz(0 Hz起动)的范围内工作,在机车运行时,辅助变流器最低工作频率是15 Hz;
? 辅助逆变器最大输出容量(短时)为250 kVA; ? 辅助逆变器1、2额定容量为180 kVA。 5.6.1.2 辅助电源3输出(恒频恒压逆变器):
? 输出电压为460 V; ? 输出频率为60 Hz;
? 辅助逆变器最大输出容量(短时)为250 kVA; ? 辅助逆变器3额定容量为180 kVA。 5.6.1.3 辅助变流器元件模块技术参数:
? 标称输入电压为2800 V;
? 标称输出电压为1130 Vrms,相间; ? 标称电流为84.4 A; ? 最大电流为200 A;
? IGBT元件参数为4.5 kV/600 A; ? IGBT元件开关频率大于1000 Hz; ? IGBT门极驱动消耗功率为5 W;
? IGBT门极驱动单元原次、边绝缘电压为6700 V; ? 车上更换时间不大于60 min(整个CM-M模块); ? 使用温度范围为-40℃~+50℃(短时70℃)。 5.6.1.4 机车辅助电源系统采用冗余设计,当一组电源故障时,其余电源能维持全车辅助系统供电,而不降低辅助系统的定额值。 5.6.1.5 系统须有足够的过载能力,在短时间内能承受住负载起动电流的冲击;并在负载突变条件下,瞬间输出电压变化尽量小,不得影响所有负载电机电器的正常工作。 5.6.1.6 输出的交流电压为近似正弦波,最大变化率1000 V/ms。 5.6.1.7 内设自动监测装置,具有自诊断和故障记录功能,并能在司机室显示屏上显示系统运行状态及故障情况,便于故障分析和维修。
5.6.1.8 辅助电源系统具有完备的保护,至少包括过电压、欠电压、过载、接地、过热等保护项目。
5.6.1.9 辅助变压器:
? 绝缘等级为H级; ? 重量为600 kg;
? 外形尺寸为875 mm3347 mm3697mm (L3W3H); ? 冷却方式为强迫风冷; ? 绕组形式为DY5n; ? 变比为2.42:1;
? 额定输入电压为1130 V rms; ? 最高输入电压为3500 V峰值; ? 额定输出电压为460 V; ? 额定输入电流为84.4 A; ? 额定输出电流为282 A; ? 额定频率为60 Hz;
? 频率范围为15 Hz~60 Hz; ? 额定容量为180 kVA; ? 最大容量为250 kVA; ? 额定效率为95%。 5.6.2 辅助机组 5.6.2.1 牵引通风机组:
17
TJ/JW012—2014
? 通风量为5.5 m/s; ? 静态压力为3050 Pa; ? 电动机功率为30 kW;
? 电动机轴承润滑方式为全寿命润滑(密封轴承); ? 电动机轴承寿命为30000 h;
? 噪声(最高转速时)为94 dB(A)。 5.6.2.2 主变压器油泵:
3
? 油流量为72 m/h; ? 电机功率不大于9 kW。 5.6.2.3 主变压器油散热器:
? 散热量为200 kW;
3
? 循环油量为72 m/h; ? 最高入口油温为90 ℃; ? 出口油温为小于85 ℃;
? 入口空气温度为环境温度12 ℃; ? 出口空气温度为环境温度32 ℃。 5.6.2.4 牵引变流器水散热器:
? 散热功率为75 kW;
3
? 循环水量为18 m/h; ? 入口水温为63 ℃; ? 出口水温小于59 ℃;
? 最高冷却空气入口温度为40 ℃;
? 冷却空气出口温度为环境温度12 ℃;
3
? 通风量为13 m/s; ? 材质为铝。
5.6.2.5 牵引变流器水泵:
? 送水能力为300 L/s; ? 电机功率不大于2 kW; ? 水压为0.76 kPa;
? 需要与逆变器和冷却器匹配 ; ? 噪声指标为不大于70 dB(A)。 5.6.2.6 冷却塔通风机组:
3
? 通风能力为12.9/9.4 m/s; ? 静态压力为1700 Pa; ? 电机功率为29/19 kW;
? 噪声不大于95 dB(A),35 Hz。 5.7 机车控制电源
5.7.1 机车使用铅酸蓄电池,容量为 170 Ah。 5.7.2 蓄电池充电机组:
? 输出电压(浮充模式)为DC 110 V,允差为±1%; ? 输入电压为三相460 V/60 Hz,380 V/50 Hz; ? 额定输出电流为100 A; ? 输出电压纹波小于2 V; ? 质量为80 kg;
? 外形尺寸为1200 mm31000 mm3520 mm (L3W3H)。 5.7.3 机车蓄电池充电机组采用冗余设计。
5.7.4 机车装有软件来控制报警信息,一旦蓄电池电压低于94 V,发出声光警报。当蓄电池电压再低于电压88 V时,牵引制动力被锁定,微机系统断电,防止蓄电池深度放电,保证断开蓄电池重新连接后,受电弓可以再次正常升起。 5.7.5 蓄电池和机车控制能够由通常的开关控制。
18
3
TJ/JW012—2014
5.7.6 蓄电池安装在机械设备间的专用蓄电池箱里面。
5.7.7 蓄电池的两极和连接线都有明显的正负极标识,防止蓄电池和充电器间错误连接。 5.8 机车控制系统
机车电子控制系统采用基于TCN网络标准的结构形式,通过TCN车辆总线连接各相关设备,重联机车之间采用WTB列车总线联接。各电子装置符合IEC 60571:2012标准的各项要求。
机车控制系统以及列车通讯网络系统符合相关的EMC标准。接触网电压和波形变化、邻近机车升降受电弓、通断电路均不影响其正常工作。 5.8.1 控制系统功能
至少包括下述内容: ? 机车牵引特性控制;
? 机车再生制动特性控制; ? 机车顺序逻辑控制; ? 牵引变流器控制; ? 辅助变流器控制; ? 空电联锁制动控制; ? 机车重联控制;
? 空转、滑行保护控制; ? 轴重转移补偿控制;
? 轮径自动修正和手动修正的功能;
? 牵引和制动工况下牵引电机电流最大值限制控制; ? 机车故障诊断与保护,故障状态信息显示、存储功能; ? 微机转储功能; ? 无人警惕控制; ? 自动过分相;
? 通风机转速自动控制;
? 冗余控制功能,保证在工作单元失效时能自动转换;
? 冗余就是提供双路输入和输出通道,控制系统本身具有冗余结构,在运行时执行自
检:
? 地面电源移车; ? 自动换端控制。 5.8.2 控制系统组成
5.8.2.1 机车电子控制系统结构如图5所示:
19
TJ/JW012—2014
元件代号:
ADC—辅助配电柜; LVPC—低压电源柜: BC—总线集线器 ; AFC—辅助滤波柜; CAB—司机室 CMP—空气管路柜; TCMS—微机柜; CON—牵引变流器; DCU—牵引控制单元;
GW—MVB和WTB之间的网关连接器; HVC—高压柜; HVAC—加热、通风和空调单元; IDU—智能显示单元; I/O—输入/输出单元; ATP—行车安全柜; SC—星型集线器; SPIF—变流器网络接口。
图5 机车电子控制系统结构
5.8.2.2 主要功能单元:
a) 主处理单元(VCU):
? 主处理单元(VCU)采用冗余设计,整个系统由两个相同的VCU构成,但在运用
中只有一个VCU(主VCU)执行机车全部控制,另一个(从VCU)做为备份。在主VCU发生故障时,从VCU将自动投入工作,不影响机车的正常运行。主、从VCU在运用中循环变换。
? 在两台机车重联运行时,本务机车的主VCU成为两台重联机车的主VCU。其主
VCU通过WTB列车总线向其它从VCU发出控制命令和整定值。从VCU通过WTB车辆总线传递命令和整定值到它们的子系统,从而保证1台机车只有1个VCU可用时,两台机车也可以照常运行。
b) 牵引控制单元(DCU)负责电力牵引设备的开环、闭环控制,一个DCU通过线变流器
控制单元控制两个牵引变压器绕组、通过辅助控制单元控制一个辅助变流器、通过两个电机控制单元控制两台电机。每一台牵引电机都有一个牵引控制单元,从而实现单轴控制。机车装有三个相同的变流器,每个变流器装有一个DCU及附属的控制单元。DCU具有开环控制、闭环控制和监控机车牵引设备的功能,作为牵引系统的一个部分,主要具有下列功能:
? 设定牵引力和再生制动力闭环控制的给定值; ? 四象限变流器控制; ? 牵引电机控制;
? 开关装置的控制 (例如预充电接触器、线路开关); ? 监视变流器、牵引电机和其他牵引设备; ? 防空转/滑行控制;
? 提供和储存牵引有关的诊断数据;
? 通过通讯总线进行DCU与VCU以及其他控制单元之间的数据交换。
20
TJ/JW012—2014
c) 输入/输出模块(I/O)配置有微处理器、网络接口和诸如逻辑输入/输出、继电器
输入/输出、模拟输入/输出等多种输入输出接口。输入/输出模块(I/O)采用冗余设计,从而提高机车控制与诊断系统的性能、可靠性以及经济性。 d) 每个司机室有一个IDU,在不同区域显示运行信息和维修/故障信息。 e) 制动系统控制单元(IPM))具有车辆总线通讯接口,通过车辆总线与机车控制系统
进行数据交换,实现机车制动系统的控制,故障信息显示、故障诊断等功能。 f) 辅助变流器控制单元(ACU)完成辅助逆变器、蓄电池充电器以及辅助系统接触器的
控制。辅助变流器控制单元以冗余方式工作,机车共装有3套ACU。 5.8.3 监测与诊断
5.8.3.1 每个司机室中正常运行显示下列信息:
? 一般故障; ? 空转;
? 接触网电压; ? 蓄电池;
? 机车运行工况。 5.8.3.2 监测下述状态:
a ) 控制系统对外接口的状态在机车显示屏上实时显示出来,有清晰的信号名称、拓扑
位置和状态量。
b) 各控制单元的生命信号在机车显示屏上实时显示出来,有清晰的单元名称、拓扑位
置和状态量。
c) 机车重要运行数据的状态在机车显示屏上实时显示出来。
d) 对司机操作的监测:司机的各种操作指令在机车显示屏上实时显示出来,对有效操
作的执行过程和无效的操作的因果关系都有清晰的指示。
5.8.3.3 机车的故障诊断:
机车控制系统具有自诊断功能,自诊断信息可在司机显示器上进行显示。
机车的各种故障实时记录,所记录的数据采用先进先出模式,总是保持最新的记录(不少于10k条故障的记录容量),故障信息至少包含代码、故障位置、故障名称、发生时间、结束时间和用于指导机务人员检查并排除故障的车间文本。
对于发生的机车重要故障,机车控制系统不仅要记录故障发生时的故障信息,还同时要记录故障发生前和故障发生后一段时间内机车相关信息,以便于机车故障波形回放。
故障对策:控制系统采用双路双套冗余(通信介质采用双通道热备,VCU采用双套热备,重要的I/O采用双份热备)。单路故障时,可自动切换,自动切换过程中可短暂保护性动作,但自动切换过程时间不能超过20 s,切换完成后不能损失功能和动力;双路故障时,紧急制动。
5.8.3.4 司机室显示信息尽量要求用微机显示屏进行显示,并且可自动对其显示亮度进行调节;电仪表等显示信息是对微机显示信息的补充。
5.8.3.5 采用微机显示器(IDU)进行显示,对不同类别的显示信息用色彩予以分开。显示方式按照规范化司机室技术规范的要求。
5.8.3.6 显示器(IDU)具有显示各种故障信息的功能,并能提供故障处理建议。
5.8.3.7 机车能实现机车级状态信息、故障信息的诊断和记录,而且状态信息、故障信息、诊断信息和故障记录的具体信息都能通过的不同界面查阅。 5.8.3.8 机车故障信息显示至少包括:
? 主电路接地故障; ? 总风缸空气压力低; ? 制动管压力低; ? 制动故障; ? 蓄电池充电; ? 变压器温度高; ? 蓄电池电压低; ? 辅助电路接地故障;
21
TJ/JW012—2014
? 控制电路接地故障。
此外,可具有对司机有用的其他信息显示,以便快速诊断故障,保持列车正常运行。 5.8.4 信息采集及转储
控制系统具有与无线发送装置的接口。 5.8.5 无人警惕控制
机车有无人警惕控制功能,在速度高于3 km/h,且换向手柄不在“0”位时,该装置起作用,具备在机车静止状态下的试验功能。
来自ATP或无人警惕的停车命令都会导致停车,使来自其它装置的操纵命令失效。 5.8.6 控制系统的维护、保养
故障检测从设计上保证显示出机车设备故障的可能原因,每一个检测到的故障储存在IDU中,给司机一个附加的帮助文本(如机车运用受到影响),保留一个单独的文本方便维修人员查询故障。 5.9 其他电器设备
仪表具有在黑暗环境下发光功能,可通过开关进行控制。
机车上的各种DC 110 V电器在DC 77 V~137.5 V范围内可靠工作。 5.9.1 司机操控电器
5.9.1.1 司机室主要操作设备布置符合UIC 651:2002及可以实现的用户要求。各操作设备、仪表及显示设备的显示及标识采用中文。
5.9.1.2 各类手动开关 :司机室内设有万转开关和控制按钮。 5.9.2 仪表
5.9.2.1 一个双针电动仪表显示网压/控制电压,另一个显示牵引/制动力。
5.9.2.2 一个双针压力表显示总风缸压力/制动管压力,另一个双针压力表显示两个转向架的制动缸压力。
5.9.2.3 电度表分别计量机车耗电量和再生制动反馈电量。 5.9.3 状态指示灯
状态指示灯显示机车设备状态,可以调整灯光亮度。 5.9.4 液晶显示屏
5.9.4.1 显示屏显示语言采用简体中文,计量单位采用公制。显示屏设备符合IEC 60571:2012规定。
5.9.4.2 显示器额定工作电压为DC 24 V,并可在DC 14 V~36 V下工作。
5.9.4.3 显示器可自动调节屏幕亮度,亮度调节范围为10%~100%,屏幕的最大亮度为
2
350 cd/m;按键的背光适应环境亮度自动设置为开通或关闭状态。显示器同时具有屏幕亮度手动控制模式,操作者可通过软件控制屏幕亮度。在采用手动方式时,自动亮度控制功能失效。屏幕的可视范围为水平140°,垂直110°。
5.9.4.4 显示器上电或复位后,应用程序在60 s内响应启动。 5.9.4.5 显示器采用以太网进行通讯。
5.9.4.6 显示器的前面板符合IP65安全防护等级。 5.9.4.7 重量应小于4 kg。
5.9.4.8 可维护性要求:显示器能在20 min内被拆卸并更换; 5.9.5 自动换端功能 机车具有自动换端功能。 5.9.6 机车外部灯具
22
TJ/JW012—2014
采用低功耗、符合电磁兼容要求的灯具,推荐采用冷光源灯具。 5.9.6.1 头灯照度符合TB/T 2325.1—2006要求,电磁兼容要求按EN 55015:2006规定,具有减光功能,其参数符合:
? 工作电压为DC 110 V; ? 额定电流为0.91 A; ? 启动电流为小于2.5 A。 5.9.6.2 辅照灯/标志灯:符合TB/T 2325.2-2013的规定,机车前窗下部左右两侧各设有一个辅照灯和一个标志灯。每个标志灯由可分别显示红、白色的LED组成,灯光控制按技规执行。机车辅照灯具有闪光功能,此功能可通过辅照灯多位置开关进行切换。 5.9.6.3 在机车车体下部适当位置每侧安装2个检查用照明灯。除了固定照明装置,另设有行灯插座。 5.9.7 插座
安装在车体外侧适当位置,具体如下:
? 每侧各1个3相380 V/50 Hz的插座,可实现库内动车,辅助电动机试验和蓄电池
充电;
? 对外部电源标称电流要求的最大值为125 A; ? 设有一个蓄电池充电的外接DC 110 V插座。 5.10 电线、电缆、接插件 5.10.1 5.10.2 5.10.3 5.10.4 5.10.5 5.10.6 产品。
所有电线、电缆均采用无卤低烟阻燃型。 所用的电线、电缆有足够的耐压和绝缘性能。
所用的电线、电缆容量满足使用要求并留有适当余量。
所用的电气接插件在任何工况下保证接触良好,并具有良好防水防潮性能。 电线、电缆的布置方式充分考虑电磁兼容问题。
尽量减少电线电缆的种类和规格型号,对于同一种类的电线、电缆使用同一厂家的
6 机械部分技术要求
6.1 机车车体 6.1.1 基本要求
6.1.1.1 车体符合GB 146.1—1983电力机车限界的要求,并符合客运车站高站台限界的要求。
6.1.1.2 车体采用整体承载的框架式焊接结构。顶盖为可拆卸顶盖,以便于车内设备吊装,密封结构可多次重复使用并保持其密封性能。
6.1.1.3 车体结构符合标准化、系列化、模块化设计原则并满足可靠性、可用性、可维护性与安全性的要求。
6.1.1.4 车体良好密封,以防止风、沙、雾、雨、雪、污水等对车内设备的侵袭。 6.1.1.5 主要技术参数:
? 车体宽度为2950 mm;
? 车体宽度(扶手杆处)为3100 mm; ? 车体总长(两端面间)为21985 mm; ? 车钩中心线距轨面高为880 mm±10 mm; ? 车体顶盖距轨面高为4250 mm。 6.1.2 载荷及强度要求
6.1.2.1 车体(包括司机室)承载能力按TB/T 2541—2010确定。此外纵向压缩载荷取3000 kN,纵向拉伸载荷取2500 kN。
6.1.2.2 车体进行疲劳强度评估。
23
TJ/JW012—2014
6.1.2.3 整备状态车体弯曲自振频率与转向架点头和浮沉振动频率的比值不小于1.4。整备状态车体最低弯曲自振频率不得低于10 Hz。
6.1.2.4 车体排障器中央的底部承137 kN的静压力而不产生永久性变形。
22
6.1.2.5 车体内部件及其紧固件承受的运用载荷,按纵向2.5 m/s 、横向1.5 m/s、垂向
2
2.0 m/s(未包括重力加速度)的加速度作用于部件自身质量的惯性力计算。许用应力为材料屈服极限考虑1.5的安全系数。 6.1.2.6 在设计紧固件时,冲击载荷按作用于部件自身质量的惯性力计算。参考加速度是纵向3 g~5 g,横向1 g、垂向加速度是按az = -(1±c)g,在车两端取c为2,在车体中心取c为0.5。许用应力不超过材料屈服极限。
6.1.2.7 结构的承载能力按强度、变形、频率和疲劳强度及寿命等项指标进行评价。 6.1.3 车体结构与材料要求
6.1.3.1 车体为整体承载结构,由底架、侧墙、车顶、两端司机室、司机隔墙等组成一个整体。采用可拆卸的活动顶盖,在机车检修库内,天车吊钩距轨面高度不超过9000 mm条件下,能把车体内各屏柜、各机组等单独吊出和吊入。
6.1.3.2 车体采用中央走廊方式,宽度不小于600 mm,走廊地板要求平整防滑。 6.1.3.3 采用底架与车内设备安装骨架焊接的一体化结构。 6.1.3.4 底架侧梁上设有四个强度足够的吊销套孔,并在前后端牵引梁上设有四个救援用的吊销孔(带一个转向架起吊,另一个转向架留在轨道上)。
6.1.3.5 底架侧梁底部设有四个架车支承座和供检修用的四个支承点,在车体支承座架起距轨面高度不超过2500 mm的条件下,转向架和主变压器可自车体下推出,其位置不致妨碍架车作业。
6.1.3.6 车体与转向架之间设有备用的联接装置,以便在需要时将车体同转向架一并吊起。 6.1.3.7 车体两端前下部安装排障器,排障器能方便上下调节,以保证其距轨面高度为 +10
110 0 mm。
6.1.3.8 更换车钩及缓冲器需要先拆下排障器以便操作。 6.1.3.9 机车的两端设有调车员脚踏板,并有相应的扶手。机车第一级脚蹬上平面距轨面高度为420 mm±20 mm。
6.1.3.10 车顶面进行防滑处理,确保车顶检查作业人员安全。
6.1.3.11 车体钢结构材料要求具有良好的使用性能,6 mm(含6 mm)以下钢板采用冷轧钢板,6 mm以上钢板允许采用热轧钢板。 6.1.3.12 车体材料:
a) 牌号为Q345E,符合标准GB/T 1591—2008规定:
? 最小拉伸极限为470 MPa~630 MPa; ? 屈服极限为345 MPa。
b) 牌号为09CuPCrNi,符合标准为TB/T 1979—2003规定:
? 最小拉伸极限为480 MPa; ? 屈服极限为345 MPa。
c) 牌号为Q235A,符合标准GB/T 700—2006规定:
? 最小拉伸极限为375 MPa~500 MPa; ? 屈服极限为235 MPa。
d) 车体焊接材料型号为J422,符合标准GB/T 5118—1995。 6.1.4 制造要求
6.1.4.1 首件焊接要求 :
a) 对首件车体和其他重要结构件的所有高应力焊缝和高应力焊区进行X射线或超声探
伤;
b) 高应力焊缝和高应力焊区根据有限元分析和/或强度试验的结果确定,临界疲劳焊区
和焊缝单独标注;
c) 车体的高应力焊缝和高应力焊区X射线或超声探伤符合国家相关标准或对应的国际
标准。焊缝探伤按GB/T 3323—2005、GB/T 11345—1989、GB/T 6417.1—2005、
24
TJ/JW012—2014
GB/T 6417.2—2005标准。 6.1.4.2 批量焊接要求:
a) 所有的焊缝需作100%的目视检查; b) 对所有高应力焊缝进行磁粉或着色探伤检查。随机地对疲劳负载焊缝进行X光探伤,
焊缝检查将在制造文件中说明;
c) 车体上的焊缝不得有气孔、夹渣、裂纹等缺陷,符合GB/T 6417.1—2005,
GB/T 6417.2—2005系列标准的焊接要求。 6.1.5 车体检测
6.1.5.1 车体钢结构总成后,底架上挠度保持在0~15 mm。
6.1.5.2 车体钢结构总成后,两侧二系弹簧安装面高度差不大于±2 mm。 6.1.5.3 机车落成后,在平直道上有下列规范:
? 每节车体前后水平差不大于10 mm(在车钩纵平面参考点处测量)。
? 在每一个横截面,两个纵向参考点(距离3000 mm)的高度差不大于6 mm(机车坐
落在水平面上)。 6.1.6 车体油漆
车体油漆符合TB/T 2393—2001和TB/T 2879—1998等标准的要求。 车体涂装后保证6年内没有基材锈蚀、漆膜掉块等现象。 6.2 车钩及缓冲器
6.2.1 车钩及缓冲器满足机车双机重联牵引万吨列车的需要。
6.2.2 车钩能与TB/T 3044—2002、TB/T 3046—2002规定的各型车钩相联挂。车钩装有下作用式单侧手提杆。
6.2.3 缓冲器采用大容量弹性胶泥缓冲器,其容量不低于100 kJ,此时的阻抗力为2500 kN。缓冲器和车体牵引梁的连接具有超载保护措施。 6.2.4 车钩材料:
? 牌号E级钢,符合标准TB/T 2942—1999; ? 材料最小拉伸极限为830 MPa; ? 屈服极限690 MPa。 6.2.5 车钩强度:
a) 钩体最小破坏载荷4005 kN;
b) 最大永久变形为加载3115 kN时不大于8 mm; c) 钩舌最小破坏载荷为3430 kN。
6.2.6 车钩及缓冲器能在不架起车体的情况下进行拆装检修。 6.3 转向架 6.3.1 基本要求
6.3.1.1 采用三轴转向架,构架采用焊接结构,牵引电机采用滚动抱轴悬挂方式,满足最大运用速度120 km/h的要求。
6.3.1.2 转向架采用标准化、系列化、模块化、轻量化设计,符合可靠性、可用性、可维护性与安全性的规定,尽量达到无磨耗、免维修的要求。转向架便于从车体下推出,轮对轴箱装置便于更换。
6.3.1.3 转向架主要由轮轴驱动系统、构架、一、二系悬挂系统、牵引装置、电机悬挂装置、基础制动装置、空气管路、附属装置等组成。
6.3.1.4 车轮踏面外形符合TB/T 449—2003中JM3的要求。 6.3.1.5 构架与车轴之间有良好的绝缘,并另设接地装置保证构架与车轴之间具有良好的导电性,以避免产生轴承电蚀。 6.3.1.6 主要技术参数:
? 最高运行速度为120 km/h; ? 轴式为Co - Co;
25
TJ/JW012—2014
? ? ? ? ? ? ? ? ? ?
轴重为25t,允差为-3%~1%; 转向架固定轴距为231950 mm; 转向架中心距为12950 mm; 轨距为1435 mm;
轮对内侧距(空载)为1353?1 mm;
轮径(新/半磨耗/磨耗)为1250 mm/1200 mm/1150 mm; 通过最小曲线半径为125 m; 牵引装置为单牵引杆结构; 转向架自重为28500 kg; 每轴簧下重量为5400 kg。
?0.56.3.2 主要性能
6.3.2.1 转向架符合本技术条件对机车运行稳定性、平稳性、运行品质等动力学性能的要求。 6.3.2.2 转向架与车体有良好的耦合,通过悬挂系统抑制冲击和振动激扰对车体的影响。 6.3.2.3 转向架避免产生频率与车体固有频率相同或相近的振动。 6.3.2.4 转向架及其主要零部件至少符合TB/T 2368—2005对结构强度(包括:静强度与疲劳强度)的要求,以及有关标准对弹簧强度、轮轴强度等方面的要求,并根据运用条件进行结构强度分析。
6.3.2.5 在设计紧固件时,冲击载荷按纵向3g、横向1g、垂向3g(包括重力加速度)的加速度作用于部件自身质量的惯性力计算。许用应力不超过材料屈服极限。 6.3.3 构架
6.3.3.1 构架采用高可靠性结构。构架由两个侧梁、一个牵引梁、一个横梁和两个端梁组成。各梁均是焊接箱形结构。高应力连接点、连接面均要求加工。构架上的电机吊座、基础制动吊座、减振器安装座等安装座有足够的强度。
6.3.3.2 构架符合TB/T 2368—2005对结构强度的要求。 6.3.3.3 构架材料牌号为Q345E,符合标准为GB/T 1591—2008,材料最小拉伸极限470 MPa~630 MPa,屈服极限为345 MPa。
6.3.3.4 构架焊接材料型号按照焊接和基本材料的要求来选择,应符合相关标准的规定。 6.3.3.5 构架结构强度试验确认其在运行中受组合作用力时不会产生永久变形和裂损的危险,确认构架的实际疲劳性能、可能存在的薄弱环节及其安全系数。 6.3.3.6 构架采用三维有限元分析和结构模态计算进行应力与频率分布、结构固有频率、动力响应及耐久性等分析,对电机吊座结构及其附近的结构强度应进行重点分析,构架结构应进行优化设计。
6.3.3.7 构架进行焊缝疲劳强度评估。
6.3.3.8 构架加工完成后,保留明显的水平基准标志,并用钢印打上构架型号和代号。 6.3.3.9 防腐与油漆满足气候环境和运用条件的要求。 6.3.4 轮轴驱动系统
6.3.4.1 轮对驱动制动系统由驱动齿轮箱(含齿轮)、轮对、轴箱、牵引电机、制动盘和抱轴箱等部件组成。
6.3.4.2 轮轴驱动系统根据机车的动力学性能、可靠性、维修性进行科学合理的系统设计。 6.3.4.3 转向架轮轴驱动系统作为完整的系统,在转向架落成前,先完成该系统的集成,并进行该系统的联调工作。
6.3.4.4 牵引电机和驱动齿轮箱采用一体化整体设计。牵引电机输出轴与小齿轮轴之间设薄膜联轴节,小齿轮轴两端各设一个轴承。 6.3.4.5 抱轴箱、牵引电机和齿轮箱组成一个刚性构件。一端通过两个分别安装于抱轴箱内和齿轮箱内的滚动轴承支承在车轴上,另一端通过一个吊挂点悬挂于转向架构架上。 6.3.5 轮对
6.3.5.1 轮对由车轮、车轴、轴箱装置等组成。
26
TJ/JW012—2014
6.3.5.2 车轮:
a) 采用整体辗钢车轮,选择经过优化的轻量化结构;
b) 车轮重量小于840 kg。车轮残余静不平衡值不大于75 g2m;
c) 车轮制造采用先进的冶炼和加工工艺,以提高车轮的安全性,防止踏面剥离等故障
的发生; d) 车轮符合UIC 812-3:1984要求。每个车轮进行逐个探伤检查,其材料和机械性能为:
? 车轮材料为 R8(UIC 812-3:1984);
22
? 抗拉强度为860 N/mm~980 N/mm; ? 延伸率为13%;
? 冲击韧性为15 J(常温下)。
6.3.5.3 车轴:
a) 车轴有良好的几何形状,有足够的刚度和抗疲劳的能力。车轴的设计满足标准要求,
车轴材料、制造及质量满足GB 5068—1999和TB/T 2072—1989要求,车轴设计寿命达到400万公里的要求;
b) 车轴坯锻制,消除内应力。成品轴探伤检查。轴端有钢印打上的轴号。车轴选用优
质钢材,其材料和机械性能满足GB 5068—1999标准要求,主要参数如下: ? 车轴材料牌号JZ50钢材;
2
? 屈服点不小于330 N/mm
2
? 极限强度不小于593 N/mm ? 延伸率不小于19%; ? 断面收缩率不小于35%;
22
? 冲击韧性中四个试样平均值不小于34 J/cm,个别试样最小值不小于29 J/cm。 c) 车轴采取防止运行时激起异物打击造成损坏的措施。 6.3.5.4 轮对组装:
a) 轮对组装满足TB/T 1463相关要求;
b) 轮对残余动不平衡值不大于75 g.m,不用加重法调整轮对不平衡量; c) 车轮与车轴组合采用压装配合,轮座轮缘侧凸悬量为2.5 mm 、非轮缘侧凸悬6.5 mm (符合EN 13104及TB/T 1463要求),车轮与车轴的过盈量为0.285 mm~0.355 mm; d) 轮轴组装时记录压装和反压的载荷位移曲线。 6.3.5.5 轴箱装置 :
a) 轴箱装置由轴箱体和轴承等组成,轴箱装置有良好的承载能力和密封性能; b) 轴箱材料为C级钢;
c) 轴箱体前后端是密封的。轴箱体满足接地装置和速度传感器的安装要求; d) 轮对每侧各有一套自密封型轴承,轴承计算寿命大于300万公里;
e) 轴箱轴承尺寸:内径160 mm、外径270 mm。在正常运行条件下,轴承温升不超过
40℃,最高温度不超过120℃;
f) 在各端轴的一端设接地装置,接地装置易于安装和拆卸。接地装置确保车辆接地良
好,不允许造成轴箱轴承电蚀现象。接地电刷与滑环磨耗量的比不小于10; g) 轴箱设有速度传感器,拆装方便。 6.3.6 一、二系悬挂系统与牵引装置 6.3.6.1 一系悬挂系统
一系悬挂系统由轴箱拉杆、橡胶件、钢弹簧、减振器等组成。
每轴箱通过两个弹簧与构架连接。每转向架在端轴上设2个一系垂向减振器,该减振器安装在车轴中心线上,两端分别连接轴箱与构架侧梁。端轴通过一系减振器实现轮对与转向架的整体起吊,中间轮对通过特殊的吊杆实现轮对与转向架的整体起吊。主要参数如下:
a) 一系弹簧:
? 刚度为0.995 kN/mm; ? 静挠度为48.3 mm。 b) 一系垂向减振器:
27
TJ/JW012—2014
? ? ?
阻尼为7.5 kN/0.1 m/s; 行程为90 mm;
安装尺寸为330 mm。
6.3.6.2 二系悬挂系统
二系悬挂系统由弹簧、橡胶垫、减振器、止挡、起吊装置等组成。
每转向架通过4个螺旋弹簧与车体连接,弹簧安置在构架侧梁上。每转向架有两个横向和两个垂向减振器连接车体与转向架。主要参数如下:
a) 二系弹簧:
? 刚度为839.5 N/mm; ? 静挠度为135.3 mm。 b) 二系横向减振器:
? 阻尼为7.5 kN/0.1 m/s; ? 行程为185 mm。 c) 二系垂向减振器 :
? 阻尼为15 kN/0.1 m/s; ? 行程为185 mm。 6.3.6.3 牵引杆
牵引杆采用无磨耗结构,且联接部位有可靠的防松、防脱措施。
2
牵引杆承受转向架质量乘30 m/s的纵向载荷而不发生永久变形,承受转向架质量乘2
50 m/s的纵向载荷而不发生损坏(允许永久变形)。
牵引杆橡胶关节径向刚度为20 kN/mm。 6.3.6.4 转向架和车体的连接
车体和转向架能同时吊起;
在转向架低速脱轨时,转向架的起吊构件的损坏有限,以保证救援时可以通过提升车体来使转向架复轨。
6.3.6.5 一、二系悬挂系统和牵引杆
应能适应整车动力学性能的要求,一系悬挂系统方便更换轮对。 6.3.6.6 弹簧
钢弹簧的设计、制造及质量满足相关标准的要求。
弹簧在运用200万公里后,自由高变形量不得大于1%。 6.3.6.7 减振器
应有永久性的型号、阻尼特性、生产年月的标志。 6.3.7 驱动齿轮箱
6.3.7.1 驱动齿轮箱能承受列车运行过程中的所有载荷,包括牵引和制动产生的扭矩、牵引电机在短路条件下的扭转振动和冲击扭矩、惯性力和驱动系统的相应载荷等。
6.3.7.2 驱动齿轮箱设有油量观察装置,观察装置上有明确的最少油量和最多油量标识线。观察窗应予以防护,以防石击和保持清洁。
6.3.7.3 驱动齿轮箱设有加油孔、排油孔,在落车状态下,借助排油孔能将箱体内的润滑油全部排放尽。
6.3.7.4 驱动齿轮箱动密封采用迷宫密封,以保证外界污染物、水不进入齿轮箱内(仅限于飞溅的水),并保证齿轮箱内部的润滑油不泄漏。 6.3.7.5 齿轮箱采用飞溅润滑,在规定的环境中和使用条件下,保证轴承和牵引齿轮润滑充分。润滑油正常换油周期不大于3年或20万公里,以先到者为限。 6.3.7.6 传动齿轮采用优质合金钢制成。要求如下:
a) 齿轮参数:
28
TJ/JW012—2014
? 传动比为4.952; ? 齿数为104/21; ? 模数8.75; ? 螺旋角12°; ? 压力角20°。
b) 齿轮材料牌号及机械性能:
? 材质18CrNiMo 7-6(DIN EN 10084:2008);
2
? 屈服点不小于700 N/mm
2
? 极限强度不小于1000 N/mm ? 延伸率不小于8%;
? 断面收缩率不小于35%;
6.3.7.7 齿轮箱材料为 EN GJS 400-18-LT, 按EN 1563:2005规定。 6.3.7.8 驱动齿轮箱效率不小于98%。 6.3.7.9 齿轮箱噪声试验将基于ISO 3095:2005和ISO 3381:2005随整车进行。不单独对齿轮箱测量。 6.3.8 滚动抱轴箱
材料为EN GJS 400-18-LT,机械性能符合EN 1563:2005标准。所有采用脂润滑的轴承应设有加油嘴。 6.3.9 基础制动
每个车轮上装有一套单元制动装置,装有带弹簧蓄能停放制动装置的轴位为第一、三、四、六轴。 6.3.10 附属装置
6.3.10.1 轴箱与构架之间设有垂向、横向止挡以限制轮对与构架之间的相对运动,参数为:
a)垂向止挡间隙为25 mm;
b)横向止挡间隙:
? 端轴为15 mm; ? 中心轴为25 mm。
6.3.10.2 转向架构架与车体之间设有垂向、横向、摇头及点头止挡以限制车体与构架之间的相对运动,参数为:
a) 垂向止挡间隙为30 mm弹性间隙5 mm; b) 横向止挡间隙为±40 mm弹性间隙10 mm; c) 转向架与车体最大转角为4.5°; d) 点头止挡允许最大角度为1.5°。
6.3.10.3 转向架的前端安装扫石器以清扫轨面。转向架扫石器距轨面高度30 mm (在轮缘磨耗范围内可调)。
6.3.10.4 转向架上装有喷脂式轮缘润滑装置,在该装置正常使用的情况下,保证机车轮缘
4
磨耗小于0.3 mm/10 km。 6.3.11 制造要求
6.3.11.1 材料:
a) 转向架所用材料均符合环境保护的要求; b) 转向架所用材料均符合相关标准;
c) 车轮材质的选用除考虑车轮强度和韧性指标外,还要考虑轮辋硬度与钢轨硬度的匹
配,以减少轮轨的磨耗。
6.3.11.2 首件焊接要求 :
a) 对首件转向架构架和其他重要结构件的所有高应力焊缝和高应力焊区进行X射
线或超声探伤;
b) 高应力焊缝和高应力焊区根据有限元分析和强度试验的结果确定,临界疲劳焊
29
TJ/JW012—2014
区和焊缝单独标注;
c) 转向架的高应力焊缝和高应力焊区的X射线或超声探伤应符合相关标准。 6.3.11.3 批量焊接要求:
a) 所有的焊缝需作100%的目视检查;
b) 对所有高应力焊缝进行磁粉或着色探伤检查。对于高应力粗大焊缝,下凸缘100%
X射线探伤,上凸缘10% X射线探伤(第一个构架100% X射线探伤); c) 可随机选取“高应力焊缝”进行测试。 6.3.11.4 转向架组装几何尺寸及公差:
a) 新造机车车轮轮径差:同轴不大于0.5 mm,同转向架不大于1.0 mm,同车不大于
2.0 mm;
b) 使用时允许的机车车轮轮径差:同轴不大于3 mm,同转向架不大于12 mm,同车不
大于40 mm;
c) 转向架构架两侧轴箱拉杆安装面距离偏差不大于0.5 mm;
d) 转向架构架两侧梁在固定轴距与轴颈中心距交点处的对角线之差不大于2 mm,四
角高之差不大于4 mm;
e) 一系弹簧按车辆试验载荷进行高度选配,同一轮对一系弹簧高度差不大于2 mm,
同一转向架一系弹簧高度差不大于3 mm,同一转向架二系弹簧高度差不大于4 mm; f) 转向架在专用的工装设备上施加额定载荷后测量轴重和轮重的偏差;
g) 测量基准易于接近。提供的资料中包括测量点位置及测量方法,在需用专用工具进
行测量时,提供专用测量工具。
6.3.11.5 转向架的总成要求:
a) 转向架的组装在专用的工装设备(可施加额定载荷)上进行,以保证组装精度; b) 转向架在车体给定的重量下进行静载荷试验;
c) 静载荷试验能给出转向架的每一轮重、轴重及轮重差。
7 制动及供风系统技术要求
制动及供风系统主要包括风源及干燥系统、制动控制系统(含司机室主要设备)、基础制动系统和撒砂系统,以及辅助系统中的空气压缩机系统。 7.1 总体要求
7.1.1 采用基于AAR规则的机车制动系统
在对压缩机油进行预热后,机车制动系统能在-40℃的环境温度下启动,具体预热时间为30 min。
7.1.2 投入使用的时间要求
对于-25 ℃或以上的环境温度,制动系统的电气控制系统能在100 s内投入使用。 7.1.3 紧急制动距离要求
紧急制动的距离要求在平直道上,当时速120 km/h时不大于1100 m。 7.1.4 标志要求
控制元件和显示元件通过粘贴耐磨的象形图加以识别。此外,每一个制动模块或部件上有一个自粘性的英文和中文标志。 7.1.5 机械要求
7.1.5.1 连接件、紧固件等均为公制尺寸且符合国际标准。
7.1.5.2 确保维护的容易性,易磨损的零部件无须专门工具就能容易地接近和拆卸。 7.1.5.3 所有的材料满足技术规范规定的气候条件。 7.1.5.4 所有部件设计成避免受到腐蚀。
7.1.5.5 维修人员可以容易地接近和操作紧固件、测试端口和测试零件。保护上述器件免受
30
TJ/JW012—2014
湿气或灰尘的侵入。
7.1.5.6 安装或拆卸制动系统部件或压缩空气风源系统时不使用特殊的工具。 7.1.5.7 压缩机和干燥器间的管路接触潮气,采用橡胶软管和不锈钢管;原则上车内所有其它管路采用不锈钢管或经过防腐处理的钢管,转向架部分采用不锈钢管或内部经过防腐处理的钢管。
7.1.5.8 除了功能模块内的管道,铜管不容许作为替代品在制动柜内的使用。 7.1.5.9 管件采用公制尺寸,管件连接螺纹是英制。
7.1.5.10 塞门的手柄按下列规定安装:在工作位置时手柄与管路平行,且能方便操作。软管设计寿命至少6年。
7.1.5.11 如果不同的材料组合在一起,确保这样的组合不会导致接触腐蚀或类似的问题。此项同样适用于所有的连接件和紧固件,所有的安装表面有防腐保护。 7.1.5.12 管路如使用快装接头,使用卡套式(非橡胶密封)快装接头。
7.1.5.13 机车制动系统的总风联管、列车管、制动平均管接口满足铁道部的相关标准或要求。供风管折角塞门和总风软管组成连接的接头形式采用Rc1;列车管折角塞门和列车管软管组成连接的接头形式采用Rc1?。 7.1.6 防护等级
主要制动部件防护等级如下: ? IPM为IP31; ? EBV为IP23; ? RIM/CJB为IP31; ? EPCU为IP55。 7.2 风源及干燥系统
风源及干燥系统主要包括:主空气压缩机、主空气干燥器和过滤器、主风缸、辅助空气压缩机、辅助空气干燥器和过滤器、辅助风缸等。 7.2.1 主空气压缩机组
7.2.1.1 每台机车装有两台排气量不小于2400 L/min的空气压缩机。压缩空气进入制动系统总风缸前,经过干燥装置处理。
7.2.1.2 空气压缩机出口的压缩空气质量达到ISO 8573-1:2010固体颗粒3级,油4级的标准。
7.2.1.3 经过干燥装置处理后的压缩空气质量要达到ISO 8573-1:2010固体颗粒2级,油3级的标准。
7.2.1.4 经过过滤器后进入制动系统的压缩空气的质量符合ISO 8573-1:2010固体颗粒2
33
级(固体颗粒含量小于1 mg/m,尺寸小于1μm),油2级(含量小于0.1 mg/m,溶度小于0.1 ppm),水2级的标准。
7.2.1.5 主空气压缩机组采用2台螺杆式空气压缩机,技术参数如下:
? 排气量为2400 L/min; ? 额定压力为1000kPa;
? 电机功率为21.5(1±7%)kW; ? 重量为240(1±3%)kg;
? 振动为空压机组安装在橡胶减震垫上,这样就不会向支撑体传播振动; ? 滤清器要求:进气口的滤清器采用带有人造滤网的合成滤清器形式。 7.2.1.6 空气净化干燥装置要求:
? 干燥剂要求为颗粒状;
? 更换周期:在满足7.2.1.2要求的空气清洁度条件下,8年。 7.2.2 空压机启停控制
当总风压力低于680 kPa±20 kPa,启动两台空气压缩机工作,压力达到900 kPa±20 kPa时停止工作;当总风压力低于750 kPa±20 kPa但不低于680 kPa±20 kPa时,启动一台空
31
TJ/JW012—2014
气压缩机工作,压力达到900 kPa±20 kPa时停止工作。
两台空压机按合理周期定期轮换工作。 7.2.3 总风安全阀设定值
空气压缩机出口后总风管路安全阀设定值为950 kPa±20 kPa。 7.2.4 机车总风缸
7.2.4.1 总容积不小于1600 L。
7.2.4.2 机车装有符合TB/T 304—2011标准的钢制总风缸。
7.2.4.3 总风缸安装在空气干燥器后,因此只需安装排水塞门而不需要排水阀。
7.2.4.4 过滤器直接连接到干燥器后、总风缸前,因此所有使用压缩空气的部件,包括控制阀,都将得到清洁的空气。
7.2.4.5 在900 kPa总风压力下,总风缸管路的泄漏量不大于20 kPa/5 min。 7.2.4.6 对总风缸材质的要求:钢材符合TB/T 304—2011。 7.2.5 辅助空气压缩机组
7.2.5.1 每台机车设有一台辅助空气压缩机组,额定风压为800 kPa。 7.2.5.2 排气量为70 L/min,允差±6%。 7.2.5.3 电机功率为860 W。
7.2.5.4 连续工作为不大于10 min。
7.2.5.5 机车设有50 L的升弓风缸,风缸储存800 kPa压缩空气在24 h后,泄漏不得大于50 kPa。
7.3 制动控制系统 7.3.1 系统概述
7.3.1.1 系统漏泄:
600 kPa压力条件下,在机车制动系统完全充满风后,切断列车管的补风,要求列车管每5 min漏泄量不大于10 kPa。
7.3.1.2 机车制动系统有以下的制动功能:
? 动力制动; ? 自动空气制动; ? 单独制动; ? 紧急制动;
? 采用弹簧储能的停放制动。 7.3.1.3 其它功能要求:
列车管压力可以设定为500 kPa或 600 kPa,控制系统在这两种压力下可以正常运用。 制动控制系统具有阶段缓解和一次缓解的选择功能,具有自动保压、自动补风作用,也可根据需要取消自动补风。 7.3.1.4 控制手柄:
? 制动作用可以通过操纵三个手柄实施,制动手柄的动作灵活、可靠。自动制动手柄
(列车制动)和单独制动手柄(机车制动)控制空气制动,主控制器是动力制动控制手柄也可控制自动制动;
? 单独制动手柄控制机车制动缸压力;
? 自动制动手柄控制列车管压力,进而控制着全列车的空气制动; ? 机车动力制动也可以由司机主控制器控制。 7.3.1.5 空气制动和动力制动联合作用功能:
? 机车制动控制系统有将列车空气制动和机车动力制动联合应用的功能,并且机车动
力制动优先使用。该制动控制系统能实现自动制动手柄的指令与机车主控制系统之间进行通信,以使机车的动力制动能根据自动制动手柄的指令来实施。只要机车动力制动可利用,就被激活。
32
TJ/JW012—2014
当用自动制动手柄实施列车常用和紧急制动操作时,机车动力制动与车辆空气制动可同时使用,机车动力制动力的大小与自动制动手柄对应的列车管减压量所产生的机车空气制动力相匹配。机车施行动力制动时,机车自动空气制动被切除,制动缸不得有压力。
? 当用单独制动手柄实施机车制动操作时,出于安全原因,施加空气制动力。
? 当机车通过制动管压力施加动力制动的同时,可以通过单独制动手柄施加单独空气
制动,这时将产生动力制动(自动制动)和空气制动(单独制动)的叠加。当制动缸压力达到90 kPa时,切除动力制动。
? 在制动过程中,允许司机通过司机控制器增加动力制动,但是不能通过司机控制器
减小动力制动。动力制动力可以通过不同的方式获得(制动管传感器或司机控制器),数值较高者生效。
? 当动力制动指令同时来自自动制动手柄或者司机控制器时,数值较高者生效。 ? 当动力制动失效时,动力制动将被切除,动力制动和空气制动的联锁功能失效,空
气制动根据制动手柄的制动指令自动起作用。
? 特别是紧急制动时,为保证安全,机车空气紧急制动可靠地作为动力制动的后备,
即在动力制动失效时,立即投入空气制动使机车制动缸充风。 ? 空气制动的投入和动力制动的切除协调,以减小列车的冲动。 7.3.1.6 动力制动和空气制动的联锁:
如果司机首先通过司机控制器施加了动力制动,然后使用自动制动,自动制动指令同样会使动力制动起作用,这种情况下将执行两个指令的较大者。当施加单独制动时,空气制动可以激活,当制动缸压力达到90 kPa时,切除动力制动。
当司机通过单独制动手柄施加空气制动,在机车制动缸压力达到90 kPa时,动力制动将被切除或阻止。
7.3.1.7 与使用其他机车制动系统的兼容:
机车制动系统与26-L、JZ-7、EL-14 、DK-1、CCBⅡ或EUROTROL型制动系统兼容,与装有上述制动系统的机车可以重联操作。 7.3.1.8 断钩保护功能:
当列车分离时,机车能切断列车管补风,防止总风缸的压缩空气流失。在机后1584 m或120 辆货车以内发生断钩时,能够切断列车补风,并产生紧急制动作用。
注:断钩总是意味着制动管断裂,这将在分离的列车部分自动施加自动制动。在这两种情况下,制动
管的风源将被切断(AAR),因而在各种突发情况下,制动管压力的降低足以触发紧急制动。
7.3.1.9 机车制动控制系统中的主要部件和功能应有冗余设计。 7.3.1.10 制动信息显示:
显示屏能显示总风缸、均衡风缸、列车管、制动缸压力和列车管充风流量的信息,以及故障诊断和报警信息。如果故障发生在相同型号的重联机车上,本务机车显示屏上也能读取重联机车的故障信息。这些信息通过列车总线(WTB)传输。
显示的制动信息内容以中文为主。 7.3.1.11 系统自诊断:
? 系统有自诊断功能。要求提供系统自诊断的详细内容; ? 系统有故障记录、分析功能;
? 系统有良好的人机界面(中文)和RS232或者改进的接口,以便诊断信息的下载和
分析;
? 下载的数据、文件能在中文Windows环境下进行处理,所有分析结果都以中文方式
显示;
? 状态监控系统记录制动系统的各种临界状态,同时具备存储功能。记录的状态数据
满足机车维护时的需要。
7.3.1.12 机车两端的总风管、列车管和制动缸平均管上分别安装有防撞塞门。 7.3.2 制动操作模式
7.3.2.1 由主司机控制器的给出的动力制动,操纵主司机控制器到制动位,施加机车的动力制动,动力制动力的大小与司机控制器的位置成正比。
33
?
TJ/JW012—2014
7.3.2.2 自动制动手柄的常用制动
自动制动与动力制动通过制动管内的压力计联合作用,正常操作时,自动制动命令会通过动力制动执行,同时锁定空气制动。当司机有意识地切除动力制动时,锁定解除,自动制动命令将只具有空气制动的特性。
充风缓解作用:自动制动手柄在运转位时,实现列车管的定压充风及机车制动缸的完全缓解。
在紧急制动后使用运转位充气缓解时,机车列车管压力从零升至480 kPa(500 kPa定压)和升至580 kPa(600 kPa定压)的时间分别小于9 s和11 s。
在一次缓解时,机车制动缸压力从常用制动最高压力降至40 kPa的时间小于7 s(500 kPa定压)或8.5 s(600 kPa定压)。
常用制动作用:列车管最小减压量为50 kPa,机车制动缸压力为100 kPa±15 kPa。 常用制动可连续制动至最大减压位。 定压为500 kPa时:列车管最大减压量140 kPa,机车制动缸最大压力为360 kPa±15 kPa。 定压为600 kPa时:列车管最大减压量170 kPa,机车制动缸最大压力为420 kPa±15 kPa。 机车制动缸压力与列车管减压量成线性比例关系。
机车均衡风缸的减压速度能进行调整:从500 kPa降至360 kPa的时间为5 s~7 s;从600 kPa降至430 kPa的时间为6 s~8 s。
有过量减压作用。能够进行超出列车管最大减压量的减压作用。 7.3.2.3 单独制动:
操作单独制动手柄能控制机车的单独制动和单独缓解,而不会影响列车管的压力变化。 当单独制动手柄处于制动区时,机车执行空气制动作用。
单独制动执行时只进行空气制动,如果要施加机车动力制动,由司机控制器施加。 单独制动全制动时,机车制动缸的最高压力为300 kPa±10 kPa,制动缸压力从零升至285 kPa的时间为2 s~4 s。
当单独制动手柄处于运转位时,机车缓解制动。全缓解时,机车制动缸压力从300 kPa降至40 kPa的时间为3 s~5 s。
单独制动手柄具有单缓功能,能缓解机车因自动制动产生的制动作用,包括动力制动,单独制动手柄单缓后自动复位。
常用制动的制动缸压力,在单缓后不能恢复。 紧急制动的制动缸压力,在单缓后允许恢复。 7.3.2.4 紧急制动 :
a) 紧急制动可以有下列几种方式产生:
? 自动制动手柄在紧急位; ? ATP惩罚制动; ? 拉紧急制动阀;
? 列车分离等其它原因造成的紧急制动。
b) 自动制动手柄在紧急位或ATP引发紧急制动时,机车实施动力制动,空气制动备用,
车辆实施空气制动;
c) 列车分离和拉紧急制动阀排风(列车管减压速度大于80 kPa/s)时,触发紧急制动
作用;
d) 机车制动控制系统设计为失电执行常用制动,而紧急制动作用是得电触发紧急制动
电磁阀获得;
e) 在任何紧急制动和惩罚制动(由司机或自动实施)时,机车制动系统切断列车的牵
引作用及切断列车管的补风作用;
f) 任何紧急制动作用保持至机车完全停止。紧急制动发生后,保证在机车停车至少60 s
后且自动制动手柄在紧急位方可缓解紧急制动作用;
g) 各种紧急制动时,机车在15 km/h~80 km/h速度范围内自动撒砂; h) 空气紧急制动时,制动缸的升压速率不低于常用制动时的升压速率; i) 单机紧急制动时,列车管从定压(500 kPa)降至0的时间小于3 s(需要8#放风阀的
配合)。机车制动缸最高压力为450 kPa±20 kPa。
7.3.2.5 停放制动:
34
TJ/JW012—2014
停放制动只用于完全停车后;
停放制动靠弹簧动作,通过压缩空气缓解; 停放制动装置能手动机械缓解;
通过控制停放制动电磁阀,司机操作停放制动按钮可进行停放制动的实施和缓解;机车110V电源断电后,停车制动自动实施;
? 任何情况下,停放制动弹簧力与机车制动缸空气压力不可叠加实施; ? 停放制动需要有明确的状态指示;
? 停放制动控制压力的状态通过机车主控系统的压力传感器加以诊断;
? 车侧有明确的停放制动状态指示,绿色为停放制动释放状态,红色为停放制动作用
状态;
? 在停放制动状态,方向手柄离开“0”位后,机车显示屏醒目显示警告,同时封锁牵引。 7.3.2.6 重联机车的操作:
? 机车制动机具备重联功能;
? 重联机车或双司机室机车的非操作端的自动制动手柄和单独制动手柄取出或锁闭,
使其失去控制功能;
? 当机车设置为重联机车后,在该机车上有指示;
? 在制动平均管的作用下,本务机车制动控制系统能实现对重联机车的制动和缓解控
制,以及作为重联机车通过制动平均管响应本务机车的制动和缓解操作控制。重联机车的制动缓解作用与本务机车的制动缓解协调一致;
? 当重联机车分离时,能阻止总风压力的过快流失,保持触发的紧急制动作用。 7.3.2.7 无动力回送:
? 当机车作为无动力车在列车编组中运输时,制动系统执行列车制动模式;
? 在无动力回送过程中,当列车管达到最大减压量时,回送机车的制动缸压力最高为
250 kPa±20 kPa。
7.3.2.8 动力制动的防滑由机车控制系统实现。 7.3.3 司机室内装置
7.3.3.1 主司机控制器:
? 主司机控制器控制机车动力制动;
? 制动手柄包括自动制动手柄和单独制动单独手柄;
? 单独制动手柄仅控制机车的制动;而自动制动手柄通过控制列车管压力来控制整个
列车的制动和缓解;
? 自动制动手柄和单独制动手柄安装在操纵台面上;
? 两个手柄均以远离司机(推)的方向移动作为制动作用,以靠近司机(拉)的方向
移动为缓解作用;
? 自动制动手柄在操作时有明显的位置感,运转、最小制动位、制动区、最大制动位、
抑制位、重联位及紧急制动位等位置明确;
? 单独制动手柄在操作时有明显的位置感,有运转位、制动区和最大制动位; ? 单独制动手柄具有单缓操作功能,并且单缓后手柄能自动复位。 7.3.3.2 紧急制动阀:
紧急制动动作还能够通过执行司机室内独立的紧急制动-阀(带手把)进行,紧急制动-阀能大通量地排出列车管的压力空气,触发机车紧急制动作用。 7.3.3.3 显示器:
? 在机车司机操纵台上有显示器显示制动系统的相关信息;
? 与制动相关的诊断功能、自检、校准、故障和事件标记允许通过显示器来执行。 7.3.3.4 压力表:
? 机械压力表用于在司机室的显示;
? 在压力表检定使用期限内,其显示的测量数据正确。压力表精度不低于1.5级; ? 总风管和列车管的压力显示(双针)压力表; ? 两个转向架的制动缸压力显示(双针)压力表; ? 压力表应带有110 V的照明。
35
? ? ? ?
TJ/JW012—2014
7.3.4 制动系统的硬件接口
制动系统的硬件接口见表1。 7.3.5 LOCOTROL的接口
7.3.5.1 预留安装机车无线远程控制系统(LOCOTROL)的安装位置和布线空间。
7.3.5.2 有、无使用机车无线远程控制系统(LOCOTROL)系统时,都确保制动系统所有必需的功能。
表1 制动系统硬件接口
内 容 紧急制动 ATP(LKJ05)惩罚 零速 动力制动互锁 无人警惕 常用 紧急 得电激活 得电激活 得电激活 机车在逻辑零速度(0.5km/h)时指示 动力制动激活 采用常用制动 说 明
7.4 基础制动系统 7.4.1 基础制动形式
采用装有制动盘的车轮,每个车轮有制动缸和制动卡钳,作用于安装在车轮两侧的制动盘上。
7.4.2 单元制动缸
7.4.2.1 数量3直径为83φ203 mm+43φ254 mm。 7.4.2.2 带有闸片间隙自动调整装置。 7.4.2.3 制动闸片的更换简便。
7.4.2.4 基础制动装置传动效率(紧急制时)大于0.95。 7.4.2.5 机车空气制动率为23.5%。 7.4.3 停放制动单元
7.4.3.1 每转向架个数为2。 7.4.3.2 停放制动率为12.2%。
7.4.3.3 保证在30‰坡道上安全停放。 7.4.4 制动单元闸片
7.4.4.1 闸片的材料为合成。
7.4.4.2 闸片的平均摩擦系数为0.35。 7.4.4.3 磨耗及使用寿命为19 mm。 7.4.4.4 闸片温度限值为350 ℃。 7.4.4.5 轮盘温度限值为峰值600 ℃。
7.4.4.6 摩擦系数与制动初速度、磨合情况、闸片压力、温度和大气条件无关。 7.5 撒砂系统
7.5.1 砂箱的数量和布置
7.5.1.1 每转向架数量为4个。 7.5.1.2 砂箱容积为35 L。
7.5.1.3 砂箱盖严密防潮,能防止雨雪侵入。 7.5.2 撒砂管出口
36
TJ/JW012—2014
撒砂管出口部分采用橡胶管,出砂口最低点距轨面25 mm~30 mm;距车轮踏面最近点15 mm~30 mm。
7.5.3 砂子的规格要求
使用砂子的规格要求砂子符合TB/T 3254—2011中的相关规定。 7.5.4 撒砂控制
7.5.4.1 撒砂量为0.3 L/min ~0.7 L/min。 7.5.4.2 应有砂子烘干系统。
7.5.4.3 撒砂喷嘴的位置和形状要保证砂粒能正确撒在车轮踏面与钢轨相交处。 7.5.4.4 机车撒砂系统与空气制动、防空转滑行等装置配合动作。 7.5.4.5 可以通过司机室里撒砂脚踏开关实施撒砂。 7.6 可维护性
7.6.1 系统设计、原材料选择以及质量流程减少用于检查、维护、测试以及维修的时间和费用。
7.6.2 部件要求定期维护、检查且易从机车上拆除及更换。 7.6.3 同一车型上同一型号的部件能相互替换。
7.6.4 尽量避免对部件的调整,但在产品设计时考虑用户的环境要求。 7.6.5 管路及管路连接系统8年免维修,各种阀类和制动缸8年免维修,各类电子或电气件4年免维修。
8 司机室技术要求
8.1 综述
8.1.1 机车有两个具有同样操作功能的司机室,分别设在机车前后端。 8.1.2 司机室的结构和设备布置符合人机工程学的要求,适于单司机执乘,便于司机操作和日常的检查维修,司机室内宽敞明亮,司机能方便地接近司机室内的每一个部位。 8.1.3 司机室有良好的照明。
8.1.4 司机室具有良好的了望条件。
8.1.5 司机室设有空气温度调节及取暖装置。 8.1.6 司机室具有保护工作人员的安全措施。
8.1.7 司机室的顶棚、侧墙、地板有隔热保温性能。
8.1.8 司机室的噪音按照UIC 651:2002规定的检测方法测试,不超过75 dB(A)。 8.2 司机室布置
8.2.1 司机室结构满足UIC 651:2002中2.2的规定。 8.2.2 司机室的尺寸满足UIC 651:2002中2.1的规定。 8.2.3 司机室瞭望条件满足GB 5914.1—2000 的相关要求。 8.2.4 司机室内操纵台、侧墙、车门、地板和顶棚的色彩反射系数符合UIC 651:2002中2.12的规定。
8.2.5 除了满足上述要求外,司机室还符合UIC 617-6:1977的相关要求。 8.3 司机操纵台布置 8.3.1 布置总则
8.3.1.1 操纵台的设计考虑到乘务人员的身材及其所执行的操作任务(操纵相关的设备及显示器)。
8.3.1.2 操纵台的布置能方便司机就坐及移动双腿,也能够让司机站着操纵。
8.3.1.3 所有与运行有关的操纵装置、仪表、显示屏、操控开关、带转换、调节性的开关以及各种按钮等均布置在操纵台主台面上。
8.3.1.4 气候控制开关、辅助开关、作业转换开关布置在操纵台主台司机右侧立柱面板上;
37
TJ/JW012—2014
操纵台副台台面上仅设置一风笛按钮。
8.3.1.5 操纵台/座椅配合及推荐尺寸采用UIC 651:2002中附录8的配置方案。 8.3.1.6 操纵台台面的材质采用环保材料。 8.3.1.7 操纵台的表面结构不会产生镜面效果,操纵台上的可视显示板、操纵台的其他部位、周围环境的亮度比分别为1:3:10。 8.3.2 具体分区
8.3.2.1 制动区的布置:
? 制动状态显示屏(与主显示屏合并),作为其备用显示的两块压力表(总风缸/列车管,
制动缸/制动缸)布置在制动区;
? 与空压机、制动状态有关的开关、按钮也布置在制动区内。 8.3.2.2 运行区的布置:
? ATP显示屏; ? 双针速度表;
? 机车状态指示灯布置在双针速度表的下方;
? 各种操控开关、各种照明开关、标志灯开关布置在运行区内。 8.3.2.3 牵引区的布置:机车的状态以显示屏或仪表的形式显示在牵引区;启动程序开关和按钮布置在牵引区内。
8.3.2.4 司机控制器/空气制动阀的选型与布置充分考虑司机有足够的置腿空间和记点平台面积;风笛按钮布置在司控器附近。
8.3.2.5 气候区设在操纵台主台右侧立柜面板上,板上布置刮雨器、空调、采暖、前窗玻璃加热等转换开关;前窗玻璃喷水按钮以及电源插座等器件。 8.4 司机室照明
8.4.1 司机室总照明系统的光照度,在地板面上始终具有30 lx,在司机操纵台面上始终具有60 lx。当蓄电池总开关断开后,司机室仍保留足够的光照,以便乘务人员能方便地观察和走动。
8.4.2 仪表灯和记点灯的照明为不眩目的光色,与一般照明光色有所区别。当采用附加照明时,这些灯光也不使司机感到刺眼。
8.4.3 司机室照度的检测按TB/T 2011—1987执行。
8.4.4 除了满足上述要求外,还应符合UIC 651:2002中2.8的相关要求。 8.5 司机室设备
司机室至少包括以下设备。 8.5.1 前窗(玻璃、刮雨器、遮阳帘)
8.5.1.1 前窗玻璃:
? 采用分层电加热玻璃,有除霜、加热功能,玻璃与钢结构采用胶粘接。 ? 采用安全防碎玻璃,其抵抗冲击性要求符合UIC 651:2002中的相关要求。 ? 物体的冲击试验按UIC 651:2002中相关规定执行,允许最大的列车速度为140 km/h。 ? 前窗玻璃避免反射和高热量传递,不使观察景象畸变,同时具有良好的隔热以防止
正常情况下凝结和结冰。 ? 前窗玻璃尽可能的降噪。
8.5.1.2 采用电动刮雨器,带有喷淋装置。刮刷面积符合司机视野要求。 8.5.1.3 前窗设有可调遮阳装置。
8.5.1.4 除了满足上述要求外,还应符合GB 5914.2—2000的规定。 8.5.2 侧窗
8.5.2.1 侧窗采用安全防碎玻璃,符合UIC 651:2002的相关要求。
8.5.2.2 侧窗开启的时候,司机可以探身出去观察列车。在紧急情况下,司机能够打破侧窗玻璃经侧窗逃离司机室。
38
TJ/JW012—2014
8.5.2.3 除了满足上述要求外,还应符合GB 5914.2—2000中相关的规定。 8.5.3 后视镜
8.5.3.1 侧窗外装有手动后视镜,每侧一个。 8.5.3.2 后视镜可以进行手动调节。
8.5.3.3 当后视镜打开处于正常工作位时满足可视性和机车限界的要求。 8.5.4 司机室门及锁具
8.5.4.1 每个司机室两侧设有带锁的入口门,门有专用的钥匙才能打开,且4个入口门用1把钥匙打开。
8.5.4.2 司机室通过走廊门与机械间相连接,入口门及走廊门符合机车密封性要求。 8.5.4.3 司机室门尺寸符合GB 6770—2000中的相关规定。 8.5.5 司机座椅
8.5.5.1 司机室内两侧各设一个司机座椅, 该座椅有足够的稳定性,能进行上下、前后及转动的调节,并在转动范围不碰及其他设备。
8.5.5.2 司机座椅的设计可让司机在必要时迅速离开司机室。司机座椅的设计允许司机根据需要站着操纵。
8.5.5.3 司机室内提供两把固定式折叠座椅(添乘座椅),置于司机室后墙上。 8.5.5.4 满足上述要求之外,按UIC 651:2002中第5章相关要求执行。 8.5.6 空调装置(制冷+加热)
司机室设有空调及取暖装置,空调具有制冷、空气过滤和补新风作用。双端司机室空调可同时工作,单独控制。
除满足上述要求之外,还符合UIC 651:2002中2.9的相关要求。 8.5.6.1 机车空调技术参数:
? 额定功率为6.2 kVA; ? 电压为33460 V; ? 制冷量为5.8 kW;
? 空气过滤器形式为人造滤网。 8.5.6.2 取暖装置:
? 结构形式为集成在空调内的加热器,5.4 kW(电压33460 V); ? 独立的对流加热器,331.5 kW;
? 地板加热器(2个加热板)(可选项), 231 kW; ? 脚炉为230.5 kW; ? 膝炉为230.3 kW; ? 电压为220 V;
? 司机室空调装置的工作不能受压缩机工作的影响,司机室空调和司机室温度加热装
置的控制分别进行。 8.5.7 司机室内装饰
8.5.7.1 司机室内部装饰采用无毒、阻燃材料。 8.5.7.2 地板平坦。
8.5.7.3 地板覆盖防滑易清洁的材料。 8.5.7.4 地板具有阻燃、防滑和吸音特性。
8.5.7.5 燃烧特性满足UIC 564-2中的相关要求。 8.5.8 脚蹬、扶手
机车上设有脚蹬、上车扶手,该装置满足UIC 651:2002中2.4、2.5的相关要求。
39
TJ/JW012—2014
9 其他技术要求
9.1 下述设备按照安装要求预留安装位置和接口:
a) TMIS车号识别设备:双向电子标签和车载标签编程器(装在机车安全信息综合监测
装置内);。
b) 机车安全信息综合监测装置(TAX2型); c) LKJ型列车运行监控记录装置; d) LAIS车载设备(无线车载传输设备);; e) J T-C系列机车信号车载系统设备;
f) 机车综合无线通信设备(CIR);
g) 机车远程监视与诊断系统(CMD系统)。 9.2 机车标识及标记
机车标识及标记按照GB/T 25333—2010要求执行。 9.3 生活设施
9.3.1 饮水及食品加热设备
司机室内设有冰箱和水、食物加热装置,使用AC 230 V电源。 9.3.2 卫生设施
机车车载卫生间:
a) 机车车载卫生装置是集洗手、集便、排风、低温加热为一体的机车设备,采用
非直排式结构,排泄物独立收集处理,框架式结构卫生间,应具有集便器、水箱、水箱液位检测开关和加热防冻装置、污物箱(肥料箱)、状态显示面板及故障报警装置、取暖器、通风排气扇、洗手台、节水水龙头、照明灯、废物收集装置、地漏、冲洗开关、排气照明开关、扶手等设施。 b) 内部净空高度不应小于1800 mm。
c) 主门宽度不应小于450 mm,高度不应低于1700 mm。
d) 卫生间箱体采用框架式结构,能满足整体吊装、拆卸和机车正常运行工况的强度及
刚度要求,整体起吊时结构无塑性变形,弹性变形不应大于3 mm。 e) 卫生间框架壳体要满足保温及隔音要求。
f) 在实现收集污物的同时,还应具有面板状态显示、照明、排风、取暖、加热器加热、
排污管加热(如有)、集便器故障和污物箱满载报警功能。
g) 上水管注水口要求:上水管注水口如图6所示,材料为KTH300-06或QT450-10,表
面涂防锈漆。
图6 上水管注水口
h) 卸污口要求(如有):卸污口应采用不锈钢材质,卸污口接头型式尺寸应符合
EN 14420-7:2007的表A.1中DN65的要求。
i) 卫生装置内的各部件表面应不易污染并易于清洗,采用的非金属材料阻燃性应符合
40
TJ/JW012—2014
TB/T 3138—2006中的相关规定。
j) 水箱、污物箱容量要求:一次整备后至少可连续使用40次。 k) 卫生间通风方式要求废气直接排出车外。 9.3.3 其它设施
司机室内设有至少两个衣帽钩,布置在司机室后墙上适当的位置上。能够承担10 kg的重量。
司机室设置烟灰缸。烟灰缸设在司机易于触及的地方。 10 检验要求
对机车的质量、规格和性能等进行准确全面的检验,含出厂检验和型式检验。 10.1 出厂检验
机车及主要部件通过出厂检验,结果能符合本文件及相关要求。 10.2 型式检验
10.2.1 机车及主要部件通过型式检验,结果符合本文件及相关要求。
10.2.2 机车整车、系统及主要部件异地生产或进行重大设计修改及重大工艺调整,须重新做型式检验。
10.2.3 承担型式检验的单位具有相应资质。
10.2.4 对已通过型式检验、并有批量装车实绩的部件,可提供符合本型机车相关技术要求的有效型式检验报告或证明材料。
10.2.5 未做型式检验或型式检验未能符合全部要求的部件不得装车。
10.2.6 主要部件(包含但不限于以下部件)为受电弓、高压电压互感器、高压电流互感器、避雷器、真空主断路器、受电弓隔离开关、主变压器、牵引变流器、牵引电机、辅助变流器、主辅变流功率模块、辅助电机、微机控制系统(含网络)、蓄电池、蓄电池充电器、各类开关电器、通风机组、散热器、司机室空调装置、司机室前窗雨刷装置、司机控制器、车体、转向架构架、基础制动装置(含单元制动器、闸片、制动盘)、空气压缩机、压缩空气净化干燥装置、制动机、车轮、车轴、轴箱、一系悬挂弹簧、二系悬挂弹簧、各类减振器、牵引电机轴承、轴箱轴承、滚动抱轴承、传动齿轮及联轴节、齿轮箱、车钩及缓冲装置、卫生间、6A系统装置。
11 RAMS要求
按EN 50126进行产品各阶段的可靠性分析。
按IEC 60300-3-3开展产品全寿命周期成本分析。
41
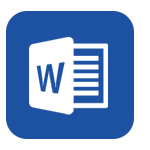





正在阅读:
TJJW 012-2014 HXD3B型电力机车总体技术规范(报批稿)04-19
秋冬男装搭配技巧 - 图文02-27
ExcelVBA编程实例(150例)05-22
石家庄学院内刊 - 图文05-19
不要走得太急02-10
使用普通电烙铁焊接铝材和不锈钢的简易方法07-29
弟弟上学了作文800字06-24
WebSphere MQ 命令11-16
花没开过,我没来过、你没走过,花没见过09-30
- 多层物业服务方案
- (审判实务)习惯法与少数民族地区民间纠纷解决问题(孙 潋)
- 人教版新课标六年级下册语文全册教案
- 词语打卡
- photoshop实习报告
- 钢结构设计原理综合测试2
- 2014年期末练习题
- 高中数学中的逆向思维解题方法探讨
- 名师原创 全国通用2014-2015学年高二寒假作业 政治(一)Word版
- 北航《建筑结构检测鉴定与加固》在线作业三
- XX县卫生监督所工程建设项目可行性研究报告
- 小学四年级观察作文经典评语
- 浅谈110KV变电站电气一次设计-程泉焱(1)
- 安全员考试题库
- 国家电网公司变电运维管理规定(试行)
- 义务教育课程标准稿征求意见提纲
- 教学秘书面试技巧
- 钢结构工程施工组织设计
- 水利工程概论论文
- 09届九年级数学第四次模拟试卷
- 电力机车
- 报批
- 技术规范
- 总体
- HXD3B
- TJJW
- 2014
- 012
- 冲压课程设计说明书 - 图文
- 1515P1037《西方会计》
- 2015-2016化学实验教学计划(下)
- 4R项目培训心得
- 模电课后(康华光版)习题答案4
- 小学班主任工作热点及难点问题
- 2017年云南省接受军转干部安置考试
- 小学三年级语文期末考试质量分析
- 备战2012中考:中考语文古诗词赏析精华试题汇编
- 2017新苏教版一年级语文下册课文填空(全版)
- 浙江省永嘉县2013届初中毕业生第一次适应性考试英语试题 2
- 浙大《 数字电子技术基础》课程期末考试试卷
- 麒麟区2011年公交城乡一体化
- 岳麓版必修1第15课《辛亥革命》word学案
- 《入党志愿书》本人填写部分模板、要求、方法、注意事项(1)
- 中级保育员培训实操练习题61
- 工程咨询继续教育考试城市道路标准体系及主要规范介绍80分
- 多媒体技术基础 电大网上作业1(平时作业一)
- 建筑施工企业将工程劳务发包给不具备用工主体资格的组织或自然人
- 塑胶电镀件检验标准