煤气终冷洗苯工艺比较
更新时间:2023-09-18 18:35:01 阅读量: 幼儿教育 文档下载
- 煤气洗苯后苯含量标准推荐度:
- 相关推荐
煤气终冷洗苯工艺比较
一、煤气终冷工艺流程 1、煤气终冷和机械化除萘工艺 来自硫铵工段煤气在终冷塔内自下而上流动,在流动过程中与经由隔板孔眼喷淋而下的冷却水流密切接触,从55-60℃冷却至 21-27℃,部分水汽被冷凝下来,同时还有相当数量的萘也从煤气中析出,并被水冲洗下来,煤气含量可从2000-3000mg/Nm3,降到800-1200mg/Nm3。冷却后的煤气去洗苯塔脱苯。含萘冷却水由塔底经水封管自流入机械化刮萘槽,水和萘在槽中分离后,水自流入凉水架冷却到30-32℃,再由泵抽送经冷却器冷却到21℃左右后,回终冷塔循环使用。在刮萘槽中积聚的萘,定期用水蒸气间接加热熔化后流入萘的扬液槽,再用水蒸汽压送往焦油槽或焦油氨水澄清槽。亦可用冷凝工段的初冷冷凝液来熔化萘,熔萘后的冷凝液自流返冷凝鼓风段,这样既简化了操作又改善了劳动条件。
该流程的优点是操作稳定,便于管理,缺点是该工艺流程的除萘率受冷却水温的影响,故塔后的煤气含萘量较高。水和萘不能充分分离,部分萘被水带到凉水架, 增加了凉水架清扫工作,因其排污水量大,刮萘槽结构复杂且笨重,基建费高。该洗萘法仅用于硫铵生产工序之后。
2、煤气终冷和焦油洗萘工艺 含萘冷却水从终冷塔底部流出,经液封管导入焦油洗萘器底部并向上流动。热焦油经伸入器的分布管均匀喷洒在筛板上,通过筛板孔眼向下流动,在与水对流接触过程中将水中含萘降到800mg/Nm3以下。洗萘后的焦油从洗萘器下部排出,经液位调节器流入焦油槽。焦油在循环使用24小时后,经加热静止脱水用泵送往焦油车间加工处理,送空的焦油槽再接受冷鼓工段的新鲜焦油以备循环洗萘使用。从洗萘器上部流出的水进入水澄清槽,分离出残余焦油后,自流到凉水架。分离出的焦油及浮在水面上的油类、萘等混合物自流到焦油槽。焦油洗萘比机械化除萘效率高,但操作复杂。
该流程的优点是不仅可以把冷却水中的萘几乎全部清除,而且对水中的酚有一定萃取作用结果,减少凉水架的清扫次数,有利于冷却水的进一步处理。缺点是操作复杂,出口煤气含萘量高,用水量大,后期仍需进行污水处理。
3、油洗萘和煤气终冷工艺 饱和器来的50-55℃的煤气进入木格填料洗萘塔底部,塔顶喷洒温度为55-57℃的洗苯富油进行洗萘。富油进塔温度比煤气温度高5-7℃,使煤气含萘可由2000-2500mg/Nm3降到500-800mg/Nm3。除萘后的煤气进入终冷塔,该塔为隔板式,分两段。上段用从凉水架来的循环水冷却至20-23℃的循环水喷淋,将煤气再冷却25℃左右,额外水从终冷塔底部经水封管流入热水池;然后用泵送至凉水架,经冷却后自流入冷水池。再用泵送至终冷冷塔的上下两端,送往上端的水须于间冷器用低温水冷却,由于终冷器只是为了冷却煤气,
3
所以终冷循环水量可减至2.5-3吨/1000标米煤气
该流程的优点是塔后煤气含萘量要前两种工艺流程,用水量为水洗萘的一半,因而可减少含酚污水的排放量。缺点是该流程油洗萘在较为高的温度下进行,塔后煤气含萘量仍较高,煤气温度波动;操作复杂,洗油耗量大,脱苯困难,仍需进行污水处理。
4、横管终冷喷洒轻质焦油洗萘工艺 从硫铵工段来的煤气由塔顶进入,与连续喷洒的轻质焦油并流差速接触速冷,至横管段继续冷却至21-25℃,同时脱萘
至450毫克/标米3以下,然后从塔底排出,进入旋风捕雾器除掉夹带的焦油,萘和凝结水雾,然后去洗苯塔。轻质焦油由其补充至塔底循环油槽,循环油由槽底泵出至槽中部,顶部喷洒,与横管束和煤气接触换热,同时溶解煤气中析出的萘,然后经液封回循环槽。(此过程中,循环油槽内,入塔处,出塔处油温基本相同)。焦油循环至一定程度,用泵送至焦油上段。18℃的冷冻水由塔下部横管冷却器进入,向上经串联着的各横管器与塔内循环油,煤气间接换热绳温,然后从塔的外部排出。由于该工程主要依靠降低煤气的温度使煤气中萘析出,并由轻质焦油将萘溶解,因此煤气温度需降至21℃左右。 如此低温,就决定了必须要有低温水的焦化厂才易采用该工艺。
该流程的优点是:1、此工艺不仅对煤气中的萘的脱除率高,而且冷却效果非常好。出口煤气约 21℃左右,煤气含萘量大约在 350-450mg/Nm3。2、无须洗油,只须自产轻质焦油,节约洗油耗量;煤气中的萘直接转入焦油,降低了萘的损失。3、该系统阻力小,风机电耗低;操作维护简便;无污染;占地面积小,基建费用少。4、由于煤气冷却不直接与水接触,所以无含酚污水的处理。
二、洗苯工艺
1、焦油洗油吸收法 目前,国内焦化厂主要采用洗油吸收法回收煤气中的苯族烃,经过终冷的煤气温度降至25~27℃,然后进入洗苯塔回收苯族烃,回收方法大致分为下列三种:1.洗油吸收法 用洗油在洗涤塔中回收煤气中毒苯族烃,再将吸收了苯族烃的洗油(富油)送入脱笨蒸馏装置中,以提取粗苯,脱笨后的洗油(贫油)经过冷却后,重新送至洗涤塔循环使用,洗油吸收法又分为常压吸收法和加压吸收法,加压吸收法可以强化生产过程,适用于煤气远距离输送或用作合成氨厂原料的情况下采用。吸附法:2.吸附法 使煤气通过具有微孔组织比表面很大的活性炭或硅胶等固体吸附剂,苯族烃即被吸附在其表面上,直至达到接近饱和状态,然后用水蒸气直接进行解析,即得粗苯。用活性炭做吸附剂,
可将煤气的苯族烃完全吸附下来但此法要求煤气净化的程度较高,加之吸附剂价格昂贵,因此在工业上应用受到一定的限制,而多用于煤气苯族烃的定量分析。凝结法:3.凝结法 在低温加压的情况下,使苯族烃从煤气中冷凝出来,此法比吸收法所得到的粗苯质量好,但煤气的压缩及冷冻过程复杂,阻力消耗大,设备材质要求高。目前国内焦化厂主要采用洗油吸收法回收煤气中的苯族烃,油吸收法可分为焦油洗油吸收法和石油吸收法。煤气经最终冷却到25-27℃后进入洗苯塔。塔前的煤气含粗苯 32-40 克/标m3,塔后的煤气中含粗苯低于2克/标m3。从脱苯工序来的贫油,含苯0.2-0.4%,进入贫油槽,用贫油泵进入洗苯塔顶部,从塔顶喷淋而下,含苯量增至2.5%左右。用富油泵将富油从塔底抽出,送往脱苯工序。
脱苯后的贫油送回贫油槽循环使用。本设计所选用的就是这种工艺流程,但洗苯塔有多种形式,选择合适的塔型是值得研究的。用洗油回收煤气中的粗苯的方法,所用的洗苯塔有多种形式,但工艺流程基本一样。
洗苯塔底部为洗油接受槽,用钢板与煤气部分隔开,从塔顶下来的洗油经U 型管流入该槽,U型管内有一定的液位,足以封位煤气,阻止它进入油槽从放散管溢出。洗苯塔喷头上方设置捕雾器,以捕集的油滴,减少洗油损失,塔顶还有一个喷口,以清洗捕雾层。
2、石油洗油回收粗苯 用石油洗油回收粗苯的工艺流程与用焦油洗油回收的一样,只是在设计贫油槽时,须考虑经常排油渣和生成腐蚀物。目前国内使用的是有洗油为轻柴油,与焦油洗油比较耗量低,油水分离容易,具有较高的稳定性,长期使用后其物理化学性质几乎不变,此外,石油洗油吸萘的能力强,一般塔后煤气含萘量可低于150mg/Nm3.石油洗油的缺点是洗苯能力较低,富油含苯量为1.2~0.3%,故循环洗油量每吨(180℃前粗苯为 65m3)和脱笨的耗气量较多,
此外,在洗苯过程生成难溶的油渣,容易堵塞换热设备,含油渣的洗油和 水容易形成乳蚀液,影响正常操作,所以洗油含渣量不宜大于20mg/ρ.另外焦化厂使用石油洗油需外购,因此多数焦化厂采用焦油洗油。为了满足从煤气中回收和制取粗苯的要求,洗油具有如下性能:1)常温下对苯族烃有良好的吸收能力,在加热时又能使粗苯很好的分离出来。2)有足够的化学稳定性,即在长期使用中吸收能力基本稳定。3)在吸收操作温度下不应析出固体沉淀物。4)易于水分离,且不能生成乳蚀物。5)有较好的流动性,易于用泵抽送并能在调料上均匀分布。 由于石油洗苯工艺流程缺点较多,特别选型上存在难题,故一般不采用它,而多采用第一种工艺流程。
三、富油脱苯
1、生产一种产品的工艺流程
如图1.1所示,来自洗苯工序的富油依次与脱苯塔顶的油气和水汽的混合物、脱苯塔低排除的热贫油换热后温度达110~130℃进入脱水塔。脱水后的富油经管式炉加热至180~190℃进入脱苯塔。脱苯塔顶逸出的90~92℃的粗苯蒸汽与富油换热后温度降到75℃左右进入冷凝冷却器,冷凝液进入油水分离器。分离出水后的粗苯流入回流槽,部分粗苯送至塔顶做回流,其余的作为产品采出。脱苯塔底部排出的热贫油经贫富油换热器进入热贫油槽,再用泵送贫油冷却器冷却至25~30℃后去洗苯工序循环使用。脱水塔顶逸出的含有萘和洗油的蒸汽进入脱苯塔的精馏段下部。在脱苯塔精馏段切取萘油。从脱苯塔上部断塔板引出液体至油水分离器分离出水后返回塔内。脱苯塔用的直接蒸汽是经管式炉加热至400~450℃后,经由再生器进入的,以保持再生器顶部温度高于脱苯塔底部温度。
为了保持循环洗油质量,将循环油量的1%~5%的富油入塔前的管路引入再生器进行再生。在此用蒸汽间接将洗油加热至160~180℃,并用过热蒸汽直接蒸吹,其中大部分洗油被蒸发并随直接蒸汽进入脱苯塔底部。残留于再生器底部的残渣油,靠设备内部的压力间歇或连续地排至残渣油槽。残渣油中300℃前的溜出量要求低于40%。洗油再生器的操作对洗油耗量有较大的影响。在洗苯塔捕雾,油水分离及再生器操作正常时,每生产1t 180℃前粗苯的煤焦油洗油耗量可在100kg以下。
上述流程是一种十分稳定可靠的工艺流程。一些操作经验丰富的工人,经过精心操作表明:该流程中的脱水塔可以省略;脱苯塔精馏段可以不切取萘油也不会造成萘的积累;脱苯塔上部不会出现冷凝水,因此断塔板和油水分离器可以省略;从而使脱苯装置、管线、阀门大大简化,操作简捷方便,并进一步降低了洗
油消耗。实际上使用计算机对脱苯塔装置作模拟计算从理论上为此提供了支撑。实现萘在贫油中不积累的关键是:脱苯塔装置操作稳定;脱苯塔顶温度、直接蒸汽温度和用量及富油如脱苯塔温度等指标适宜等;煤气在初冷器和电捕焦油器将萘和煤焦油脱出较好。
图1.1生产一种产品的流程
1一脱水塔;2一管式炉;3一再生器;4一脱苯塔;5一热贫油槽; 6一换热器;7一冷凝冷却器;8一冷却器;9一分离器; 10一回流槽。
2、生产两种产品的工艺流程
如图1.2所示,与生产一种苯流程不同是脱苯塔逸出的粗苯蒸汽经分凝器与富油和冷却水换热,温度控制为88~92℃后进入两苯塔。两苯塔顶逸出的73~78℃的轻苯蒸汽经冷凝冷却并充分离出水后进入轻苯回流槽,部分送至塔顶作回流,其余产品采出。塔底引出重苯。
脱苯塔顶逸出粗苯蒸汽是粗苯、洗油和水的混合蒸汽。在分凝器冷却过程中生产的冷凝液称之为分缩油,分缩油的主要成分是洗油和水。密度比水小的称为轻分缩油,密度比水大的称为重分缩油。轻、重分缩油进入分离器,利用密度不同与水分离后兑入富油中。通过调节分凝器轻、重分缩油的采出量或交通管(轻、重分缩油引出管道间的连管)的阀门开度可调节分离器的油水分离情况。从分离器排出的分离水进入控制分离器进一步分离水中夹带的油。
图1.2生产两种产品的流程
1—脱水塔;2—管式炉;3—再生器;4—脱苯塔;5—热贫油槽;6—两苯塔;7
—分缩器;8—换热器;9—冷凝冷却器;10—冷却器;11—分离器;
12—回流柱; 13—加热器。
3、生产三种产品的工艺流程
生产三种产品的工艺流程有一塔式和两塔式流程。
(1) 一塔式流程 即轻苯、精重苯和萘油溶剂均从一个脱苯塔采出。自洗苯工序来的富油经油气换热器及二段贫富换热器、一段贫富换热器与脱苯塔低出来的170~175℃热贫油换热到135~150℃,进入管式炉加热到180℃进入脱苯塔,在此用再生器来的直接蒸汽进行气提和蒸馏。脱苯塔顶部温度控制在73~78℃,逸出的轻苯蒸汽在油气换热器、轻苯冷凝冷却器经分别与富油、16℃低温水换热冷凝冷却至30~35℃,进入油水分离器,在与水分离后进入回流槽,部分轻苯送至脱苯塔顶做回流,其余作为产品采出。脱苯塔底部排排出的热贫油经一段贫富油换热器后进入脱苯塔底部热贫油槽,再用泵送经二段贫富油交换器、一段贫油冷却器、二段贫油冷却器冷却到27~30℃至洗苯塔循环使用。
精重苯和萘溶剂油分别从脱苯塔侧线引出至各自的回流槽。从脱苯塔上部断塔板上将塔内液体引至分离器与水分离后返回塔内。从管式炉后引出1%~1.5%的热富油,送入再生塔内,用经管式炉加热到400℃的蒸汽蒸吹再生。再生残渣排入残液槽,用泵送油库工段。系统消耗的洗油定期从洗油槽经富油泵入口补入系统。各油水分离器排出的分离水,经控制分离器排入分离水槽送鼓风工段。各
储槽的不凝气集中引至鼓风冷凝工段初冷前吸煤气管道。
(2) 两塔式流程 即轻苯、精重苯和萘溶剂油从两个塔采出。与一塔式流程不同之处是脱苯塔顶逸出的粗苯蒸汽经冷凝冷却与水分离后流入粗苯中间槽。部分粗苯送至塔顶做回流,其余粗苯用作两苯塔的原料。脱苯塔侧线引出萘溶剂油,塔底排出热贫油,热贫油经换热器、贫油冷却器冷却后至洗苯工序循环使用。粗苯经两苯塔分馏,塔顶逸出的轻苯蒸气经冷凝冷却及油水分离后进入轻苯回流槽,部分轻苯送至塔顶作回流,其余作为产品采出。重质苯、萘油溶剂分别从两苯塔侧线和塔底采出。在脱苯的同时进行脱萘的工艺,可以解决煤气用洗油脱萘的萘平衡,省掉了单独脱萘装置。同时因洗油含萘低,又可进一步降低洗苯塔后煤气含量。
四、洗油再生
无论是采用什么加热方式,在粗苯蒸馏系统中均需设置再生器。使用再生器的作用是将循环洗油的一部分连续引入再生器,在器内洗油被加热到一定的温度,使洗油中的不饱和化合物聚合,作为高沸点残渣排出,以保证循环洗油的质量。如果再生器失去作用,洗油质量变坏的速度是很快的。某厂的生产实践表明,两个月的时间,循环洗油的粘度就由1.52°E25增长到3.7~3.8°E25, 270℃的馏出量由60%左右下降到45%~48%,300℃前的馏出量下降到80%左右。
众所周知,循环洗油质量的恶化会造成洗油粘度和比重的增加,洗油分子量增大,从而直接影响苯的吸收操作,造成粗苯回收率下降。不仅如此,洗油质量的好坏对脱苯操作影响也很大。因此,再生器的正常操作是保持和稳定循环洗油质量和保证粗苯装置正常运行的关键之一。
具体工艺流程没有查到,详见课本。
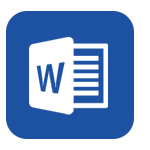





正在阅读:
煤气终冷洗苯工艺比较09-18
SMITH圆图分析与归纳11-13
良种桉种植对生态环境影响与对策01-04
七年级数学上册第5章走进图形世界5.2图形的运动同步练习(新06-08
饲料毒物与卫生学01-04
选修一第六单元《俄国农奴制改革》教学案11-16
模拟电子电路课件3第三章负反馈04-22
关于环境的调查报告12-12
Unit 1 How tall are you教案10-01
13级康复专业人体发育学A卷答案03-02
- 2015小学四年级数学下册加法交换律和加法结合律练习题
- 2017年士兵军考之诗词阅读与欣赏考点:《乌江亭》
- 工分制管理-专项制度-撰写范例
- 政治生活辨析题
- 广东部分-广东省电力行业协会
- 多向度性格测验-试题
- 造型材料与工艺(03) - 图文
- 广播电视台招聘考试判断题题库(52题 附答案)
- 2.17过秦论复习题
- 长江大学文理学院13届计算机复习备考资料
- 2018年人教版小学语文六年级毕业总复习资料
- 自然辩证法论文
- 201101高二地理(必修)试题
- 八年级外研版英语作文集锦
- 机械工程材料课后习题答案资料
- 参与式教学的内涵与特点
- 凹模机械加工工艺设计(精)
- 人教版新目标七年级英语上册Unit2This is my sister知识点课时练习单元语法聚焦练习题附答案
- 光刻技术
- 家长一封信