盘式制动器设计说明书原版
更新时间:2023-04-26 12:29:01 阅读量: 实用文档 文档下载
盘式制动器设计说明书
原版
IMB standardization office【IMB 5AB- IMBK 08- IMB 2C】
课程设计说明书
学院机电工程学院
专业班级 12级车辆工程2班
学号
姓名邓汉佳、林滔、
吴广军、吴一平
指导老师冯桑
2016年 01 月 10日
目录
第一章汽车制动系概述 (3)
第二章汽车主要参数 (5)
第三章制动器形式的选择 (5)
第四章盘式制动器主要参数的确定 (9)
1制动盘直径D (9)
2制动盘的厚度h (9)
3摩擦衬块外半径R2与内半径R1 (9)
4制动衬块工作面积A (9)
五盘式制动器的设计计算 (9)
1.同步附着系数的确定 (9)
2.制动力分配系数的确定 (10)
3.前,后轮制动器制动力矩的确定 (11)
4.制动强度和附着系数利用率 (11)
5.制动器最大制动力矩 (13)
6.制动器因数 (13)
7.应急制动和驻车制动所需的制动力矩 (14)
8.衬块磨损特性的计算 (15)
9.盘式制动器制动力矩的计算 (16)
第六章制动器主要零部件的结构设计 (18)
1.制动盘 (18)
2.制动钳 (18)
3.制动块 (18)
4.摩擦材料 (18)
5.制动器间隙的调整方法及相应机构 (19)
6.液压制动驱动机构的设计计算 (19)
(19)
(21)
(21)
第一章汽车制动系概述
使行驶中的汽车减速甚至停车,使下坡行驶的汽车的速度保持稳定,以及使已经停驶的汽车保持不动,这些作用统称为汽车制动。
对汽车起到制动作用的是作用在汽车上,其方向与汽车行驶方向相反的外力。作用在行驶汽车上的滚动阻力,上坡阻力,空气阻力都能对汽车起制动作用,但这外力的大小是随机的,不可控制的。因此,汽车上必须设一系列专门装置,以便驾驶员能根据道路和交通等情况,借以使外界在汽车上某些部分施加一定的力,对汽车进行一
定程度的强制制动。这种可控制的对汽车进行制动的外力,统称为制动力。这样的一系列专门装置即成为制动系。
1 制动系的功用:使汽车以适当的减速度降速行驶直至停车;在下坡行驶时,使汽车保持适当的稳定车速;使汽车可靠的停在原地或--=-坡道上。
2 制动系的组成
任何制动系都具有以下四个基本组成部分:
(1)供能装置——包括供给、调节制动所需能量以及改善传能介质状态的各种部件。其中,产生制动能量的部位称为制动能源。
(2)控制装置——包括产生制动动作和控制制动效果的各种部件。
(3)传动装置——包括将制动能量传输到制动器的各个部件。
(4)制动器——产生阻碍车辆的运动或运动趋势的力的部件,其中也包括辅助制动系中的缓速装置。
较为完善的制动系还具有制动力调节装置以及报警装置、压力保护装置等附加装置。
3 制动系的类型
(1)按制动系的功用分类
1)行车制动系——使行使中的汽车减低速度甚至停车的一套专门装置。
2)驻车制动系——是以停止的汽车驻留在原地不动的一套装置。
3)第二制动系——在行车制动系失效的情况下,保证汽车仍能实现减速或停车的一套装置。在许多国家的制动法规中规定,第二制动系是汽车必须具备的。
4)辅助制动系——在汽车长下坡时用以稳定车速的一套装置。
(2)按制动系的制动能源分类
1)人力制动系——以驾驶员的肢体作为唯一的制动能源的制动系。
2)动力制动系——完全靠由发动机的动力转化而成的气压或液压形式的势能进行制动的制动系。
3)伺服制动系——兼用人力和发动机动力进行制动的制动系。
按照制动能量的传输方式,制动系又可分为机械式、液压式、气压式和电磁等。同时采用两种以上传能方式的制动系,可称为组合式制动系。
4 设计制动系时应满足如下主要要求:
1)具有足够的制动效能。行车制动能力是用一定制动初速度下的制动减速度和制动距离两相指标来评定的;驻坡能力是以汽车在良好路面上能可靠的停驻的最大坡度来评定的。详见GB/T7258-2004
制动距离:是指机动车在规定的初速度下急踩制动时,从脚接触制动踏板(或手触动制动手柄)时起至机动车停住时止机动车驶过的距离。
制动减速度:是指机动车制动时车速对时间的导数。制动稳定性要求:是指制动过程中机动车的任何部位(不计入车宽的部位除外)不允许超出规定宽度的试验通道的边缘线。
表制动距离和制动稳定性要求
表制动减速度和制动稳定性要求
2)工作可靠。行车制动装置至少有两套独立的驱动制动器的管路,当其中一套管路失效时,另一套完好的管路应保证汽车制动能力不低于没有失效时规定值的30%。行车和驻车制动装置可以有共同的制动器,而驱动机构则各自独立。
3)在任何速度下制动时,汽车都不应丧失操纵性和方向稳定性。
4)防止水和泥进入制动器工作表面。
5)制动能力的热稳定性良好。
6)操作轻便,并具有良好的随动性。
7)制动时,制动系产生的噪声应尽可能小,同时力求减少散发出对人体有害的石棉纤维等物质,以减少公害。
8)作用滞后性应尽可能好。作用滞后性是指制动反应时间,以制动踏板开始动作至达到给定的制动效能所需的时间来评价。
9)摩擦片应有足够的使用寿命。
10)摩擦副磨损后,应有能消除因磨损而产生间隙的机构,且调整间隙工作容易,最好设置自动调整间隙机构。
11)当制动驱动装置的任何元件发生故障并使其基本供能遭到破坏时,汽车制动系应有音响或光信号等报警装置。
防止制动时车轮被抱死有利于提高汽车在制动过程中的转向操纵性和方向稳定性,缩短制动距离,所以近年来防抱死制动系统(ABS)在汽车上得到了很快的发展和应用。此外,由于含有石棉的摩擦材料在石棉有致癌公害问题已被淘汰,取而代之的各种无石棉型材料相继研制成功。
第二章汽车主要参数
主要尺寸:轴距:2920mm
质量:1540kg
质心高度(满载):850mm
质心到前轴距离:1790mm
质心到后轴距离:1130mm
轴荷分配:空载(前/后):739/801kg满载:960/1040kg
制动形式:浮钳盘式制动
车轮:前/后:225/60R17
第三章制动器形式的选择
制动器主要有摩擦式、液力式和电磁式等几种形式。电磁式制动器虽有作用滞后性好、易于连接而且接头可靠等优点,但因成本高,只在一部分总质量较大的商用车上用作车轮制动器或缓速器;液力式制动器一般只作缓速器。目前广泛使用的仍为摩擦式制动器。
摩擦式制动器按摩擦副结构形式不同,可分为鼓式,盘式和带式三种。带式制动器只用作中央制动器;鼓式和盘式制动器的结构形式有多种,如下所示:
图制动器分类表
盘式制动器的制动盘有两个主要部分:轮毂和制动表面。轮毂是安装车轮的部位,内装有轴承。制动表面是制动盘两侧的加工表面。它被加工得很仔细,为制动摩擦块提供摩擦接触面。整个制动盘一般由铸铁铸成。铸铁能提供优良的摩擦面。制动盘装车轮的一侧称为外侧,另一侧朝向车轮中心,称为内侧。
制动盘制动表面的大小由盘的直径决定。大型车需要较多制动功能,它的制动直径达12in或者更大些。较小较轻的车车用较小的制动盘。通常,制造商在保持有效的制动性能的情况下,尽可能将零件做的小些,轻些。
按轮毂结构分类,制动盘有两种常用型式。带毂的制动盘有个整体式毂。在这种结构中,轮毂与制动盘的其余部分铸成单体件。
另一种型式轮毂与盘侧制成两个独立件。轮毂用轴承装到车轴上。车论凸耳螺栓通过轮毂,再通过制动盘毂法兰配装。这种型式制动盘称为无毂制动盘。这种型式的优点是制动盘便宜些。制动面磨损超过加工极限时能很容易更换。
制动盘可能是整体式的或者通风的。通风的制动盘在两个制动表面之间铸有冷却叶片。这种结构使制动盘铸件显着的增加了冷却面积。车轮转动时,盘内扇形叶片的旋转增加了空气循环,有效的冷却制动。
盘式制动器具有散热快,重量轻,构造简单,调整方便等优点。特别是高负载时耐高温性能好,制动效果稳定,而且不怕泥水侵袭,在冬季和恶劣路况下行车,盘式制动比鼓式制动更容易在较短的时间内令车停下。虽然盘式制动器的制动盘与空气接触的面积很大,但很多时候其散热效果还是不能让人满意,于是有的制动盘上又被开了许多小孔,加速通风散热以提高制动效率,这就是通风盘式制动器。一般来说,尺寸大的制动盘要比尺寸小的制动盘散热效率高,而通风盘则要比实体盘的散热效率高。四轮轿车在制动过程中,一般前轮的制动力要比后轮大,后轮起辅助制动作用。因此,一般情况下,汽车前轮制动盘的尺寸要比后轮大,且前轮多采用通风盘,后轮多采用实体盘或通风盘。
根据制动盘固定元件的结构形式,盘式制动器可分为钳盘式制动器和全盘式制动器两类。
钳盘式制动器
钳盘式制动器的固定摩擦元件是制动块,装在与车轴连接且不能绕车轴线旋转的制动钳中。制动衬块与制动盘接触面积很小,在盘上所占的中心角一般仅30o~50o,故盘式制动器又被称为点盘式制动器。
全盘式制动器
全盘式制动器摩擦副的固定元件和旋转都是圆盘形的,分别称为固定盘和旋转盘。其结构原理和摩擦离合器相似。
多片全盘式制动器的各盘都封闭在壳体中,散热条件较差。因此,有些国家正在研制一种强制液冷多片全盘式制动器。这种制动器完全封闭,内腔充满冷却油液。冷却在制动器内受热升温后,被液压泵吸出,而后被压送入发动机水冷系中的热交换器,在此受发动机冷却水的冷却后再流回制动器。
钳盘式制动器按制动钳的结构不同,分为以下几种。
1.固定钳式
制动钳固定安装在车桥上,既不能旋转,也不能沿制动盘轴线方向移动,因而其中必须在制动盘两侧装设制动块促动装置,以便分别将两侧的制动块压向制动盘。这种形式也成为对置活塞式或浮动活塞式。
固定钳式制动器存在着以下缺点:
1)液压缸较多,使制动钳结构复杂。
2)液压缸分置于制动盘两侧,必须用跨越制动的钳内油道或外部油管来连通。这必然使得制动钳的尺寸过大,难以安装现代化轿车的轮毂内。
3)热负荷大时,液压缸和跨越制动盘的油管或油道中的制动液容易受热汽化。4)若要兼用于驻车制动,则必须加装一个机械促动的驻车制动钳。
这些缺点使得固定钳式制动器难以适应现代汽车的使用要求,故70年代以来,逐渐让位于浮钳盘式制动器。
图钳盘式制动器结构分类
a)固定钳式 b)滑动钳式c)摆动钳式
2.浮动钳式
(1)滑动钳式制动钳可以相对于制动盘作轴向滑动,其中只有在制动盘的内侧置有液压缸,外侧的制动块固定安装在钳体上。制动时活塞在液压作用下使活动制动
压靠到制动盘上,而反作用力则推动制动钳体连同固定制动块压向制动盘的另一侧,直到两制动块受力均等为止。
(2)摆动钳式它也是单侧液压缸结构,制动钳体与固定在车轴上的支座铰接。为实现制动,钳体不是滑动而是在与制动盘垂直的平面内摆动。显然,制动块不可能全面而均匀的磨损。为此,有必要经衬块预先作成楔形。在使用过程中,衬块逐渐磨损到各处残存厚度均匀后即应更换。
2.浮钳盘式制动器的制动钳一般设计得可以相对制动盘转向滑动。其中,只在组、制动盘的内侧设置液压缸,而外侧的制动块则附加装在钳体上。
浮动钳式制动器的优点有:
1)仅在盘的内侧有液压缸,故轴向尺寸小,制动器能进一步靠近轮毂;
2)没有跨越制动噢案的油道或油管,加之液压缸冷却条件好,所以制动液汽化的可能性小;
3)成本低
4)浮动钳的制动块可兼用于驻车制动。
与鼓式制动器相比,盘式制动器有如下优点:
1)热稳定性好。原因是一般无自行增力作用。衬块摩擦表面压力分布较鼓式中的衬片更为均匀。此外,制动鼓在受热膨胀后,工作半径增大,使其只能与
蹄中部接触,从而降低了制动效能,这称为机械衰退。制动盘的轴向膨胀极
小,径向膨胀根本与性能无关,故无机械衰退问题。因此,前轮采用盘式制
动器,汽车制动时不易跑偏。
2)水稳定性好。制动块对盘的单位压力高,易将水挤出,因而浸水后效能降低不多;又由于离心力作用及衬块对盘的擦拭作用,出水后只需经一,二次制
动即能恢复正常。鼓式制动器则需经十余次制动方能恢复。
3)制动力矩与汽车运动方向无关。
4)易于构成双回路制动系,使系统有较高的可靠性和安全性。
5)尺寸小,质量小,散热良好。
6)压力在制动衬块上分布比较均匀,故衬块上磨损也均匀。
7)更换制动块简单容易。
8)衬块与制动盘之间的间隙小(~),从而缩短了制动协调时间。
9)易实现间隙自动调整。
盘式制动器的主要缺点是:
1)难以实现完全防尘和锈蚀(封闭的多片式全盘式制动器除外)。
2)兼作驻车制动器时,所需附加的手驱动机构比较复杂。
3)在制动驱动机构中必须装用助力器。
4)因为衬块工作面积小,所以磨损快,寿命低,需用高材质的衬块。
因此,从结构,散热,技术,成本等多方面考虑,决定采用浮钳盘式制动器(前轮)。
第四章盘式制动器主要参数的确定
1.制动盘直径D
制动盘直径D应尽可能取大些。这时制动盘的有效半径得到增加,可以见效制动钳的加紧力,降低衬块单位压力和工作温度。受轮辋直径的限制,制动盘的直径通常选择为轮辋直径的70%-79%。总质量大于2t的汽车取上限。
轮辋直径为17英寸,又因为M =1540kg ,所以D 取340mm.
2 制动盘的厚度h
制动盘厚度h 对制动盘质量和工作时的温升有影响。为使质量小些,制动盘厚度不宜取的很大;为减小温升,制动盘厚度又不宜取的过小。制动盘可以做成实心的,或者为了散热通风需要在制动盘中间铸出通风孔道。在本设计中:前制动器采用通风盘,取厚度h =25mm ;后制动盘采用实心盘,取厚度h =12mm
3 摩擦衬块外半径R2与内半径R1
推荐摩擦衬块外半径R2与内半径R1的比值不大于。若比值偏大,工作时衬块的外缘与内侧圆周速度相差较多,磨损不均匀,接触面积减少,最终将导致制动力矩变化大。
取外半径R2=140mm ,内半径R1=100mm
4 制动衬块工作面积A
在确定盘式制动器衬块工作面积A 时,根据制动衬块单位面积占有的汽车质量,推荐在范围内选用。
汽车满载质量为1540kg ,前轮满载时地载荷为960kg ,
45.3960
? c ㎡
? c ㎡
所以A 取90c ㎡
五 盘式制动器的设计计算
质心高度 hg =850mm 轴距L =2920mm
质心到前轴距离a =L 1=1790mm 质心到后轴距离b =L 2=1130mm
汽车总质量M =1540kg
轮胎有效半径R =328mm
1. 同步附着系数的确定
对于前、后制动器制动力为固定比值的汽车,只有在附着系数?等于同步附着系数0?的路面上,前、后车轮制动器才会同时抱死。当汽车在不同?值的路面上制动时,可能有以下情况:
(1)当?<0?,β线位于I 曲线下方,制动时总是前轮先抱死。它虽是一种稳定工况,但丧失转向能力。
(2)当?>0?,β线位于I 曲线上方,制动时总是后轮先抱死,这时容易发生后轴侧滑使汽车失去方向稳定性。
(3)当0??=,制动时汽车前、后轮同时抱死,是一种稳定工况,但也失去转向能
力。
如何选择同步附着系数 0?,是采用恒定前后制动力分配比的汽车制动系设计中的一个较重要的问题。在汽车总重和质心位置已定的条件下,的数值就决定了前后制动力的分配比。
0?的选择与很多因数有关。首先,所选的0?应使得在常用路面上,附着系数利用率较高。具体而言,若主要是在较好的路面上行驶,则选的0?值可偏高些,反之可偏低些。从紧急制动的观点出发,0?值宜取高些。汽车若常带挂车行驶或常在山区行驶,0?值宜取低些。此外,0?的选择还与汽车的操纵性、稳定性的具体要求有关,与汽车的载荷情况也有关。总之,0?的选择是一个综合性的问题,上述各因数对0?的要求往往是相互矛盾的。因此,不可能选一尽善尽美的0?值,只有根据具体条件的不同,而有不同的侧重点。
随着道路条件的改善和汽车速度的提高,由于制动时后轮先抱死引起的汽车甩尾甚至掉头所造成的车祸日益增多。值宜取大些。根据设计经验,取= 2. 制动力分配系数的确定
上式表明:汽车在附着系数?为任意确定值的路面上制动时,各轴附着力即极限制动力并非为常数,而是制动强度q 或总制动力B F 的函数。当汽车各车轮制动器的制动力足够时,根据汽车前、后轴的轴荷分配,前、后车轮制动器制动力的分配、道路附着系数和坡度情况等,制动过程可能出现的情况有三种,即
(1)前轮先抱死拖滑,然后后轮再抱死拖滑;
(2)后轮先抱死拖滑,然后前轮再抱死拖滑;
(3)前、后轮同时抱死拖滑。
以1f F ,2f F 为坐标的曲线,即为理想的前、后轮制动器制动力分配曲线,简称I
曲线,如图 3. 3所示。如果汽车前、后制动器的制动力1f F ,2f F 能按I 曲线的规律分
配,则能保证汽车在任何附着系数?的路面上制动时,都能使前、后车轮同时抱死。
此客车前后制动器制动力为定比值。常用前制动器制动力与汽车总制动力之比来表明分配的比例,称为制动器制动力分配系数,用β表示,即:
μμβF F 1
= ()
21μμμF F F += ()
式中,为前制动器制动力;为后制动器制动力,为后制动器总制动力。 由于已经确定同步附着系数,则分配系数可由下式得到:
3. 前,后轮制动器制动力矩的确定
为了保证汽车有良好的制动效能,要求合理地确定前,后轮制动器的制动力矩。
先计算出前,后制动力矩的比值:
根据汽车满载在沥青,混凝土路面上紧急制动到前轮抱死拖滑,计算出后轮制动器的最大制动力矩2M μ:
e g r qh L L
G M ?μ)(12-=其中q 为制动强度,r e 为车轮有效半径。 在这里,67.0850)6.07.0(17909.01790)(011=?-+?=-+=
g h L L q ???,r e =328mm 所以952.6659243287.0)85067.01130(2920
8.915402=???-?=μM 848.847540952.66592456
.0156.0121=?-=-=μμββM M 4.制动强度和附着系数利用率4.制动强度和附着系数利用率
上面已给出了制动强度q 和附着系数利用率ε的定义式。下面再讨论一下当
?=0?、?<0?和?>0?时的q 和ε。根据所定的同步附着系数0?,由式()及式()得 L h L g
02?β+= ()
L h L g
011?β-=- () 进
而求得 q h L L
G Gq F F g B B )(021?ββ+=
== () q h L L G Gq F F g B B )()1()1(012?ββ-=-=-= () 当?=0?时:11?F F B =,22?F F B =,故?G F B ==14715,q=?;ε=1。
当?<0?时:可能得到的最大总制动力取决于前轮刚刚首先抱死的条件,即
11?F F B =。则总制动力F B 、制动强度q 和附着系数利用率ε分别为
g
B h L GL F )(022???-+= () g
h L L q )(022???-+= () g
h L L o )(22??ε-+= () 当?>0?时:可能得到的最大总制动力取决于后轮刚刚首先抱死的条件,即22?F F B =。则总制动力F B 、制动强度q 和附着系数利用率ε分别为
g
B h L GL F )(011???-+= () g
h L L q )(011???-+= () g
h L L )(011??ε-+= () 本设计中汽车的β值恒定,其0?值小于可能遇到的最大附着系数,使其在常遇附着系数范围内ε不致过低。在?>0?的良好路面上紧急制动时,总是后轮先抱死。
5.制动器最大制动力矩
对于选取较大的同步附着系数0?值的汽车,从保证汽车制动时的稳定性出发,来确定各轴的最大制动力矩。当0??>时,相应的极限制动强度?
e g
f r qh L L
G T ?)(1max 2-= () max max 211f f T T ββ
-= ()
对于本车即对于常遇到的道路条件较差、车速较低因而选取了较小的同步附着系数0?值的汽车,为了保证在0??>的良好的路面上(例如?=)能够制动到后轴和前
轴先后抱死滑移(此时制动强度q ?=),前、后轴的车轮制动器所能产生的最大制动力力矩为:
1max 12()f e g e G T Z r L h r L ???==
+=3640N 2max 1max 1f f T T β
β-==1558N
6.制动器因数
式给出了制动器因数BF 的表达式,它表示制动器的效能,又称为制动器效能因数。其实质是制动器在单位输入压力或力的作用下所能输出的力或力矩,用于评价不同结构型式的制动器的效能。制动器因数可定义为在制动鼓或制动盘的作用半径上所产生的摩擦力与输入力之比,即
PR T BF f
=
式中:f T ——制动器的摩擦力矩;
R ——制动鼓或制动盘的作用半径;
P ——输入力,一般取加于两制动蹄的张开力(或加于两制动块的压紧力)的平
均值为输入力。对于钳盘式制动器,两侧制动块对制动盘的压紧力均为
P ,则制动盘在其两侧工作面的作用半径上所受的摩擦力为2f P (f 为
盘与制动衬块间的摩擦系数),于是钳盘式制动器的制动器因数为
f P
fP BF 22== 式中:f 为摩擦系数,本设计中取f =;则BF =
7.应急制动和驻车制动所需的制动力矩
1).应急制动
应急制动时,后轮一般将抱死滑移,故后桥制动力为:
???g
a B h L gL m F F +==122 () 此时所需的后桥制动力矩为:
434.176********.0850
7.029*******.9154012=???+??=+=e g a e B r h L gL m r F ?? 现用后轮制动器作为应急制动器,则单个后轮制动器的制动力矩为F B2r e
2).驻车制动
汽车上坡停驻时,后桥附着力为:
)sin cos (12αα??L
h L L g m F g a += () 汽车在下坡停驻时,后桥附着力为:
)sin cos (12αα??L h L L g m F g a -=' ()
汽车可能停驻的极限上坡路倾角α1,可根据后桥上的附着力与制动力矩相等的条件求得,由1111sin )sin cos (
ααα?g m L h L L g m a g a =+ () 得 31.28850
7.029*******.0arctan 11=?-?=-=g h L L ??α 1α是保证汽车上坡行驶的纵向稳定性的极限坡路倾角。同理可推出汽车可能停驻的极限下坡路倾角为 62.19arctan 11=+='g
h L L ??α 安装制动器的空间,制动驱动力源等条件允许的范围内,应力求后桥上上驻车制动力矩接近由1α所确定的极限值74.234758031.28sin 3288.91540sin 1=???= αe a gr m ,并
保证下坡路上停驻的坡度不小于法规的规定值。
8. 衬块磨损特性的计算
摩擦衬块的磨损受温度,摩擦力,滑磨速度,制动盘的材质及加工景况,以及衬块本身材质等许多因素的影响,因此在理论上计算磨损特性极为困难。但试验表明,影响磨损的最重要因素还是摩擦表面的温度和摩擦力。
从能量的观点来说,汽车制动过程即是将汽车的机械能的一部分转变为热量而耗散的过程。在制动强度很大的紧急制动过程中,制动器几乎承担了汽车全部动能耗散的任务。此时,由于制动时间很短,实际上热量还来不及逸散到大气中就被制动器所吸收,致使制动器温度升高。这就是所谓制动器的能量负荷。能量负荷越大,则衬片(衬块)的磨损越严重。对于盘式制动器的衬块,其单位面积上的能量负荷比鼓式制动器衬片大许多,所以制动盘表面温度比制动鼓的高。
各种汽车的总质量及其制动衬片(衬块)的摩擦面积各不相同,因而有必要用一种相对的量作为评价能量负荷的指标。目前,各国常用的指标是比能量耗散率,即单位时间内衬片(衬块)单位面积耗散的能量,通常所用的计算单位为W/mm 2。比能量耗散率有时也称为单位功负荷,或简称能量负荷。
双轴汽车的单个前轮及后轮制动器的比能量耗散率分别为
βδ1
222112)(21tA v v m e a -?= () )1(2)(212
22212βδ--?=tA v v m e a () j
v v t 21-= () 式中,a m 为汽车总质量;δ为汽车回转质量系数;12,v v 为制动初速度和终速度(m/s );j 为制动减速度(m/s 2);t 为制动时间(s );1,2A A 为前,后制动器衬片(衬块)的摩擦面积(mm 2);β为制动力分配系数。
在紧急制动到停车的情况下,v 2=0,并可认为δ=1,故
β1
211221tA v m e a ?= () )1(2212
212β-?=tA v m e a () 乘用车的盘式制动器在1100/(27.8/)v km h m s =和0.6j g =的条件下,比能量耗散率应不大于mm 2。
由于采用前盘后鼓,所以仅计算前轮衬块的摩擦特性。 t=6=(s)
)/(00.2100
18063.4256.08.2715402121mm W e =??????=
式中,M μ为单个制动器的制动力矩;R 为制动鼓半径(衬块平均半径m R 或有效半径e R );A 为单个制动器的衬片(衬块)摩擦面积。 所以196.0100
1801202848.8475400=??÷=f (N/mm 2) 9. 盘式制动器制动力矩的计算
图 盘式制动器的计算用图
盘式制动器的计算用简图如图 所示,假设衬块的摩擦表面与制动盘接触良好,且各处的单位压力分布均匀,则盘式制动器的制动力矩为
fNR T f 2= ()
式中:f ——摩擦系数,取值;
N ——单侧制动块对制动盘的压紧力
R ——作用半径
图 钳盘式制动器的作用半径计算用图
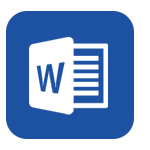





正在阅读:
盘式制动器设计说明书原版04-26
和路雪在中国市场竞争分析报告03-09
道路运输管理人员考试题库01-12
骄傲的我作文400字07-06
第十章 液压伺服系统05-15
试论如何做好工程监理工作04-27
砌体工程的质量通病与控制10-26
木业有限公司环保应急预案03-19
2022年重庆师范大学美术学院专业论文写作复试之外国美术简史复试04-10
ICAO英语考试总结12-06
- 教学能力大赛决赛获奖-教学实施报告-(完整图文版)
- 互联网+数据中心行业分析报告
- 2017上海杨浦区高三一模数学试题及答案
- 招商部差旅接待管理制度(4-25)
- 学生游玩安全注意事项
- 学生信息管理系统(文档模板供参考)
- 叉车门架有限元分析及系统设计
- 2014帮助残疾人志愿者服务情况记录
- 叶绿体中色素的提取和分离实验
- 中国食物成分表2020年最新权威完整改进版
- 推动国土资源领域生态文明建设
- 给水管道冲洗和消毒记录
- 计算机软件专业自我评价
- 高中数学必修1-5知识点归纳
- 2018-2022年中国第五代移动通信技术(5G)产业深度分析及发展前景研究报告发展趋势(目录)
- 生产车间巡查制度
- 2018版中国光热发电行业深度研究报告目录
- (通用)2019年中考数学总复习 第一章 第四节 数的开方与二次根式课件
- 2017_2018学年高中语文第二单元第4课说数课件粤教版
- 上市新药Lumateperone(卢美哌隆)合成检索总结报告
- 盘式
- 制动器
- 原版
- 说明书
- 设计
- 培训班元旦联欢会活动策划方案范文
- 2012年浙江省湖州市中考数学试题含答案.docx
- 冀人版科学三年级上册《观察土壤》教案附教学反思
- 【华中农业大学专业】华中农业大学招生网站-华中农业大学分数线
- 议论文论点论据大全
- 懒癌晚期作业LEGO乐高科技系列机械组Technic42009移动起重机
- 大尺寸4K 电视涌现市场
- 壁花少年中英文对照.word
- IELTS保7争8必背高频词汇
- 《专题4硫、氮和可持续发展》教材分析
- 华师在线作业(答案) Word的常见操作考题 2021年计算机基础统考
- 20KV及以下配电网工程预算定额使用指南
- 弹性力学基础(程尧舜 同济大学出版社)课后习题解答
- 操作系统期末总结复习学习资料.docx
- 管理信息系统题库(附答案)
- 东华客户关系管理复习题答案
- (完整版)2019年高考物理试题(全国1卷)lpf(可编辑修改word版)
- 泰安市世界环境保护日启动仪式新闻稿
- 10.Progress in probability density function methods for turb
- 重庆市人教版七年级上册数学 压轴题 期末复习综合测试题