180吨天电镀污泥干化及熔炼处理工艺设计最终版
更新时间:2023-10-22 22:59:01 阅读量: 综合文库 文档下载
- 180吨天宫空间站推荐度:
- 相关推荐
设计总说明
电镀污泥中的铜、镍、银等重金属氢氧化物不稳定,随意堆放时在雨水的淋溶作用会渗漏到土壤中污染环境,并通过生物链危害人类健康。但电镀污泥中所含的重金属都是不可再生资源,不对其进行回收意味着重大的浪费。
本设计要求处理180吨/天的电镀污泥,原污泥为经过脱水处理的含水率约75%的湿污泥。针对电镀污泥的特点和废物资源化利用的要求,结合国内处理电镀污泥的成功经验,决定选用先干化后熔炼的处理工艺。虽然该工艺设备投资成本较高,但其对重金属回收率高,处理流程短,炉渣可回收利用,可实现资源的综合利用。
设计基本工艺流程为:储泥室→回转烘干机→制砖机→熔炼炉→粗金属、炉渣、煤灰等回收。
本设计所用的主要设备有回转烘干机、砌块成型机、密封式熔炼炉、脉冲布袋收尘器、脱硫塔、活性炭吸附塔等。设计工艺总投资为417.64万元。
关键词:电镀污泥,干化,熔炼,重金属,回收
Design illuminate
Copper, nickel, silver and other metal hydroxides in electroplating sludge is not stable, if piled up at random at leaching by the rain .its can leak into the soil and pollute the environment, and harm human health through the food chain. But the heavy metals in electroplating sludge are non renewable resources, not to recovery means huge waste.
In this design, projects required to treat 180 tons/day electroplating sludge. Moisture content of the original sludge,which has been pressed by the frame filter,is approximately 75%. Aiming at the characteristic of electroplating sludge, and in the light of the successful experience of external treatment of electroplating and mature technology of internal treatment of that, we select drying and smelt technology. Although this process equipment investment cost much, but it have the high recovery rate of the heavy metal, the short process , and the slag can be Recyclable.
Basic process is: Stored mud room → Rotary dryer →brick machine →smelt→ Ash and other recycled.
The main equipment used in the design is Rotary Dryer, smelter, block making machine, Pulse bag filter, desulfurization tower, activated carbon adsorption tower and so on. The total investment is 4176400 yuan.
Keywords:electroplating sludge, mummification, smelt, heavy metal, recycle
目 录
1、概述 ...................................................................................................................................... 1
1.1设计名称 ...................................................................................................................... 1 1.2设计要求 ...................................................................................................................... 1 1.3处理处置的一般要求 .................................................................................................. 1 1.4项目意义 ...................................................................................................................... 2 2、设计背景 .............................................................................................................................. 3
2.1电镀污泥的特点 .......................................................................................................... 3 2.2电镀污泥处理处置现状 .............................................................................................. 3 2.3电镀污泥处理与处置方法 .......................................................................................... 4
2.3.1固化剂固化 ....................................................................................................... 4 2.3.2填埋 ................................................................................................................... 5 2.3.3焚烧热处理 ....................................................................................................... 5 2.4电镀重金属污泥的资源化综合利用 .......................................................................... 5
2.5.1回收重金属 ....................................................................................................... 6 2.5.2生产改性塑料制品 ........................................................................................... 8
3、设计范围、依据及原则 ...................................................................................................... 9
3.1设计范围 ...................................................................................................................... 9 3.2设计依据 ...................................................................................................................... 9
3.2.1国家法律、法规及政策 ................................................................................... 9 3.2.2地方法规及政策 ............................................................................................. 10 3.2.3技术规范和行业标准 ..................................................................................... 10 3.3设计原则 .................................................................................................................... 11 4、设计内容 ............................................................................................................................ 12
4.1工艺流程及说明 ........................................................................................................ 12 4.2干化工艺 .................................................................................................................... 14
4.2.1干化过程 ......................................................................................................... 14
4.2.3加热方式 ......................................................................................................... 14 4.2.4污泥干化的热源 ............................................................................................. 15 4.2.6干化设备 ......................................................................................................... 16 4.2.7选型计算 ......................................................................................................... 16 4.3制砖工艺 .................................................................................................................... 20 4.4熔炼工艺 .................................................................................................................... 21
4.4.1工艺计算 ......................................................................................................... 22 4.4.2进气量计算 ..................................................................................................... 25 4.4.3出气量计算 ..................................................................................................... 26 4.5除尘系统 .................................................................................................................... 26
4.5.1重力沉降室设计计算 ..................................................................................... 27 4.5.2U型管式冷却器选择 ...................................................................................... 28 4.5.3除尘器设计计算 ............................................................................................. 28 4.6污染气体处理系统 .................................................................................................... 31
4.6.1双碱法脱硫 ..................................................................................................... 31 4.6.2活性炭吸附法脱氮 ......................................................................................... 33 4.7灰渣处理系统 ............................................................................................................ 34 4.8功能区布置 ................................................................................................................ 34 5、工艺成本概算 .................................................................................................................... 36
5.1土建及设备投资概算 ................................................................................................ 36 5.2设备安装调试费用 .................................................................................................... 37 结论 .......................................................................................................................................... 38 参考文献 .................................................................................................................................. 39 致谢 .......................................................................................................................................... 40
1、概述
1.1设计名称
180吨/天电镀污泥干化及熔炼处理工艺设计。 1.2设计要求
某电镀污泥处理中心建设内容为:
(1)一套电镀污泥烘干系统,用于对进厂电镀污泥进行干化,处理能力为180吨/天(进厂湿污泥,含水率约75%左右);
(2)一套制砖设备,用于将干化后的电镀污泥制成砖状;
(3)一套鼓风熔炼设备,用于熔炼干化后的电镀污泥(干污泥,含水率约20%)。 选择合适的工艺流程,计算各处理构筑物的主要参数,选定主要设备的型号及处理能力,并绘出总平面布置图、工艺流程图、空气管道布置图、烘干设备剖面图,对辅助构筑物进行布置和设计,给出整个工程的投资概算。
1.3处理处置的一般要求
污泥处理、处置应实施全过程管理,并体现“减量化、稳定化、无害化”的原则,在坚持“安全、环保”的原则下,实现污泥的综合利用,回收和利用污泥的能源和物质。 污泥处理工艺的选择应优先选择污泥源头削减、污泥稳定化和能源回收等污泥处理工艺,降低总体运行费用和能耗,减轻末端污泥处置的负荷,缓解污泥在处理和处置过程所带来的环境污染问题。
污泥处理和处置技术的选择遵循因地制宜的原则,应首先根据电镀污泥的性质和特点、当前的处理水平和污泥处理厂技术情况、消纳途径和消纳能力等实际情况,确定最佳的污泥最终处置或综合利用方式,然后经严格的技术经济论证和环境影响评价,选用合理的处理、处置工艺。
1
应依据环境保护规划、固体废弃物处理处置规划的要求,对污泥进行区域性规划和专项规划,合理确定污泥处理和处置设施的布局和设计规模,确保污泥的最终安全处置。
污泥应以最终安全处置为目标,鼓励多种形式的综合利用和处置,鼓励以政府采购为主导的污泥土地利用,限制性的采用填埋和农业利用技术。在土地资源紧张且经济较为发达的地区,可选用干化、熔炼技术,污泥熔炼灰渣应优先考虑综合利用[1]。 1.4项目意义
电镀废水处理过程中产生的污泥含有有害重金属,它具有易积累、不稳定、易流失等特点,如不加以妥善处理,任意堆放,其直接后果是污泥中的Cu、Ni、Zn、Cr等这些重金属在雨水淋溶作用下.将着污泥一土壤/水一农作物一人体的路径迁移,并可能引起地表水、土壤、地下水的次生污染,甚至危及生物链,造成严重的环境破坏。针对电镀污泥的特点及其危害性.从环境污染防治和资源循环利用的角度考虑,主要采用以下两种处理方式,一是经过处理后,使污泥不会引起二次污染而丢弃并贮存,即无害化处置;二是使对污泥中的重金属资源进行综合回收,即资源化利用。本项目投运后可最大限度解决电镀污泥污染问题,并真正做到污泥减量化、稳定化、无害化、资源化处置。
2
2、设计背景
电镀污泥是指电镀行业中废水处理后产生的含重金属污泥废弃物,被列入国家危险废物名单。作为电镀废水的“终态物”,虽然其量比废水要少得多,但是由于废水中的Cu、Ni、Cr、Zn、Fe等重金属都转移到污泥中,从某种意义上说,电镀重金属污泥对环境的危害要比电镀废水严重。如果对这种危害性极大的电镀污泥不作任何处置,其对生态环境的破坏是不言而喻的,另一方面,如果对电镀污泥中品位极高的重金属物质不加以回收利意味着资源的巨大浪费。目前,由于我国电镀行业存在厂点多、规模小、装备水平低及污染治理水平低等诸多问题,大部分电镀污泥仍只是进行简单的土地填埋,甚至随意堆放,对环境造成了严重污染。因此,对电镀重金属污泥进行无害化处置和资源化综合利用势在必行。 2.1电镀污泥的特点
多数的电镀废水处理方法都要产生污泥,而化学沉淀法是产生污泥的主要来源。有些方法,如离子交换法和活性炭法虽不直接产生污泥,但在方法的某些辅助环节,如再生液的处理也要产生污泥。由于化学法在国内外都被作为一种主要的处理方法,所以电镀污泥的形势是很严峻的。按照对电镀废水处理方式的不同,可将电镀污泥分为混合污泥和单质污泥两大类。前者是将不同种类的电镀废水混合在一起进行处理而形成的污泥;后者是将不同种类的电镀废水分别处理而形成的污泥,如含铬污泥、含铜污泥、含镍污泥、含锌污泥等。但是,实际上大多数电镀小企业的废水经过处理后得到的多是混合污泥。因此,目前针对电镀污泥的处理和资源化利用也是以混合污泥为主要对象[2]。
2.2电镀污泥处理处置现状
电镀污泥可以分为分质污泥和混合污泥两大类,不同类型的污泥采用不同的方法加以处理和利用。国外对有价值的分质电镀污泥一般是送交冶炼金属,如铬污泥、镍
3
污泥用于炼不锈钢,铜污泥用于炼铜等。而对于混合污泥多采用固化处理,如经水泥固化并经浸渍检验合格后安全填埋。日本、美国、西欧等国家对污泥处理的专业化程度很高,都设有专门的污泥处理工厂,负责本地区的电镀污泥处理。国内处理电镀污泥侧重于含铬分质污泥的综合利用研究。近年来对混合污泥也开始研究其处理和应用技术,并逐渐走上了专业化处理的道路。 2.3电镀污泥处理与处置方法
污泥无害化是一个非常广泛的概念,实际上现在还做不到对污泥无害化处理。如现代技术还无法将污泥中的重金属完全去除。但是从狭义上讲,污泥无害化处理可以理解为减量、去除、分解或者固定污泥中的有害物质及消毒灭菌,以减轻处理后的污泥在污泥最终处置中对环境造成的危害。狭义上的污泥无害化处理过程.往往包括在稳定处理之中。如厌氧和好氧消化除了降解有机物外,还可以大大减少病原体的数量。脱水前的石灰调理、热工调理、巴氏灭菌或者长期储存可使污泥消毒,在污泥固态好氧发酵中.通过腐质酸等可以与污泥中离子态重金属发生反应,从而钝化重金属的危害。污泥处理与处置的无害化技术是实现污泥资源化利用的前提条件。中国在2001年12月17日发布的《危险废物污染防治技术政策》(环发[2001]199号)中,要求到2015年,所有城市的危险废物基本实现环境无害化处理处置。现行电镀污泥无害化处理方法有:
2.3.1固化剂固化
在危险固体废物诸多处理手段中,固化技术是危险废物处理中的一项重要技术,在区域性集中管理系统中占有重要地位。和其他处理方法相比,它具有固化材料易得、处理效果好、成本低的优势。固化过程是利用添加剂改变废物的工程特性(例如渗透性、可压缩性和强度等)的过程。近年来,美国、日本及欧洲一些国家对有毒固体废物普遍采用固化处置技术,并认为这是一种将危险物转变为非危险物的最终处置方法,所采用的固化材料有水泥、石灰、玻璃和热塑料物质等。其中,水泥固化是国内外最常用的固化技术,在美国被认为是一种很有前途的技术,它被证明对一些重金属的固定是
4
非常有效的。美国国家环保局也确认它对消除一些特种工厂所产生的污泥有较好的效果。 2.3.2填埋
从经济、技术、废物现状来看,填埋技术是比较适合中国国情的一项危险废物无害化处置途径,但国内针对电镀污泥这一类危险废物的填埋技术仍处于较低的水平。由于对大多数工业危险废物只是简单的堆放或填埋,因此,对环境的破坏相当严重,特别是对地下水的污染问题十分突出。但技术的障碍是有限期的,在目前和不久的将来,填埋仍然是必要的。特别强调的是危险废物的安全填埋,即在填埋前必须进行预处理使其稳定化,以减少因毒性或可溶性造成的潜在危险。近年来,国家逐步提高了对电镀污泥等危险废物的管理和处置力度。1995年,在广东深圳建成了第一座符合国际标准的危险废物填埋场,2001年,国家颁布了《危险废物填埋污染控制标准》(GB18598—2001),这对电镀污泥真正实现无害化处置打下了良好的基础。 2.3.3焚烧热处理
污泥焚烧是利用高温将污泥中的有机物彻底氧化分解,最大程度地使污泥中的某些剧毒成分毒性降低。通过焚烧热处理,可以大大减少电镀污泥的体积,降低对环境的危害。此外,焚烧的产物还有利用价值,如灰渣可用于制砖、铺路或他用,焚烧产生的热量可用于发电。因此,焚烧热处理是实现电镀污泥减量化、无害化的一种快捷、有效的技术。近年一些学者在焚烧减容的基础上,对焚烧渣的资源化利用进行了广泛的研究,廖昌华等[3]以含低浓度Cu、Ni的电镀重金属污泥为研究对象,在适宜的温度下,通过焚烧预处理,使污泥中的重金属含量提高,从而为最终浸出有价金属制取海绵铜和硫酸镍产品创造了条件。但是,由于这种方法能耗较高,对焚烧设备和条件有一定要求,一般的小电镀厂难以承受巨额的处理费用,所以很难得到大面积的推广。 2.4电镀重金属污泥的资源化综合利用
由于资源贫化和环境污染的加剧,电镀污泥作为一种重要的重金属资源加以回收
5
利用,一直是国内外研究的重点。工业化国家上世纪70—80年代已普遍重视从电镀污泥中回收重金属的新技术开发。中国在“七五”和“八五”期间也专门设立了关于电镀污泥资源化的攻关课题。作为一种廉价的二次资源,只要采用适当的处理方法,电镀污泥便能变废为宝,带来可观的经济效益和环境效益。随着经济与社会的快速发展,电镀污泥的资源化利用将逐渐成为前景广阔的绿色产业。 2.4.1回收重金属 1、浸出一沉淀法
对电镀污泥进行选择性浸出,使其中的重金属分组溶出,这是回收重金属的关键一步,也是决定后续金属回收率的关键所在。金属的浸出溶解主要有酸浸和氨浸两种工艺。目前国际上偏向于采用选择性相对较好的氨浸。由于沉淀法分离回收浸出液中的重金属,工艺简单,应用较为广泛。捷克的研究者[4]提出了一种处理镍电镀污泥的多级沉淀工艺,并在实验室进行了研究。该技术包括污泥酸浸、多种沉淀方法净化硫酸盐浸出液,使共存于镍电镀污泥中的杂质,如Fe、Zn、Cu、Cr、Cd、Al等被脱除,最后一级沉淀中镍以氢氧化物的形式从净化溶液中分离出来。镍的最终沉淀物达到的纯度足以在冶金工业中直接再利用。毛谙章等[5]研究了硫化物沉淀分离提纯、氯酸钠硫酸体系浸出回收铜的工艺路线,铜的总回收率达到94.5%。陈凡植等研究采用常温下浸出、铁屑置换、多步沉淀净化制取硫酸镍和固化处理工艺综合利用电镀污泥,得到的海绵状铜粉,品位在90%以上,回收率达95%,还可以得到工业纯的硫酸镍,镍的回收率大于80%。 2、浸出一溶剂萃取法
电镀污泥的溶剂萃取法,是在浸出液中加入与水互补相容的有机溶剂,或含有萃取剂的有机溶剂,通过传质过程,使污泥中的某些重金属物质进入有机相,从而达到分离浓集的目的,也称液一液萃取法。20世纪70年代,瑞典国家技术发展委员会支持Chalmers大学开发了Am—MAR“浸出一溶剂萃取”工艺回收电镀污泥中的Cu、Zn、Ni等重金属物质,并逐步形成工业规模。葡萄牙的J·E·Silva等[6]对含有Cu、Cr、Zn、Ni等重金属的电镀污泥,采用硫酸浸出一置换除铜一沉淀除铬一D2EHPA和
6
Cyancx 272萃取分离锌、镍一结晶的工艺进行了研究。结果显示,D2EHPA对锌的萃取率要比Cyancx 272高,且存在于有机相中的锌能全部被回收,经过结晶后,能得到纯度相当高的硫酸镍产品。在铜、铬的去除阶段,铜的回收率达90%,产生的Cr—CaCO3,沉淀,有可能制作硅酸盐材料。
3、电解法
根据物理化学中的电解基本原理,在国内一些冶炼厂对主要含Fe(OH)3和Cr(OH) 组分的污泥进行了电解法处理,其中武汉冶炼厂的方法值得借鉴。他们将一定量的水和硫酸加入到污泥中,沸腾后静止30 min,过滤后的滤液移至冷冻槽,然后加入理论量1~2.5倍的硫酸铵,使生成硫酸铬和硫酸铁转变为铁矾,根据铬矾和铁矾在低温(75℃)条件下溶解度的不同而达到铬、铁的分离,最后,可回收90%以上的铬。 4、氢还原分离法
氢还原分离金属物质是种较成熟的技术。上世纪50年代以来,在工业上用氢气还原生产铜、镍和钴等金属,取得了显著的经济效益和社会效益。采用湿法氢还原对电镀污泥氨浸产物中的Cu、Ni、Zn等有价金属进行了综合回收处理,成功地分离出金属铜粉和镍粉。实验结果表明,在弱酸性硫酸铵溶液中,可以获得较好的铜镍分离效果。所得两种金属粉末的纯度可达到99.5%,符合3 铜粉和3 镍粉的产品要求,铜的回收率达到99%,镍的回收率达到98%以上。并且在此基础上,对还原尾液中的锌进行了回收。该法流程简单,投资少,产品纯度高,值得在工业生产中进一步改进推广。 5、煅烧酸溶法
Jitka Jandova等[7]通过实验研究发现,对含铜电镀污泥进行酸溶、煅烧、再酸溶,最后以铜盐的形式回收,是一种简便可行的方法。在高温煅烧过程中,大部分杂质,如Fe、Zn、Al、Ni、si等转变成溶解缓慢的氧化物,从而使铜在接下来的过程中得以分离,最终以Cu 4(SO4 )6 H20的形式回收。这种方法流程简单,不需要添加别的试剂,具有较强的经济性和简便性。但回收得到的铜盐含杂质较多,工艺有待进一步优化。 6、高温还原工艺
以含铜污泥为例:制砖后的含铜固体废物送人熔炼炉,加入焦炭与造渣剂石英石
7
和石灰石,焦炭燃烧放出的热量足以使炉料熔化,并使熔体过热,同时形成一定的还原气氛,使铜及其它金属氧化物还原,得到铜含量大于81%的粗铜与铜含量约为40%的冰铜。具体反应过程为:
在高温作用下,高温还原物料中的铜发生氧化,形成Cu2O,由于铜对硫的亲和力大于铁对硫的亲和力,所以在高温还原过程中,产出的Cu2O被炉料中的FeS硫化成Cu2S。还原过程中产生的FeO将与炉料中的SiO2及CaO等造渣物质形成炉渣,含铜率小于0.4%。由于冰铜与炉渣实际上不相互溶解,并且两者比重相差较大,从而可较好地分离,从而得到冰铜产品。 2.4.2生产改性塑料制品
电镀污泥与废塑料联合生产改性塑料制品是国内一项独创的新技术,由上海多家科研单位联合开发。其基本原理是采用塑料固化的方法,将电镀污泥作为填充料,与废塑料在适当的温度下混炼,并经压制或注塑、成型等过程,制成改性塑料制品。电镀污泥在专用TGZS 300型高湿物料干燥机中经400—600℃高温干燥后,重金属基本达到稳定,浸出试验符合国家标准。研究表明,未经改性的电镀污泥与塑料之间属物理混合,故属包裹型固化。但是,经用表面活性剂(如油酸钠)改性处理后,经X射线粉末衍射图谱分析表明,具有显著的化学作用,提高了污泥的疏水性,接触角达100。左右,因此可以推断与塑料有较好的相容性,充填均匀,机械性能将有所改善。该工艺生产的塑料制品(包含改性、干化后的电镀污泥),通过浸出试验表明,重金属的浸出率和塑料制品的机械强度都能达到规定指标。电镀污泥与废塑料联合生产改性塑料制品,既解决了废料的安全处置,又充分利用了废物资源,是变废为宝,综合利用,实现废物资源化的重要途径,具有良好的社会和环境效益。
8
3、设计范围、依据及原则
3.1设计范围
选择合适的工艺流程,计算各处理构筑物的主要参数,选定主要设备的型号及处理能力,并绘出总平面布置图、工艺流程图、空气管道布置图、烘干及焚烧设备剖面图,对辅助构筑物进行布置和设计,给出整个工程的投资概算。 3.2设计依据
3.2.1国家法律、法规及政策
(1)《中华人民共和国环境保护法》(1989.12.26); (2)《中华人民共和国节约能源法》(2008.4.1); (3)《中华人民共和国可再生能源法》(2006.1.1); (4)《中华人民共和国城市规划法》(1990.4.1); (5)《中华人民共和国土地管理法》(1998.8.29); (6)《中华人民共和国大气污染防治法》(2000.4);
(7)《中华人民共和国固体废物污染环境防治法》(2005.4.1); (8)《中华人民共和国环境噪声污染防治法》(1996.10);
(9)《全国生态环境保护纲要》,国务院国发[2000]38号,(2000.11.26); (10)《建设项目环境保护管理条例》,国务院第253号令,(1998.11); (11)《建设项目环境保护设计规定》(1987.3.20);
(12)《关于落实科学发展观加强环境保护的决定》,国发〔2005〕39号;
(13)《产业结构调整指导目录》,国家发展和改革委员会第40号令,(2005.12); (14)《国家危险废物名录》(2008.8.1);
(15)《危险废物转移联单管理办法》(国家环保总局令第5号),(1999.10.1); (16)《危险废物污染防治技术政策》(环发[2003]199号);
9
(17)《关于核定建设项目主要污染物排放总量控制指标有关问题的通知》(国家环
保总局,环办[2003]25号)。 3.2.2地方法规及政策
(1)《广东省建设项目环境保护管理条例》,广东省人大常委会(2004.7.29第二次
修改;
(2)《广东省环境保护条例》(2005.1.1);
(3)《广东省乡镇企业环境保护管理办法》,粤府[1994]12号; (4)《广东省环境保护规划纲要(2006-2020年)》(2006); (5)《广东省固体废物污染环境防治条例》(2004.5.1); (6)《广东省排放污染物许可证管理办法》(2001.7);
(7)《关于加强固体废物监督管理工作的意见》,粤环〔2006〕114号,(2006.12.27); (8)《关于进一步明确危险废物管理有关问题的通知》,粤环〔2007〕79号,2007
年9月27日;
(9)《广东省固体废物污染防治规划(2001-2010)》,粤环[2003]54号;
(10)《关于进一步明确固体废物环境管理有关问题的通知》,粤环〔2008〕117号,
(2008.8.25);
(11)《广东省严控废物处理行政许可实施办法》(2009.5.1); (12)《广东省环境保护规划》(2005.3);
(13)《广东省产业结构调整指导目录》(2007年本)粤发改产业【2008】334号。 3.2.3技术规范和行业标准
(1)《电镀污染物排放标准》(GB21900-2008); (2)《电镀行业清洁生产评价指标体系(试行)》; (3)《清洁生产标准电镀行业》(HJT314-2006); (4)《环境风险评价技术导则》(HJ/T169-2004); (5)《危险废物污染防治技术政策》环发[2001]199号。
10
3.3设计原则
(1)贯彻执行国家工程建设与城市的发展相协调,既保护环境,又最大程度地发挥工程效益。根据设计要求,所选处理工艺力求技术先进成熟、处理效果好、运行稳妥可靠、高效节能、经济合理,确保污泥处理效果,减少工程投资及日常运行费用。妥善处理和处置污泥处理过程中产生的废气,避免造成二次污染。
(2)为确保工程的可靠性及有效性,提高自动化水平,降低运行费用,减少日常维护检修工作量,改善工人操作条件。
(3)采用现代化技术手段,实现自动化控制和管理;做到技术可靠、经济合理。 (4)在征地范围内,厂区总平面布置力求在便于施工、便于安装和便于维修的前提下,使各处理构筑物尽量集中,节约用地,扩大绿化面。
(5)厂区建筑风格力求统一,简洁明快、美观大方,并与厂区周围景观相协调。 积极创造一个良好的生产和生活环境,把处理厂设计成现代化的园林式工厂。 (6)尽量减少二次污染。
11
4、设计内容
4.1工艺流程及说明
本项目使用的电镀污泥处理装置主要由干化、制砖、熔炼以及烟气处理四部分工艺组成。
电镀污泥运进厂,含水率约为75%,首先投入烘干机烘干水分。烘干机采用高温烟气烘干电镀污泥水分,高温烟气来自燃煤燃烧室,烟气进入烘干机内的温度为300~900℃,当污泥水分含量降至约20%,由皮带输送至制砖机制砖,再送入熔炼炉内。加入焦炭与造渣剂石英石和石灰石,焦炭燃烧放出的热量足以使炉料熔化,并使熔体过热,同时形成一定的还原气氛,使铜及其它金属氧化物还原,得到铜、镍含量大于8 1%的粗铜镍与铜含量约为40%的冰铜[9]。
燃烧炉燃煤产生的煤渣主要成分是轻质的硅酸盐类无机物,不属于危险废物,可以用作建筑辅材使用,直接送水泥厂作为水泥生产的辅助原料使用。
烘干机布袋除尘器收集的粉煤灰及粉尘可能含有重金属,属于危险废物,送相关资质公司处理。
烘干机出口烟气与熔炼炉尾气集中处理,烟气中含有大量的粉尘和少量的二氧化硫、氮氧化物、重金属,经重力沉降室、U形管冷却、布袋除尘、双碱法脱硫、沥青活性碳吸附催化还原脱氮等处理,最后经高烟囱排入大气,烟气中污染物排放浓度能够达到《大气污染物排放限值》(DB44/27-2001)第二时段二级标准和《工业炉窑大气污染物排放标准》(GB9078-1996)的要求。
重力沉降室和布袋除尘器收集的集尘灰属于危险废物,送相关资质公司处理。工艺流程见图4.1:
12
电镀污泥 集尘灰 重力沉降布袋除尘器 危险废物送相关资质公司处理 U形冷却器 集尘灰 双碱法脱沥青活性炭吸附催化烟囱 烟尘、SO2、氮氧化物 焦炭、铁矿石、石灰 噪音 干化污泥 烘干机 粗铜、镍 制砖机 熔炼炉 炉渣 煤渣 噪音 煤 燃烧炉 用作建材 送水泥厂综 合利用 图4.1 电镀污泥熔炼工艺流程及产污分析图
13
4.2干化工艺
干化工艺的选择和设计应充分考虑降低污泥吨水蒸发热耗和吨水蒸发电耗,综合 选择干化产品含固率、干化热源和介质、循环气体量和温度,根据实际情况配置循环气体净化和余热回收。 4.2.1干化过程
干化意味着在单位时间里将一定数量的热能传给物料所含的湿分,这些湿分受热后汽化,与物料分离,失去湿分的物料与汽化的湿分被分别收集起来,这就是干化的工艺过程。
从设备角度来描述这一过程,包括上料、干化、气固分离、粉尘捕集、湿分冷凝、固体输送和储存等。如果因物料的性质(粘度、含水率等)可能造成干化工艺的不稳定性的(如黏着、结块等),则有必要采用部分干化后产品与湿物料混合的工艺(返料、干泥返混)。此时,在上料之前和固体输送之后应相应增加输送、储存、分离、粉碎、筛分、提升、混合、上料等设备[10]。 4.2.2加热方式
污泥干化的加热方式:直接干化和间接干化。
干化是依靠热量来完成的,热量一般都是能源燃烧产生的。燃烧产生的热量存在于烟道气中,这部分热量的利用形式有两类:
(1)直接利用:将高温烟道气直接引入干燥器,通过气体与湿物料的接触、对流进行换热。这种做法的特点是热量利用的效率高,但是如果被干化的物料具有污染物性质,也将带来排放问题,因高温烟道气的进入是持续的,因此也造成同等流量的、与物料有过直接接触的废气必须经特殊处理后排放。
(2)间接利用:将高温烟道气的热量通过热交换器,传给某种介质,这些介质可能是导热油、蒸汽或者空气。介质在一个封闭的回路中循环,与被干化的物料没有接触。热量被部分利用后的烟道气正常排放。间接利用存在一定的热损失。对干化工艺来说,直接或间接加热具有不同的热效率损失,也具有不同的环境影响,是进行项目
14
环评和经济性考察的重要内容。直接加热形式中热源烟气直接成为介质,其热效率接近燃烧效率本身。其余加热形式均是通过换热设备将热传给某种介质的间接加热。烟气可以通过热交换器将热量传给空气,空气作为换热介质与湿物料进行接触。烟气可以提高热交换器将热传递给导热油或蒸汽,然后利用导热油或蒸汽来加热金属或工艺气体,由金属热表面或工艺气体与湿物料进行接触。这两类换通过热交换器的换热均形成一定的热损失,一般来说在8-15%之间。
根据电镀污泥的性质,综合考虑设备成本、人力成本等因素,本设计使用直接干化法。
4.2.3污泥干化的热源
干化的主要成本在于热能,降低成本的关键在于是否能够选择和利用恰当的热源。 干化工艺根据加热方式的不同,其可利用的能源来源有一定区别,一般来说间接加热方式可以使用所有的能源,其利用的差别仅在温度、压力和效率。直接加热方式则因能源种类不同,受到一定限制,其中燃煤炉、焚烧炉的烟气因量大和腐蚀性污染物存在而难以使用,蒸汽因其特性无法利用。按照能源的成本,从低到高,分列如下: (1)烟气:来自大型工业、环保基础设施(固废焚烧炉、电站、窑炉、化工设施)的废热烟气是零成本能源,如果能够加以利用,是热干化的最佳能源。温度必须高,地点必须近,否则难以利用。
(2)燃煤:非常廉价的能源,以烟气加热导热油或蒸汽,可以获得较高的经济可行性。尾气处理方案是可行的。 (3)热干气:来自化工企业的废能。
(4)沼气:可以直接燃烧供热,价格低廉,也较清洁,但供应不稳定。 (5)蒸汽:清洁,较经济,可以直接全部利用,但是将降低系统效率,提高折旧比例。可以考虑部分利用的方案。
(6)燃油:较为经济,以烟气加热导热油或蒸汽,或直接加热利用。
(7)天然气:清洁能源,但是价格最高,以烟气加热导热油或蒸汽,或直接加热利用。
15
考虑燃料的成本、易得性等因素,本设计选用燃煤作为烘干燃料。 4.2.4干化设备
市场上的污泥干燥设备主要有:回转式烘干机(即转鼓干燥机)、间接加热式回转圆通干燥机、带粉碎装置的回转圆通干燥机、流化床干燥机、蝶式干燥机、浆叶式干燥机、盘式干燥机、带式干燥机、太阳能污泥干燥房等。
本设计选用回转式烘干机,相对于其他干燥设备,回转式烘干机有以下特点: 1、回转式烘干机热效率高,节能效果明显。
2、烘干机理科学公道、高效节能。物料在内筒与热气流以辐射、对流、传导形式进行热交换,在外筒热交换以传导、对流形式并用。
3、该机长度缩短,有利于工艺布置。整机长度比单筒烘干机缩短约40%左右,从而减少厂房的建筑面积,节约工程投资,也更适合于老厂改造的工艺布置。 4、该机采用物料与热气流顺流烘干工艺,合用范围广。它能适应粘土、煤、矿渣、铁粉等各种原材料的烘干,也合用于冶金、化工等部分的各种散状物料的烘干。 5、该机结构紧凑。整机水平布置,采用托轮支承,取消了大小齿轮传动,代之以托轮传动,使设备安装更利便、操纵更简朴、运行更可靠、运转率更高。
6、多种扬料板设计,角形扬料板与万字扬料板有机结合,使物料与热烟气交换更充分,减少了烘干机筒体内“风洞”产生的机理。
7、采用变频调速,调整烘干机设备筒体转速,根据入机水分,产量要求,采用适当的转速,确保下道工序的需求[9]。 4.2.5选型计算
本项目要求湿污泥在干燥机中干燥至水分含量为20%,干燥机的选型按上述干燥率进行选择,选用燃煤烟气作为热介质,选择回转式干燥机,干化后输送至制砖机。并有燃烧系统一套,以提供干燥烟气。
回转式烘干机的生产流程如图所示,其主要附属设备有烘干机燃烧室,输送带与烟气处理装备等。污泥由皮带机2送至喂料端锻,经下料溜子进入烘干机5。回转式
16
9 9 10 离心泵 鼓风机 管道管件 2 4 1 台 65FZS-25 台 — 批 0.8 0.5 — 1.6 2 20 192.6 外购件 外购件 外购件 小计T2 5.2设备安装调试费用
设备运输安装费按设备投资10%计算,调试费用按设备总投资3%计算,具体费用见表5.3:
表5.3安装调试费用表
编号 T3 T4 小计T5
内 容 运输费、安装费T3=T2×10% 调试费=T2×3% 金额(万元) 19.26 5.78 25.04 工艺建设总投资:T1 + T2 + T3 = 417.64万元
37
结论
在本次设计方案中,通过研究电镀污泥的特点、来源、处理方法、工艺流程以及组合工艺路线的选择,并参照了国内处置电镀污泥的成功经验,采取了成熟、稳定、节能、占地少、效率高的先干化后熔炼的处理工艺。原本含水率为75%的电镀污泥经过回转烘干机后,通过压力成型制成砖状进入鼓风熔炼炉熔炼,其熔炼余物回收利用,烘干、熔炼烟气通过冷却管、双碱脱硫塔、活性炭吸附塔最后由烟囱排放至大气中。所用工艺稳定实用,技术先进成熟,运行管理容易。从整体看,整个工艺流程布局合理,工艺总投资为417.64万元。
本项目属于固体废物处置项目,是一项环保工程,处置对象是电镀污泥,本着对危险废物“减量化、资源化和无害化”的原则,该项目的建设可以提高当地的清洁生产水平,促进相关产业实现可持续发展,有利于改善当地的环境质量,对削减地区危险废物排放量,改善环境质量和城市投资环境,促使地区发展,具有很好的社会效益。
38
参考文献
[1] 赵由才. 实用环境工程手册: 固体废物污染控制与资源化[M]. 化学工业出版社,
2002:15-19.
[2] 石太宏,陈可. 电镀重金属污泥的无害化处置和资源化利用[J]. 污染防治技术,
2007,20(2):48-52.
[3] 廖昌华,孙水裕,张志.焚烧温度对电镀污泥后续处理影响研究[J].再生资源,
2002(5):34-36.
[4] 梁俊兰.从电镀污泥中回收镍[J].有色冶炼.1999,28(6):46-48. [5] 毛谙章.陈志传,张志清.等.电镀污泥中铜的回收[J].化工技术与开发,2004.33(2):
45-47. [6] Silva J E.Paiva A P.Solvent Extraction Applied to the Recoveryof Heavy Metals
from Galvanic Sludge[J].Journal of Hazard OU8 Materials,2005,B120:113-118. [5] Jitka Jandova,Tatana Stefanova,Romana Niemczy kova.Recovery of Cu—
concentrates from Waste Galvanic Copper Sludges[J].Hydrometallurgy,2000,57:77-84.
[8] 贾金平,杨 骥.电镀重金属污泥的处理及综合利用现状[J].上海环境科学,1999,
18(3):139-146.
[9] 叶海明,王静.电镀污泥中铜的回收[J].化工技术与开发,2010.39(8):56-58. [10] 俞珏瑾.污泥干化焚烧处理工艺和设计要点[J].中国市政工程,2009, 3: 64-68. [11] 孙倬.重有色金属冶炼设计手册(铜镍卷)[M].冶金工业出版社, 2007:96-100,
150-156..
[12] 王志魁,刘丽英,刘伟.化工原理[M].北京:化学工业出版社,2011:90-97. [13] 换热器型式与参数(第三版) [S]. 北京:中国石油化工集团公司设备设计技术中心
站,2006.
[14] 赫吉明,马广大.大气污染控制工程(第二版)[M].北京:高等教育出版社,2002,
195-200.
39
致谢
本设计是在宁寻安教授的指导下完成的,从设计的选题、设计说明书的撰写和资料的获取到设计最后完成。宁老师都倾注了大量的心血,给与了我细心的指导和必要的支持。老师严谨的治学态度和一丝不苟的作风,都给我留下了深刻的印象。宁老师不仅教给我学问,更以他为人师表襟怀坦荡的风范,教会我怎样做人,这些将使我终身受益。在此,谨向宁老师表示衷心的感谢!
感谢学院领导对我全方面发展所给予的关心与支持;感谢全体老师对我的谆谆教诲;感谢同窗四年的环境学院全体同学所给予的珍贵友谊。
祝全体老师工作顺利,家庭美满幸福;祝全体同学一切顺利,前程似锦!
40
烘干机筒体转速一般为2r/min~5r/min,倾斜度一般为3%~6%.物料在筒体回转时,由高端向低端运动,从低端落入出料罩,经翻板阀卸出,再由皮带机运走.而热气体由燃烧室3进入烘干机筒体,与物料进行热交换,使物料强烈脱水,气体温度下降.废气经处理后由烟囱8排至大气。.
图4.2 回转烘干机流程示意图
1-料仓 2-皮带输送机 3-燃烧室 4-鼓风机 5-烘干机 6-除尘器 7-脱硫除氮 8-烟囱
17
回转烘干机的规格是以筒体的直径和长度表示,目前我国常用的几种规格的烘干机及设备操作控制参数如表4.1、4.2所示:
表4.1 几种规格的烘干机设备参数
表4.2 回转烘干机的操作控制参数
干燥物料的种类 进烘干机热气温度(℃) 出烘干机废气温度(℃) 出烘干机物料温度(℃) 石灰石 800-1000 100-150 100-120 矿渣 粘土 烟煤 400—70 90-120 60-90 1.5-3.0 无烟煤 500-700 90-120 60-90 1.5-3.0 700-800 600-800 100-150 80-110 80-100 1.5-3.0 80-100 1.5-3.0 烘干机出口气体流速(m/s) 1.5-3.0 注:河南宏科重工机械设备有限公司数据
18
1、选型计算:
处理量180/天,经计算出成品料60吨,待处理水分120吨 即:每小时处理水分为 120÷24=5(吨)。 设计污泥在烘干机内蒸发强度约70 kg/m3。h 故处理5吨/h水分所需要的有效烘干容积为 5000÷70=71.43 m3 设安全系数为§=1.2 则:
烘干机有效容积为 71.43×1.2=85.72 m3
经计算,Ф2.4×19米烘干机有效烘干机容积为:85.95 m3,故日处理180吨污泥的烘干机选型为Ф2.4×19米回转式烘干机。
2、进出气量计算:
常压常压下水的蒸发热为2675.9KJ /kg, 每小时处理水分为: 120÷24=5 吨
每小时消耗热量: 5000×2675.9=1.37×107kJ 标准煤热值为:29300.92kJ/kg
所以,每小时需消耗标准煤:1.37×107÷29300.92=467.56kg
燃煤中各种元素的质量含量,具体值见表4.3:
表4.3 燃煤煤质分析表
项目 收到基全水分 符号 Mt Mad Aar Vdaf Qnet,ar 单位 % % % % kj/kg 设计煤种 10.8 3.05 15.318 37.98 22700 19
工 分析基水分 收到基灰分 可燃基挥发分 应用基低位发热量 业 分 析
碳 Car Har Oar Nar Sar,ar % % % % % 58.31 3.69 10.166 0.966 0.75 元素分析氢 氧 氮 全硫 注:东莞某电镀污泥处理厂数据
4.3制砖工艺
高炉冶炼时,料柱要能够透气,否则就会悬料。料柱的透气性和炉料的空隙度有
20
(1)进气量:
1kg燃煤完全燃烧时所需要的理论需氧量:
g煤CO2 =C÷12×22. 4 = 1.09m3 g煤H2O = H÷8×22. 4 = 0.204m3 g煤SO2 = S÷32×22. 4= 0.00052m3 g煤O2= O÷32×22. 4= 0.0071m3 g煤N2 =N÷28×22. 4 = 0.00077m3
理论需氧量O2= g煤CO2 +g煤H2O÷2 +g煤SO2-g煤O2=1.18542 m3 空气中氧气含量为21%,则:
V空气=1.18542÷21%=5.6448 m3
设空气过量系数α = 1. 3,则实际空气量:
V= V空气×1.3×467.56kg =3431.10 m3/h
(2)烟气量:
设计出口烟气温度为100~120℃,所以出口水蒸气为气态。蒸汽量:
5×106÷18×22.4=6222.22 m3/h
出口烟气量:
6222.22 m3/h+3431.10 m3/h+(0.102+0.00077)×467.56kg=9701.37 m3/h 记为 10000 m3/h。
关,所以要求炉料要有一定的粒度和强度。如果矿粉入炉,则高炉的透气性变差,会使高炉的冶炼无法正常进行。为了解决此问题,需将干化后污泥制砖后再进行熔炼。 根据厂家提供数据,选择QT6-15型制砖机可满足设计要求。 QT6-15型技术参数及产量表见表4.4、表4.5: 表4.4 QT6-15型全自动砌块成型机技术参数 成型 周期 15~20 托板尺寸 850*680*25 装机容装机重成型机外形尺寸量(kw) 量(t) (mm) 38 12 7250*2950*3480 表4.5 QT6-15型全自动砌块成型机产量表: 最高振动频率(转/分) 4500 产品 标砖 多排孔砖 空心砌块砖 注:河南森达重工数据
规格(mm) 240*115*53 240*115*90 390*190*190 块/托板 30 15 6 块/小时 7200 3600 1440 4.4熔炼工艺
传统的铜锍熔炼鼓风炉的炉顶是敞开的,只能处理烧结矿或块矿,烟气含SO2浓度低,仅0.5%左右,难以回收,造成环境污染。20世纪50年代以后,国外、国内冶炼厂相继开发了料封式密闭鼓风炉,直接处理铜精矿,并采用了富氧熔炼。
密闭鼓风炉熔炼工艺流程简单,产出的炉渣含铜0.2%~0.3%,不需炉渣处理工序。因而投资较省,建设周期较短,比较适宜于小型铜冶炼厂采用。 该工艺的缺点如下:
一、床能率及脱硫率均比较低,导致能耗高、铜锍品位低;二氧化硫浓度低,导致铜锍吹炼工序、制酸工序的投资及生产费用增加。
二、不适于处理难熔脉石含量高的铜精矿,如精矿含SiO2 15%以上,则渣熔点升高,焦率增高。
21
图4.3 密封式鼓风熔炼炉
熔炼炉以焦碳为燃料和还原剂,炉膛内温度高达1250~1300℃。高温下,含铜污泥中的铜盐等重金属盐分解为氧化铜,80%氧化铜和一氧化碳接触还原为铜,即生成粗铜产品。由于铜对硫亲和力较强,20%氧化铜和污泥中的硫结合生成硫化亚铜,即得到冰铜产品。
高温下,含镍污泥中的镍盐等重金属盐分解为氧化镍,由于含镍污泥中镍的品位较低,一般为5%左右,因此氧化镍基本都是与污泥中的硫结合生成二硫化三镍,即得到冰镍产品。由于炉温高达1250℃以上,且铜镍比重大,铜、镍在炉底呈液态,定期将炉内的铜、镍等重金属放出成型,可得到粗铜、冰铜以及冰镍。
由于加入了铁矿石和石灰石,熔炼炉渣流动性好、比重小且提高了渣的回收率,所以炉渣在铜镍等重金属的上方,能由炉子上部的出口自动排放,流出的高温炉渣进行水淬,得到玻璃体粒化水淬渣,重金属均固溶于玻璃体中,具有极好的安定性,可外卖作为除锈冲洗剂或水泥厂生产硅酸盐水泥的原料[11]。 4.4.1工艺计算
本项目处理电镀污泥主要化学成分(干基)为:
22
表4.6 电镀污泥中主要的化学成分(干基)
含铜 元素 Cu Fe 25 SiO2 33 CaO 6 CaO 5 Na 5 Na 1.8 Zn 1.2 S 1.1 Ni 0.3 S 1.5 其它 13.4 其它 32.5 污泥 含量(%) 15 含镍 元素 Ni Fe SiO2 22 29 Al2O3 Zn 2 1.2 污泥 含量(%) 5 注:1、干基为不含水污泥
2、数据为东莞某电镀污泥熔炼处理厂环评数据
根据中国电镀行业产业架构,铜、镍污泥按3:5计算。
1、含铜污泥熔炼物料平衡计算
日处理干化电镀污泥60吨,含水率20%,则污泥干基为:
60×0.8=48t
每小时处理量:48÷24=2t 日待处理水分:12t 处理含铜干污泥量:(1)吹炼渣数量及成分
铜吹炼时,铁全部进入吹炼渣,吹炼成份根据工厂生产实践[11]选定为(%):Fe 50,Cu 3.5,SiO2 25,S 1.0
则吹炼渣量为:
(2)鼓风炉炉渣成分的确定
根据工厂生产实践,选定炉渣成分为(%):Cu 0.22~0.25,Fe 32,CaO 6,SiO2 10;
(3)熔剂量及炉渣量计算
由于炉渣中Fe,CaO的含量允许在一定范围内波动,故焦炭中的灰分在计算是可忽略不计。计算时取Cu,Fe,CaO等不可回收的损失约为污泥中成分的0.5%。
进入炉渣中的Fe可按污泥中的Fe量(损失后)计算:
23
750×0.25×0.995=186.56kg
鼓风炉渣量:186.56÷0.32=583kg
设石灰石含CaO52%,其它成分48%,则需要加入的石灰石熔剂:
(4)烟尘量
根据密封炉生产实践,烟尘产率一般为6~8%,取7%计算,则: 烟尘量: (750+375+583+26.01)×0.07=121.38kg 出炉物料量:750+375+583+26.01+121.38=1855.39kg/h 2、含镍污泥物料平衡计算 处理含镍干污泥量:(1)吹炼渣数量及成分
吹炼时,铁全部进入吹炼渣,吹炼成份根据工厂生产实践[11]选定为(%):Fe 50,Cu 3.5,SiO2 25。
则吹炼渣量为:
(2)鼓风炉炉渣成分的确定
根据工厂生产实践,选定炉渣成分为(%):Ni 0.9,Fe 52,CaO 1.5,SiO2 45,S 0.8。
(3)熔剂量及炉渣量计算
由于炉渣中Fe,CaO的含量允许在一定范围内波动,故焦炭中的灰分在计算是可忽略不计。计算时取Ni,Fe,CaO等不可回收的损失约为污泥中成分的0.5%。
进入炉渣中的Fe可按污泥中的Fe量(损失后)计算:
1250×0.22×0.995=273.62kg
鼓风炉渣量:273.62÷0.52=526.19kg
设石灰石含CaO52%,其它成分48%,则需要加入的石灰石熔剂:
24
(4)烟尘量
根据密封炉生产实践,烟尘产率一般为6~8%,取7%计算,则: 烟尘量: (1250+550+526.19+65.31)×0.07=167.40kg 出炉物料量:1250+550+526.19+65.31+167.40=2558.90kg/h
所以,熔炼炉总出炉物料量为:
1855.39 +2558.90=4414.29 kg/h
4.4.2进气量计算
根据生产实践,当采用富氧空气熔炼时,焦率一般为6~9%,普通空气 熔炼时,焦率一般为8~11%,本设计选用富氧空气熔炼时,焦率确定为9%。所以: 焦炭使用量: 4414.29×0.09=397.74kg/h 本设计使用焦炭成分见表4.7:
表4.7 焦炭成分
成分 % C 90.1 灰分 8.6 S 0.7 H 1.0 各成分的物质的量:
C:S:H:
熔炼污泥时污泥进入烟气中的硫: 含铜污泥 S:含镍污泥 S:
25
所需氧气量计算: mO2=mC+mS+
=
V= mO×22.4=799.42m3/h
空气中氧气含量为21%,则:
V空气=799.42÷21%=3806.78 m3
设空气过量系数α = 1. 3,则实际空气量:
V= V空气×1.3×467.56kg =4948.81 m3/h
4.4.3出气量计算
在熔炼过程中污泥中水分会已水蒸气形态排出,所以 熔炼炉出口烟气量:
V=4948.81+(500/18+19.90)×22.4=6016.79m3/h
记为61004.5除尘系统
熔炼烟气中粉尘的主要成分为惰性无机物质,如灰分、无机盐类、可凝结的气体污染物质及有害的重金属氧化物,其含量在450~22500mg/m3 之间,视运转条件、废物种类及熔炼炉型式而定 [13]。
烘干机烟气经过一套布袋除尘、双碱法脱硫以及沥青活性碳吸附催化还原脱氮处理,最后经高烟囱排入大气,烟气中污染物排放浓度能够达到《大气污染物排放限值》(DB44/27-2001)第二时段二级标准和《工业炉窑大气污染物排放标准》(GB9078-1996)要求。
熔炼炉烟气经过一套重力沉降、U形管冷却、布袋除尘、双碱法脱硫以及沥青活性碳吸附催化还原脱氮处理,烟气中污染物排放浓度能够达到《大气污染物排放限值》(DB44/27-2001)第二时段二级标准和《危险废物焚烧污染控制标准》(GB18484-2001)的要求。
26
4.5.1重力沉降室设计计算 1、 沉降原理
重力沉降室是通过重力作用使尘粒从气流中沉降分离的除尘装置。含尘气流进入重力沉降室后,由于扩大了流动截面积而使气体流速大大降低,使较重颗粒在重力作用下缓慢向灰斗沉降[12]。 2、沉降速度的计算
本设计所处理的含尘气体是由烘干机和熔炼炉排出,最大排放烟气量q为6100m3/h。假设气体处于层流区,则沉降速度u为:
u?2gdp(?p??)18?
式中:dp—颗粒直径,取50μm;
?p—颗粒的密度,取2000kg/m3;
3
—气流的密度,取0.779kg/m; ?
-5—空气粘度,300℃取2.97×10Pa·s。 ?
9.8?(50?10?6)2?(2000?0.779)?0.09m2/s 得: u?18?2.97?10?5 3、沉降室尺寸的计算 沉降面积A:
A?q6100?3600??18m2 u0.092颗粒在沉降室中分离出来的条件是:
LH? vu 式中:L—沉降室的长度,m;
v—颗粒运动的水平分速度,取0.5m/s; H—沉降室的高度,取1.6m。
27
1.6?0.5?8.7m,取为9m。 0.092A18?2m 沉降室的宽W为: W??L9 得: L?故沉降室的尺寸为9×2×1.6m。 4.5.2 U型管式冷却器选择
U形管式冷却器的结构特点是只有一块管板,换热管为U形,管子的两端固定在同一块管板上,其管程至少为两程。管束可以自由伸缩,当壳体与U形换热管有温差时,不会产生温差应力[13]。
本设计选用U形管式冷却器,利用水作为冷却剂。熔炼炉出口烟气1000℃,设计冷却到200℃。选用AES325-2.5-10型可满足设计要求。AES325-2.5-10型U形管式冷却器参数见表4.8:
表4.8 AES325-2.5-10型U形管式冷却器参数
DN mm 管长 M 管程数 U型管计算传设备净充水水型号规格 规格 热面积 重 m2 Kg 1395 重 Kg 370 325 3 4 Φ25 15.8 AES325-2.5-10 4.5.3除尘器设计计算 1、除尘器种类选择
选择除尘设备时,应首先考虑粉尘负荷、粒径大小、处理风量即允许排放浓度等因素,若有必要则再进一步深入了解粉尘的特性(粒径尺寸分布、平均与最大浓度、真密度、粘度等)及废气的特性(如压力损失、温度、湿度及其他成分等),以便作合适的选择。布袋除尘器是固体废物焚烧系统中最重要的除尘设备[14]。
本设计选用袋式除尘器。袋式除尘器是含尘气体通滤袋(简称布袋)滤去其中粉尘离子的分离捕集装置,是过滤式除尘器的一种。自从19 世纪中叶布袋除尘器开始用于工业生产以来,不断得到发展,特别是20 世纪50 年代,由于合成纤维滤料的出现脉
28
冲清灰及滤袋自动检漏等新技术的应用,为袋式除尘器的进一步发展及应用开辟了广阔的前景。
通常认为袋式除尘器对尘粒的捕集分离过程包括以下两个过程:
(1)过滤材料对尘粒的捕集 当含尘气体通过过滤材料时,滤料层对尘粒的捕集是多种效应综合作用的结果。这些效应主要包括惯性碰撞、截留、扩散、静电和筛滤等效应。
(2)粉尘层对尘粒的捕集 过滤操作一定时间后,由于粘附等作用,尘粒在滤料网孔间产生架桥现象,使气流通过滤料的孔径变得很小,从而使滤料网孔及其表面迅速截留粉尘形成粉尘层。在清灰后依然截留一定厚度的粉尘,称为粉尘初层。由于粉尘初层中粉尘粒径通常避嫌微笑,因此筛滤、惯性、截留核扩散等作用都有所增加,使粉尘效率显著提高。由此可见,袋式除尘器的高效率,粉尘初层起着比滤料本身更为重要的作用。一般合成纤维布的网孔为20~50 μm,如为起毛的的则为5~10μm,用这样的滤料,只要设计得当,就是0.1μm的尘粒也能获得接近100%的除尘效率。 袋式除尘器主要有以下优点:
(1)袋式除尘器对净化含微米或亚微米数量级的粉尘粒子的除尘效率较高,一般可达99%,甚至可达 99.99%以上;
(2)这种除尘器捕集多种干性粉尘,特别是对于高比电阻粉尘,采用袋式除尘器净化要比用电除尘器的净化效率高很多 ;
(3)含尘气体浓度在相当大的范围内变化 对袋式除尘器的除尘效率和阻力影响不大;
(4)袋式除尘器可设计制造出适应不同气量的含尘气体的要求。除尘器的处理烟气量可从每小时几立方米到几百万立方米;
(5)袋式除尘器也可做成小型的,安装再散尘设备上或散尘设备附近,也可安装在车上做成移动式袋式过滤器,这种小巧、灵活的袋式除尘器特别适应于分散尘源的除尘;
(6)袋式除尘运行稳定可靠,没有污泥处理和腐蚀问题,操作和维护简单。除尘器为上进下排外滤方式袋式除尘器,袋内设有弹簧骨架。清灰时,滤袋上、下同时一
29
组气阀,用压缩空气自动定时对滤袋进行压力喷吹清灰。具有处理风量大,喷吹压力低且气量大,滤袋拆装方便等优点。
图4.4 袋式除尘器结构图
2、除尘器计算
烘干烟气量10000 m3/h,熔炼烟气量6100 m3/h。烟气含尘浓度较高,净过滤风速不超过1.0m/min(GB16297).设计流速取0.8m/min 计算,则布袋的过滤面积:
S=16100÷(0.8×60)=335.42m2
布袋除尘器型号参数表如表4.9:
表4.9 布袋除尘器型号参数表
型号 处理风量(m3/h) A >100g/mn3 PPW32-3 5000 PPW32-4 6500 PPW325 9000 PPW32-6 PPW64-3 PPW64-5 PPW64-6 PPW64-7 11500 13000 18000 22000 26000 ≤B 100g/mn3 6900 8030 11160 13390 17800 22300 26700 31200 30
过滤风速(m/min) 总过滤面积(m2) 净过滤面积(m2) 收尘器室数(个) 滤袋总数(条) 448收尘器阻力(Pa) 出口气体含尘浓度(mg/m3n) 设备总重(kg) 96 64 3 96 128 96 4 128 160 128 5 160 1.0~1.2 192 256 160 192 6 4 192 256 1500~1700 <50 320 256 5 320 384 320 6 320 448 384 7 384 2400 3400 4400 5400 6900 8800 9700 11800 注:泰州祥荣机械制造有限公司数据
选用气箱脉冲袋式除尘器型号都为PPW64-7。 4.6污染气体处理系统
根据对生产工艺全流程及废气产生源的分析,本项目工艺废气污染物主要来源于烘干机以及熔炼炉排放的烟气,主要含有SO2以及NOx,必须经过处理,达标排放。 4.6.1双碱法脱硫
双碱法是先用可溶性的碱性清液作为吸收剂吸收SO2 ,然后再用石灰乳或石对吸收液进行再生,由于在吸收和吸收液处理中,使用了不同类型的碱,故称为双碱法。钠钙双碱法是以碳酸钠或氢氧化钠溶液为第一碱吸收烟气中的SO2 ,然后再用石灰石或石灰作为第二碱,处理吸收液,再生后的吸收液送回吸收塔循环使用[14]。由于采用钠碱液作为吸收液,不存在结垢和浆料堵塞问题,且钠盐吸收速率比钙盐速率快,所需要的液气比低很多,可以节省动力消耗。钠钙双碱法在国外(如日本、美国) 已有大型化成功应用,在日本和美国至少有50 套双碱法脱硫装置,成功应用于电站和工业锅炉。 双碱法脱硫工艺原理如下: 吸收反应
二氧化硫吸收过程的主要反应式为:
2NaOH + SO2 →Na2SO3 + H2O NaCO3 + SO2 →Na2SO3 + CO2↑
31
Na2SO3 + SO2 + H2O →2NaHSO3
此过程的主要副反应为氧化反应, 生成Na2SO4 :
Na2SO3 + 1/2O2 →Na2SO4
用石灰浆进行再生:
2NaHSO3 + Ca (OH)2 → Na2SO3 + CaSO3 ·1/2H2O ↓+ 3/2H2O Na2SO3 + Ca (OH)2 + 1/ 2 H2O →NaOH + CaSO3·1/2H2O ↓
以上钠钙双碱法工艺的特点,是先用钠碱清液吸收SO2 ,然后用石灰乳再生吸收液。由于是清液吸收,不仅脱硫效率高,而且可以避免湿式石灰/ 石灰石法所经常遇到的吸收器和管道内易结垢的问题。
双碱法烟气脱硫技术是利用氢氧化钠溶液作为启动脱硫剂,配制好的氢氧化钠溶液直接打入脱硫塔洗涤脱除烟气中SO2来达到烟气脱硫的目的,然后脱硫产物经脱硫剂再生池还原成氢氧化钠再打回脱硫塔内循环使用[18-19]。脱硫工艺主要包括5个部分:
(1)吸收剂制备与补充;(2)吸收剂浆液喷淋;(3)塔内雾滴与烟气接触混合;(4)再生池浆液还原钠基碱;(5)石膏脱水处理。 脱硫塔设计计算 塔径及底面积计算: 塔内流速:取v?3.2m/s
D=2r=0.88m 取塔径为1.0米。底面积S=∏r2=0.78m2 脱硫塔高度计算:
液气比取L/G= 4 烟气中水气含量设为15%
L?Q?HG4?16100?(1?0.15)3G??54.74m/h 循环水泵流量:Q?310001000(l/m) 取每台循环泵流量Q?50m。选65FZS-25型耐腐蚀离心泵,流量28m3/h,扬程26米,功率4.5KW ,2台。
32
计算循环浆液区的高度: 取循环泵8min的流量
H1=7.33÷0.78=9.40m
计算洗涤反应区高度:
停留时间取1秒
洗涤反应区高度H2=3.2×2=3.2m 除雾区高度取4米: H3=4m 脱硫塔总高度H=H1+H2+H3=16.60m 4.6.2活性炭吸附法脱氮
活性炭吸附塔是用活性炭作吸附剂吸附去除尾气中NOX的技术。活性炭能吸附NO2,还能促进NO氧化成NO2。特定品种的活性炭还可使NOX还原为N2。活性炭可定期用碱液再生。NOX尾气中氮含量大有利于吸附;水分的存在亦有利于吸附,湿度大于50%时,这种影响更为显著[20]。活性炭吸附法可同时脱附尾气中的硫氧化物。本设计的脱氮处理设备采用活性炭吸附塔。如图4.7:
图4.5 活性炭吸附塔
33
活性炭吸附塔规格参数如表4.10:
表4.10 活性炭吸附塔规格参数
烘干烟气和熔炼烟气脱氮处理活性炭吸附塔采用型号为LXT-4。 4.7灰渣处理系统
烘干系统炉渣是由煤燃烧产生的,炉渣都为一般工业固废,主要成分是轻质的硅酸盐类无机物,不属危险固体废物,送水泥厂作为水泥生产的辅助原料使用。熔炼炉渣经水冷却后,形成玻璃体粒化水淬渣,重金属均固溶于玻璃体中,具有极好的安定性,主要成分是轻质的硅酸盐类无机物,重金属的浸出浓度远低于毒性鉴别标准,可用作建筑辅材或造船厂的除锈材料。 4.8功能区布置
在作平面布置时,应根据各构筑物的功能要求和,结合地形和地质条件,确定它们在厂区内平面的位置,对此,应考虑:
(1)功能分区明确,管理区、污泥处理区相对独立; (2)构筑物布置力求紧凑,以减少占地面积,并便于管理; (3)考虑近、远期结合,便于分期建设,并使近期工程相对集中; (4)各处理构筑物顺流程布置,避免管线迂回;
34
(5)变配电间布置在既靠近厂区进线,又靠近用电负荷大的构筑物处,以节省能耗;
(6)建筑物尽可能布置为南北朝向; (7)交通顺畅,使施工、管理方便。
功能区平面布置除遵循上述原则外,还应根据城市主导风向,进水方向、排水方向,工艺流程特点及厂区地形、地质条件等因素进行布置,既要考虑流程合理,管理方便,经济实用,还要考虑建筑造型,厂区绿化及与周围环境相协调等因素。
35
5、工艺成本概算
5.1土建及设备投资概算
主要工艺构筑物有储泥室、烘干车间、制砖车间、熔炼车间等 ,该部分建设投资见表5.1:
表5.1构筑物投资表
序号 1 3 4 5 小计T1 名称 储泥室 烘干车间 制砖车间 熔炼车间 结构 钢混 砖混 砖混 钢混 数量 1 1 1 1 单位 座 座 座 座 规格 5×5×4m 30×4×3m 10×5×4m 30×10×4m 造价(万元) 20 70 40 70 200 主要工艺设备有烘干设备、制砖设备、熔炼设备、脱硫设备、除尘设备、脱氮设备等。设备投资见表5.2:
表5.2 主要设备投资表
编名 称 号 1 2 3 4 5 6 7 8 回转式烘干机 密封鼓风熔炼炉 制砖机 袋式除尘器 脱硫塔 重力沉降室 U型管式冷却器 活性炭吸附塔 数 量 1 1 1 1 1 1 1 1 单规格 单价投资 备注 (万元) 45 60 14 12 13 15 2 10 外购件 外购件 外购件 外购件 — — 外购件 外购件 36
位 型号 19m 套 Ф2.4×套 — 台 QT6-15 台 PPW64-7 16m 座 Ф0.8×座 9×2×1.6m (万元) 45 60 14 12 13 15 台 AES325-2.5-10 2 座 LXT-4 10
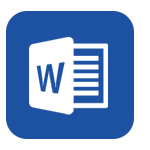





正在阅读:
压力容器操作人员取证考试题(B)12-07
开题报告101-11
薛瑞萍推荐的阅读书目03-02
《宏观经济学》课后练习题4-1005批注10-05
2022年桂林电子科技大学201工程力学之材料力学复试实战预测五套04-06
2018法考理论真题考点精解之法的运行03-30
linux添加路由命令11-22
实习鉴定评语【优秀6篇】03-22
- 多层物业服务方案
- (审判实务)习惯法与少数民族地区民间纠纷解决问题(孙 潋)
- 人教版新课标六年级下册语文全册教案
- 词语打卡
- photoshop实习报告
- 钢结构设计原理综合测试2
- 2014年期末练习题
- 高中数学中的逆向思维解题方法探讨
- 名师原创 全国通用2014-2015学年高二寒假作业 政治(一)Word版
- 北航《建筑结构检测鉴定与加固》在线作业三
- XX县卫生监督所工程建设项目可行性研究报告
- 小学四年级观察作文经典评语
- 浅谈110KV变电站电气一次设计-程泉焱(1)
- 安全员考试题库
- 国家电网公司变电运维管理规定(试行)
- 义务教育课程标准稿征求意见提纲
- 教学秘书面试技巧
- 钢结构工程施工组织设计
- 水利工程概论论文
- 09届九年级数学第四次模拟试卷
- 熔炼
- 污泥
- 电镀
- 最终
- 工艺
- 处理
- 设计
- 180
- 格兰诺维特 - 经济行为与社会结构(沈原译)
- 激光焊接传热过程的数值计算讲解
- 新明锐BCM长编码
- 晋亿扣件简介 - 图文
- 基础综合英语 邱东林版
- Dosbox安装windows98
- press 和pressure的详细区别及练习(附答案)
- 最新部编人教版一年级语文上册:1.秋天(说课稿)
- 1rr万科集团财务分析
- 一语 王学一
- 经济学试卷
- 反洗钱选择题,考试题库
- 浅谈新型干法熟料生产线的烧成系统
- 国网重庆市区供电公司“四措一案”管理实施细则(2018年修订版)
- 水泥搅拌桩监理细则
- 六性分析报告
- 2019年《联觉》语文阅读答案 及解析-实用word文档(3页)
- 使用自动加渣控制系统有何效益
- 优秀房屋立面改造、维修、翻新、加固施工组织设计(技术标)(31)
- 农村学生营养餐计划实施细则