模具设计专业课程设计-支架的冲孔落料级进模设计
更新时间:2023-05-22 16:02:01 阅读量: 实用文档 文档下载
- 冲压模具设计课程设计推荐度:
- 相关推荐
模具设计专业课程设计
前言
改革开放以来,随着国民经济的高速发展,市场对模具的需求
量不断增长。近年来,模具工业一直以15%左右的增长速度快速发展,模具工业企业的所有制成分也发生了巨大变化,除了国有专业模具厂外,集体、合资、独资和私营也得到了快速发展。近年许多模具企业加大了用于技术进步的投资力度,将技术进步视为企业发展的重要动力。一些国内模具企业已普及了二维CAD,并陆续开始使用UG、Pro/Engineer、I-DEAS、Euclid-IS等国际通用软件。虽然中国模具工业在过去十多年中取得了令人瞩目的发展,但许多方面与工业发达国家相比仍有较大的差距。例如,精密加工设备在模具加工设备中的比重比较低;CAD/CAE/CAM技术的普及率不高;许多先进的模具技术应用不够广泛等等,致使相当一部分大型、精密、复杂和长寿命模具依赖进口。
导柱式冲裁模的导向比导板模的准确可靠,并能保证冲裁间隙的均匀,冲裁的工件精度较高、模具使用寿命长,而且在冲床上安装使用方便,因此导柱式冲裁模是应用最广泛的一种冲模,适合大批量生产。尤其是在我国加入WTO之后,在全球化经济竞争的市场的环境下,为生产符合“交货期短”、“精度高”、“质量好”、“价格低”等要求服务的模具产品,研究、开发、改进模具生产设备与模具设计方式更具有深远的现实意义和紧迫性。
模具设计专业课程设计
目录
一.前言 1 二.任务书 3 三.工艺分析 4 四.工艺方案的确定 4 五.冲孔落料工作部分 工艺设计
1.计算毛坯尺寸 5
2.画排样图 6 3.计算冲压力 8 4.计算中心压力 9 5.凸凹模刃口尺寸的计算 9 6.压力机的选择 11 7.落料冲孔级进模部分尺寸校核 12
六.弯曲模工作部分 工艺计算
1.弯曲工件的毛坯尺寸计算 14
2.弯曲力计算 15 3.凸模与凹模的圆角半径 15 4.弯曲模凸凹模间隙 17 5.凸、凹模工作尺寸 18 6.冲压设备的选择 19
模具设计专业课程设计
7.模具的总体结构 20 8.主要零部件的设计及选择 21 9.模具制造装配要点 23
八.心得与体会 24 九.参考文献 26
任务书
一、课题名称:支架的冲孔落料级进模设计 二、工件图:
三、设计要求:
模具设计专业课程设计
1.绘制该工件制作所需的模具总装图。(A1图纸) 2.绘制该模具的凸模、凹模零件图一套。 3.编写完整的设计说明书。
4.将说明书装订成册,各图纸折成A4大小。
5.将以上所有资料装于档案袋里,并在封面写上班级、名字和学号。
四、设计期限:2007年6月25日 至2007年6月29日
工艺分析
该制件形状简单,尺寸较小,厚度适中,一般批量,属于普通冲压件,应注意以下几点:
1)2XΦ4.5mm两孔壁距及周边距仅2.25~2.5mm,在设计模具时应加以注意
2)制件为对称弯曲,控制回弹是关键
3)制件较小,从安全上考虑,要采取适当的取件方式 4)有一定的批量,应该重视模具材料和结构的选择,保证一定的模具寿命
工艺方案的确定
根据制件工艺性分析,其基本工序有落料、冲孔和弯曲三种。按其先后顺序组合,可得如下方案
1.冲孔—落料—弯曲 级进模完成冲孔落料,单工序模完成弯曲
模具设计专业课程设计
2.落料—冲孔—弯曲 单工序模分别完成落料,冲孔,弯曲 方案2)属于单工序冲压。由于此制件生产批量较大,尺寸较小,这种方案生产率低,操作不安全,故不宜采用。
方案1)冲裁件内外所能达到的经济精度为IT14.将以上精度与零件简图中所标注的尺寸公差相比较,可认为该零件的精度要求能够在冲裁加工中得到保证.其它尺寸标注、生产批量等情况,也均符合冲裁的工艺要求,故决定采用利用导板或导柱导套进行定位、刚性卸料装置、自然漏料方式的落料冲孔级进模进行加工.
工艺设计
1)计算毛坯尺寸 相对弯曲半径为 R/t=1/0.8=1.25>0.5 式中 R——弯曲半径(mm) T——料厚(mm)
可见,制件属于圆角半径较大的弯曲件,应先求弯曲变形区中性层曲率半径p(mm)。由文献[2]中性层的位置计算公式
P=R+Xt
式中 X——由实验测定的应变中性层位移系数。 由文献[2]表4-4应变中性层位移系数X值,查出X=0.34 P=(1+0.34×0.8)=1.272mm
模具设计专业课程设计
由文献[3]圆角半径较大(r>0.5t)的弯曲件毛坯长度计算公式 L=l1+l2+πα/180*(r+xt) 式中 L——毛坯展开总长度 α——弯曲中心角()
x——中心层位移系数,见表4-7 由图1可知
L=2(l1+l2)+l3+4πα/180*(r+xt) 查表4-5,当r/t=1.25时,x=0.34,可得
L=4+2×(7.95+4.4)+4×π90/180×(1+0.34×0.8)
=28.7+7.998=36.688≈37(mm) 图1
2)画排样图
(1)冲裁件的面积
分析零件的形状特点及精度要求,考虑采用采用直排有废料排样方式, 如图2所示
.
图2 冲裁件
计算冲裁件的面积A
A=36.688×9-2π r≈-(9×9-πR²)
=36.688×9-2×3.14×2.25²-(9×9-3.14×4.5²) =330.192-31.7925-17.415
模具设计专业课程设计
=280.9845mm²
(2) 搭边值、切口宽与条料宽度的确定
由文献[3]表3-17条料宽度公差△、表3-18侧刃裁切的条料的切口宽F,得
F=0.5mm △=0.15
由文献[3]表3-16搭边值的确定,得 a1=0.8 a=1.0
本设计中采用侧刃定距的模具,故按下式计算: 条料宽度 B0-△=(Dmax+2a+nb1)0-△ 导料板间的距离 A=B+Z=Dmax+2a+nb1+Z
其中查表3-1703-18得: 保证间隙Z=0.55mm,条料宽度的单向负偏差△=0.15mm。
条料宽度:B10-△=(Dmax+2a)0-△=(36.688+2*1+2*1.5)0-0.15=410-0.15 步距:S=9+0.8=9.8
导料板间的距离:A1=B+Z=Dmax+2a+Z=36.688+2*1+2*1.5+0.55=41.55mm
模具设计专业课程设计
图3排样图
查文献[1]表4-1,选板材规格为1200mmX600mmX0.8mm,每块可剪600mmX41mm,材料剪裁利用率达99.9% 3)材料利用率计算
由文献[2]材料利用率通用计算公式: =A。/AX100%
式中 A。——得到制件的总面积(mm²) A——一个步距的条料面积(LXB)(mm²) 得 =280.9845/(9.6*41.55)X100%=70.44%
3)计算冲压力
(1)冲裁力F冲
F冲=Lt бb或F冲=KLtτ。
模具设计专业课程设计
式中 K——系数,K=1.3 L——冲裁周边长度(mm) τ。——材料的抗剪强度(MPa) бb——材料的抗拉强度(MPa)
得 бb=295~430(MPa)(为方便计算,取400(MPa)) F冲=400*0.8*(2*4.5*3.14+9*3.14+2*28+2*9+5)N =43.3KN (2)卸料力
F
卸
K卸F
根据《冷冲压模具设计与制造》(北京航空航天大学出版社,王秀凤主编)提供的表2.10得K卸 0.05
F卸=0.05*43300N=2165N (3)顶出力
F
顶
K顶F
根据《冷冲压模具设计与制造》(北京航空航天大学出版社,王秀凤主编)提供的表2.10得
K
顶
0.08
F顶=0.08*43300N=3464N
(4)选择冲床时的总冲压力:
F总=F冲+F卸+F顶=43300+2160+3464=48924N 初选压力机 查文献[2]表1-8开式双柱可倾压力机参数,型号规格为
模具设计专业课程设计
J23-25
4)计算压力中心
因冲裁件尺寸较小,冲裁力不大,且选用了双柱导柱式模架,估计压力中心是在模架的中心,不会超出模柄端面之外,因此不必详细的计算压力中心的位置
5)计算凸、凹模尺寸:
本制件形状简单,可按配作法加工计算刃口尺寸。
由于零件是由冲孔、落料两道工序完成的,所以落料以凹模为基准尺寸,冲孔以凸模为基准尺寸,计算如下: 1)凹模磨损后变大的尺寸(IT14) A1(27),A2(9)A3(R4.5) 计算公式为:
查表3-8得x1=x2=x3=0.5
图
4
模具设计专业课程设计
2)凸模磨损后变小尺寸 B凸1=Φ4.5 计算公式为
由文献[3]表3-4冲裁模初始双面间隙Z得到Zmin=0.072
Zmax=0.104,落料凸模刃口尺寸按凹模实际刃口尺寸配作,冲孔凹模刃口尺寸按凸模刃口尺寸配作,保证双面间隙值0.072mm~0.104mm。 3)侧刃尺寸:
侧刃为标准件,根据送料步距和修边值查侧刃表,按标准取侧刃小尺寸。
由文献[4]表5-32侧面切口值尺寸得 侧刃宽度B=6mm, L=50mm 间隙取在凹模上,故侧刃孔尺寸为: B=6.12 (mm) L=50.12
(mm)
压力机的选择
根据压力机选用原则:
模具设计专业课程设计
在中小型冲压件生产中,主要选用开式压力机
对于冲孔,落料等施力行程很小的冲压工序,可直接选用公称压力大于或等于冲压所需工艺力总合的压力机。
首先冲床的公称压力应大于计算出的总压力;最大闭合高度应大于冲模闭合高度+5mm;工作台台面尺寸应能满足模具的正确安装。按上述要求,结合工厂实际,可称用J23-15开式双柱可倾压力机。并需在工作台面上配备垫块,垫块实际尺寸可配制。 双柱可倾压力机J23-25参数: 公称压力:250KN 滑块行程:65mm 最大闭合高度:270mm 连杆调节量:55mm 工作台尺寸(前后垫板尺寸(厚度模柄尺寸(直径最大倾斜角度:
×左右):50mm ×深度
):Φ40×60 ):370×560
冲孔落料级进模部分尺寸校核 1.冲孔落料级进模模总图
模具设计专业课程设计
图5装配图 2凸模外形尺寸的确定
1.凸模结构基本类型 冲裁中小型零件使用的凸模,一般都设计
成整体式,本凸模采用阶梯式,固定部分采用凸缘式,固定方式采用固定板固定。
2.凸模长度 采用固定卸料板,故凸模长度应按下式计算: L=h1+h2+h3+h
式中 h1——凸模固定板厚度,取50mm。 h2——固定卸料板厚度,取20mm。 h3——导料板厚度,取8mm
h ——增加厚度,取30mm。
模具设计专业课程设计
则,凸模长度 L=50+20+8+30=108mm 3其他主要零部件结构
凸模固定板100×90×45mm; 下模卸料板100×90×18mm; 4闭合高度计算
H=50+90+20+30-5=185mm, 90mm为凸模长度,-5mm是考虑
弯曲模具工作部分
工艺计算
1.弯曲工件的毛坯尺寸计算
根据原始数据可得 t =0.8 r =1
所以r/t =1/0.8 = 1.25 >0.5
所以 根据《冷冲压工艺及模具设计》4-4 得 L= l直1 + 2(l直2 +l直3)+4l弯 L直1=6-2=4mm
L直2=9.75-1-0.8=7.95mm L直3=8-2×0.8-2×1=4.4mm
L弯 =лα(r+xt)/180=л90(1+0.34×0.8)=1.997 所以L=4+2(7.95+4.4)4×1.997=36.688mm
式中
L直1 l直2 l直3 —直边区长度 L弯—弯曲部分长度
模具设计专业课程设计
r—零件内弯曲半径 α—弯曲中心角
k— 中性层内移系数值。取0.34
《冷冲压工艺及模具设计》表4-7 t—弯曲件厚
2.弯曲力计算
弯曲力受材料力学性能,零件形状与尺寸,弯曲方式,模具结构形状与尺寸等多种因素的影响,很难用理论分析方法进行准确计算。因此,在生产中均采用经验公式估算弯曲力。 F校= AP
= 9×25.5×80MPa =18.36KN 式中:F校—校正弯曲力 A—校正部分投影面积 P—单位面积校正力
根据《冷冲压工艺及模具设计》表4-7 取0.34
3.凸模与凹模的圆角半径
(1)凸模圆角半径
弯曲件的相对弯曲半径r/t较小时,凸模角半径rp可取弯曲件的内弯曲半径r,但不能小于允许的最小弯曲半径。如果r/t值小
模具设计专业课程设计
于最小相对弯曲半径,应先弯成较大的圆角半径,然后再用整形工序达到要求的圆角半径。当弯曲件的相对弯曲半径r/t较大且精度要求较高时凸模圆角半径应根据回弹值进行修正。
由于影响rmin/t的因素很多,rmin/t值的理论计算公式并不实用。所以在生产中主要参考经验数据来确定rmin/t值。由《冲压工艺与模具设计》表4-1可查得:10钢最小相对弯曲半径rmin/t=0.8 (2)凹模圆角半径
凹模的圆角半径rd 不能过小,以免增加弯曲力,擦伤工件表面。对称压弯时两边凹模圆角半径rd应一致,否则毛坯会产生偏移 rd值通常按材料厚度t来选取 t=0.8mm < 2mm 时rd=(3~6)t 取rd=4 (3)凹模深度
凹模的工件深度将决定板料的进模深度,对于常见的弯曲件,弯曲时不需全部直边进入凹模内。只有当直边长度较小且尺寸精度要求高时,才使直边全部进入凹模内,凹模深度过大,不仅增加模具的消耗,而且将增加压力机的工作进程,使最大弯曲力提前出现。中小型弯曲件通常都使用模具在机械压力机上进行加工,最大弯曲力提前出现,对压力机是很不利的。凹模深度过小,可能造成弯曲件直边不平直,降低其精度。因此,凹模深度要适当。由《冲压工艺与模具设计》表4-12可得
L0=15
模具设计专业课程设计
4.弯曲模凸凹模间隙
弯曲
形时,必须选择适当的凸凹模间隙。间隙过大,会造成U
形件两边不半径,上宽下窄,降底工件的尺寸精度, 间隙过小,使弯曲力增大,直边壁厚变薄,容易擦伤工作表面,加速凹模的磨损,降低凹模使用寿命,弯曲凸、凹模间隙是指单边间隙。为了能顺利地进行弯曲,间隙值应梢大于板料的厚度。同时应考虑下列因素的影响,弯曲件宽度较大时,受模具制造与装配误差的影响,将加大间隙的不均匀程度,因此间隙值应取大些。宽度较小时间隙值可以取小些,硬材料则应取大些,弯曲件相对弯曲半径r/t较小时可以取大些。此外还应考虑弯曲件尺寸精度和板料厚度偏差的影响
综上所述,对于尺寸精度高要求一般的弯曲件板料为黑色金属时,单边Z可按下式计算: Z= tmax +Ct =0.87+0.05×0.8 =0.91
取单边间隙为0.92mm 式中:tmax——板料最大厚度 C——间隙系数,见表4-14 t板厚公称值
模具设计专业课程设计
5.凸、凹模工作尺寸
弯曲凸、凹模工作尺寸的计算与工件尺寸的标注形成有关。一般原则是:当工件标注外形尺寸时,应以凹模为基准件,间隙取在凸模上,当工件标注内行尺寸时,应以凸模为基准件,间隙取在凹模上,并来用配作法制模。
综上所述:
Lp =(L+0.75△)0
-δ
p
=(6+0.75×0.62)0
-0.018 =6.4650-0.018(mm) 式中 Lp凸模宽度基本尺寸 L工件横向基本尺寸
△工件横向尺寸公差
δd凸模制造偏差,一般取IT7~9级,或取工件公差的~1/4。
1/3、
模具设计专业课程设计
6.冲压设备的选择
因工件是大批量生产,精度要求不高冲裁力较小则选用通用压力机,通用机身又分开式和闭式两种,开式机身的钢性教弱,适用中小型冲压加工,而闭式机身适用于大中型冲压加工。选用开式双柱可倾压力机JA23—10 其参数如下:
公称压力 100KN 滑块行程 45mm 行程次数 145/min 最大封闭高度 180mm 封闭高度调节量高度 工作台尺寸 360 垫板厚度 35mm 电动机功率 1.10KW 模柄孔尺寸
×240mm φ30×55 35mm
模具设计专业课程设计
7.模具的总体结构
模具采用中间导柱模架,模具由上模板、凸模固定板组成。卸料方式才用弹性卸料,以橡胶为弹性元件。下模部分由下模座、凹模板、导板垫板等组成。 模具结构如下图所示
1.橡胶块 2.销钉 3.导板 4.凹模 5.定位板 6.凸模固定板 7.垫板 8.螺钉 9.模柄 10.上模座 11.导套 12.凸模 13.顶件块 14.导套 15.下模座
模具设计专业课程设计
8.主要零部件的设计及选择
(1)凸模的固定方法
凸摸在上模的正确固定应该是既保证凸摸工作可靠和良好的稳定性,还要使凸摸在更换或修理时,拆装方便。该凸摸的固定方式选用如下图所示的固定方法。
(用螺钉固定的落料凸模)
(2)定位板的设计
定位板的侧壁设计成平直的。定位板的内侧与条料接触,外侧与凹模平齐,这样就确定了定位板的宽度。条料的宽度为9mm,凹模的宽度是70mm。则定位板的宽度为:
B=9.4mm
定位板厚度:2㎜
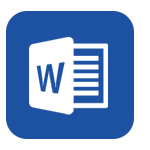





正在阅读:
民族理论与民族政策试卷02-21
immune cell 免疫细胞08-17
一场精彩的篮球比赛作文500字06-25
2017年初级会计实务练习题09-25
低压智能化管理的应用12-17
汽车采样机使用及维护说明书04-08
第二章有理数同步练习题05-26
java部分06-19
- 教学能力大赛决赛获奖-教学实施报告-(完整图文版)
- 互联网+数据中心行业分析报告
- 2017上海杨浦区高三一模数学试题及答案
- 招商部差旅接待管理制度(4-25)
- 学生游玩安全注意事项
- 学生信息管理系统(文档模板供参考)
- 叉车门架有限元分析及系统设计
- 2014帮助残疾人志愿者服务情况记录
- 叶绿体中色素的提取和分离实验
- 中国食物成分表2020年最新权威完整改进版
- 推动国土资源领域生态文明建设
- 给水管道冲洗和消毒记录
- 计算机软件专业自我评价
- 高中数学必修1-5知识点归纳
- 2018-2022年中国第五代移动通信技术(5G)产业深度分析及发展前景研究报告发展趋势(目录)
- 生产车间巡查制度
- 2018版中国光热发电行业深度研究报告目录
- (通用)2019年中考数学总复习 第一章 第四节 数的开方与二次根式课件
- 2017_2018学年高中语文第二单元第4课说数课件粤教版
- 上市新药Lumateperone(卢美哌隆)合成检索总结报告
- 冲孔
- 设计
- 专业课程
- 模具设计
- 支架
- 《房地产估价相关知识》模拟试卷(一)
- 三门峡市陕州区五年级下学期英语期末质量监测试卷
- 聪明排湿气轻身一夏天
- 消防控制室火灾事故紧急处理程序123456
- 幼儿园家长助教心得
- 最新游园活动方案范文(1)
- 31.《快乐王子》1
- 2第2章 国际货币制度习题答案
- 安捷伦中高端示波器
- 龙门起重机安全操作规程
- 领导理念和领导艺术
- 三门峡市陕州区五年级英语(上册)期中考试试卷
- 《气学中医简介小册子》二.气学五行
- 7光的折射与全反射(一)
- 淘金热gold rush淘金者gold miners
- 动漫人物生日大全
- 江苏省木渎高级中学高二语文期末模拟试卷及试卷分析
- wingdings字体,webdings字体,RGB颜色对照表
- 04 第四章 组织结构与设计
- 七年级英语词汇竞赛试题1