丁辛醇概述
更新时间:2024-04-22 19:14:01 阅读量:1 综合文库 文档下载
丁辛醇
一、性质及用途
正丁醇为无色透明的易燃油状液体,有刺激性气味,可与水形成共沸物,沸点117.7℃,具有刺激和麻醉作用,手部可发生接触性皮炎;2-乙基己醇俗称辛醇,是无色透明的易燃油状液体,有刺激性气味,与水形成共沸物,低毒,沸点185℃。由于丁醇和辛醇可以在同一装置中用羰基合成法生产,故习惯称为丁辛醇。
丁醇主要作为树脂、油漆和粘接剂的溶剂和增塑剂的原料(如邻苯二甲酸二丁酯)此外还可用作选矿用的消泡剂、洗涤剂、脱水剂和合成香料的原料。
辛醇可直接作为有机溶剂用于油漆、涂料、照相、造纸和纺织、轻工等行业,但其最重要的用途是与邻苯二甲酸酐酯化反应得到邻苯二甲酸二辛酯(DOP),DOP是聚氯乙烯的重要增塑剂,用量相当大,其它酯类如脂肪族二元酸酯类及磷酸酯类等,这些酯均可作为塑料的主增塑剂和耐寒辅助增塑剂。
二、设计单位
1、华陆工程科技有限责任公司(化学工业部第六设计院)——西安市高新区唐延南路7号华陆大厦
装置能力(万序号 公司名称 山东华星石化集团有1 限公司 利华益集团股份有限2 公司 天津渤海化工有限责3 任公司天津碱厂 辛醇 异丁醛 16.45 2.85 英国DPT公司,低压羰基合成 丁辛醇 丁辛醇扩建 7 13.5 7 日本三菱,低压羰基合成 1988 1998 1994 2004 2004 投产时专利商/工艺技术 间 英国DPT公司,低压羰基合成 2009 产品名称 吨/年) 丁辛醇 24 丁辛醇 22.5 英国DPT公司,低压羰基合成 2010 丁辛醇 22.5 英国DPT公司,低压羰基合成 2010 4 中石化齐鲁石化公司 5
北京化工四厂 丁辛醇
合成气 丁辛醇扩建 7,300Nm3/h 8 7 9,000Nm3/h 美国德士古公司,重油气化 英国DPT公司,低压羰基合成 英国DPT公司,低压羰基合成 美国德士古公司,重油气化 1994 1993 1986 1986 6 中石油大庆石化总厂 丁辛醇 合成气
2、中国寰球工程公司华北规划设计院——河北省涿州市范阳西路122号
中石油吉林石化公司12万吨/年丁辛醇装置扩建改造项目 2000年 英国DPT公司低压羰基合成工艺
3、中石化集团上海工程有限公司——上海市浦东新区张杨路769号
(a) 中国石化股份有限公司齐鲁分公司丁辛醇装置技术改造项目 2.85万吨/年异丁醛及16.41万吨/年辛醇 2005年 EPC 英国DPT公司低压羰基合成工艺
(b) 扬子巴斯夫合资公司丁辛醇项目 12.5/11万吨/年 2005年EPC BASF公司低压羰基合成工艺
4、惠生工程(中国)有限公司——上海浦东张江高科技园区
惠生(南京)化工有限公司25万吨/年丁辛醇项目 10/2.43/12.5万吨/年 2011年 工艺未知
三、生产工艺简介
工业上正丁醇有5种生产工艺,分别为发酵法、乙醛缩合法(Aldol法)、齐格勒法、丙烯羰基合成法。辛醇生产工艺主要有羰基合成法、乙醛缩合法两种。目前,羰基合成法是丁辛醇主流生产工艺。 ① 发酵法
粮食或其他淀粉质农产品,经水解得到发酵液,在丙酮-丁醇菌的作用下发酵得到丙酮-丁醇和乙醇的混合物,然后经精馏分离即得到相应产品。该法设备简单、投资少,但消耗粮食多,生产能力小,因而限制了他的发展。
随着生物技术工程的发展,近年来采用固定化细胞生产丁醇、丙酮的生产能力已有很大的提高。预计未来,原料将会更加多样化,各种木质纤维素原料将在丙酮、丁醇生产中大量使用,丁醇的产量将会有更大的提高。
② 乙醛缩合法
乙醛在碱性条件下进行液相缩合制得2-羟基丁醛,然后经脱水成为丁烯醛(俗称巴豆醛),丁烯醛再经催化加氢制得正丁醇。此法操作压力低,无异构生产,但流程长、步骤多、设备腐蚀严重,生产成本较高,目前只有少数厂家采用此法生产。 ③ 齐格勒法
齐格勒丁辛醇生产方法是以乙烯为原料,采用齐格勒法生产高级脂肪醇,同时副产丁醇的方法。 ④ 丙烯羰基合成法
丙烯羰基合成法,又称氢甲酰化法,首套工业化装置于1944年建成投产。该工艺过程是丙烯与合成气进行氢甲酰化反应生成正丁醛和异丁醛,丁醛催化加氢得到正丁醇和异丁醇;丁醛经缩合脱水生成2-乙基己烯醛,然后催化加氢得到辛醇。丙烯羰基合成法又有高压钴法、中压法(改良钴法、改良铑法)、低压法(低压铑法)。低压法于1976年工业化,目前新建装置均采用低压羰基合成工艺,且已有多套高压钴法装置已改为低压铑法。羰基合成丁辛醇装置生产工艺主要工段为:气-液相羰基合成反应,羰基反应液的蒸馏分离,正丁醛缩合反应,正/异丁醛、辛醛加氢反应,辛醇蒸馏精制,正/异丁醇蒸馏精制。
丙烯羰基合成法的主流技术专利商如下:
高压法:鲁尔 (Ruhr)技术、巴斯夫(BASF)技术、三菱(MCC)技术、壳牌(Shell)技术。 中压法:壳牌(Shell)技术、鲁尔-化学(Ruhr-chemic)技术、三菱(MCC)铑法技术。 低压法 :巴斯夫(BASF)技术、 伊士曼(Eastman)技术、戴维(Davy UCC Johnson Matthey)技术、三菱化成(MCC)技术。 (一)高压羰基合成法
1944~1965年为高压羰基合成法发展阶段,首套工业化装置于1944年在德国鲁尔公司建成。主要包括鲁尔、巴斯夫、三菱化成和壳牌等几种技术,20世纪60年代采用高压法新建装置较多,成为当时生产丁辛醇的主要方法。羰基合成反应压力为19.6~29.4MPa。
尽管高压钴法技术比较成熟,但由于反应压力高、反应产物的正异构比低,鲁尔工艺装置维修工作量较大,而巴斯夫工艺设备腐蚀较严重,需采用含钼不锈钢和不锈钢材料,增加了建设费用等问题,因此自70年代中后期低压法工业化后,不再采用高压羰基合成技术新建丁辛醇装置。但目前高压法在羰基合成醇中仍占一定的位置,主要以生产高碳醇为主。
(二)中压法(改良钴法、改良铑法)
1965~1976年为羰基合成中压法阶段,这期间约有6~7套装置采用该技术建成投产。 1、壳牌公司改性钴催化剂中压羰基合成工艺
壳牌公司开发了以烷基膦改性的配位体改性钴催化剂,反应温度由传统高压法的 110~180℃提高到160~200℃,反应压力下降为7~10 MPa,由于采用复合催化剂,氢甲酰化反应、缩合和加氢反应在同一个反应器中进行,产品包括C4和C8醇。 该工艺的优点为:①反应压力大大降低,设备费用降低。②氢甲酰化反应和醛加氢反应在同一个反应器中进行,省去了传统工艺中的醛加氢和醛精制流程,流程较短。③省去了传统工艺中催化剂的脱钴、活化再生等部分。该工艺的缺点为:①催化剂活性低,物料停留时间长,因此反应器体积需增大5~6倍,一般是数个反应器串联操作。②在反应条件下催化剂的加氢活性大,大约10%~15%的丙烯加氢转化为丙烷(而传统钴法只有2%~3%的丙烯加氢为丙烷),原料消耗较大。③催化剂中使用过量的三正丁基膦,催化剂成本较高。④正丁醇与辛醇的比例难以调节。该工艺技术主要在壳牌公司内部采用,未见有大的发展。
2、鲁尔铑催化剂中压羰基合成方法
该工艺采用水溶性铑催化剂,羰基合成反应温度110~130℃,压力~7 MPa,反应选择性高,正、异构比较高。该工艺的优点是采用水溶性铑催化剂,催化剂与粗醛只需简单的相分离就可回收循环使用;铑在水相中损失量很小;反应产生的高沸物、副产物随醛带出,不存在于催化剂溶液中;催化反应选择性高,正异构比高;失活催化剂在装置区内回收,不需送外地回收金属铑;反应热低压蒸汽得以利用,动力消耗量低。不足之处在于其羰基合成反应压力比其他低压铑法羰基合成反应压力高。该工艺技术主要在赫斯特公司内部采用。 (三)低压羰基合成工艺
低压法主要有Davy-UCC技术、巴斯夫技术、三菱化成和伊士曼等几种技术,液相循环低压改性铑法是当今世界最先进、最广泛采用的技术。 1、UCC/Daw/Johnson Mattey低压羰基合成工艺
美国UCC和英国Davy及Johnson Mattey 3家公司共同开发的铑催化剂低压羰基合成技术,简称UCC/Davy法或U.D.J法,于1976年工业化装置投入生产,目前世界约60%左右的丁辛醇装置采用该技术。
该工艺依据羰基合成催化剂循环方式的不同又分为气相循环工艺和液相循环工艺。液相循环工艺于1984年投入工业化应用。与气相循环工艺相比,液相循环工艺将两台
并联反应器操作改为两台串联操作,不仅增大了反应器的容积利用率,而且加快了反应速率,可使同样大小反应器的能力提高50%~80%。采用液相循环工艺已在世界建成若干套生产装置。近年来,联碳与戴维公司又开发了新一代技术“UCC/DAVY MK-IV”,该工艺采用铑/异-44双亚磷酸盐催化体系,其活性高,铑浓度大幅降低,由于原料转化率高,可使烯烃氢甲酰化反应实现一次性转化,不需循环。但新催化剂的制备比较复杂,亚磷酸盐配体不稳定易堵塞管道和设备,因此,目前国外丙烯氢甲酰化反应仍广泛采用油溶铑膦工艺。
UCC/Davy低压羰基合成工艺原料消耗低、产物正异构比较高,反应压力低、操作容易,物料对设备腐蚀低,流程短,设备较少,投资低。液相循环工艺问世后,生产效率进一步提高。该工艺是羰基合成最先进的技术之一。该工艺的缺点是铑催化剂对毒物很敏感,对合成气和丙烯原料的净化要求较高。 2、三菱化成低压羰基合成工艺
该工艺采用铑络合物催化剂,反应压力和反应温度低,产物正异构比较高,物料对设备腐蚀低。该工艺虽然省去了闪蒸和蒸发过程,但设置了醛塔专门分离催化剂,且催化剂回收系统复杂,并需连续向反应器补加新鲜催化剂,流程长、设备多,总投资较大。 3、巴斯夫低压羰基合成工艺
该工艺于1982年实现工业化,羰基合成采用铑的络合物为催化剂,以三苯基膦为配位体,用丁醛和高沸物配制成催化剂溶液。催化剂采用液相循环工艺,每年抽出约10%~15%催化剂送工厂再生,同时补充新鲜催化剂。
巴斯夫低压羰基合成工艺的原料和公用工程消耗低,正异构比例较高且有变化弹性,反应压力低,采用一台鼓泡塔型反应器及液相加氢工艺,流程简单,操作方便,物料对设备腐蚀小,投资低,是羰基合成最先进的技术之一。 4、美国伊士曼公司羰基合成工艺
该技术过去未商业转让,目前仅在美国和新加坡各有1套装置运行。该技术的主要特点是产品方案灵活,其独有的乙烯-丙烯共进料工艺技术可同时生产丁醛和丙醛及相关的醇类产品,以适应市场需求。
四、DAVY液相循环低压铑法工艺
目前工业上普遍使用的DAVY 丙烯羰基合成法是由DAVY/DOW(原Kvaerner/UCC)联合开发的第二代低压铑法羰基合成工艺——液相循环工艺。采用的催化剂是配位体三苯基膦的铑膦络合物,由于其稳定性好,沸点也较高,催化剂与反应产物一起离开反应器,通过闪蒸及蒸发将催化剂溶液分离出来,再循环回反应器,使得生产能力大大提高。
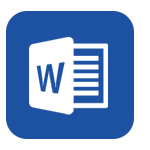





正在阅读:
丁辛醇概述04-22
2019年小学生寒假通知书参考12-02
新宁县中医医院医改情况汇报12-28
女性健康知识讲座主持词02-23
2012 工作总结08-22
一至十的十组成语接龙10-30
一基于共词分析的中国战略人力资源 管理研究的热点探析10-27
桥台路堤过渡段作业指导书10-27
中国社会思想史期中作业04-08
- 多层物业服务方案
- (审判实务)习惯法与少数民族地区民间纠纷解决问题(孙 潋)
- 人教版新课标六年级下册语文全册教案
- 词语打卡
- photoshop实习报告
- 钢结构设计原理综合测试2
- 2014年期末练习题
- 高中数学中的逆向思维解题方法探讨
- 名师原创 全国通用2014-2015学年高二寒假作业 政治(一)Word版
- 北航《建筑结构检测鉴定与加固》在线作业三
- XX县卫生监督所工程建设项目可行性研究报告
- 小学四年级观察作文经典评语
- 浅谈110KV变电站电气一次设计-程泉焱(1)
- 安全员考试题库
- 国家电网公司变电运维管理规定(试行)
- 义务教育课程标准稿征求意见提纲
- 教学秘书面试技巧
- 钢结构工程施工组织设计
- 水利工程概论论文
- 09届九年级数学第四次模拟试卷
- 丁辛醇
- 概述
- FGD电气
- 电商物流最后一公里问题研究
- 1-7章典型例题-v1
- 新人教版九年级物理全册习题答案
- 积分变换2009年A卷(含答案) - 图文
- 汇编语言实验报告
- Danaher-harvard business review 上(中文)
- 图形的平移、旋转与轴对称中考真题精选(部分难题有答案)
- 多部门联席会议制度
- shp文件格式说明
- 毕博马原第三单元题目
- 安龙职校绣娘培训结业晚会主持词
- 山东大学网络教育计算机网络基础期末考试复习
- 员工面谈记录表
- 同济大学考研 线性代数知识点(十)
- 2018-2019高考语文总复习 专题十五 文言断句与简答
- 抗菌药物持续改进PDCA
- 压力容器(乙炔)操作规程
- 2017年9月宁波十校联考化学
- 小学语文四年级期中试题