基于PLC的电力变压器冷却控制装置的研究
更新时间:2023-11-15 12:57:01 阅读量: 教育文库 文档下载
毕业设计说明书(论文)
基于PLC的电力变压器 冷却控制装置的研究
2011年06月 南 京
I
摘要
针对目前运行的大型电力变压器冷却控制装置存在的控制回路复杂、可靠性低、故障率高、控制误差大等问题,提出并研制了一种新型的变压器强迫油循环风冷控制装置。装置以西门子S7-200(CPU224)型PLC作为控制器构建了变压器冷却控制系统;系统以变压器顶层油温为被控量,提出了有差值裕度的投、切温度阀值的控制策略;提出了按冷却器的持续运行和累积运行时间自动均衡投切冷却器的控制方法;此外装置还具有通信及远方监视、故障定位、信息显示等功能。目前,装置已经在福建漳州莆美、角美220kV变电站投入使用。运行表明,该装置可靠性高、控制精确、并能延长冷却器组寿命,满足了大型变压器冷却控制装置智能化控制的要求。
关键字:变压器,冷却控制系统,可编程序控制器,负反馈控制
Abstract
To the problem exit in the cooling control device for large capacity transformer,such as the complicated control circuit,low reliability, high fault rate,large control error, the principle and implementation of a cooling control device for forced oil-circulated large capacity transformer based on PLC is presented in this paper.The device use siemens S7-200 PLC(CPU224)as controller, construct the cooling control system for
transformer;the transformer temperature as the control system‘s controlled variable,use control strategy of switch on and off value,which have margin in them,combine the accumulate operating time and continual operating time of cooling units,realize balanced,integrated auto control of cooling device.Beside this,the device has other functions such as,communication and remote surveillance,fault locating,information display.The devices have been used in Pumei and Jiaomei 220kV transformer substation.Zhangzhou.Fujian province.The results of operations show that the device is of high operation reliability, accurate control.Can prolong the service life of the cooling unit.The requirements of the intelligent control for large capacity transformer cooling device are satisfied.
KEY WORDS:transformer, cooling control system,PLC,negative feedback control
III
目录
摘要 .................................................................................................................................. II Abstract ........................................................................................................................... III 第一章 绪论 .................................................................................................................... 2
1.1课题来源及研究目的与意义 ................................................................................................. 2 1.2冷却控制装置研究现状 ......................................................................................................... 3 1.3本毕业设计的具体工作 ......................................................................................................... 4
第二章 强迫油循环冷却及控制系统运行分析 ............................................................ 5
2.1强油循环风冷却器及控制器的结构和工作原理 ................................................................. 5 2.2大型油冷变压器发热和散热计算 ......................................................................................... 8
第三章 冷却控制装置的功能和控制方法 ................................................................ 12
3.1电力变压器运行规程中关于冷却控制的规定 ................................................................... 12 3.2变压器冷却控制装置的功能设计 ....................................................................................... 13 3.3冷却控制装置功能模块设计 ............................................................................................... 14 3.4 控制方法和策略研究 .......................................................................................................... 16
第四章 冷却控制装置的硬件设计 .............................................................................. 21
4.1电气元件及在装置中的应用 ............................................................................................... 21 4.2可编程序控制器................................................................................................................... 23 4.3装置电气连接....................................................................................................................... 26 4.4通讯连接 .............................................................................................................................. 33
第五章 软件设计 .......................................................................................................... 35
5.1可编程序控制器编程 ........................................................................................................... 35 5.2上位机监视软件设计 ........................................................................................................... 40
第六章 结论和展望 ...................................................................................................... 45
6.1结论 ...................................................................................................................................... 45 6.2展望 ...................................................................................................................................... 46
参考文献 ........................................................................................................................ 47 附录1 英文文献翻译 ................................................................................................... 51 附录2 英文文献原文 ................................................................................................... 62
1
表示冷却器内部管路发生故障,同时控制电路启动备用冷却器;当潜油泵或风扇电动机发生故障时,热继电器动作,使主触点打开从而保护电动机,经过一定延时启动备用冷却器,并发出故障信号。备用冷却器在正常情况下是不投入运行的。辅助冷却器(在―辅助‖位置的冷却器)在负载较低时是不投入运行的,变压器绕组温度(如70℃)或顶层油温(如55℃)达到规定值时,温度控制器触点闭合,或负载电流达到额定值的70%时,使线圈励磁,从而使辅助冷却器投入运行。
C.故障回路
故障回路能在现场的总控制箱内观察到信号,它有如下4种:
(1)当两个电源都消失而使全部冷却器停止工作时,经适当延时,使断路器跳闸将变压器从网路上切除,发冷却器全停信号;
(2)当电源发生故障时发出故障信号;
(3)当工作、辅助冷却器发生故障,备用冷却器投入时,发出故障信号; (4)当备用冷却器投入运行后产生故障时发出故障信号。
2.1.3现行大型变压器冷却装置的配置和特点
目前我国大型电力变压器冷却装置的配置情况是:根据变压器容量的大小,配置数组强油风冷却器,每组风冷却器由l台油泵和3~4台风扇组成。运行中为满足变压器的各种运行工况,一般要求冷却器1台备用(运行冷却器故障时可自动投入运行)、1台辅助(变压器负荷电流大于70%额定电流或变压器顶层油温高于某一定值时自动投入运行)、其余所有冷却器全部投入运行。上述的冷却装置配置有其不尽人意的地方,如SFP7-240000/330型主变压器装设有6台冷却容量250KW的风冷却器,在夏季高温季节,变压器满负荷运行,变压器冷却装置全部投入,但其上层油温仍高达70℃左右。但在夜间尤其是在暴雨过后的夜间,因负荷和气温骤降,虽然已将变压器辅助冷却器停运,但变压器油温仍降至30℃以下,也就是油温的变化幅度超过了环境温度的变化。在冬季负荷较低或特别寒冷的季节,因油温过低,不得不对其进行加油,这对变压器的安全运行和寿命将十分不利。
以上情况都反映出现行配置的变压器冷却装置存在的设计和使用上的缺陷,这些都对变压器的运行和寿命产生不利影响。
2.1.4风冷却器控制线路存在的问题
现在运行的继电式控制系统由于受所采用器件的约束、在设计和控制策略方
7
面不够完善,因此主变压器经常因风冷控制系统故障而带病运行,严重地影响电网可靠运行。通过分析主要存在以下不足:
a.控制装置的控制功能通过接线连接各种继电器、接触器和其他器件实现,控制装置的线路复杂、接点接线较多,导致控制装置可靠性低、故障率高,维护工作量大。
b.控制装置的机电逻辑电路是由各种继电器来完成的,而继电器常会出现线圈烧毁或接点烧死等故障,可靠性差,造成控制系统的可靠性不高。
c.变压器负荷波动引起辅助冷却器频繁启动。当主变负荷在某一范围内波动时,测量主变负荷的电流继电器或测量变压器油温的温度继电器会频繁动作,将导致辅助冷却器频繁地启停。如果辅助冷却器的油泵、风扇电机启动过于频繁,还会进一步导致热继电器动作,从而使辅助冷却器退出运行,这样会缩短冷却器电气设备的使用寿命。同时,冷却器组的频繁启停还会加重变压器油流带电现象。
d.冷却器组设定的运行、辅助、备用和停止4种固定状态不能在线调整。不能在线调整冷却器组的状态,将导致某些冷却器组长期处于工作状态,使冷却器组尤其是油泵和风扇电机过疲劳运行,这对于冷却器组的使用寿命和安全运行十分不利。
e.冷却器在投入时不能分时分批投入,一方面造成启动电流过大,另一方面多个潜油泵突然启动会加重变压器油流带电现象。
f.装置的电动机缺相和过载保护由热继电器完成,保护功能不可靠,运行中因电动机过载和缺相而使电动机烧毁的情况经常发生。
g.冷却器控制回路存在设计缺陷。有些文献提到的冷却控制装置运行中存在的设计缺陷:工作冷却器的空气开关跳开后不能启动备用冷却器;工作电源交流接触器失磁造成主变开关跳闸;更换接触器和空气开关时易造成短路等。
2.2大型油冷变压器发热和散热计算
引起变压器运行中整体温度变化的原因主要有变压器的损耗和环境气温的影响。变压器投入运行后会产生损耗:一种是空载损耗、另一种是负载损耗,变压器的损耗转换为热量以对流、辐射的形式散发出来。本节对变压器损耗、散热进行计算、分析。
2.2.1变压器损耗计算
变压器损耗包括变压器的空载损耗和负载损耗。变压器空载损耗在变压器投运后就一直存在,不随变压器所带负载的大小变化;负载损耗则随变压器所带负荷的大小而改变,与负荷电流的平方成正比,变压器总损耗在不同负载时的计算公式为:
?P=P0+Pl=P0+I2R (2.1)
?P——变压器的总损耗
P0——变压器的空载损耗
Pl——变压器在一定负载电流下的负载损耗
I——变压器的负载电流 R——变压器绕组的等值电阻
设变压器的额定负载电流为Ie,则在额定负载电流下的变压器额定负载损耗
Pk的计算公式为:
Pk=Ie2R (2.2)
空载损耗P0和额定负载损耗Pk变压器铭牌中给出。
由公式(2.1)、(2.2)可得负载电流为,时变压器损耗的计算公式为:
?P=P0+Pk?IIe?2
(2.3)
变压器损耗将转变为热量向外发散,从而引起变压器发热和变压器油温升高。随着变压器温度的升高,它们对周围介质就有一定的温度差,从而将一部分热量传结局围介质。
2.2.2变压器散热方式
变压器散热过程中常遇到的不是单一的传热方式,而是变压器油流过铁芯表面、变压器油流过冷却器箱体内表面、空气流过冷却器箱体外表面时发生的对流、热传导和热辐射联合作用的传热过程。
热传导是物体不发生相对移动,从高温物体到低温物体之间的热量传递,单纯的热传导现象只有在密实的固体中才能观察到。热对流是指流体各部分之间发生相对位移、冷热流体质点相互掺混所引起的热量传递。只要绝对温度不为零度(0 K),物体都会不停地以电磁波的形式向外界辐射能量,同时又不断地吸收来自外
9
界物体的辐射能,当物体向外界辐射的能量与从外界吸收的辐射能不相等时,该物体就与外界产生热量的传递。这种传热方式称为热辐射。
变压器运行中绕组和铁芯产生的损耗转变为热量通过热对流、热传导和热辐射使变压器油温升高,变压器油上升进入散热器,形成变压器油的自然对流;强迫油循环冷却器中潜油泵的作用就是加速变压器油的流动,强制变压器油对流,加速热对流,在变压器油对流给热过程中同时发生着热传导和热辐射。变压器箱壁内侧热量从变压器油中以热对流、热传导和热辐射的形式传给冷却器。变压器箱壁外测热量从箱壁以热对流、热传导和热辐射的形式传给空气,同时风扇吹风强迫空气流动,加速热对流。变压器散热如图2.3所示:
变压器油空气变压器壁箱
图2.3 变压器散热图
2.2.3变压器散热计算
冷却控制系统中控制量为变压器顶层油温,所以只给出变压器油对空气的平均温升计算公式。油对空气的平均温升由油和箱壁间、箱壁内及箱壁对周围介质之间的温差组成。油与箱壁的温差较小,一般为3-6℃,箱壁内的温差小于1℃,可忽略不计。箱壁和周围介质(空气)之间的温差一般要占(油-空气)总温差的90%左右。热量从油箱向周围介质中的散发主要是通过对流和辐射散热的方式进行。
2.2.3.1对流散热计算
根据实验,单位对流散热系数可用下式表示:
qR=KK?4Q1 瓦/米2℃ (2.4)
单位面积上因对流散入空气中的热量(与温差qR——箱壁与空气温差为l℃时,有关,温差大,散入空气中的热量就大)
Q1——箱壁表面温度与空气温度之差
K——散热系数(经验系数)
K?——形状系数,与油箱外形有关
油箱表面因对流作用的散热量计算公式为:
1.25QR1=qRQ1FR=KK?FRQ1 瓦 (2.5)
FR——对流表面积,即油箱平滑部分和油管等的展开表面积之和(米2)
qRQ1——单位面积上由于对流散入空气中的总热量(瓦米2)
2.2.3.2辐射散热计算
根据试验和辐射定律,借辐射散入空气中的热量和辐射体温度及周围物体(或空气)温度间的关系为:
(T1100)?(T2 q??CT1?T2q?4100)4 瓦米2℃ (2.6)
——为温度为l℃时,辐射体单位表面积上辐射出的热量
T1、T2——辐射体及空气(周围物体)的绝对温度(K)T1=273+t1,T2=273+t2
C——常数,与辐射物体的表面情况有关
式(2.6)在很大范围内都是适用的。为了计算方便,根据试验可将(2.6)式简化为
q??K?4Q1 瓦米2℃ (2.7)
Q1——箱壁表面温度与空气温度之差 K?——经验常数
从油箱全部表面辐射出的热量为:
1.25Q??q?Q1F??K?F?Q1 瓦 (2.8)
F?——箱辐射表面积,当油箱是平滑油箱时为全部表面面积;当油箱是管式
油箱时为外周界。
变压器的总散热量为:
1.25Q?QR?Q?=K?F?Q1+KK?FRQ11.25 瓦 (2.9)
11
第三章 冷却控制装置的功能和控制方法
3.1电力变压器运行规程中关于冷却控制的规定
在变压器冷却控制装置的设计中参考了电力变压器运行规程(DL/T 572-95)中关于强迫油循环电力变压器冷却装置及运行条件的规定,规定如下:
3.1.1对变压器的冷却装置的要求
a.要求油浸式变压器本体的冷却装置、温度测量装置等应符合GB6451的要求。 b.按制造厂的规定安装全部冷却装置。
c.强油循环的冷却系统必须有两个独立的工作电源并能自动切换。当工作电源发生故障时,应自动投入备用电源并发出音响或灯光信号。
d.强油循环变压器,当切除故障冷却器时应发出音响或灯光信号,并自动(水冷的可手动)投入备用冷却器。
e.风扇、水泵及油泵的附属电动机应有过负荷、短路及断相保护;应有监视油泵电机旋转方向的装置。
f.强油循环冷却的变压器,应按温度和(或)负载控制冷却器的投切。
3.1.2变压器温度限值
强迫油循环变压器顶层油温一般不应超过表3.1的规定(制造厂有规定的按制造厂规定)。当冷却介质温度较低时,顶层油温也相应降低。
表3.1 油浸式变压器顶层油温一般限值
冷却方式 冷却介质最高温度(℃) 最高顶层油温(℃) 强迫油循环风冷 40 85
3.1.3 强迫油循环冷却变压器的运行条件
a.强迫油循环冷却变压器运行时,必须投入冷却器。空载和轻载时不应投入过多的冷却器(空载状态下允许短时不投)。各种负载下投入冷却器的相应台数,应按制造厂的规定。按温度和(或)负载投切冷却器的自动装置应保持正常。
b.强迫油循环变压器投运时应逐台投入冷却器,并按负载情况控制投入冷却
器的台数。
c.强迫油循环风冷变压器,当冷却系统故障切除全部冷却器时,允许带额定负载运行20分钟。如20分钟后变压器顶层油温尚未达到75℃,则允许上升到75℃,但这种状态下运行的最长时间不得超过1小时。
3.2变压器冷却控制装置的功能设计
通过对大型变压器强迫油循环风冷却及控制系统的分析,结合电力变压器运行规程的要求和电力系统自动化设备的发展趋势,本论文设计完成的变压器冷却控制装置可完成的功能如下:
1.冷却控制装置能控制两路独立电源为冷却装置供电,可由开关选择一路电源为―主‖电源,一路为―辅‖电源。―主‖电源故障后冷却控制装置能发出―电源故障‖信号并投入―辅‖电源,保证了冷却装置供电的可靠性;两路电源都发生故障,能发出―装置失电‖信号,并能够将全部风冷却器切除。
2.变压器高、中、低三侧开关全部断开,经过一段时间的延时使变压器完全冷却后所有风冷却器自动停运;变压器三侧开关任一侧开关闭合时,冷却控制装置按需要自动投运风冷却器。
3.冷却控制装置能控制8组风冷却器,取消了固定运行方式的工作模式,装置能按变压器油温自动、依次投入相应台数的冷却器,变压器负荷和环境温度变化,油温能始终维持在一个稳定的温度范围内;冷却器按温度依次投入,防止了冲击电流的产生,同时可以预防或改善油流带电现象。
4.冷却控制装置在产生投、切决策时采用有差值裕度投、切阀值的控制策略,可以有效的避免冷却器组频繁投切的问题。
5.冷却控制装置投入后,计时冷却器投入工作后的持续运行时间并能自动累积冷却器的工作时间(持续工作时间的和)即累积运行时间,在需要投入时投入累积运行时间最短的冷却器,在需要切除时切除持续运行时间最长的冷却器,使冷却器组均衡工作,提高了冷却器组的工作可靠性和使用寿命。
6.湿热季节,由凝露温度监控器监视环境温度、湿度,并能根据湿度情况和湿度持续时间情况将全部风冷却器投入,避免冷却器机械部分受潮腐蚀,以保证需要时能正常投运。
7.冷却控制装置能检测冷却器的风扇和潜油泵电动机发生的缺相、堵转、短路、过载故障并提供保护。
8.冷却控制装置能检测每组冷却器的风扇和潜油泵电动机故障、油路故障及
13
控制冷却器投切的接触器故障,如有故障发生控制装置自动将该组冷却器切除,发出故障及报警信号;故障消除,可以手动复位故障信号。
9.风冷却器全停时,能发出报警信号,并允许带额定负载运行20分钟,如20分钟后顶层油温尚未达到75℃,则允许上升到75℃,但这种状态下运行时间超过1小时后,将变压器高、中、低三侧开关跳闸,变压器停运。
10.冷却控制装置可以通过串行口与上位计算机通信,将变压器的部分运行信息、冷却及控制装置的运行信息、故障信息传送到上位机,实现远方监视功能。
11.冷却控制装置能在显示控制面板显示冷却及控制装置运行中的各种信息,包括电源运行、故障,风冷却器运行、故障,接触器故障信号;同时可以选择手动操作,以手动方式投、切冷却器组。
12.当温度达到一定数值时,自动接通控制箱内的风扇散热装置,保证设备内部温度满足要求;湿度达到一定值时,启动控制箱内的加热装置,防止装置箱体内凝露的产生。
3.3冷却控制装置功能模块设计
本文设计的变压器冷却控制装置的核心是PLC,装置的大多数功能通过可编程序控制器来实现,根据冷却控制装置的功能设计,以PLC为核心,整个控制装置由6个功能模块组成,如下图所示。
变压器冷却控制装置的控制功能通过电源监视控制、冷却器投切保护、凝露温度监控、就地控制与显示、通讯、上位计算机监视六个功能模块实现,功能模块的实现方法和作用简要介绍如下:
1.电源监视控制模块。模块通过小型电压继电器监视两路独立电源的状态(两路独立电源为冷却装置供电),判断电源是否缺相,由两个断路器控制电源的投切;将两路电源的故障信号和断路器辅助节点所反映的电源工作状态信号送入可编程序控制器,经可编程序控制器综合判断产生控制电源投切的控制命令,由断路器执行电源投切动作。
凝露温度监控模块电源检测控制模块可编程序控制器冷却器投切保护模块通讯模块上位计算机监视模块就地控制与显示模块 图3.1 冷却控制装置功能模块框图
2.冷却器投切保护模块。模块采用交流接触器控制冷却器的投入和切除,自动空气开关和电动机保护器配合实现对风扇和潜油泵电动机的短路、过载、堵转和缺相保护。可编程序控制器采集变压器温度信号、运行状态信号、油流继电器反映的冷却器油流状态信号、反映电动机故障状态的空气开关状态信号和交流接触器状态信号,由可编程序控制器根据送入的这些信号进行电动机、油流和接触器故障的判断和定位并产生投切冷却器的控制命令,由交流接触器执行投切动作。
3.凝露温度监控模块。模块采用凝露温度监控器对环境的温度、湿度进行实时监控,当湿度达到设定值后其凝露负载输出接通,信号送到可编程序控制器,由控制器决策定时投运全部风冷却器:同时湿度达到设定值时控制装置能启动冷却控制装置箱体内的加热装置,为控制装置箱体除湿;温度达到设定值时启动装置箱体内风扇,给控制装置散热。
4.就地控制和显示模块。在控制面板可以选择―手动‖或―自动‖投切冷却器,在―手动‖模式下可以手动投切冷却器;可以选择哪一路电源为―主‖电源;也可以手动复位故障信号。同时显示电源和风冷却器组的各种故障、投入状态信息以及变压器过流、超温、风冷却器全停等信息。
15
5.通讯模块。通讯模块通过PLC上的RS485口经串口长线延长器与远方的上位计算机通信,定期的将变压器、冷却器和冷却控制装置的运行信息、故障信息通过串口传送到上位计算机。
6.上位计算机监视模块。该模块使用Visual c++对串口编程,从串口采集变压器、冷却器和冷却控制装置的运行信息、故障信息,实现信息在上位计算机的动态显示和故障报警功能。可编程序控制器是变压器冷却控制装置的核心,它采集电源的状态和控制电源用断路器的状态信号、变压三侧开关和温度信号、冷却器的油流和电动机状态信号、凝露温度信号及各种选择操作信号综合判断产生控制决策、故障报警信号,并处理通讯将各种运行信息和故障信息上传到上位监控机,实现上位计算机对变压器冷却系统的监视。
3.4 控制方法和策略研究
控制方法和控制策略的研究是变压器冷却控制装置设计开发中的重要部分,它是变压器冷却控制设计的前提,电气连接和程序设计都是依据控制控制方法和策略而展开。采用了合理的控制方法和控制策略才能完成控制装置的设计功能,同时控制方法和策略的优劣将直接影响控制装置的性能。
变压器冷却控制装置的核心功能就是根据变压器油温自动投、切冷却器使变压器油温维持在一个稳定的范围内,满足变压器运行对温度的要求。在冷却控制装置中结合变压器冷却装置的特点我们采用了断续负反馈控制的控制方法、有差值裕度的投、切温度阀值的控制策略和按运行时间投切冷却器的控制方法。这些控制方法和策略的运用解决了冷却器频繁投切和不均衡工作等问题。
3.4.1变压器油温自动控制的控制方法
通过对冷却装置的工作特性进行分析,在变压器冷却控制装置的设计中采用了断续负反馈控制模型搭建了变压器油温自动控制系统,实现对变压器油温的自动控制。油温自动控制系统框图如图3.2所示,控制系统以变压器顶层油温作为被控量;PLC作为控制器;交流接触器作为执行机构;冷却装置作为被控对象:温度继电器作为变送器;将引起变压器油温变化的变压器负荷和环境温度看作控制系统的外部扰动。
串口设置失败打开串口成功建立线程等待串口无数据读取数据解析数据刷新显示
图5.3 上位计算机监视软件流程图
图5.4 串口参数设置对话框
5.2.3线程的建立及串口数据的读取、解析和显示
监视软件创建一个新的事件线程,它负责监视串口的事件。当有事件发生时,它向监视软件的主线程发送一个Windows消息。监视软件的主线程在消息响应函数中处理发生的事件。
当可编程序控制器向串口发送数据后,事件线程监视到串口数据缓冲区中有数据,将发出一个消息,监视软件的主线程在消息响应函数中调用读串口函数将串口数据缓冲区中的数据读出,接着调用数据解析函数。
解析函数的编写要依据表5.1所示的通讯信息编码表,首先获得读取数据的每个字节的高4位,每个字节的高4位是信息标示位,通过高4位可以判断传送过来的每个字节所代表的内容,然后根据字节的后4位对程序中关于冷却器及控制装置状态的一些变量进行赋值。
将读取的数据解析并赋值给函数的变量后就调用显示函数,显示函数根据变量显示变压器冷却及控制装置的状态,如图5.5所示:
43
图5.5 冷却器监视界面
如果变压器状态、电源状态或冷却器状态发生变化,包括变压器油温变化、电源投切、冷却器投切、冷却器故障、冷却器故障恢复等等,可以在监视界面产生一个记录项,记录项包括事件的类型和发生的事件,如图5.5所示。另外这些记录项可以通过程序保存产生一个文本文件(*.txt格式),文本文件中记录了事件发生的类型和发生的时间,可以方便记录和查询。
第六章 结论和展望
6.1结论
针对目前大容量电力变压器冷却控制装置存在的问题及电网的发展要求,在对目前大型电力变压器冷却及控制装置深入调研的基础上,提出了基于可编程序控制器的变压器冷却控制装置,并设计开发了基于PLC的大型电力变压器冷却控制装置。
本课题完成的变压器冷却控制装置主要由电源监视控制、冷却器投切保护、凝露温度监控、就地控制与显示、通讯、上位计算机监视六个功能模块组成。采用PLC实现变压器冷却装置的控制,所有的控制功能通过编程实现,极大的简化了系统接线,加上PLC自身的高可靠性,大大提升了装置的可靠性和自动化程度。
在变压器冷却控制装置的设计开发中,针对传统继电式控制装置控制方法的不足,本文提出了一种有差值裕度的投、切温度阈值进行综合投切控制的控制策略,这种投切控制策略可以有效的避免冷却器组的频繁投切,对提高冷却器的使用寿命有很大帮助;本装置结合冷却器组的持续运行和累积运行时间,给出了冷却装置的自动均衡控制方法,这种控制方法避免了冷却器组的长时间停运或工作,使冷却器能够均衡工作,能解决冷却器不均衡工作所带来的问题;装置可以判断电源和电动机发生的故障并进行故障定位,同时将电源和冷却器的运行工况等信息通过PLC的串口将这些信息上传到上位计算机,上位计算机可以显示变压器冷却及控制装置的工况,实现远方的监视;在湿热季节湿度过高时,冷却控制装置可以将冷却器全部投入运行一段时间,避免了因湿度过大、电动机长时间停运造成的电动机抱轴现象;对冷却器电动机实现更加可靠的缺相、堵转、短路、过载保护;此外还可以实现冷却器全停与变压器保护相结合功能以及信息显示和就地控制等功能。
本文设计的变压器冷却控制装置已经在漳州电业局莆美220kV变电站和角美220kV变电站投入使用,运行表明,本课题完成的基于PLC的变压器冷却控制装置功能完善、运行可靠、控制准确、并能延长风冷却器组的寿命,满足现今了大型变压器冷却装置智能化控制的要求。对变压器安全、可靠运行有重要意义和实用价值。
45
6.2展望
本文设计的变压器冷却控制装置在功能和可靠性方面都满足了变压器的运行要求。但是随着电网对智能化和可靠性要求的不断提高,对于变压器冷却器控制装置来说,可在以下几个方面有进一步的完善和提高。
设计变压器冷却控制装置具有远方控制功能。可以通过串口或工业以太网络将可编程序控制器与变电站监控计算机连接,使可编程序控制器能接受上位监控计算机的控制命令,对电源和冷却装置、控制装置进行远方操作。
随着固态继电器SSR制造技术的不断成熟,装置可以采用固态接触器作为执行器件。固态继电器具有切换速度快、寿命长、抗干扰能力强等优点,可以提高变压器冷却控制装置的可靠性。
要求温度(参考输入)PLC(控制器)接触器(执行机构)外部扰动冷却装置(被控对象)温度继电器(变送器)
图3.2 变压器油温自动控制系统框图
本装置采用的断续反馈控制系统不同于一般的恒值负反馈控制系统或随动负反馈控制系统,断续负反馈控制系统的特点是系统对被控对象的控制作用不连续,与此对应,外部扰动导致被控量变化,经控制系统的控制作用,被控量最终不能稳定在某一定值而是一个值的范围,这是由被控对象的特性决定的。对变压器温度自动控制系统而言只能按组投切冷却器实现对温度的控制,所以难以实现对变压器油温的定值控制,只能使其维持在一个温度范围内。
变压器油温自动控制系统的工作过程是,变压器负荷或环境温度变化引起变压器油温的变化,变压器油温变化通过温度继电器采集送入到可编程序控制器,可编程序控制器根据一定的控制策略产生控制冷却器投切的控制决策输出,控制决策通过接触器实现对冷却器组的投切,通过冷却器组的投切控制变压器油温的变化。
3.4.2 综合投、切控制策略
继电式控制装置在控制冷却器自动投切上通常的做法是,设定固定的温度阀值,变压器油温超过阀值继电器动作,投入―辅助‖冷却器,顶层油温低于设定阀值将投入的―辅助‖冷却器切除。这种做法的缺点是,当变压器温度在设定的温度阀值附近波动时,将造成冷却器组的频繁投切。
3.4.2.1控制策略原理
针对冷却器频繁投切的问题,在变压器油温自动控制系统中提出了有差值裕度的投、切温度阀值进行综合投切控制的控制策略,经实践证明这种控制策略可
17
以有效的避免冷却器组的频繁投切的问题,投切过程如图3.3所示:
投冷却器切冷却器TTtT(变压器油温)
图3.3 按温度投切冷却器过程示意图
图中横坐标T表示变压器油温,纵坐标表示是否投切冷却器,Tq为切除冷却器温度阀值,Tt为投入冷却器温度阀值。Tt-Tq即为差值裕度Td。
Td?Tt?Tq (3.1)
式中:Td——差值裕度
Tt——投入冷却器温度阀值 Tq——切除冷却器温度阀值
冷却器组的投、切过程是:变压器油温上升,当油温超过Tt时,需要有冷却器投入工作;变压器顶层油温下降,当油温低于Tq时,需要切除部分冷却器;当变压器油温维持在Tq到Tt之间的温度值时,装置不做任何投、切动作;在需要投入或切除冷却器时需要与按累积运行时间和持续运行时间进行投切控制的控制方法配合,具体产生投切某组冷却器的控制决策。 3.4.2.2控制参数的整定
有差值裕度的投、切温度阀值的控制策略的关键在于控制参数的整定,投入温度阀值Tt可以根据变压器运行规程要求或变压器生产厂商规定确定。差值裕度
Td (或者是Tq,在Tt确定后两者可以互相确定)的选取非常关键,在一定程度上决
定了装置控制功能的优劣。
Td的选取必须恰当,变压器负荷平稳且变压器顶层油温在Tt右侧附近时,投
入一组风冷却器;由于冷却器的投入变压器油温下降,如果选取Td过小使油温降
至Tq以下,需要切除冷却器;在切除冷却器后,冷却器的退出工作变压器油温上升并超过Tt,需要再次投入冷却器;如此往复将造成冷却器的频繁投/切。如果Td过大,将导致变压器油温在一个大范围内变动。 差值裕度Td的选取应遵循如下算法:
Td?Tt?Tt'?Tm (3.2)
式中:Td——差值裕度
Tt——投入冷却器温度阀值
Tt'——油温为Tt时,投入一组冷却器且稳定后的变压器油温 Tm——为温度裕度
Td可以由变压器生产厂家通过试验获得,也可以由运行人员根据运行经验整
定。
3.4.3按运行时间投切的控制方法
不同于继电式控制方式,投切的只是处于―辅助‖运行方式冷却器,采用温度负反馈控制方法的变压器油温自动控制系统中取消了固定的―工作‖、―辅助‖、―备用‖运行方式,有差值裕度的投、切控制策略产生投切控制决策时,就需要采用本节介绍的按持续运行时间和累积运行时间进行投切控制的控制方法,做出具体投切某组冷却器的控制决策。
首先介绍一下冷却器的持续运行时间和累积运行时间的概念。持续运行时间表示冷却器每次投入运行的时间,从冷却器组投入运行开始计时,冷却器退出运行计时被清零,重新投入运行后重新开始计时。累积运行时间表示冷却器每次投入运行的持续运行计时的累积,同时在―手动‖操作模式下,有冷却器投入运行也需要计时运行时间并累加到累积运行时间中。
在变压器油温自动控制系统中,按有差值裕度的投、切温度阀值进行综合投切控制决策和按持续运行时间和累积运行时间投切控制配合做出具体投切某组冷却器的工作过程如图3.4所示的流程:
首先由有差值裕度投、切阀值的控制策略产生是否投切的控制输出;然后再判断是否允许投切,因为在刚做完投切冷却器动作后必须延时一段时间等待变压器油温稳定后再做投切动作,否则在短时间内会投入或切除过多的冷却器,可能造成冷却器组的频繁投切。如果允许投切,就进入投切处理;如果不允许投切,则直接进入是否有冷却器持续运行时间超时的判断;如果判断有冷却器持续运行
19
时间超时,执行切处理,切除持续运行时间超时的冷却器;没有冷却器持续运行时间超时,循环会有差值裕度投切阀值的投切控制决策。
有差值欲度投切阀值的投切控制是禁止投切否投投或切选取累积运行时间最短的未投入冷却器开始计时投入冷却器的持续运行时间。处理输出禁止投切5分钟是有冷却器持续运行时间超时否选取持续运行时间最长的投入冷却器累加切除冷却器时间到累积运行时间。处理输出切
图3.3 投切冷却器决策流程图
投运冷却器的过程是从未投入冷却器的队列中选出累积运行时间最短的冷却器,控制交流接触器投入冷却器,冷却器投入后开始计时持续运行时间;切除冷却器的过程是从投入冷却器队列中选出持续运行时间最长的冷却器,控制交流接触器切除冷却器,同时将本次投运的持续运行时间累加到该台冷却器的累积运行时间。选择最短累积运行时间和选择最长持续运行时间冷却器的方法将在PLC编程中具体介绍。
第四章 冷却控制装置的硬件设计
变压器冷却器控制装置要用到诸如可编程序控制器、凝露温度监控器、接触器等电气元件,本章我们介绍冷却控制装置设计中用到的主要电气元件及其在控制装置中的应用,装置的电气连接。
4.1电气元件及在装置中的应用 4.1.1凝露温度监控器
凝露温度监控器是监视工作环境湿度、温度,当湿度、温度达到设定值能启动用户连接的凝露负载和控温负载的一种自动化工业仪器。我们设计的冷却控制装置采用LWK-D2(TH)型凝露温度监控器,它具有两个相对独立的工作单元:一路凝露监控;一路温度监控,具有体积小、寿命长等特点。电气连接如图4.1所示:
温度传感器控温负载凝露传感器123456789101112凝露负载相线中线AC220V
图4.1 凝露温度监控器电气图
凝露温度监控器的端子1、2连接温度传感器,5、6连接凝露传感器,3、4连接控温负载,7、8连接凝露负载,11、12连接交流220V电源。LWK-D2(TH)型凝露温度监控器的工作原理是:监控器通过凝露传感器和温度传感器对工作环境的湿度、温度等指标长期自动检测、采样;当工作环境有凝露产生的可能时,能自动判断并瞬间启动凝露负载;工作环境温度高于设定温度值时,相应的控温负载
21
也将开启;环境温湿度低于设定要求时才停止工作,重新进入监控状态,如此自动循环。
在冷却控制装置中凝露温度监控器监视环境的温度、湿度,有凝露产生的可能时。启动装置箱体内的加热装置,同时将―凝露‖信号送到PLC用于判断启动冷却器;当温度超过设定值,将装置箱内风扇启动,为控制装置散热。具体接线,将在本章的―冷却控制装置电气接线‖一节中详细介绍。
4.1.2电动机保护器
变压器冷却控制装置采用GDH系列电动机保护器与自动空气开关组合实现对电动机的缺相、过负荷、堵转和短路保护。GDH系列电动机保护器集缺相、过流、堵转保护为一体,具有工作灵敏可靠、安装方便、故障率低等优点,是替代热继电器实现电动机保护的理想换代产品。电动机保护器具体接线方法将在本章―冷却控制装置电气接线‖一节中叙述。
4.1.3开关器件
变压器冷却控制装置中要用到断路器、接触器、空气开关、转换开关等。这些器件主要选用施奈德公司的产品,施奈德公司的产品功能卓越、具有较高的安全稳定性和电气统一性。
装置选用继电器和开关的名称和型号规格如下: 断路器,型号:NS-100,3P,AC380V 接触器,型号:CA2-DN2205C 接触器,型号:LC1,32A,AC220V 空气开关,型号:GV2-M20,13-18A,400V 空气开关分励线圈,型号:AS225,AC220V 空气开关辅助节点,型号:LA1-DN22 小型继电器,型号:MAX7A,AC250V 信号继电器,型号:DX-8,0.025A 中间继电器,型号:MAX DC220V 转换开关,型号:LW5-15D7612/9 熔断器,型号:RTl8-32,32A
由于所用继电器和开关器件种类和型号较多,在此不一一介绍。在本章―冷却
控制装置电气接线‖一节中,结合具体实现电路介绍其在变压器冷却控制装置中的使用和作用。
4.2可编程序控制器
在以可编程序控制器为核心的变压器冷却控制装置中,输入、输出通过可编程序控制器连接起来,构成完整的控制系统。输入为可编程序控制器提供完成控制功能所必须的数字量、模拟量;可编程序控制器采样输入,执行编制的程序,根据程序设计对所采集信息进行综合分析、判断并作出决策,产生数字量、模拟量输出,驱动执行器件,完成控制功能。
4.2.1可编程序控制器的输入输出
根据变压器冷却控制装置的功能设计和结构设计,同时结合冷却控制装置的设备选型,可以确定可编程序控制器输入/输出的来源或者去向及输入/输出的性质和数量,如表4.1所示。
表4.l中给出了可编程序控制器的输入/输出名称,输入来源和输出去向以及输入/输出的性质及数量,从表可知可编程序控制器共有36路数字量输入和23路数字量输出。输入,输出性质及点数的确定非常重要,成为可编程序控制器选型的一项重要指标,可编程序控制器连同其输入,输出模块必须满足输入,输出点数的要求。
23
表4.1可编程控制器的输入输出
输入/输出名称 ―自动‖工作状态 ―手动‖工作状态 ―主/辅电源选择‖ Ⅰ、Ⅱ电源正常 Ⅰ、Ⅱ路电源投入 三侧开关状态 切除冷却器温度 投入冷却器温度 报警温度 凝露状态 油流状态 电动机状态 风冷却器的投入状态
合计
冷却器的投入信号 冷却器故障信号 冷却器故障类型
控制风冷却器接触器
指示装置 指示装置 控制电源断路器
分输入 控制电源断路器
合输入 变压器控制屏
合计
来源/去向 转换开关 转换开关 拨码开关 电源检测继电器 断路器辅助触点 三侧开关辅助触点 温度继电器 温度继电器 温度继电器 凝露温度控制器 油流继电器 自动空气开关 控制冷却器接触器
性质及数量 1路数字输入 1路数字输入 1路数字输入 2路数字输入 2路数字输入 1路数字输入 1路数字输入 1路数字输入 1路数字输入 1路数字输入 8路数字输入 8路数字输入 8路数字输入 36路数字输入 8路数字输入 8路数字输入 3路数字输入 1路数字输入 2路数字输入 1路数字输入 23路数字输入
输入 输出电源分信号 电源合信号 掉三侧开关信号
4.2.2可编程序控制器的选择
根据变压器冷却控制装置对可编程序控制器控制功能、输入/输出性质及点数,存储容量的要求,综合考虑性能、可靠性、价格等方面的因素,我们选用西门子S7-200型PLC作为冷却控制装置的控制器。可编程序控制器的选型,主要从以下几个方面考虑:
(1)控制功能。所选择PLC能最大限度的满足控制系统的控制功能是选择PLC时首先考虑的问题。S7-200型PLC代替了很多定时器、计数器、继电器所实现的功能,该PLC具有位逻辑、计数、定时、移位循环、比较、数字运算等指令,同时支持子程序和中断,能通过串口完成通讯,在控制功能方面,S7-200型PLC能满足冷却控制装置的功能需求。
(2)输入/输出性质及点数要求。我们选用CPU224(14数字输入/10继电器输出),CPU有内部电源可以为CPU自身,扩展模块和其他用电设备提供5V和24V直流电源。同时采用如下扩展模块,EM221(16路数字输入),EM222(8继电器输出),EM223(8数字输入/8继电器输出),共38路数字量输入和26路输出。扩展模块通过与CPU连接的总线连接电缆取得5V直流电源。不同规格的CPU提供的电源容量不
同,需要根据实际应用就电源容量进行规划计算,如表4.2所示:
表4.2 PLC电源计算
CPU电源预算 CPU224AC/DC/继电器
系统要求 EM221,5V电源要求 EM222,5V电源要求 EM223,5V电源要求 CPU224,14输入 CPU224,10继电器线圈
EM221,16输入 EM222,8继电器线圈
EM223,8输入 EM223,8继电器线圈
总需求 总电流差额
5V直流 660MA 减去以下电源需求
5V直流 70MA 40MA 80MA 190MA 剩470MA
24V直流 280MA 减去以下电源需求
24V直流
14*4=56MA 10*9=90MA 16*4=64MA 8*9=72MA 8*4=32MA 8*9=72MA 386MA 剩106MA
从表中电源计算可以看出,装置需要额外提供24V直流电源,需加装直流电源
25
后系统才能正常工作。在输入/输出性质及点数要求方面,采用上面提到的CPU和扩展模块能满足装置的要求。
(3)存储容量。CPU224具有8192字节的程序存储器和5120字节的数据存储区,能满足程序编写对存储容量的要求。
(4)从电源和带负载能力方面考虑。S7-200型PLC适合运行于额定电压为120~220V交流电源的场合,在变电站能提供220V交流电源;输出为继电器输出,继电器触点的电位对电源和输入是隔离的,可以将各种不同的负载连接到继电器输出。S7—200型PLC满足了电源和带负载能力的要求。
(5)安全可靠性方面。变压器冷却控制装置安装地点电磁环境复杂,对设备的安全可靠性提出了更高的要求。所选择的PLC在满足前文所述指标的前提下,安全可靠性问题是我们最关注的,因为冷却控制装置能否可靠运行将直接影响变压器的可靠运行。西门子S7-200型PLC具有较强的抗振性,及很强的电磁兼容性(EPIC),并完全符合各项工业标准,能够应用于各种气候条件。使用简单方便,并且模块不需要太多的附件和放置空间,使得控制柜的体积变得更小;不易于磨损,节省维护费用;编程十分简单,此外S7-200型PLC价格相对较低,降低了控制装置的成本。
我们综合考虑控制功能、存储容量和输入/输出点数、电源和带负载能力、安全可靠性方面及安装使用等各个方面,选用S7-200型PLC作为控制装置的控制器,能从各个方面满足我们的控制要求。
4.3装置电气连接
4.3.1电源监控和凝露温度监控部分电气接线
冷却系统由两路电源供电,可以通过开关选择一路为―主‖电源,一路为―辅‖电源,电源监视控制部分的作用是,监视两路电源的状态,并将电源状态信号送入可编程序控制器;同时接受可编程序控制器的控制命令,通过断路器动作选择一路电源为装置供电。凝露温度监控器可以实时监视环境的温度、湿度,条件达到时可以启动凝露负载、温度负载,对可能产生的凝露、超温情况采取应对措施。
电源监控和凝露温度监控部分电气接线原理如图4.2所示:
在图4.2所示线路中,小型电压继电器1YJ、2YJ、3YJ的线圈分别连接电源l的三相X1、X2和X3负责监视电源l的状态,三个电压继电器的常开触点串联后连接中间继电器1ZJ的励磁线圈。电源各相均正常时小型继电器1YJ、2YJ和3YJ的常开
触点都闭合,中间继电器1ZJ的线圈励磁,1ZJ常开触点闭合;1ZJ的常开触点连接可编程序控制的输入端,送入电源状态信号。小型电压继电器4YJ、5YJ、6YJ和中间继电器2ZJ的配合实现对电源2的监视,接线和工作原理与电源1的监视电路类似。
中间继电器LZJ的触点负责为断路器和凝露温度监控器提供电源,当电源1正常时,LZJ的常开触点闭合,常闭触点打开,由电源1为断路器和凝露温度监控器的工作提供电源;当电源l非正常时,LZJ的常开触点打开,常闭触点闭合,由电源2为断路器和凝露温度监控器供电。
断路器可执行可编程序控制器输出的电源选择控制指令,为冷却器组及控制装置选择一路电源。接触器的A4为―分闸‖输入,A2为―合闸‖输入,―分闸‖输入具有更高的优先级,即两输入端都为有效状态时,断路器优先执行―分闸‖动作。接触器的主触头分别连接两电源和变压器冷却装置的电源进线,输入端连接可编程序控制器的输出和断路器常闭辅助触点的组合。图中Q3.4为控制1JC的―合闸‖信号,Q3.5为控制1JC的―合闸‖信号,Q3.6为控制1JC和2JC的―分闸‖信号。2JC的常闭辅助触点和Q3.4串联接入UC的―合‖输入端可以防止两电源同时投入,因为2JC处于―合闸‖状态时,电源2供电,其常闭辅助触点打开,1JC的。―合闸‖输入端处于无信号的状态,电源2不能投入。同理1JC的常闭辅助触点和Q3.5串联接入2JC的―合闸‖输入端可以防止电源同时投入的情况发生。
凝露温度监控器的工作原理已经介绍过。图中ch11为温度传感器,chl2为湿度传感器;WCG为冷却控制装置箱体内的如热装置,3ZJ为中闻继电器的励磁线圈,WCG和3ZJ连接到凝露温度监控器的―凝露负载‖输出;D为风冷控制装置箱体内的风扇电动机,连接到凝露温度监控器的―温度负载‖输出;id为冷却控制装置箱体的照明装置,一端连冷却控制装置的电源,N连接控制装置电源的中线。
27
X1X2X3N11YJX11X12X13N24YJ3RD118412635wcg3ZJKID1272YJ5YJch11ch123YJ6YJN1RD2RD2JCQ3.41ZJ2ZJ5YJ6YJ1JCQ3.5Q3.6B4A1A21JCA4B4A2A4A12JC4YJ1ZJ1YJ2YJ3YJ1JC2JCX11X12X13
图4.2 电源监视控制接线图
中间继电器3ZJ的励磁线圈连接到凝露监控器的―凝露负载‖输出,当环境湿度达到设定值时,―凝露负载‖输出接通,中间继电器3ZJ励磁,其常开触点连接到可编程序控制器的输入,为可编程序控制器提供凝露信号。冷却控制装置箱体内的加热装置WCG连接凝露监控器的―凝露负载‖输出,当环境湿度达到设定值时,凝露负载接通,加热装置启动为控制装置除湿,保证冷却控制装置的可靠工作。冷却控制装置箱体内的风扇连接到凝露控制器的―温度负载‖输出,为了保证冷却控制装置的可靠工作,当环境温度达到设定值时,温度负载将被接通,风扇投入运转为冷却控制装置散热。冷却控制箱体内的照明装置id通过开关K连接到电源,装置箱体开启开关K闭合,照明装置点亮;箱体关闭照明装置熄灭。
4.3.2冷却器电动机保护控制电气接线
本论文设计的冷却控制装置可以控制8组冷却器,每组冷却器由3个风扇和1个潜油泵组成。冷却器保护控制部分可以为冷却器风扇电动机和潜油泵电动机提供过载、堵转和缺相保护,并接受可编程序控制器的输出指令,投/切冷却器组.每组冷却器保护控制的接线是相同的,这里我们只绘出了一组冷却器保护控制的电气接线原理图,如图4.3所示:
图4.3所示线路中,IFS2、IFS4为一组冷却器中风扇电动机的电动机保护器(一个风扇IFS3未画出),IFS1为潜油泵电动机保护器,IFS1、IFS2、IFS3、IFS4分别串接在冷却装置电源和冷却器风扇电动机和潜油泵电动机之间。当电动机发生过载、短路和缺相故障时,与之连接的电机保护器的辅助触点闭合;1ZK为自动空气开关,风扇电动机保护器IFS1、IFS2、IFS3和潜油泵电动机保护器IFS4的辅助触点并联后连接到空气开关1ZK的励磁线圈,当任一电机出现故障时与之相连的电机保护器的输出触点闭合,将使空气开关1ZK的线圈励磁,使空气开关动作。1BC为控制风冷却器投/切的接触器,它的励磁线圈连接可编程序控制器的输出,可以接受可编程序控制器的控制指令,控制冷却器投切。
x13x11x121bcIFS11FS2x12145810x131FS3x111213x111617x122021x1324252829L+312367911141518192223262730311-x311-x412-x312-x413-x313-x414-x314-x415-x315-x416-x316-x417-x317-x418-x318-x411zk
图4.3 冷却器保护控制接线图
转换开关用于选择是―手动‖、―自动‖投入冷却器或处于―停止‖状态。端子连接以第一组端子为例,处于―自动‖状态端子l、2接通,处于―手动‖操作状态端子3、4接通。端子25、26、27、28连接在控制电源投切线路中。其余左侧端子分别连接
29
交流和直流电源如图所示;右侧端子2、6、10连接PLC控制接触器输出电源侧,端子3、7、11连接手动控制冷却器按钮;30连接PLC的―自动‖输入,31连接PLC的―手动‖输入;剩余的右侧端子连接PLC的故障输出电源侧。
4.3.3可编程序控制器的输入输出连接
变压器冷却控制装置的核心PLC由一个CPU模块CPU224(14数字输入/10继电器输出),三个输入输出扩展模块,EM221(16路数字输入),EM222(8继电器输出),EM223(8数字输入/8继电器输出)组成,PLC从输入端子采集信号,从输出端子输出控制信号,模块的输入输出连接如下。
4.3.3.1 CPU224的输入输出连接
可编程序控制器的CPU模块CPU224是整个装置的核心,所有的程序和数据都在CPU模块存储,控制功能和控制决策由CPU模块运行做出,CPU224有14个24V数字直流输入和10个继电器输出,CPU224输入输出连接如图4.4所示:
220V交流电源通过电源输入(L1,N)送入该模块,模块还可以向外提供24V直流电源,从电源输出(L+,M)引出。
输入I0.0和I0.1连接转换开关,分别表示―自动‖、―手动‖操作,转换开关在―手动‖位置时10.0将有效,转换开关在―手动‖位置时I0.1将有效。
输入I0.2~I0.6分别连接电源―主‖、―辅‖选择开关、中间继电器1JC和2ZJ的常开触点、断路器1JC和2JC的辅助触点。开关1KG闭合,表示选择I电源作为―主‖电源;中间继电器1ZJ、2ZJ闭合时,I0.3、I0.4将分别有效,表示1路、2路电源处于正常状态;1JC、2JC接通,其辅助触点闭合,分别表示1路、2路电源投入。
图4.4 CPU224输入输出连接
变压器三侧开关DL1、DL2、DL3的辅助触点串联作为I0.7输入。变压器三侧开关全部打开,辅助触点DL1、DL2、DL3全部闭合,该输入为有信号状态,表示三侧开关全部打开。
输入I1.0、I1.1、I1.2分别连接3个温度继电器1WJ、2WJ、3WJ的常开触点,指示变压器的顶层油温,其中温度继电器1WJ整定为切除冷却器温度阈值,温度继电器2WJ整定为投入冷却器温度阈值,温度继电器3WJ整定为―告警‖温度。
输入I1.3连接中间继电器3ZJ的一个触点,中间继电器3ZJ的励磁线圈连接凝露监控器的凝露负载,当凝露温度监控器判断发生凝露时,线圈励磁,将凝露信号通过该输入端送到PLC。
1L、2L、3L分别连接到转换开关的1X31、2X31和3X31,处于―自动‖操作模式时分别为输出Q0.0~Q0.3、Q0.4~Q0.6、Q0.7~Q1.1提供电源。Q0.0~Q0.7这8路输出分别连接控制8路控制冷却器投切接触器的励磁线圈的一端,励磁线圈的另一端连接到中线。接触器励磁线圈的电源端通过开关还连接转换开关的1X41、2X41和3X41,处于―手动‖操作模式下,为励磁线圈提供电源,可以通过按钮开关手动的投切冷却器。Q0.0~Q0.7还连接信号指示灯,当输出有信号时,将接触器线圈励磁,接触器动作其常开触点闭合,将一组风冷却器投入运行同时点亮风冷却器投入指示灯。
4.3.3.2 EM223的输入输出连接
扩展模块EM223的主要作用是扩展CPU模块的输入输出,它有8个24V直流数字输入,8个继电器输出,输入输出连接如图4.5所示:
31
图4.5 EM223输入输出连接
模块的1M和2M端接地,L+连接CPU224模块的24V直流电源输出,一方面为输入I2.O~I2.7提供电源,另一方面为继电器输出Q2.0~Q2.7的继电器线圈供电.1L和2L分别连接转换开关的4X31和5X31在―手动‖和―自动‖工作模式下分别为输出Q2.0~Q2.3和Q2.4~Q2.7的输出负载提供电源。
冷却控制装置能控制8组冷却器,8组冷却器的油流继电器1LJ~8LJ的常开触点连接24V直流电源和EM223的输入I2.0~I2.7。一组冷却器投入运行,这组冷却器中变压器油流速正常,油流继电器常开触点闭合,对应的输入变为有信号状态,变压器油流不正常,对应的输入变为无信号状态。
输出Q2.0~Q2.7连接冷却器故障信号指示灯,指示灯的另一端连接中线。变压器冷却控制装置具有故障定位功能,如果一组冷却器的电动机故障、油流或接触器出现故障,对应的信号灯被点亮。同时该组信号灯与EM222的输出配合可以确定是哪一组冷却器出现何种故障。
4.3.3.3 EM221和EM222的输入输出连接
扩展模块EM221和EM222的作用是扩展CPU模块的输入输出,EM221有16个24V直流数字输入,EM222有8个继电器输出,输入输出连接如图4.6所示:
图4.6 EM221和EM222输入输出连接
模块EM221的1M~4M端和EM222的M端接地,EM222的L+连接24V直流电源,为继电器输出的继电器线圈供电,由于受CPU24V直流电源供电容量的限制,需要额外提供24V直流电源,可以通过加装24V开关电源解决。EM222的1L端连接6X31,在―手动‖和―自动‖工作模式下分别为输出Q3.0~Q3.3的输出负载提供电源。2L连接7X31,7X31和输出Q3.4、Q3.5、Q3.6连入电源控制电路。
输入I3.0~I3.7分别连接8组自动空气开关1ZK~8ZK常开辅助触点的一端,空气开关辅助触点的另一端连接2.1V直流电源。自动空气开关与电动机保护器配合实现对风扇和潜油泵电动机的保护,正常情况下自动空气开关的辅助触点打开,当冷却器电动机出现故障时,辅助触点闭合,将各组冷却器的电动机故障信号送入可编程序控制器。
输入I4.0~I4.7分别连接控制冷却器投切的8个交流接触器1BC~8BC的常开辅助触点,交流接触器辅助触点的另一端连接24V直流电源。当一只交流接触器闭合,接触器控制的冷却器投入工作,辅助触点闭合,信号送入可编程序控制器,表示对应冷却器投入工作。
4.4通讯连接
冷却控制装置采用自由口通讯,自由口通讯是建立在可编程序控制器RS485
33
硬件基础上的一种通讯方式。自由口通讯方式通讯功能完全由用户程序控制,所有通讯任务由用户编程完成。
一般冷却控制设备到上位计算机距离较远,受到通讯距离的限制我们还采用了长线驱动器Model232D/3延长通讯距离,保证数据的可靠。驱动器无需外接电源供电,光电隔离3KV适合在恶劣环境下使用。采用4线通信,传输距离在9600bps时为1000米、性能稳定。
冷却器控制装置的通讯由PLC、PPI电缆(一端为PLC的RS485一端为RS232,可用于自由口通讯和对PLC进行编程)、长线驱动器、通讯线和上位计算是组成,如图4.7所示:
图4.7 冷却控制装置通讯组成
可编程序控制器CPU224模块的RS485口连接PPI电缆,PPI电缆的RS232口连接长线驱动器1的RS232侧,长线驱动器I的线路侧连接通信线路,通信线路的另一侧连接另一个长线驱动器2,长线驱动器2的RS232侧连接上位计算机。
第五章 软件设计
5.1可编程序控制器编程
本节首先分析介绍可编程序控制器程序流程,然后重点介绍可编程序控制器程序中几个关键点的程序编制。
5.1.1软件总体设计
可编程序控制器程序流程图如图5.1所示:
初始化无电源投入电源处理禁止投切三侧开关处理手动“自动”或“手动”停止停止处理自动首次投入否投入计时处理是初始化处理及时超时处理切切处理投切判断投投处理切除计时处理故障判断冷却器全停处理通讯处理
图5.1 可编程序控制器流程图
程序流程介绍如下,首先进行初始化,在PLC由停止到运行的第一个运行周期
35
进行初始化操作一次,初始化操作完成可编程序控制器通讯设置;清零程序中用到的计数器、定时器、故障标志位、持续运行时间和累积运行时间存储区,置位或复位程序中用到辅助标志位等。
电源处理,根据―主‖―辅‖电源选择标志输入,电源状态和电源投入状态输入进行综合判断,置位相应的输出位,为冷却装置选择一路电源为装置供电,如果没有电源投入。则跳转到停止处理。
有电源投入,接下来进行三侧开关处理。PLC判断三侧开关状态输入,三侧开关输入信号由无效变为有效,程序延时一段时间然后复位―允许投切‖标志位,延时的目的是让变压器停止工作后使冷却器继续工作一段时间,使变压器充分冷却;―允许投切‖标志位无效时跳转到停止处理;三侧开关输入信号无效,表示变压器工作,置位―允许投切‖标志位。
如果允许投切,接下来进行―手动‖、―自动‖或―停止‖操作判断,如果处于―停止‖状态,跳转到停止处理;如果处于―手动‖,跳转到计时超时处理:如果处于―自动‖状态,则进行―首次投入‖判断,这里的―首次投入‖是说冷却器由―手动‖或―停止‖转换到―自动‖;如果是首次投入则需要进行初始化投切处理,以一定的时间间隔,依次投入5组冷却器;否则直接进行投入计时处理。
投入计时处理,切除计时处理。PLC程序采用定时器结合计数器计时的方式,冷却器投入时就对投入冷却器开始计时;冷却器切除时,需要将此次运行的持续时间累加到累积运行时间存储区。
投切判断。PLC按有差值裕度的投、切温度阀值的控制策略进行投切判断:冷却器持续运行时闻计时到设定值,需要进行一次切操作,将计时时间达到的冷却器切除;凝露温度监控器凝露负载接通并且持续超过设定时间,此时将进行投操作,并且禁止切操作,将无故障冷却器全部投入运行。
投处理,切处理。投处理操作从停止运行的冷却器中选取累积运行时间最短的并置位投冷却器输出;切处理操作从运行的冷却器中选取持续运行时间最长的冷却器复位投冷却器输出;在进行投切处理后要延时投切一段时间使冷却器动作后变压器油温维持稳定,避免重复投切,延时投切同时还避免了大冲击电流的产生。
停止处理。将投冷却器输出位复位,同时复位允许投切标志位和计数器(辅助计时)。
手动时计时超时处理,在手动模式下不能自动投切冷却器,又由于受到计数器计数个数的限制,所以当持续运行时间计数器超设定值时将持续运行时间计数器计数值累加到累积运行时间存储区,持续运行时间计数器清零重新开始计时。
故障判断。PLC可根据输入的油流继电器、空气开关和接触器状态,结合投切决策进行故障定位和判断,并将判断的结果分别置位可编程序控制器发送缓冲区相应的存储位。
冷却器全停处理。冷却器全停时允许带额定负载运行20分钟,如20分钟后顶
00层油温尚未达到75C,则允许上升到75C,但这种状态下运行时间超过1小时后,置位变压器三侧开关跳闸输出,使变压器停运。
通讯处理,PLC定期的将与冷却器有关的变压器运行信息、电源状态信息、冷却器工作状态信息、故障信息通过串口发送到上位计算机,上位计算机取得这些信息,监视冷却器运行。
5.1.2电源和三侧开关处理
PLC控制电源投切用断路器的分闸输出Q3.6、断路器I合闸输出Q3.4和断路器2合闸输出Q3.5的逻辑表达式如下:
Q3.6=[I0.0?I0.1?(I0.5?I0.6)]
?[(I0.0?I0.1)?I0.2?I0.3?I0.5]?[(I0.0?I0.1)?I0.2?I0.3?I0.6] ?[(I0.0?I0.1)?I0.2?I0.4?I0.6]?[(I0.0?I0.1)?I0.2?I0.4?I0.5]?[(I0.0?I0.1)?I0.3?I0.4?I0.5?I0.6] (5.1)
Q3.4?[(I0.0?I0.1)?I0.5?I0.6?I0.2?I0.3]?[(I0.0?I0.1)?I0.5?I0.6?I0.2?I0.3?I0.4Q3.5?[(I0.0?I0.1)?I0.5?I0.6?I0.2?I0.4] (5.2)
?[(I0.0?I0.1)?I0.5?I0.6?I0.2?I0.3?I0.4] (5.3)
PLC的输入输出定义在前边已经介绍,与公式5.1对应在下列6种情况下断路器的分闸信号Q3.6有效;―停止‖状态时:断路器1或断路器2还处于合闸状态;工作状态(手动或自动)时:电源1为主电源,电源故障1但断路器1在合闸;电源1为主电源,电源1正常但断路器2在合闸;电源2为主电源,电源2故障但断路器2在合闸;电源2为主电源,电源2正常但断路器1在合闸;电源1和2都故障,但断路器1或2在合闸。
断路器1和断路器2的合闸信号都是在工作状态,并且断路器1和2全部处于分
37
闸状态下进行,与公式5.2对应断路器1的合闸信号在电源1为主电源且电源1正常和电源2为主电源,电源2故障但电源1正常这两种情况下有效。电源2的合闸信号和电源1类似。
变压器的三侧开关连接断开延时功能块,三侧开关不全部打开,功能块输出有效,三侧开关全部打开,功能块输出延时,保持有效一段时间。该功能块的作用是在三侧开关全部断开时,可以延时切除冷却器保证变压器可靠冷却。如果断路器1或断路器2处于合闸状态,并且连接变压器三侧开关的断开延时功能块的输出有效则置位允许投切标志位。
5.1.3投入计时处理、超时和切除计时处理
可编程控制器采用定时器和计数器配合计时,定时器计时5分钟=3000*100ms,计数器对定时器计数,计数15天=360小时=4320个5分钟。计时程序梯形图如图5。2所示:
图5.2 投入计时梯形图
I0.4有信号表示一组冷却器投入,T37开始计时(5分钟),计时时间到T37输出保持有效,T40开始计时,T37有效保持500mm后被复位,同时T40被复位,T40的作用是保持T37有效一段时间帮助C1计时。每5分钟计数器计数一次,M0.3恒为无效。
PLC程序将冷却器的累积运行时间保存在数据存储,C1计数到4320时(15天)C1变为有效,在―自动‖时由投切判断做出切冷却器的决策,在手动状态时需要将计数器的当前值累加到累积运行时间存储区,将计数器复位重新开始计数。无论在―手动‖还是在。―自动‖模式下,只要冷却器被切除,就将计数器的当前值累加到累积
运行时间存储区,并清空计数器重新开始计数。
5.1.4投切判断和投切处理
投切判断根据运行条件做出是否进行投切冷却器操作的决策,然后由投切处理部分进行投切处理操作。进行投切判断的依据是变压器温度结合有差值裕度的投切温度阀值的控制策略,冷却器持续运行时间计时、冷却器累积运行时间计时和凝露监控器发出的凝露信号。
当变压器油温低于设定的切温度阀值时,进行切冷却器处理;温度介于投温度阀值和切温度阀值之间时不进行投切操作;当温度高于投温度阀值时进行投冷却器处理;当有冷却器的持续运行时间超过设定值时,就需要进行切冷却器处理,由切处理部分将持续运行时间到时的冷却器切除;当凝薅信号有效并维持时间超过设定值时,将一直进行投处理,将所有的冷却器全部投入运行,此时禁止进行切处理操作直至全投冷却器计时到时。冷却器持续运行时间到时执行切除冷却器和凝露全投冷却器且投入计时到时后再由按温度投、切的控制策略根据变压器油温进行投切判断。
投处理操作是从未投入运行的冷却器中选取累积运行时间最短的冷却器投入运行。选取累积运行时间最短冷却器的方法是:将一未投入冷却器的组号和累积时间存入一个比较存储区,然后将当前存储区内累积时间与下一个存储区内冷却器的累积运行时闻比较,如比较存储区内时间较大,将当前存储区的冷却器累积时间和组号存入比较存储区,进行下一次比较.最后根据比较存储区内的冷却器组号将该组号的控制接触器输出位置位。
切处理操作与投处理操作类似,只是选取的是持续运行时间最长的冷却器(计数器c1的值)。在进行完投切操作后都需要复位一个投切等待标志位,这个标志位在投切完成后复位4秒钟,暂时不允许投切,目的是使油温变化并维持稳定再进按温度投切,防止投入或切除过多的冷却器。
5.1.5通讯处理
自由口通讯方式通讯功能完全由用户程序控制,所有通讯任务由用户编程完成.在进行自由口通讯前必须进行通讯口工作模式的初始化,包括自由口波特率、奇偶校验、每个字符的数据位个数和协议选择。在本装置中我们采用9600的波特率、无奇偶校验,每个字符有8个数据位,同时设定串口为自由口通讯模式。初始
39
化操作在程序的初始化部分完成。
可编程序控制器有一个发送缓冲区,我们将准备发送的数据放在发送缓冲区中,这些数据包括变压器温度信息,三侧开关状态信息、电源故障信息,电源投入信息,冷却器运行和故障信息,信息按字节读取和发送。
由于上位计算机在读取串口数据时可能不能够将PLC一次发送的信息全部从串口缓冲区读取完,所以需要对发送信息进行编码便于上位计算机分辨信息内容。每个字节有8位,我们将每字节的高4位作为信息标示,上位计算机在读取信息后,可以根据这个标示判断读出的信息的内容。将一个字节的低4位作为信息位,信息位包括电源状态、冷却器运行状态、油流故障、电动机故障和接触器故障等。所有信息编码如表5.1所示。
表5.1 通讯信息编码表
信息标示 7 0 1 0 1 0 1 0 1 0 1 0
6 0 0 1 1 0 0 1 1 0 0 1
5 0 0 0 0 1 1 1 1 0 0 0
4 0 0 0 0 0 0 0 0 1 1 1
3 1电源工作 投温度阀值 1油流故障 2油流故障 3油流故障 4油流故障 5油流故障 6油流故障 7油流故障 8油流故障
2 2电源正常 切温度阀值 1冷却器工作 2冷却器工作 3冷却器工作 4冷却器工作 5冷却器工作 6冷却器工作 7冷却器工作 8冷却器工作
发送信息
1 1电源正常 三侧开关 冷却器全停 1接触器故障 2接触器故障 3接触器故障 4接触器故障 5接触器故障 6接触器故障 7接触器故障 8接触器故障
0 主辅电源 2电源工作 超温油温 1电动机故障 2电动机故障 3电动机故障 4电动机故障 5电动机故障 6电动机故障 7电动机故障 8电动机故障
PLC程序采集表中的信息,每隔一段时间就将信息内容写入发送数据缓冲区,用发送指令将信息通过串口发送出去,上位计算机通过读串口内容,将信息读入上位计算机中。
5.2上位机监视软件设计
上位机监视软件包括串口的设置和打开、串口数据的读取、数据的解析显示和保存,完成对变压器冷却及控制装置的监视任务。
5.2.1监视软件总体设计
上位计算机监视软件设计流程图如图5.3所示:
首先进行串口参数的设置,包括串口号、波特率、奇偶校验位、通讯位数和停止位数,然后打开串口;串口参数的设置和打开串口都有专门的函数。如果串口打开不成功,需要重新进行参数设置。串口打开成功后可以在监视软件的状态栏显示串口的各种信息。
串口打开成功后,就要创建新的线程,新创建的线程的作用是等待串口事件发生.之所以创建新的线程,是因为新创建的线程和主线程并列运行,可提高程序运行的效率.如果串口中一直没有数据,则继续等待。
如果串口中有数据,则用读串口函数将数据读入数据存储区,然后对读入数据进行解析。因为读串口函数不能一次将串口中的数据全部读出,所以在PLC发送时就对数据进行了标示,上位监视程序需要对读入的数据进行解析才能确定发送过来的数据的具体含义。
接下来程序根据解析得到的数据刷新监视软件可视区域。然后程序又继续等待串口数据。
5.2.2串口设置和打开
在对变压器冷却及控制装置进行监视前必须进行正确的串口的参数设置和打开串口,并且串口参数的设置要和可编程序控制器参数的设置相匹配。监视软件通过对话框对串口参数,包括串口号、波特率、奇偶校验位、通讯位数和停止位数进行设置,如图5.4所示:
串口设置完成后通过监视程序的菜单调用串口打开函数将串口设置对话框中选择的串口打开,并调用串口设置函数设置串口参数。如果所选串口已经打开或串口不存在,软件会通过对话框提示,需要重新设置串口参数。串口设置成功后,在监视软件的状态栏可以显示串口的各种参数;如果串口未打开或者打开失败,在状态栏也会有显示。
如果暂时需要关闭串口,可以通过监视软件的菜单,调用串口关闭函数将串口关闭。
41
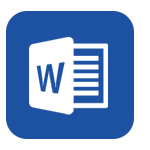





正在阅读:
基于PLC的电力变压器冷却控制装置的研究11-15
实用的贫困生助学金申请书汇总7篇03-31
分时图30分钟预测全天涨跌06-17
企业并购中的整合效应及风险分析---以海尔并购通用家电为例06-17
一棵大树作文600字06-28
2013-2014五年下册数学6单元教案03-06
关于做好离任村主职干部登记建挡工作的通知04-09
最美教师演讲稿:千言万语化作爱08-22
【工作总结】健美操教师个人工作总结05-31
- exercise2
- 铅锌矿详查地质设计 - 图文
- 厨余垃圾、餐厨垃圾堆肥系统设计方案
- 陈明珠开题报告
- 化工原理精选例题
- 政府形象宣传册营销案例
- 小学一至三年级语文阅读专项练习题
- 2014.民诉 期末考试 复习题
- 巅峰智业 - 做好顶层设计对建设城市的重要意义
- (三起)冀教版三年级英语上册Unit4 Lesson24练习题及答案
- 2017年实心轮胎现状及发展趋势分析(目录)
- 基于GIS的农用地定级技术研究定稿
- 2017-2022年中国医疗保健市场调查与市场前景预测报告(目录) - 图文
- 作业
- OFDM技术仿真(MATLAB代码) - 图文
- Android工程师笔试题及答案
- 生命密码联合密码
- 空间地上权若干法律问题探究
- 江苏学业水平测试《机械基础》模拟试题
- 选课走班实施方案
- 变压器
- 冷却
- 装置
- 基于
- 电力
- 控制
- 研究
- PLC
- 二年级数学思维训练
- 第九章课外、校外教育
- 统计学期末考试复习试卷及答案
- 三相笼型感应电动机电磁设计
- 湖北省鄂州市吴都中学2015-2016学年八年级(上)期末生物试卷(解析版)
- 实验3LL(1)语法分析程序
- 移动支付与电子支付的区别 - 图文
- 08全国造价员考试模拟试题五
- 初中英语议论文范文BB浅谈初中英语教学中阅读与写作的整合(四)!初中英语介词课件
- 电子商务支付与结算期末试题
- 2010学年《物流法律法规》期中试卷
- 生物分离工程考试范围
- 《入菩萨行论释善说海》思考题第二品-智悲佛网(精)
- 转基因在中国 - 中国转基因现状
- 工程热力学(第五版 - )课后习题答案
- 农村干部工作目标责任制考核办法
- 2010年春节期间市区文化活动安排表 - 图文
- 职前职后一体化教师培养模式的实践探索
- 历史文化名村保护规划说明书 - 图文
- 农村个人建房施工合同书