面向数控机床刀具系统的远程故障诊断平台构建
更新时间:2024-05-17 04:07:01 阅读量: 综合文库 文档下载
- 数控机床的刀具系统的组成推荐度:
- 相关推荐
摘要
数控机床刀具磨损监测对于提高数控机床利用率,减小由于刀具破损而造成的经济损失具有重要意义。有针对性地回顾了国内外各种分析刀具磨损信号方法的研究工作,详细叙述了功率谱分析法、小波变换、人工神经网络以及多传感器信息融合技术的实现形式。通过比较各种数据处理方法的优缺点,提出基于混合智能多传感器信息融合技术是数控机床刀具磨损监测实验数据处理的未来发展的主要方向。以数控机床刀具故障诊断系统构建与测试方法研究为目标,进行了刀具磨损实验。采用振动传感器、声发射传感器对切削过程中不同磨损程度刀具的信号进行检测、分析和故障诊断。以LabVIEW10.0 为开发平台,开发了一套包括数据采集模块、信号分析模块、故障诊断模块的数控机床故障诊断实验系统。
关键词:数控机床;刀具磨损监测;数据处理;LabVIEW; 声发射; 振动
Abstract
CNC tool wear monitoring would be a great significance for improving the usage rate of CNC and reducing the economic losses due to the tool breakage. The recent research progress on the signal analyzing was reviewed. Some important data process methods were detailed described,such as power spectrum analysis,wavelet transform,artificial neural network and intelligent sensor fusion technology. By comparing their features,the intelligent sensor fusion technology was introduced to be popular in data processing method for CNC tool wear monitoring. To build fault diagnosis system of CNC machine tools and get test method,tool wear experiments are carried out. Signals for cutting tool with different wearing degrees in milling process are detected and analyzed through vibration sensors and acoustic emission sensors on the milling tools. Using LabVIEW8. 6 as development platform,a fault diagnosis experimental system of CNC machine tools is developed,including data acquisition module,signal analysis module and fault diagnosis module
Key words:CNC;Tool wear monitoring;Data processing method; LabVIEW; vibration
目录
第1章 绪论 ................................................................................................................. 1
1.1研究意义 ......................................................................................................... 1 1.2国内外过程监测研究动态及其发展趋势 ..................................................... 3
1.2.1国外刀具监控技术的研究现状 .......................................................... 3 1.2.2国内刀具监控技术的研究现状 .................................................................. 4 1.3虚拟仪器 ......................................................................................................... 4
1.3.1 虚拟仪器的概念 ................................................................................. 5 1.3.2 虚拟仪器的特点和优势 ..................................................................... 5 1.3.3 虚拟仪器的结构 ................................................................................. 5 1.3.4虚拟仪器与LABVIEW ........................................................................ 6
第2章 刀具系统 ......................................................................................................... 6
2.1刀具监控系统的组成 ..................................................................................... 6
2.11信号监测 ............................................................................................... 7 2.12特征提取 ............................................................................................... 7 2.13状态识别 ...................................................................................................... 7 第3章 数据采集 ......................................................................................................... 7
3.1 数据采集系统概念 ........................................................................................ 8 3.2 数据采集系统的任务 .................................................................................... 8 3.3 数据采集系统的功能 .................................................................................... 8
3.3.1 数据采集 ............................................................................................. 8 3.3.2 信号调理 ............................................................................................. 8 3.3.3 二次数据计算 ..................................................................................... 9 3.3.4 数据显示 ............................................................................................. 9 3.3.5 数据存储 ............................................................................................. 9 3.3.6 打印输出 ............................................................................................. 9 3.3.7 人机联系 ............................................................................................. 9 3.4 数据采集系统的硬件 .................................................................................. 10
3.4.1 传感器 ............................................................................................... 10 3.4.2 前置放大电路 ................................................................................... 10 3.4.3 滤波器 ............................................................................................... 10 3.4.4 多路模拟开关 ................................................................................... 11
3.4.5 采样/保持器...................................................................................... 11 3.4.6 模/数转换器...................................................................................... 11 3.4.7 计算机系统 ....................................................................................... 11 3.5 数据采集系统的硬件 .................................................................................. 11
3.5.1 模拟信号采集与处理程序 ............................................................... 11 3.5.2 系统管理程序 ................................................................................... 11 3.5.3 通信程序 ........................................................................................... 12
第4章 刀具磨损监测实验 ....................................................................................... 12
4.1实验方案 ....................................................................................................... 12 4.2实验装置的选择 ........................................................................................... 12
4.2.1机床的选择 ........................................................................................ 12 4.2.2传感器的选择与安装 ........................................................................ 13 4.2.3 A/D卡及采集参数选择 .................................................................. 15 4.3刀具磨损监测系统 ....................................................................................... 16 4.4试验方法设计 ............................................................................................... 17 第5章 程序界面与功能实现 ................................................................................... 17
5.1 程序界面 ...................................................................................................... 17 5.3远程界面,Remote Panels技术 .................................................................. 23 第6章 实验数据分析 ........................................................................................... 26
5.1刀具损坏形式及标准 ................................................................................... 26
5.1.1刀具磨损 ............................................................................................ 26 5.1.2刀具破损 ............................................................................................ 27 5.1.3刀具磨损测量基准 ............................................................................ 27 5.2影响刀具磨损的因素 ................................................................................... 27
5.2.1 刀具本身的材料 ............................................................................... 27 5.2.2刀具表面涂抹其他材料 .................................................................... 28 5.2.3工件的材料 ........................................................................................ 28 5.2.4切削速度的影响 ................................................................................ 29
第7章 结论与展望 ................................................................................................... 29
7.1总结 ............................................................................................................... 29 7.2 展望 .............................................................................................................. 30 参考文献 ..................................................................................................................... 30 致谢 ............................................................................................................................. 31
石家庄铁道大学毕业论文
第1章 绪论
随着科技的快速发展,自动化逐步代替了人工化,突出了自动化的高速、高效、高精度和自动化,加快一系列的发展,但是也有一定的问题,其中刀具的磨损就直接影响数控机床的一些性能。刀具在不同的磨损状态会直接影响加工工件的质量问题,当磨损加剧的时候,也可能会影响机床本身的寿命,从而降低效率。本文以实验为基础,主要监测刀具磨损,在不同加工参数的前提下对刀具整个寿命阶段的一系列监测,包括振动和声发射,加工工件的表面粗糙度值,综合分析刀具在不同加工参数下所得到的数据,来得出刀具的磨损状态,并把每次加工工件的性能质量一一对应起来,实现两者的智能监测。还将其做成个数据库,把所有实验数据录入到数据库当中,以便查询以及后续的分析与研究。另外还有故障案例查询,以便能够更好地解决刀具故障问题。
1.1研究意义
制造业是国家经济发展的支柱行业,制造业的发展离不开先进制造技术的支持。自进入21世纪,随着电子、计算机、信息等高新技术的不断发展,为了适应全球化市场需求的多变性与多样化,制造技术正朝着精密化、柔性化、集成化、网络化、全球化、虚拟化、智能化和清洁化的方向发展。2000年过后,随着计算机、信息、通信等高新技术的不断发展,现代制造业朝着高速度、高效率、柔性化、集成化、自动化方向迅猛发展。其中尤以数控技术(CNC)、加工中心(MC)、柔性制造单元(FMC)、柔性制造系统(FMS)、计算机集成制造系统(CIMS)为代表[1]。
数控机床是装备制造业的工作母机,其技术水平的高低代表了一个国家制造业的发展水平。对其加工制造过程能够智能辅助决策、自动感知、智能监测、智能调节和智能维护的机床,从而支持加工制造过程的高效、优质和低耗的多目标优化运行[2]。刀具状态智能监测技术作为先进制造技术的重要组成部分,是在现代传感器技术、信号处理技术、计算机技术和制造技术基础上发展起来的新兴技术,它对于推动加工过程自动化和无人化发展具有极其重要的作用[3]。刀具作为切削过程的直接执行者,在工件的切削加工过程中不可避免地存在着磨损和破损等现象,刀具状态的变化直接导致切削力增加、切削温度升高、工件表面粗糙度上升、工件尺寸超公差、切屑颜色变化以及切削颤振的产生。在传统的机械加工过程中,刀具状态的识别是通过加工人员
1
石家庄铁道大学毕业论文
辨别切屑颜色和加工过程中的噪声等来判断,或根据加工时间判断,或在加工工序之间拆卸刀具实测其破损程度和磨损量,这些方法和加工人员的经验紧密相关,所以它不可避免地存在下列问题:
一方面,如果刀具磨损量低于磨钝标准,则会因为没有充分利用刀具的实际寿命而带来浪费,增加制造成本;另一方面,如果刀具磨损量高于磨钝标准,刀具己经磨钝或破损,则会影响工件的加工表面质量和尺寸精度,严重时甚至会损坏机床。此外,在自动化加工、无人化加工以及自适应加工过程中,不仅要求能够在加工过程中实时获知刀具的准确磨损状态,而且还要求根据刀具的磨损和破损程度改变切削参数,以便优化生产率和加工质量。解决这些问题的关键在于对刀具实际的磨损状态进行自动和实时检测。这一工作的重要性正如美国学者B.M.Karmer在CIRP35届年会上所说:在提高计算机集成制造系统生产率方面,没有任何一项技术比准确地估计刀具寿命更重要[4]。
近年来,随着市场竞争的进一步加剧,现代制造工业要求产品产量最大化、成本最小化。这迫切要求制造工业向自动化和无人化方向发展,对制造过程进行全面监测成为必然趋势,尤其是对刀具状态的监测。刀具监控技术的发展过程经历了由离线非实时监测到在线实时监测、由单一传感器监测到多传感器数据融合监测、由单项监测到集成监测、由简单的决策判别监测到智能识别监测的过程[5-7]而人工判别刀具状态已经成为制约制造工业发展的重要瓶颈,这也是刀具状态智能监测技术获得广泛研究的重要原因。
刀具状态智能监测技术是指在产品加工过程中,计算机通过检测各类传感器信号变化,实时预测刀具的磨损和破损状态,过程控制系统根据刀具状态检测结果,自动控制刀具进给以补偿刀具磨损导致零件尺寸和形状精度的变化。研究表明,CNC机床配备刀具监测系统后可减少故障停机时间的75%,提高生产率10%一60%,提高机床利用率50%以上。美国Knenametal公司的研究表明,刀具监测系统不仅提高了刀具本身的利用率,而且可避免刀具失效所导致的工件报废和机床故障,节约费用达30%
[8]
。因此,为有效防止设备的损坏、工件的报废并保证机床无故障运行,就必须发展在众多刀具状态监控技术中,切削声音检测技术以其特有的优越性已成为当今最
加工过程的刀具状态监测技术。
有效的刀具磨损监测技术之一。通过噪声传感器获取切削加工中的声音信号,并利用有效的信号处理技术提取与刀具磨损状态相关的特征信息,从而实现对刀具状态的监控。切削声音信号检测技术在数控机床刀具监控系统中的成功应用,是现代先进制造技术的一个重要成果。
因此刀具状态监测技术的目的和意义在于:
2
石家庄铁道大学毕业论文
(l)实时监测刀具状态,刀具不可靠时,加工系统对刀具磨损量进行补偿,或更换刀具;
(2)降低废品率和工件加工成本,提高工件加工质量;
(3)减少设备的停机时间,提高设备利用率和生产率,延长刀具使用寿命; (4)防止机床事故,最大限度地保证机床加工系统的安全性; (5)实现工厂自动化,最大限度地减少人对机床的干预; (6)使加工系统在最优的参数下运行。
实际上,从没有受到干扰的切削过程获取一个合适的参考信号需要大量的工作和较高的技能。即便获得了恰当的参考信号,当应用到工业实际中时,由于工作条件或加工要求的变化,又会出现另外的问题。由于所获得的参考信号是对应特定机床类型和实际切削参数的某种映射,当修改了 NC 程序或者使用不同的刀具进行切削时,这些参考信号将不能继续使用。
1.2国内外过程监测研究动态及其发展趋势
刀具状态监控技术的发展与数控技术的发展密切相关。自从上世纪50年代数控机床诞生以来,以运动、位置控制为主的数控技术不断的提高和发展,因此刀具监控作为其中的重要部分而得以同步发展。早期的刀具监控主要是刀具寿命的管理,即通过系统的计数方式对刀具的切削次数进行管理,严格说来它不算是真正意义上的刀具监控。因此在当时的数控机床应用中,刀具监控一直是制造应用的瓶颈。进入本世纪以来,随着计算机和信息技术的发展,数控系统、伺服系统的控制功能日臻完善,高速处理器、数字化控制、前馈控制和现场总线技术被广泛采用。由于信息处理技术和传感器技术的飞速发展,使得刀具监控过程所需的数据采集成为可能。
1.2.1国外刀具监控技术的研究现状
早在上世纪40年代,机械加工数控技术得以应用之前,国外对刀具磨损和破损监测技术的研究就已经开展起来。经过40多年的发展,国外在刀具磨损与破损自动监测方面做了大量的工作,监测技术和理论已得到极大的丰富和发展
Dimla认为切削力(静态和动态)和振动(加速度)信号是刀具监测领域应用比较广泛的信号,二者融合后的信息能更准确地反映刀具磨损状态[9]。 Bemhardsick通过大量的实验总结出切削力、振动和AE信号是反映刀具状态的典型信号。通过调查发现在已经公开发表的文章中,有87%的作者使用多传感器信息融合技术,并进一步指出多传感器信息融合技术和神经网络模型已经成为刀具监控系统软件开发的核心
3
石家庄铁道大学毕业论文
[10]
。Ertunc,H.M为了提高监控模型的可靠性,把测量到的力信号和能量信号分别输
入单个模糊运算法则,然后把这些单个模糊运算法则的输出送入模糊中心运算法则,以判断钻削过程中的刀具状态[11]。MannanM.A使用ccD摄像机采集刀具表面图像和微型话筒采集切削声音,用小波分析进行特征提取,最后输入神经网络进行信息融合判断刀具磨损状态[12]。D.E.Dimlasrl指出神经网络结构及训练样本决定网络分类的成败,神经网络的输出仅仅把刀具状态分为磨损或新刃远远不能满足生产加工的需要,应该提高神经网络的能力使其能分辨刀具的新刃、部分磨损、磨损和破损状态[13]。
1.2.2国内刀具监控技术的研究现状
在国内,由于数控机床与柔性制造系统等先进制造技术发展较晚,相对世界先进水平还比较落后,因此在刀具状态监测技术的研究上起步也比较晚,上世纪70年代末才开始这方面的研究。但经过近些年的努力,在检测方法和监测识别理论上都有了很大的进展,有些已接近或超过国际先进水平。
路勇等[14]建立了基于数据模糊分析模型的神经网络在线监测数控磨床刀具状态。测力计和加速计采集到的信息输入不同的数据模糊分析模型进行特征提取,然后再送入神经网络进行学习。
刘敦焰[15]以切削力和切削功率为监控参数,建立了基于切削参数(切削深度、进给量、主轴转速、工件材料及刀具材料)与刀具状态(主要考虑后刀面磨损量)的车削力及功率模型,经解藕得到的后刀面磨损量VB的实时监控方法非常有实用价值。
舒服华[16]用小波变换对信号进行精确的细分,提取出加工过程中刀具磨损的特征信息,据此分析该加工过程的刀具磨损状况,为刀具磨损的状态检测和实时补偿提供了准确的依据。
李菊欢[17]从理论、实验和计算3个方面论证了刀具磨损的分形特性,应用曼德波罗提出的分形维数分析计算方法,探讨了刀具磨损的分形结构和切削用量与刀具磨损分形维数之间的关系。研究表明,用分形维数能有效地描述刀具磨损特征,表征刀具磨损切削参数与刀具磨损之间的联系,并显示出使用分形维数作为模式聚类与识别的优越性。
1.3虚拟仪器
虚拟仪器的出现是测量仪器领域的一个突破,它彻底改变了传统仪器观,从根本上更新了测量仪器的概念,带给人们一个全新的仪器观念。虚拟仪器代表这测量仪器
4
石家庄铁道大学毕业论文
发展的最新潮流和方向,是未来仪器产业发展的一大趋势。
1.3.1 虚拟仪器的概念
从实质上讲,虚拟仪器利用硬件系统完成信号的采集、测量与调理,利用计算机强大的软件功能实现信号数据的运算、分析和处理,利用计算机的显示器模拟创传统仪器的控制面板,以多种形式输出检测结果,从而完成所需的各种测试功能。
1.3.2 虚拟仪器的特点和优势
虚拟仪器利用高性能的模块化硬件,结合高效灵活的软件来完成各项测试,测量和测控方面的应用。灵活高效的软件能创建完全自定义的用户界面,模块化的硬件能方便的提供全方位的系统集成,标准的软硬件平台能够满足同步,定时等多种应用需求。与传统仪器相比,虚拟仪器具有以下4个特点:
(1)性能高:
虚拟仪器技术是在PC技术的基础上发展起来的,因此拥有了高效的处理器和文件输入输出性能。
(2)扩展性强:
由于软件的灵活性强,所以只需更新计算机或测量硬件后,通过修改软件进行扩展。
(3)开发时间少:
虚拟仪器由于其灵活的软件功能,只需要修改应用程序或者驱动程序来适应不同仪器仪表与计算机的通信。因此较之于单独开发某一仪器仪表的时间减少了。
(4)无缝集成:
虚拟仪器软件平台为所有的输入输出设备提供了标准的接口,帮助用户轻松地将多个测量设备集成到单个系统,减少了任务的复杂性。
1.3.3 虚拟仪器的结构
5
石家庄铁道大学毕业论文
虚拟仪器系统包括仪器硬件和应用软件两大部分。仪器硬件是计算机的外围电路,与计算机一起构成了虚拟仪器系统的硬件环境,是应用软件的基础;应用软件则是虚拟仪器的核心,在基本硬件确定后,软件通过不同功能模块即软件模块的组合构成多种仪器,赋予系统特有的功能,以实现不同的测量功能。 虚拟仪器的基本结构如图2.3所示。
1.3.4虚拟仪器与LABVIEW
虚拟仪器应用程序的开发平台有很多种,莫倩最流行的是美国国家仪器(National Instruments,NI)公司的LABVIEW。LABVIEW是Laboratory Virtual Instrument Engineering Workbench (实验室虚拟仪器工程平台)单词首字母组合。LABVIEW环境中的开发的每个程序称为Virtual Instrument(VI)。
用LABVIEW作为虚拟仪器开发平台的最大优势就是程序开发效率高,这主要是由于它提供了几乎所有的经典的信号处理函数和大量现代的高级信号分析函数,这些函数用图标的方式提供给用户,使用者采用图标与连线的方式,可以像画电路板一样编写程序,非常形象,直白又便于修改和移植。才外LABVIEW程序非常容易和各种数据采集硬件集成。还可以和多种主流的工业现场总线通信以及与大多数通用的数据库连接,根据经验,使用LABVIEW开发虚拟仪器比使用基于文本的语言开发效率可以提高10~15倍,同时LABVIEW在信号处理等方面的强大功能有远非组态软件可比。
第2章 刀具系统
对刀具状态监控的研究,一方面要加强基础理论的研究,获得对刀具时效敏感的特征,发展使用可靠的新型决策模型;另一方面要加强理论和实践相结合,才能使刀具状态监控技术得到进一步的完善[18]。
2.1刀具监控系统的组成
6
石家庄铁道大学毕业论文
2.11信号监测
在加工过程中有许多种状态信号从不同角度反映刀具状态的变化,监测信号选择的好坏往往是决定监控系统成败的关键因素。监测信号应具备对刀具状态的变化反应灵敏和迅速,便于在线测量,不改变加工系统结构,信号受环境干扰小,具有较高的信噪比等特点。常用的刀具状态监测信号有切削力、功率/扭矩、声发射信号(AE)、振动、温度、切削参数、电流等。监测信号用相应的传感器获得并进行预处理,信号预处理的内容包括隔离、放大、滤波、A/D转换等。
2.12特征提取
特征提取是对监测信号的进一步加工处理,从大量信号中提取出与刀具状态变化相关的参数,一方面可以提高信号的信噪比,另一方面可以减少后期数据的处理量,提高运算速度。目前广泛使用的特征提取方法主要有时域分析方法(均值、差值、相关系数、导数值等)、频域分析方法(快速傅立叶变换、功率谱等)和时频分析方法(短时FFT、小波分析〕。特征提取后可获得反映信号本质的特征数据,它的品质对监测系统的性能和可靠性具有很重要的影响作用。
2.13状态识别
状态识别是根据所获得的刀具状态特征参数通过识别模型对加工过程的刀具状态进行分类判断,其核心是所采用的模型。模型的功能是实现从特征空间到状态空间的映射,模型可由物理关系或者根据经验公式建立。根据模型的特点可以分为固定参数模型、适应性模型和自学习模型等。多模型系统的思路是对加工过程刀具状态的检测信号通过多个模型进行分析,以获得更多的监测信息,这种系统在不增加设备成本的情况下,通过软件处理获得更多的刀具状态信息,使监测更准确更可靠。当前采用建模的主要方法有统计方法、模式识别专家系统、神经网络等。
第3章 数据采集
虚拟仪器主要用于获取真实物理世界的数据,也就是说,虚拟仪器必须要有数据采集的功能。从这个角度来说,数据采集就是虚拟仪器的核心,使用虚拟仪器必须要
7
石家庄铁道大学毕业论文
图5-1登陆界面
登陆成功后,进入系统的主界面,可以根据自己所需的功能进入相关的程序。
18
石家庄铁道大学毕业论文
在【主菜单】中点击【数据录入】进入数据的录入界面,通过【数据导入】按钮,可以将机床型号,类型,转速等等机床的详细信息直接录入到access数据库中,并且会在右边的显示栏中实时显示,每组数据都有自己的数据ID,不仅可以对信息方便的浏览,还能对不正确,或者不准确的数据点击按钮【数据删除】进行删除,进而确保数据的正确性,完整性。
图5-2 数据录入
在【主菜单】界面,点击【数据查询】按钮,通过此版块,可以查询机床属性,以及读取历史实验数据,并直观显示。
19
石家庄铁道大学毕业论文
图5-3 数据查询
在【主菜单】界面,点击【故障分析】按钮,通过故障分析模块,可以对实验数据进行频域分析,并通过类型选择,选择正常,磨损,严重磨损等方面的故障数据,形成图像,并进行数据分析。最后综合图像,数据的分析,点击【故障报表】按钮,生成诊断报表。
图5-4-1 故障分析-震动
20
石家庄铁道大学毕业论文
图5-4-2 故障分析-声发射
图5-5 报表生成
21
石家庄铁道大学毕业论文
在【主菜单】点击【案例分析】按钮,用户可以根据不同的故障类型,选择不同的故障来源,并且从案例,以及右侧分析文本框中,了解到此类故障的来源,原因以及解决方法。
图5-6 故障案例库
由于典型故障案例分类比较多,原因以及解决的方法不能及时筛选出来,此时可以通过点击【案例分析】中的【案例简要总结】按钮,直接跳转到此界面,这样是用户对问题的原因,解决的方案一目了然。
图5-7 故障案例总结
22
石家庄铁道大学毕业论文
在【主菜单】中点击【程序流程图】进入此界面,这是对此平台一个功能路径的简要概括,此功能,使用户对平台的详细功能有更深一步的了解以及概括的认识。
图5-8 系统结构图
5.3远程界面,Remote Panels技术
利用LabVIEW的网络通信节点,例如Datasocket及TCP/IP可以实现远程测控数据,但是它们的不足之处就在于,需要高深的网络知识来应用它们[19]。而且,对于以前开发完成的软件,没有远程测控功能的,则需要修改,修改需要耗费大量精力,而且,有些软件,是不能修改的[37]。
对于LabVIEW中提供的Remote Panels技术,用户可以轻松的在本地计算机上打开远程计算机上的VI,在LabVIEW中使用Remote Panels非常方便[20]。
首先,要先运行LabVIEW并配置Web Server.其配置步骤如下。
①在LabVIEW主菜单中选择工具-选项,随后,在弹出的LabVIEW“选项”对话框的下拉列表框中选择“Web服务器:配置”,进行配置,如图5.25所示。
选中启动Web服务器,启动LabVIEW Web Server。LabVIEW Web Server默认的端口号为80。通常情况下,推荐给用户自定义TCP/IP应用程序使用的网络端口的端口号为49152到65535。配置页面中的其他选项包括记录文件路径设置、服务器根目录、超时时间设定等。
23
石家庄铁道大学毕业论文
②客户访问权限设置
在下拉列表框中选择“Web服务器:浏览器访问”进行配置。如图5.26所示。 ③VI访问权限设置
在下拉列表框中选择“Web服务器:可见VI”,设置允许用户访问VI。如图5.27所示。
④为了提供网页浏览器访问,必须在配置服务器时增加一步:利用菜单中的工具>>web发布工具将网页发布出去。如下图,Web发布工具允许用户输入一个Vl的名称,并自动生成一个HTML文件。当然,要将这个HTML文件保存在“Web服务器配置”所指定的根目录中。在发布的Vl中包含了数个subVI,这些SubVI的前面板窗口在需要时也可以打开,那么只需要再将SubVI的前面板的属性设定为执行中打开即可。这样,就可以在客户端打开这些SubVI的前面板[21]。
图5-9 Web服务器
24
石家庄铁道大学毕业论文
图5-10 Web发布工具
图5-11 发布工具(2)
25
石家庄铁道大学毕业论文
图5-12 远程界面
第6章 实验数据分析
5.1刀具损坏形式及标准
刀具损坏是机械加工过程中的一个必然现象,刀具损坏的形式主要有:刀具磨损和刀具破损。
5.1.1刀具磨损
刀具磨损主要取决于工件材料、刀具材料的机械物理性能和切削条件。用不同的刀具材料切削不同的工件材料时,刀具磨损状况各有不同。刀具磨损按其发生的部位分为下面三种类型:
(l)前刀面磨损(月牙洼磨损)
切削塑性材料,当切削速度高、进给量较大时,切屑与前刀面在高温、高压、高速下接触,产生剧烈摩擦,磨损开始发生在前刀面上距刀刃一定距离处,并逐渐向前、后扩大,形成月牙洼。前刀面磨损以月牙洼最大深度KT表示。
(2)后刀面磨损
这是在薄切屑、切削速度较低,或者切削高硬度及脆性较大的材料时所发生的磨
26
石家庄铁道大学毕业论文
损情况。这时,前刀面的接触长度较小,所以磨损集中发生在刀刃及刀刃附近的后刀面上。
(3)前后刀面同时磨损
这种磨损介于前两种类型之间,发生的条件(工件材料的硬度、脆性,切削速度和进给量,刀具材料的热硬性等)也介乎其间,且刀具的磨损形式随切削条件不同可以互相转化。
5.1.2刀具破损
用脆性大的刀具材料制成的刀具进行断续切削(铣削和刨削),或者加工高硬度的材料,刀具都易产生破损。据统计,硬质合金刀具约有50~60%的损坏属于破损。刀具破损包括刀具塑性破损和刀具脆性破损,常见的崩刃、剥落、裂纹、碎断等属于脆性破损。
5.1.3刀具磨损测量基准
在加工过程中,必须制定正确的刀具磨损测量基准,才能够测量刀具的磨损状态,从而进行正确判断。生产中可根据下列现象,判断刀具是否己经磨损,从而及时换刀。
(1)后刀面的磨损宽度达到一定数值。
(2)切屑的颜色或者形状有显著的变化。以切屑的底面变得粗糙来判断刀刃的磨损情况。
(3)工件表面粗糙度显著变粗,或尺寸精度超出公差。 (4)切削力增大,出现不正常的声响和产生振动。
制定测量基准时,主要考虑刀具磨损状态对工件表面光洁度和尺寸精度的影响,且测量方便。目前,国内外研究人员都将后刀面磨损量作为测量刀具磨损量的基准,国际标准1503685一1977统一规定以1/2切削深度处后刀面上测定的磨损宽度VB作为刀具磨钝测量基准。
5.2影响刀具磨损的因素
5.2.1 刀具本身的材料
不同的刀具材料可以直接影响刀具的使用寿命。如陶瓷刀具。陶瓷刀具具有硬度高、耐磨性能及高温力学性能优良、化学稳定性好、不易与金属发生粘结等特点。陶瓷刀具的最佳切削速度通常可比硬质合金刀具高3~10倍,适用于高速切削钢、铸铁及其合金等。陶瓷刀具用于高速切削时,切削温度可高达800~1000℃甚至更高,切
27
石家庄铁道大学毕业论文
削压力也很大。因此,陶瓷刀具的磨损是机械磨损与化学磨损综合作用的结果,其磨损机制主要包括磨料磨损、粘结磨损、化学反应、扩散磨损、氧化磨损等。陶瓷刀具的磨损与切削条件密切相关,在高速切削时以高温引起的粘结磨损、化学反应、氧化磨损和扩散磨损为主。
综合实验数据对刀具磨损的影响可知切削速度的影响。
切削速度对刀具寿命有非常大的影响.提高切削速度时,切削温度就上升,而使刀具寿命大大缩短.加工不同种类、硬度的工件,切削速度会有相应的变化。
进给量是决定被加工表面质量的关键因素,同时也影响加工时切屑形成的范围和切屑的厚度.在对刀具寿命影响方面,进给量过小,后刀面磨损大,刀具寿命大幅降低;进给量过大,切削温度升高,后刀面磨损也增大,但较之切削速度对刀具寿命的影响要小.
切削深度应根据工件的加工余量、形状、机床功率、刚性及刀具的刚性来确定.切削深度变化对刀具寿命影响不大.切削深度过小时,会造成刮擦,只切削工件表面的硬化层,缩短刀具寿命.当工件表面具有硬化的氧化层时,应在机床功率允许范围内选择尽可能大的切削深度,以避免刀尖只切削工件的表面硬化层,造成刀尖的异常磨损甚至破损.
5.2.2刀具表面涂抹其他材料
在刀具表面上涂一层其他物质,有利于减少刀具的磨损,延长刀具使用寿命。涂层刀具结合了基体高强度、高韧性和涂层高硬度、高耐磨性的优点,提高了刀具的耐磨性而不降低其韧性。涂层刀具通用性广,加工范围显著扩大,使用涂层刀具可以获得明显的经济效益。一种涂层刀具可以代替数种非涂层刀具使用,因而可以大大减少刀具的品种和库存量,简化刀具管理,降低刀具和设备成本。但是刀具在现有的涂层工艺进行涂层后,因基体材料和涂层材料性质差别较大,涂层残留内应力大,涂层和基体之间的界面结合强度低,涂层易剥落,而且涂层过程中还造成基体强度下降、涂层刀片重磨性差、涂层设备复杂、昂贵、工艺要求高、涂层时间长、刀具成本上升等缺点。常用的涂层材料有碳化物、氮化物、碳氮化物、氧化物、硼化物、硅化物、金刚石及复合涂层八大类数十个品种。根据化学键的特征,可将这些涂层材料分成金属键型、共价键型和离子键型。
5.2.3工件的材料
工件材料可分为两点。一是本身就拥有较高的物理性能。有些工件的材料具有较高的硬度,如果材料较软的刀具就会对刀具磨损影响很大。再有就是被加工工件进行过热处理。使得工件材料本身的一些性能发生改变,也会影响刀具的磨损。
28
石家庄铁道大学毕业论文
5.2.4切削速度的影响
高速切削加工对刀具提出了一系列新的要求。研究表明,高速切削时,造成刀具损坏的主要原因是在切削力和切削温度作用下因机械摩擦、粘结、化学磨损、崩刃、破碎以及塑性变形等的引起的磨损和破损。因此,对高速切削刀具材料最主要的性能要求是耐热性、耐磨性、化学稳定性、抗热震性以及抗涂层破裂性能等。在高速切削加工中,与普通切削加工类似,也存在两个摩擦副:前刀面与切屑间的摩擦副和后刀面与已加工表面间的摩擦副。其中,前者影响刀具前刀面的磨损,后者影响刀具后刀面的磨损,前、后刀面的磨损均影响刀具寿命。但与普通切削相比,高速切削时刀具与工件的接触时间减少,接触频率增加,切削过程中产生的热量更多向刀具传递,因此其磨损机理与普通切削有很大区别。速切削时,应根据加工方法和加工要求确定合理的刀具磨损寿命(极限)。影响高速切削刀具磨损寿命的因素较多,如工件材料与刀具材料的匹配、切削方式、刀具几何形状、切削用量、冷却液、振动等对刀具磨损寿命都有显著影响,其影响规律与具体切削条件有关,应通过切削试验来确定各相关因素对刀具磨损寿命的影响效应。
第7章 结论与展望
7.1总结
本文主要以DHL200为实验平台,进行了实验。采用声发射,振动,两种途径进行车刀的磨损实验,并相应开发出一套具有实时信号采集、多传感器信号融合、历史信号分析、故障诊断的数控机床故障诊断系统。本文得出成果及结论总结如下:
(1)在收集大量资料的基础上进行了数控机床的故障模拟实验。文中主要介绍了刀具磨损试验。实验得出,声发射、振动是研究刀具磨损状态的很好的手段。声发射覆盖高频,振动对应低频,更加确保整个监测过程的准确性。
(2)以LabVIEW10.0为平台,开发了一套具有实时数据采集、历史信号分析、故障诊断功能的数控机床故障诊断系统。
(3)实现了数控机床故障诊断的网络化远程传输技术,替代现在常用的网络化传输的方法,并进行了比较和实现方式的说明。可以更好的满足需要远程监测的用户的需求,实现对机械设备进行远程信号的采集和状态监测,
(4)软件上利用 LabVIEW 作为编程语言,简单易学,缩短了开发时间,而且设计的操作界面美观,使用者易于操作。基于虚拟仪器的辅助教学系统设计使得单片
29
石家庄铁道大学毕业论文
机的教学过程变得简单,理论教学和实践教学均可在课堂进行,无需转换教学地点,也不受实验场地时间安排冲突的限制。
7.2 展望
近二十年来我国机械设备状态监测与故障诊断系统经历了从离线系统到在线系统、从事后维修到预防维修,从人工诊断到智能诊断的发展历程,新一代的故障诊断系统(包括软件系统和硬件系统)的研制,也是故障诊断技术的发展趋势之一。
限于知识、时间和一些客观的实验条件,本课题的研究并未做到尽善尽美,还可从以下方面展开进一步的探讨:
(1)研究更多类型监测信号实现故障状态监测的可行性,将多个监测信号进行自动合理选择,提高故障状态监测的可靠性和准确性。
(2)提供更多的信号分析的方法。如小波分析的方法可以有更多选择。
参考文献
[1].陈侃 , 基于多模型决策融合的刀具磨损状态监测系统关键技术研究,西南交通大学研究生
学位论文,2012
[2].刘飞,智能机床发展现状与技术体系框架,机械工程学报,2013. [3].曹伟青,傅攀,谢绣娴.B样条模糊神经网络在刀具磨损监测中的应用.工具技
术,2005,(12):66一68
[4].B.M. Kramer.A Comprehensive Tool Wear Model . Annals of CIPP . Vol135 , NO.1 [5].李岩,机械制造领域测量技术的发展研究机械工程学报,2010
[6].刘红奇,小波包分析技术在电流刀具磨损监测系统中的应用,华中科技大学,2010; [7].冯艳,罗良玲,夏林.基于LabvIEW的刀具磨损在线监控系统.制造技术与机床,2008,(12):17
一20;
[8].刘敦焰.基于切削参数与刀具状态的车削力及功率建模硕士学位论文.上海交通大学,2006; [9].DimlaE,Dimla.SensorsignalsfortoolwearmonitoringinmetaleuttingoPerationSareviewo
fmethods.IntemationalJoumalofMaehineTOols&Manufaeture,2000,40(8):1073-1098 [10].BenlllardSiek.FusionofHardandSoftComPutingTeehniquesinIndireet,OnlineToolWarMo
nitoring.IEEEtransaetionsonsystems,man,andcyberneticsPartC,apPlieationsandreviews,2004,32(2):80-90;
[11].H.M.Ertune,K.A.Loparo.Adeeisionfusionalgorithmfortoolweareonditionmonitoringin
drilling.InternationalJournalofMachineTOolsandManufaetuxe,2007,41(9):1347-1362
30
石家庄铁道大学毕业论文
[12].M.A.Mannan,Ashraf.A.Kassim,MaJing.APPlieationofimageandsoundanalysis teehniquestomonitortheeonditionofcuttingtools.PattenxReeognitionLetters, 2000,21(11):969一979
[13].D.E.Dimla,P.M.Lister.On-linemetalcuttingtooleonditionmonitoring.11: Tool-stateelassifieationusingmulti-layerPercePtionneuralnetworks.International
JoumalofMachineTOols&ManufactUre,2000,40(5):769-781
[14]路勇,姚英学.模糊神经网络在刀具磨损检测中的应用.机械制造,2003,41(3):47一49; [15]刘敦焰.基于切削参数与刀具状态的车削力及功率建模硕士学位论文,上海交通大学,2004; [16]舒服华.基于小波神经网络的刀具状态监测.组合机床与自动化加工技术,2006,(1):69一
70,78;
[17]李菊欢.基于分形理论和神经网络的刀具磨损在线监测硕士学位论文,华南理工大学,2003; [18].李曦.端面车削的刀具磨损监测7硕士学位论文〕.上海:上海交通大学,2005; [19].郑铁柱.复杂背景下图像分割与运动目标检测[D].云南:云南大学,2009
[20].章珂.基于虚拟仪器的电能质量监测系统的设计与研究[D].重庆:重庆大学,2009 [21].柴慧霞,基于LabVIEW的轴承状态监测及故障诊断系统实现[D].山西:太原理工大学,2005
致谢
历时将近两个月的时间终于将这篇论文写完,在论文的写作过程中遇到了许多的困难和障碍,都在老师和同学的帮助下,艰难地度过。尤其要感谢我的论文指导老师—**老师,她对我进行了无私的指导和帮助,不厌其烦的帮助进行论文的修改和改进。在此向帮助和指导过我的老师表示最衷心的感谢!
感谢我的同学和朋友,在我写论文的书写过程中给予我了很多素材与建议,还在论文的撰写和排版灯过程中提供热情的帮助。
感谢这篇论文所涉及到的各位学者。本文引用了数位学者的研究文献,如果没有各位学者的研究成果的帮助和启发,我将很难完成本篇论文的写作。
由于我的学术水平有限,所写论文难免有不足之处,恳请各位老师和学友批评和指正!
31
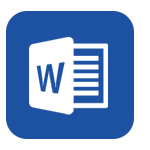





正在阅读:
秦兵马俑教学设计(含学讲方式)04-03
激光原理实验 - 图文11-04
弘扬科学精神 提升科学素养09-16
我喜爱的小熊作文600字06-30
b6重庆市2013届九年级化学下学期“个适课堂”第一次月考试题(无答案) 新人教版06-10
钢筋混凝土现浇工程施工合同协议书范本03-24
浅谈如何指导小学生进行课外阅读10-14
北体体育管理学要点和问题04-24
电子行业职业技能鉴定理论试卷 中级证M卷04-13
- 多层物业服务方案
- (审判实务)习惯法与少数民族地区民间纠纷解决问题(孙 潋)
- 人教版新课标六年级下册语文全册教案
- 词语打卡
- photoshop实习报告
- 钢结构设计原理综合测试2
- 2014年期末练习题
- 高中数学中的逆向思维解题方法探讨
- 名师原创 全国通用2014-2015学年高二寒假作业 政治(一)Word版
- 北航《建筑结构检测鉴定与加固》在线作业三
- XX县卫生监督所工程建设项目可行性研究报告
- 小学四年级观察作文经典评语
- 浅谈110KV变电站电气一次设计-程泉焱(1)
- 安全员考试题库
- 国家电网公司变电运维管理规定(试行)
- 义务教育课程标准稿征求意见提纲
- 教学秘书面试技巧
- 钢结构工程施工组织设计
- 水利工程概论论文
- 09届九年级数学第四次模拟试卷
- 数控机床
- 刀具
- 远程
- 构建
- 诊断
- 故障
- 面向
- 系统
- 平台
- 七年级地理天气和气候同步检测试题
- 干部职工作风纪律整顿心得体会6篇-最新年文档
- 互联网+的论述
- 贵州威宁企业孵化器项目可行性研究报告
- 景观生态学综述
- 江苏二级建造师继续教育考试复习资料(法规与项目管理)
- 中国新能源汽车产业政策深度调研报告2018年版(目录) - 图文
- 管道完整性管理-5完整性评价技术
- 2016年秋人教版三年级数学上册第六单元《多位数乘一位数》测试题
- 2018年输送设备市场调研及发展前景趋势预测 (目录)
- 高频实验指导书
- 8.1中东 学案 5(人教新课标七年级下册) - 图文
- 青岛写字楼报告
- 浅谈小学数学教育中学生想象力的培养
- 立体几何练习题(含答案)
- 管理学习题集
- 竹炭纤维简介
- 体育保健复习资料
- 《鹬蚌相争》教学实录
- 疾病控制人员三基试题库及答案