武钢三炼钢250吨转炉施工组织设计
更新时间:2024-05-29 13:46:01 阅读量: 综合文库 文档下载
- 武钢三炼钢厂推荐度:
- 相关推荐
目录 1. 工程概述 2. 组装场地
3. 组装专用平台、台架及工装 4. 设备进场 5. 施工平面布置 6. 安装 7. 转炉就位 8. 转炉倾动装置安装 9. 施工工期计划网络 10. 施工技术措施 11. 安全技术措施 12. 工、机具及材料汇总表 13. 附图
1. 工程概述
武钢三炼钢厂是武钢双1000吨配套工程,其年生产能力最小为250吨合格钢水和180吨合格连铸板坯,首期工程为“二吹一”配置,主要设备为两公称容量各250吨顶、底复吹转炉和一台双流板坯连铸机,其转炉系统由德国曼内斯曼-德马克冶金技术公司提供全面技术服务,主体设备由西班牙欧控公司组织制造。
一冶机装承担的250吨转炉系统,主体设备:转炉炉壳、转炉托圈、转炉悬挂装置、耳轴轴承及轴承座、转炉倾动装置等,该转炉是我国续宝钢后最大的一座转炉,因为运输和制造地的原因,上述设备均是分为各个部件运到安装现场,其中:转炉炉壳分为三段:转炉托圈分为两半圈,(具体净重,箱尺寸见表1)在安装现场将其组装、焊接后就位。
该工程的组、安装的难度之大,在我国冶金建设史上是首例,因此,严谨的技术、施工准备,有目的地焊工培训,各种专用机、工具的购置等工作是保证转炉安装质量和工期的先决条件。 附表1 部件名称 炉壳上锥 中段 下段 长轴半托圈 短轴半托圈 净重(KG) 69758 83172 110749 115320 106561 长×宽×高(mm) 8500×8500×3030 8500×9910×4310 10460×10460×3850 13000×5500×5300 11400×5500×5300 2. 组装场地
2.1 组装场地的平面位置,组装场地设在主厂房AB跨(7)~(9)线之间(见附图01)
2.2 组装场地的要求:由表01可见,组装后炉壳重量为2630679t;托圈为221.881吨;加上轴承及轴承箱总重量达517吨,炉壳全高10.8m;YBJ202-83规定: 垂直度:全长<5.5mm 两耳轴同心度:<1.5mm
外形尺寸及体积如此大的设备,组装精度要求这么高,就要求组装台架放置在牢固的地基上,保证在整个组装过程中不产生不均匀下沉现象,为此,要求在组装场地区域内的地面应在组装之前按设计要求完成地坪的施工达到设计承载值。 3. 组装专用平台,台架及工装
组装平台采用δ=30~40mm钢板,铺设在地板上,铺设区域见附
图01。
组装炉壳及托圈专用台架均为钢结构台架,组装炉壳和托圈各一
套(见附图02、03)。
由于组装好的炉体不能马上吊运至基础上,因此需临时存放台架
一套(见附图01)存放组装好的第一台炉体,以便在组装台架上组装第二台炉体。
炉壳、托圈组装、吊运工装:
3.4.1 炉壳每圈的吊运用原炉壳上的吊耳吊装,钢绳选用6×37+1
d=52.0mm k=1667MPa 单根安全吊重:34.1吨 选用四根长度7m,吊环先用40吨,8个。
3.4.2 托圈每半圈的吊运均用原托圈上的吊耳吊装,在轴颈处设一个专用夹吊点,钢绳先用6×37+1 d=52.0mm k=5 δ=1667MPa 单根安全吊重:34.1吨 选用四根,每根14m,吊环选用40吨,8个。
3.4.3 托圈整体吊运至炉体组装处,采用8点吊装,钢绳选用上述14m四根双吊,吊环选用40吨,8个。 3.4.4 轴承吊具见轴承安装。
3.4.5 组装好后的整体炉体吊运至临时承放台及运输车上,采用专用吊具(见附图07)。 4 设备进场
4.1 炉壳及托圈等部件,根据一冶施工组织总设计及现场实际平面,拟定从AB跨(12)线进入厂房,设备部件最大宽度10.46m,最大高度5.30m,最大长度为13.0m,考虑到拖车组高度为1.20m,故AB跨(12)线外及(11)线山墙处应保证最长,最宽件运输车组的转弯半径?m,最高件的通过空间7m。
4.2 设备进场后的堆放场地在(10)~(12)线450吨/80吨桥吊覆盖区域内(见附图01)。
5. 施工平面布置及用电点等(见附图01)。
5.1 施工平面布置及设置工人休息室,工具、机具存放室、氧气乙炔气存放处等设施。
5.2 施工用电量约:1250Kw(峰值) 主要用电器:交流焊机 8台 256Kw 直流焊机 4台 112Kw 焊条烘箱 2台 20Kw 空压机6m2 1台 30Kw
坦克加热带(620×370 10Kw)85片 850Kw 油箱电加热器 4支 40Kw 其他 10Kw 6.
组、安装(安装工序见工序图)
托圈组装:将两个半托圈依次吊至组装台架上,利用设备部件原
组装定位件将托圈组对好,其水平方向垂直方向的调整用千斤顶调整。在中心轴孔中拉一根钢琴线,并加辅佐线和光学仪器配合在4个点控制组装托圈的同轴度,其几何尺寸符合规范要求或国外提供要求后,经专检、甲方质监人员、外方专家共同认可后,方可进行焊接工序(焊接工艺另见焊接作业设计)。
炉壳组装
将炉壳下段吊至炉壳组装台上,按要求找正好。焊好就位支承点
支承座(八个)
吊运已焊接组装合格的托圈至下炉壳上,并支撑好。 吊运中段炉壳与下炉壳组对达到要求。 按焊接工艺(另见焊接作业设计)焊接炉壳。
将已焊接合格的炉壳与托圈用柔性联接装置按设计要求连接起来
(注:仍需用四个70吨~100吨千斤顶顶着托圈,并用钢制支座将托圈牢固支起)
基础验收及测量放线 轴承支座安装 平台搭设 轨道安装 二次灌浆 托圈组装、焊接 钢水罐车安装 支座精平 炉壳组装、焊接 炉体悬挂装置安装 轴承及轴承箱安装 转炉就位 转炉找正 润滑油注入 倾动装置安装 冷却水系统 试运转
炉底砌筑 工序图表
吊运上段锥体至炉体上,找正、焊接(包括出钢口焊接)
托圈耳轴如在国外未到“零位线”,还需在轴端标是“零位线”(转
炉处于垂直吹炼位置)。
轴承支座安装 基础测量及放线
6.3.1.1基础按《YBJ201-83>有关条款进行检查验收。
6.3.1.2根据土建移交的中心及标高点,投放出支座安装的控制网点,投刻在中心标板及基准点上,中心标板及基准点的布置见附图
支座就位
因现无详细资料,根据出国人员带回的图,暂拟定选用40吨液压吊将两侧轴承支座吊至基础上,吊装示意图见附图。
支座安装
国外图纸31388130和31388230所示支座,其设计意图利用支座上的4个M36调整螺栓找正支座,根据此图拟定用调整螺栓找正,支座四周加放若干支撑垫铁,初拧紧地脚螺栓交付二次灌浆,二次灌浆料应符合设计要求,待二次灌浆应达到设计强度时终拧紧螺栓。 将两侧下轴承座吊至支座进行安装检查(轴线、高程等)符合设计要求后,做好标记,再吊下组装在炉体上待运。
轴承、轴承箱安装
安装轴承前,要先测量轴承实际内经(内经千分尺1.5m)和轴颈
处的实际外经(特制大外卡配合内经千分尺)计算出实际公盈量。
根据实际公盈量,确定出是单加热轴承膨胀,还是加热轴承膨胀,
冷却轴颈缩小同时进行的方案
方案确定后,根据实际过盈量,实际操作时间内因温升或温降而
造成的膨胀收缩量,计算出轴承加热、轴颈冷缩后的需要量。
加热轴承制作一个加热油箱采用管式电加热器10Kw4根,油:轧
钢机油。冷缩轴承可用液氮对中心轴内喷吹。加热温度控制100~120°C(热电偶控制)
制作2套吊装轴承用专用吊具(见附图)
用专用吊具将轴承吊入油箱内加热,加热过程中可用一根经计算
确定的标准样板来检查轴承的膨胀量。
用罐车将液氮运至现场,在轴承加热同时,对轴颈进行喷吹冷缩。 用吊车将已加热膨胀的轴承吊出,利用托圈上已焊好的拉耳挂上1
吨倒链2台,挂在轴承专用吊具上将轴承拉入轴上,这两台倒链待轴承冷却完已定位在设计位置上方可取下。
将轴承箱装在轴承上,轴承箱安装时要检查轴承瓦座与轴承箱体
的接合情况是否符合技术要求,至于轴承与轴瓦的结合情况待整体安装就位后再检查。 7
将全部组装好的炉体吊至临时存放台架上,固定好待就位 炉体就位
该炉体耳轴中心标高为+12.250m,承运台架也很高,从±0.000标
起,运输过程中,炉口高程可达+18.000m,炉体、承运台架、运输车辆总重可达:650吨,这样一个庞大物体的水平运输,其运输轨道的平直度,基础的承压强度均直接影响转炉炉体安全运输,因此,要求A-B-C列,(4)-(5)-(6)线间的钢水运输车轨道按设计要
求完成,轨道安装标准(YBJ202-83).
转炉炉体运输采用450吨钢水运输车,由于是超载运行,可能要
对该车进行加固,现无车详图,无法拟出加固方案,待车到货后,现场视情况加固,或采用双车运算。
炉体承运台架采用钢结构框架形式(见附图05)
转炉运输车的牵引动力用5吨慢速电动卷扬机,牵引速度1m/min,
牵引滑轮组为4×4(具体布置见附图01)。
用450吨桥吊将炉体(517吨)吊运在承运台架上(超载15%),
当吊运至承运台架下降至承运台架支承点间距约100mm时,用千斤顶(200t-300t)升顶接住,接稳后,用支座支撑好并焊接牢固后,松开千斤顶。
当运输车拖至转炉基础处(可用定位轨卡定位),升起千斤顶顶劳
炉壳,切割开支座焊缝,缓慢地同时降下千斤顶,让炉体轴承箱平稳地座在轴承箱支座上,并找正好,如找正过程中,尚需调整高度时,亦可利用承运车台架升顶调整。
待1#炉体经检查其安装达到设计要求后,方可将承运台架吊至
2#炉钢水运输车上进行2#转炉炉体的就位工作,其方法同1#转炉炉体就位法。 8
转炉倾动装置的安装
由于无该装置的详图,其发运形式,重量亦不知,故无法提出具
体安装方案,只能参照宝钢300t转炉方案,暂拟一方案。
制作一个钢台架,高度从±0.000平面至基础上平面,将倾动装
置用总铁水吊车至钢台架上,采用滑道加倒链的方法,拉到基础上的专用钢滑道板上(δ=50mm)在钢滑道板用四台合适的千斤顶将倾动装置顶起,调整至安装高度,再水平牵引安装在耳轴上。
安装前B-B1跨转炉传动侧(5)-(4)、(6)-(5)+11.000平
台不得,待倾动装置安装就位后方可施工。 9
炉体组装,就位施工工期,劳动力计划网络。
炉体组装待现场条件具备,设备部件到货后即可进行。炉体就位
需待汽化烟道系统安装就位后进行。(汽化烟道系统安装另见方案) 10
网络见网络图。 施工技术措施
施工前 ,仔细消化设计,认真详细的进行技术交底。
焊接前,对焊工进行培训,其培训人员可25-30名。培训合格后,
方可进行实体焊接。
施工操作中需定量控制的,均采用各种标定计器进行控制,如加
热采用热电偶等。
施工过程中,严格按审定方案作业,严格执行“三检”制度,工
序合格后才能进行下道工序。
施工过程中所用计器计量器具均经计量测验合格方可用于施工计
量。 11
现场实行挂牌施工,标准、工艺做到人人皆知。 安全技术措施
正式吊装前,需对桥式吊车450t-80t司机进行熟练操作培训,以
保证大件的准确,平稳吊装,培训人员不少于3人。
所有吊具,吊索均要逐一进行检验,确认合格后方可突入,千斤
顶均要进行负载试升顶,合格后方可使用,每次重载均应检查确认后方可再次使用。
全体施工人员均需经安全交底方可进入现场施工,并自觉按安全
操作规程执行。
吊装的信号应准确、明白,哨音清晰,专人指挥,卷扬牵引时,
各滑轮处设专人看守,紧急情况有权通知司机停车。
托圈、炉壳焊接处搭设的脚手架(采用门型架上铺设木跳板)应
符合安全标准,并有挂设安全带的挂点,(脚手架的具体搭设根据焊接作业设计的焊接工序而定) 12
所有用电器每天均应检查其安全使用的可靠性。 焊接作业的安全技术见焊接作业设计。 工、机具及材料
名称 320t千斤顶 100t千斤顶 70t千斤顶 数量 4台 16台 4台 备注 顶升整个转炉 组装托圈 支撑托圈 50t千斤顶 倒链各种 内径千分尺 大外卡 千分表 经纬仪 水准仪 水准仪 H20×4 H10×1 5t慢速电动卷扬 6×37+1-52.0 6×37+1-21.5 卡环 卡环 钢板 型钢 脚手架钢管 脚手架扣件 门型脚手架 木跳板 枕木
8台 20台 1.5m 1.2m J2 R2 N3 配铟钢尺 KD滑子 导向滑子 δb=1667MPa δb=1667MPa 40t 10t 各种 各种 组装组对 1套 1把 8块 1台 1台 1套 2套 2个 1台 200m 250m 8个 4个 220吨(平台、支撑台架等) 30吨(支撑台架、安全设施) 3.5吨 400套 120付 300块 50根 施工网络计划及劳动力安排 1
九四年 10月 11月 12月 1月 2月 3月 4月 5月 九五年 6月 7月 8月 9月 10月 11月 12月
450/80t桥式吊安装施工网络日期97年3月份97年4月份97年5月份主小车下部UC2设备安装8UC1设备安装16ABCD与GHEF梁连接151718GHEF梁连接副小车主小车就位就位192021三炼钢450/80t桥式吊施工网络进度表GH梁设EF梁设吊装并推吊装并推设备备安装备安装AB梁出作业区出作业区进场清洗123设备456911121314安装CD梁设ABCD梁吊装并推备安装连接出作业区主小车下部UC设备安装7主小车下部UC设备安装10其它设备安装22穿主、副钢绳232425无负荷试车负荷试车26桥架检查调试单体试车吊机调配劳动力组织10t25t16t80t钳工6人架工8人电焊1人火焊1人电工1人测量工4人1、以上时间为绝对工期,桥式吊正式上场安装时间估计为97年3月份,由于现场实际情况,主梁及副梁不能同时运抵现场,需安装完一片进一片,故设备安装不能同时进行;2、因安装工程受生产条件限制,故整个安装周期拉长,作业序列为单工序作业。备注炉体存放平台A0/10t0/80t炉体组装平台15×15225m215×15225m2在圈组装平台设备存放区设备进场0514B工具间焊机房氧气乙炔扒渣机平台6m3空压机CD12346789101112施工平面布置图炉体组装工序示意图
托圈组对焊接台架示意图 A-A托圈支撑示意图 运送台架示意图 炉体吊具 450t/80t千斤顶滚杠道板台架基础基础10t倒链倾动装置安装示意图 三炼钢转炉炉壳即托圈焊接方案 一、三炼钢250t-LD转炉炉壳总重276t,分上、中、下三段在现场焊接,两条环缝总长53米。两台共106米。托圈总重232t。分长轴、短轴两部分,在现场对接,其箱型断面连接焊缝总长15米,两台共
30米。 二、炉壳的焊接
1. 转炉炉壳材质有两种,WSTE285和WSTE355,厚度有三种规格,δ=65mm,δ=85mm,δ=95mm,焊缝要求100%超波探伤验收标准DIN8565T3-BS级合格,其具体焊接接头形式如下图: 2. 炉壳的焊接方法设备及焊接材料
炉壳选用CO2气体保护半自动焊。为保证焊接质量,选用芬兰产KEMPPT牌PSS3500/5000型。焊接材料选用HOSMn2SiAф1.2,焊丝保护气体与Ar混合气体。(暂定为CO2气体保护焊) 3. 焊接规格参数
a、焊接电流 180-280A b、焊接电压 22-28V c、电源极性 直流反接法
d、保护气体 Ar+CO2 打底填充50%:50%,盖面80%:20% 气体流量14-20l/min
f、喷嘴 喷嘴直径ф25mm,喷嘴到工件距离15-20mm g、焊接速度 350-400mm/min 4. 焊接工艺措施
a、 组装前将坡口附近50mm范围打磨干净,不留间隙 b、
焊前CO2气体必须进行干燥处理,倒臵24小时,放水两至三
次,使用时还必须通过硅胶干燥器再处理一次。
c、 预热:预热温度100-125°C,用履带式远红外加热器加热,焊缝
两侧均匀布臵,保温厚度50mm。温度控制采用热电偶自动测温控制。 d、
点固 点焊同正式焊接规范一样,点固长度80×200
e、 焊接程序 沿周长方向靶等分,两人一组,(轮流操作),同向施焊,采用间断对称焊法300×300,层间温度必须控制在250°C左右,经常用测温笔监控。同时要注意焊接变形,随时采取反变形施焊措施。
f、 炉壳上中环缝是先外后内,内面气刨,中下环缝是先内后外,外面气刨,内外同时盖面。 g、
盖面时调整混合气体比例,增加Ar气流量,保证良好外观成
型。 三. 托圈的焊接
1、 托圈材质为WSTE355,其截面为箱体结构,上下盖板及侧板焊
接位臵如下图,焊缝均100%超波探伤,按DIN856T3-BS级验收合格。其焊接接头形式如下图: 2、 焊接方法设备及材料
托圈焊接位臵有平焊、立焊、仰焊,选择手工电弧焊比较合理。电源为逆变式弧焊电源,焊接材料为E5018结构钢焊条。 3、 焊接工艺参数
a、 焊接电流 焊接电流 焊接电压
ф3.2 90-140A 22-24V
ф4 130-180A 24-26V
ф5 170-250A 25-27V b、 电源极性 直流反接法 c、 焊接速度 200-300mm/min 5. 托圈焊接工艺措施
a、 组装前将坡口附近50mm处打磨干净,不留间隙 b、 预热:预热温度100-150°C,预热方式同炉壳一样。
c、 焊接成序:先焊立缝,四条立缝四人同时在中心线焊接1/3,然
后上下盖板,侧板同时对称焊接,焊速较快,焊道要薄,控制层间温度不大于250°C。
d、 托圈安装精度要求高,同轴度为±1.5mm,焊接时在轴孔中心线
拉一钢线,用内径千分尺在垂直方向,水平方向长轴、短轴各两套共八处检查,随时用反变形的焊位校正。
e、 托圈上下盖板及侧板焊缝全部为先内后外,外面气刨,清根一定
要彻底,同时保证尽可能清根深度宽度一致,全位臵对称焊接。 f、 焊工应严格按焊接技术要求操作,尽量保持焊缩一致,每一焊道
要清理干净。
四. 炉壳及托圈焊接的安全措施
无论是炉壳还是托圈,焊接量较大,通风条件差,而且作业环境温度高,所以必须采取鼓风机或抽风扇通风。电热器加热,加热前一定要检查绝缘情况,保证安全用电。另外,由于焊缝要立体作业,脚手架一定要安全可靠。 五. 焊工培训
1、 培训项目
针对炉壳及托圈的环境特点,专项培训:(1)CO2气体保护半自动焊,环境位臵横焊。(2)厚板手工电弧板环接位臵,平焊、立焊、仰焊。 2、 培训人数,每项20人 3、 培训时间,每项一个月 4、 培训考核:5、 培训用材
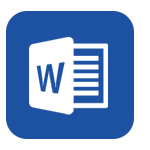





正在阅读:
武钢三炼钢250吨转炉施工组织设计05-29
车身型式的定义11-05
物理奥赛模拟试题04-12
防雷、防静电安全管理制度06-11
2022年关于学校德育个人工作总结范文03-23
动词第三人称单数练习题12-13
苏教版小学语文第二册教案07-04
- 多层物业服务方案
- (审判实务)习惯法与少数民族地区民间纠纷解决问题(孙 潋)
- 人教版新课标六年级下册语文全册教案
- 词语打卡
- photoshop实习报告
- 钢结构设计原理综合测试2
- 2014年期末练习题
- 高中数学中的逆向思维解题方法探讨
- 名师原创 全国通用2014-2015学年高二寒假作业 政治(一)Word版
- 北航《建筑结构检测鉴定与加固》在线作业三
- XX县卫生监督所工程建设项目可行性研究报告
- 小学四年级观察作文经典评语
- 浅谈110KV变电站电气一次设计-程泉焱(1)
- 安全员考试题库
- 国家电网公司变电运维管理规定(试行)
- 义务教育课程标准稿征求意见提纲
- 教学秘书面试技巧
- 钢结构工程施工组织设计
- 水利工程概论论文
- 09届九年级数学第四次模拟试卷
- 转炉
- 炼钢
- 组织设计
- 武钢
- 施工
- 250
- SMT实训心得体会
- 四年级下学期音乐教案
- (山香版)教材重点笔记 - 1教育学
- 中学生文史知识题
- 000单片机函数信号发生器设计
- 公共行政学学习指导简答题参考答案
- 华为笔试--ICD呼叫中心试题库(203题)
- TMS320F28035中文数据手册-2013版
- 永州三下乡日志 - 图文
- 生理学复习资料选择题的练习及答案
- 四年级语文培优补差工作计划
- 倚天照海处 流水高山境——读《曾国藩传》有感
- 部编版新人教版小学语文一年级下册:21.小壁虎借尾巴(课堂实录
- 电梯技术题库
- 湖南省三级综合医院评审标准考评办法
- 07款别克君威使用说明书
- 《模拟电子技术》复习题10套及答案
- 化学校本课程《趣味化学实验》
- 网络营销学习指导与练习教材习题答案
- 工程审计中的问题和对策